注射模具调试要点
模具调试又叫做试模,它是模具制造过程三大程序(即设计、加工、试模)中,最后的也是关键的工序。它是模具设计,模具制造的总验核。
试模的准备
模具的准备
经过研配安装后的模具,必须进行通水(应用专门的带增压装置的试验设备)、通电(主要是带有热流道和电热棒的模具,此时要进行耐高电压安全试验)等安全性试验以及模具活动部分的动作试验,例如,顶出机构,液压及机械抽芯机构等,并进行制品的厚度测量(可用粗细不同的软铅丝置于型腔、型芯之间碰模后测量、或注入特制的蜡进行测量)。另外,还要检查吊钩、锁紧机构等装置的安全性。
试模材料的准备
试模材料应选用与成品相同的塑料进行试模。
试模机床(注塑机)的选定
对注塑模具,首先根据注塑件的大小、形状确定注塑机的规格,即按注塑件在注射方向的投影面积S和选定的模腔内平均注射压力P,计算制品的工艺锁模力P2。
P2=S‧P‧η/1000
P2—制品的工艺锁模力(KN)
S—制品在开模方向的投影面积与流道投影面积(mm2)之总和
P—模内注射平均压力(MPa),依据塑料粘度和流长比而定。塑料粘度的影响因素包括树脂的特性、温度、流动剪切速率等,例如PE、PS、PP等材料粘度系数较低,PC材料的粘度系数是以上三种材料的一倍。流长比是塑料熔体自浇口至塑制件最远端的长度与塑制件平均厚度之比。流长比越大则要求模内压力P越高,一般可取20-40。
η—特性系数,一般取1.2。
注塑机的恒定锁模力应等于或者大于塑料制品的工艺锁模力。其次应复核注射量,制件的质量(包括制品及水口)应选用在注射机最大注射量的30-75%之间为宜。
注射机的恒定锁模力和注射量要同时满足上述两个条件,才能用作制品试模或加工。注射机的喷嘴孔直径应比模具浇注系统主流道口直径小(0.5-1mm)。还应考虑模具的安装尺寸、模具的闭合高度、开模距离、定位圈尺寸、顶出方式等。
试模工艺条件的选定
注射压力
试模开始不宜选用太高,应在试模中逐步提高,尤其是筋较多的模具,或者型腔较深的模具,更要注意,以免产生大量的飞边和胀模,造成脱模困难或模具受到破坏。
注射量
注射量一般以注射熔料的容积(cm3)表示,因为质量会由于塑料密度的不同而变化,而密度要受注射时间、压力、温度等影响。试模前应通过标准件测试或计算求得最大值,试模时从小到大逐渐提高,直到得到完整制品。
计算公式:
制品质量=注射量*ρ
注射量=m/ρ=l*螺杆截面积
注射行程=注射量/螺杆截面积
=注射量/0.785D2
=(m/0.785D2ρ)*1000
D—螺杆直径(mm)ρ—密度(一般取其值为1) m—制品质量(克)l—注射行程(mm)
注射速度和注射速率
注射速度是指螺杆或柱塞在注射时单位时间前进的速度(cm/s),注射速率是熔料在单位时间内从喷嘴射出的熔体容量(cm3/s)。一般为了使熔料在模具内不被迅速冷却,在制品上不出现熔接痕,要求提高注射速率。但注射速率的提高,会由于熔料流在高速产生的剪切热而使熔体破裂,或因空气动能被高速流动的熔体急剧压缩产生的热量超过材料分解热,而出现所谓困气烧焦。试模时一般先取较高速注射,发现有烧焦时再降低,直至消除为止。
注射料温
注射温度主要是由塑料树脂的性能参数确定的,为了易于注射成型,一般取上限,待注塑定型后再降到合适的值。因为料温过高会出现气痕、烧焦等缺陷。结论:试模开始应选择高料温、低压力、高射速和合适储料量(注射量)的工艺条件。依据模具实际情况,通过试模逐步调整,直至合适,并将整个试模过程作好记录。
试模制品缺陷分析
飞边
