高速干切削技术及其实现
前言
高速切削加工因具有增进生产效率、减少切削力、提高加工精度和表面质量、降低生产成本,且可加工高硬材料等诸多优点,已在航空、汽车、模具等制造业界得到广泛应用,并取得了显著的经济效益。在高速加工中,通常都大量使用切削液,以发挥其润滑、冷却、排屑作用。但随着绿色制造、清洁制造等生产理念的成熟,人们越来越清醒地意识到大量使用切削液所带来的负面影响:① 零件的生产成本大幅度提高。有统计数据表明,在零件加工总成本中,切削液费用约占16%,而刀具费用只占总成本的4%。② 造成对环境的严重污染,破坏生态环境,不利于可持续发展战略的实施。③ 直接危害车间工人的身体健康。为提高产品竞争力,实现经济效益与社会效益的统一,本研究探讨将高速切削加工和干切削技术有机结合的高速干切削技术,对于实现绿色制造及指导业界的生产,具有重要的现实意义。
1 高速干切削技术的内涵
在所见论述干切削技术的文献中,干切削技术通常都是指不使用切削液来进行切削加工的技术方法,是相对于传统的使用切削液加工(湿加工)方法而言的。笔者认为这只是狭义上的干切削技术,今天更应该从广义上来理解干切削技术:只要是在加工过程中不使用切削液或很少使用切削液,加工出的工件和形成的切屑是干燥的、“干净”(清洁)的且能保证加工质量的方法就应归人干切削技术范畴。如采用最小量润滑技术(Minimal Quantity Lubrication)法加工时,工件和切屑可保持干燥,过去称之为“准干切削”(Near-Dry cutting) ,实际上从广义来说,可认为其属于干切削范畴。所以高速干切削技术可表述为:高速干切削技术是使用高速切削加工方法,在切削过程中不使用切削液或使用微量切削液,加工出的工件和形成的切屑是干燥的、“干净”(清洁)的高精度、高效率的先进加工技术。
2 高速干切削技术实现方法
要实现高速干切削技术,就要研究用相关的技术手段在加工过程中复现、替代切削液的润滑、冷却、排屑的功用,以消除因缺少切削液而产生的刀具与工件、切屑之间摩擦的增加,以及由此引起的刀具寿命下降、工件加工质量变差等问题,从而顺利进行干切削加工,达到或超过湿加工时的生产率,并提高加工质量、刀具耐用度。这些可以从包括机床、刀具、工艺等在内的几个方面来实现。
2.1 高速干切削的机床技术
从机床技术角度出发实现高速干切削技术,主要考虑的问题是:① 切削热迅速散发;② 切屑和灰尘的快速排出;③ 采用不同的工艺方法时辅助设备的安装等。
采用高速机床
高速加工能使切削力降低30%左右,90%以上的切削热由切屑带走川,工件可基本保持室温状态,特别适合加工后容易热变形的工件。并且激振频率远高于机床和工艺系统的固有频率,加工过程平稳,振动小,铣削和车削可达到磨削的质量水平。高速加工的这些优点可弥补干切削的一些不足,二者的有机结合可实现高效、优质、无污染的加工。这也正是使用高速干切削技术的初衷。
机床结构排屑装置设计
实现快速排屑结构设计的最可靠的方法之一就是改造机床结构,使切屑能利用自身重力自动、快速地排出。这种方法只需要在原机床结构的基础上进行改造,在机床工作间内预留出一定的排屑空间,去除工作间内容易滞留切屑的平台或沟槽。或者直接把原来普通机床的主轴、刀架改为立式布置,也能实现快速排屑,这样工件在切削时就被倒置在工作间里,切屑被切离工件后自然落下。这种结构上的改造不但能可靠地实现快速排屑,而且几乎不增加机床的造价,因此得到了广泛、迅速的应用。
干切削会比传统切削产生更多的灰尘和细小切屑,这些灰尘和细小切屑一旦进人机床运动副,会加剧机床部件的磨损,若进人机床电气控制线路,则可能造成短路。所以应对机床主轴、导轨等精密运动部件进行密封,必要时设计真空、吹气或虹吸装置来排尘及辅助排屑,以保证切削过程的顺畅。
遵循模块化设计原则
由于加工方法和工件特性的差异,进行干切削加工时可能需要用到不同的辅助设备(如MQL技术中的喷油润滑装置、激光辅助加工中的激光辅助装置等)。所以机床结构应实行模块化设计,将各种辅助装置与机床主体之间的接口标准化,使机床能方便地实现不同的工件与切削方法的组合。
2.2 高速干切削的刀具技术
由于不使用切削液,干切削的切削区失去了切削液冷却、润滑,干切削时的切削温度比普通湿切削时的切削温度要高很多,刀具与切屑间的摩擦增大,加剧了刀具的磨损。刀具能否承受干切削时巨大的热能,是实现干切削的关键。只有采用高热刚度、高硬度、高冲击韧性的刀具材料,结合涂层技术以及对刀具参数和切削用量进行优化,才能够可靠地实现高速干切削。
采用性能优越的刀具材料
干切削不仅要求刀具材料具有极高的红硬性和热韧性,而且还必须有良好的耐磨性、耐热冲击和抗粘结性。超细颗粒硬质合金、金属陶瓷、陶瓷(Al2O3,Si3N4)、立方氮化硼(CBN)、聚晶金刚石(PCD)等都具有较高的红硬性和耐磨性,是目前应用最为普及的几种干切削刀具材料在选用这些刀具材料时,应与加工材料的性质、加工方法结合起来综合考虑。
超细颗粒硬质合金特别能承受较高温度的切削,具有较高的强度和冲击韧度,适用于制作干切削用的钻头和铣刀。金属陶瓷的硬度和冲击性好,但热硬性差,大多用于精加工和半精加工。陶瓷具有硬度高、化学稳定性和抗粘结性好、摩擦系数低等优点,是相对廉价的干切削刀具材料,但其强度、韧性和抗冲击性能差,适用于灰铸铁和钢的高速干切削。CBN 的硬度和耐磨性仅次于金刚石,有优良的红硬性北学稳定性和低摩擦系数,是高速干切削HRC50以上淬硬钢和冷硬铸铁等黑色金属时的理想刀具材料。PCD刀具有很高的硬度和热导率,适合高速干切削有色金属合金(如铜合金、铝合金以及钛合金)与纤维增强塑料等复合材料,但不能加工黑色金属。
上述材料又大都有脆性比较大的缺点,但是干切削相对于传统湿切削而言,消除了由于切削液使用不连续或冷却不均造成的热冲击,因此对使用这些脆性较大的超硬刀具材料更为有利。
采用涂层技术
对刀具进行涂层处理,是提高刀具性能的重要途径。涂层刀具是当今高速干切削最常用的刀具。在切削过程中涂层可以取代切削液的两大作用是:① 提供低摩擦层,取代切削液的润滑作用;② 提供低导热率层以抵抗切削热向刀具传播,取代切削液冷却刀具的作用。
涂层刀具可分为“硬”涂层刀具和“软”涂层刀具。涂层刀具的基体一般是韧性较好的硬质合金,“硬”涂层刀具是在基体上涂上一层或多层TiC、TiN、TiAlN和Al2O3之类的耐磨硬涂层,起耐热和隔热的热屏障作用。这类刀具表面硬度高、耐磨性好。其中,TiC涂层刀具抗后刀面磨损的能力特别强,而TiN涂层刀具则有较高的抗“月牙洼”磨损能力。另一类是“软”涂层刀具,也称为“自润滑刀具”,如MoS2、WS等涂层刀具。这类刀具与工件材料的摩擦系数很低,只有0.01左右,能减少切削力和降低切削温度。
在高速干切削中,常常采用多层复合涂层刀具。把硬涂层和软涂层结合在一起,即在一道涂覆工序中采用两种物理气相沉积(PVD)工艺,先产生硬涂层TiAlN,然后再在其上面通过采用溅射法产生WC/C软涂层,可以有效提高刀具使用寿命。目前新涂层技术得到了长足的发展,如高硬度、高热稳定性的金刚石薄膜涂层,由多种涂层材料的不同组合构成的纳米级涂层和为被加工材料量身定做的专用涂层等。相比较而言,纳米级涂层和专用涂层可以通过合理设计使刀具的硬度和韧性显著增加,使其具有优异的抗磨损及自润滑性能,适合用于各种材料的干切削。