常见的飞边在分型面、抽芯滑块成型面、顶出机构表面等处。首选要调整试模工艺条件,例如,注射料量是否过大、注射压力是否过大或锁模力不足(用百分表测量是否胀模)。试模工艺因素外,主要是模具零件加工精度或研配精度差、分型面与型腔交界处有小圆弧等原因造成,可采取相应措施解决。例如,分型面飞边,则应研配各碰硬面,减小分型面间隙;又如分型面与型腔交界处有小圆弧,如仅在0.03-0.06mm以内,且在壁厚允差范围内,可将分型面小圆弧磨去一些(这样会减薄制品厚度)。
顶出白印,甚至穿透制件。
顶白的原因是顶出力超出了塑料的弹性极限。首先检查脱模斜度是否过小,甚至是负角(倒扣)。其次检查型芯相关部位的研抛是否达到要求的表面粗糙度。还应检查零件配合是否过松,或该处制件壁厚过薄,或模具设计时考虑强度不足。主要是不可忽视模温,一般模温超过40℃往往是塑件顶白的主要因素。在注塑中模具变形也是可能的原因。在检查模具变形之前,也先要调整试模工艺条件,可减小注射压力至足够小,过大的注射压力也是产生白印的原因之一。
熔接痕
熔接痕是熔融的塑料树脂在充模中穿过障碍物、或者两个浇口的料流冷料前锋相遇时,熔接不良而形成的。熔接痕通常可以通过提高料温、提高模温等提高熔料流动性或提高注射速率的方法解决。当制品要求某些部位无熔接时,应改变浇口位置,或改变某些浇口及型腔尺寸的大小,即改变料流的相遇部位,把熔接痕转移到低感光区、应力不敏感区。在熔接痕的部位,增加排气孔或者开“垃圾销”,也可以减小熔接痕。
缩痕
在制品某些部位可见塑料的冷却收缩痕,尤其在制件与筋相交的表面处更明显。这是因为此处的料厚,周围较该处先冷凝,该处冷凝时已无法从周围取得熔料补充而造成。改进的方法,一是在制品设计时将筋减薄,一般筋的厚度应在相交处壁厚尺寸以下,深度不超过交界壁厚的3倍。或用气体辅助注射的方法,增加气体流道。二是注塑时,提高注射压力,适当降低料温,提高保压压力等。其中最佳的方法是采用气体辅助。
银丝瘢
在制件表面的银丝状瘢痕通常称为银丝瘢。产生的原因,主要是在熔料中或模具中混有水分,可先行将物料和模具烘干解决。有的瘢痕也可能是料温过高或熔料在料筒中停留的时间过长,注射时熔体的分解气体造成,则可用降低料温、尽量缩短熔料在料筒中的时间解决,也可适当的控制注射速度解决。
烧焦
表现为在制品某些部位有烧焦,主要是模具排气不畅、料流速度过快等原因造成,采取相应对策解决。
制件表面不光亮(未作表面腐融前)
试模时可相应的调整注射速率、料温、模温等工艺参数解决。对于模具可进一步抛光,增加排气等修整。
制件翘曲
这是由于制件冷却不均和成型应变造成的。可试模时提高注射压力、降低模温及提高熔料温解决。如仍无法解决,则应修模。可从改变浇口位置、浇口形式(扇形较直浇口好)、冷却流道部位、冷却温度均匀性等着手解决。也有用夹具将刚从模具中脱出的制品进行固定整形,解决翘曲。
注射不足
试件的某些部位有缺损。主要由注射量不足、排气不畅、注射压力低、料温低、注射速率低等原因产生,可先在试模中逐项调整工艺参数解决。
如仍难以解决则应修模。修模时应考虑模具流道是否畅通、排气是否通畅、制品该处壁厚是否过薄、冷料穴是否太小等,然后采取相应对策解决。
声明:本网站所收集的部分公开资料来源于互联网,转载的目的在于传递更多信息及用于网络分享,并不代表本站赞同其观点和对其真实性负责,也不构成任何其他建议。本站部分作品是由网友自主投稿和发布、编辑整理上传,对此类作品本站仅提供交流平台,不为其版权负责。如果您发现网站上所用视频、图片、文字如涉及作品版权问题,请第一时间告知,我们将根据您提供的证明材料确认版权并按国家标准支付稿酬或立即删除内容,以保证您的权益!联系电话:010-58612588 或 Email:editor@mmsonline.com.cn。
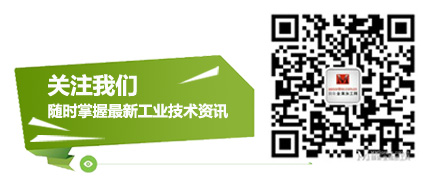
- 暂无反馈