优化刀具结构和切削用量设计的刀具结构应耐磨损、耐冲击。干切削过程中刀具与切屑接触区域的温度升高,容易导致干切削刀具的月牙洼磨损失效。因此,通常干切削刀具具有大的前角和刃倾角,以减少切屑与前刀面的接触面积,使切屑带走大量热量。干切削的高硬刀具材料一般都有较大的脆性,前角增大后刀刃强度又会降低,此时应配合以适宜的T型刃带、强化刃口以加强刀刃强度,采用适宜的负倒棱或前刀面加强单元来加强支承,分散压力。
刀具的几何参数和结构设计还应满足干切削对断屑和排屑的要求。特别是对韧性材料的加工来说,断屑非常关键。目前车刀三维曲面断屑槽的设计制造技术已经比较成熟,可针对不同的工件材料和切削用量,快速设计出相应的断屑槽结构与尺寸,大大提高切屑折断能力和对切屑流动方向的控制能力。在封闭空间进行干切削(如干钻削、干铰削、干攻螺纹等)时,应增大刀具的容屑槽空间和背锥的锥度。
由于高速切削加工具有切削力小、散热快、加工过程稳定性好等优点,在干切削的切削用量选择中,应尽可能采用较大的切削用量。
2.3 高速干切削的工艺技术
干切削和高速切削技术一样,还不是一项通用技术,高速干切削技术的应用受工艺条件、工件材料和加工类型影响,有些加工适宜采用干式切削,有些则不宜,在制定工艺时应作具体分析。高速干切削的工艺技术还在发展中,目前已有一些成熟的加工工艺方法。
加工铸铁的“红月牙”(Red Crescent)技术。这种方法是利用陶瓷或CBN刀具进行高速加工,聚集在刀具前端的热量使工件达到赤热状态,降低了工件的屈服强度,达到增大切削速度和进给速度的要求,从而大大提高了切削效率。
MQL方法。这种方法是将压缩的空气与少量的润滑液混合气化后,喷射到加工区,对刀具和工件之间的加工部位进行有效的润滑。MQL技术可以大大减少“刀具-工件”和“刀具-切屑”之间的摩擦,起到抑制温升、降低刀具磨损、防止粘连和提高工件加工质量的作用。MQL使用的润滑液是对人体健康无害的植物油或脂油,其用量极少,一般为0.03~0.2L/h,而1台典型的加工中心在进行湿切削时,切削液的用量高达20~100L/min ,是MQL润滑油用量的6万倍左右。
液氮冷却干切削和激光辅助干切削的工艺技术。液氮冷却技术的机理是采用液态氮冷却刀具的切削部位,吸收切削时的发热量,始终保持刀具在干切削下的优良切削性能,已在生产实践中用于难加工材料钦合金TC4的加工。而激光辅助干切削的工艺技术是用改善工件材料被切削部位的物理力学性能、减少加工时的切削阻力来实现干切削的。如在对氮化硅(Si3N4)工件进行硬车削时,采用激光束对工件切削区进行预热,使工件材料局部软化,可减少30~70%的切削阻力,改善了材料的可加工性,刀具磨损可降低80 %左右。干切削过程中的振动也大为减少,大大提高了材料的切除率,使干切削得以顺利进行。
3 结束语
高速干切削加工从根本上解决了切削液具有的弊端,是一种绿色加工技术,是面向21世纪的前沿制造技术。干切削技术与高速切削技术的有机结合,将获得生产率高、加工质量好和无环境污染等多重利益。
高速干切削加工技术是一项系统技术,无论在认识观念或技术上都还有许多困难和障碍需要克服,需要进行长期的努力,才能使这项加工技术日臻成熟。
声明:本网站所收集的部分公开资料来源于互联网,转载的目的在于传递更多信息及用于网络分享,并不代表本站赞同其观点和对其真实性负责,也不构成任何其他建议。本站部分作品是由网友自主投稿和发布、编辑整理上传,对此类作品本站仅提供交流平台,不为其版权负责。如果您发现网站上所用视频、图片、文字如涉及作品版权问题,请第一时间告知,我们将根据您提供的证明材料确认版权并按国家标准支付稿酬或立即删除内容,以保证您的权益!联系电话:010-58612588 或 Email:editor@mmsonline.com.cn。
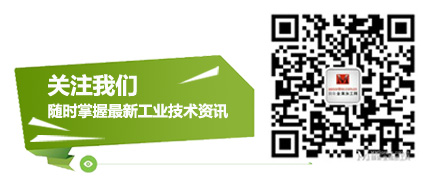
- 暂无反馈