中国模具产业发展面临各种风险
“十二五”期间,中国模具业市场份额将达2500亿元。虽然目前的模具产业具有广阔市场空间,但受外资垄断挤压产业利润空间以及内资企业自身存在种种问题的困扰,产业投资风险陡然上升。
一、外资企业正加紧蚕食模具市场
“十五”期间,我国模具企业得到快速增长,年均增速达20%。2005年中国模具行业模具销售额610亿元,比上年增长25%,加上20多亿美元的进口份额,中国模具市场容量已达800亿元左右。国际模协秘书长罗百辉预测,“十二五”期间,中国模具市场份额将达2500亿元。
近年来,国际模具制造巨头在中国投资设厂的新一轮扩张正如火如荼。德国海拉吉林落户;日本丰田模具天津设厂;芬兰贝尔罗斯公司投资兴建的深圳模具制造厂不久前正式投产,专为电信、保健、电子、汽车等行业提供高档模具产品。
外资大量独自进入,对提高我国自身的模具水平无任何帮助。外资企业拥有先进的技术和资金实力,再利用中国的劳动力和便宜的原材料,竞争优势不言而明,其一直占领的高端模具市场中国企业更加无法进入,也就是说中资企业没有机会提升档次。中资企业最怕的是自身实力尚未增强,外资企业已对中国模具市场完成垄断。
目前,我国模具企业规模仅次于日本和美国,但大多集中在中低档领域,技术水平和附加值偏低。据中国模具工业协会提供的数据,我国制造业急需的精密、复杂冲压模具和塑料模具、轿车覆盖件模具、电子接插件等电子产品模具等,仍然大量依靠进口,模具产品的进出口逆差超过10多亿美元。
二、内资企业存在的诸多问题丞待解决
全国目前共有生产模具的厂点约3万多家,其中一半以上是自产自用的。同时,绝大部分都是小型企业,近年来,模具行业结构调整和体制改革步伐加快,但设计制造水平在总体上要比工业发达国家落后许多。主要表现在:
1.行业创新能力薄弱
模具行业是技术密集、资金密集的产业,随着时代的进步和技术的发展,能掌握和运用新技术的人才异常短缺。高级模具钳工及企业挂管理人才也非常紧缺。由于模具企业效益欠佳及对科研开发和技术攻关不够重视,因而总体来看模具行业在科研开发和技术攻关方面投入太少。民营企业贷款困难也影响许多企业的技术改造,致使科技进步的步伐不大,进步不快。
2.行业整体效率低下
虽然国内许多企业采用了先进的加工设备,但总的来看装备水平仍比国外企业落后许多,特别是设备数控化率和CAD/CAM应用覆盖率要比国外企业低得多。由于体制和资金等方面的原因,引进设备不配套、设备与配附件不配套现象十分普遍,设备利用率低的问题长期得不到较好的解决。装备水平低,带来我国模具企业钳工比例过高等问题。
3.专业化、标准化、商品化程度低、协作差
模具标准化水平低,标准件使用覆盖率低也对模具质量、成本有较大影响。特别是对模具制造周期有很大影响。
4.模具材料及模具相关技术落后
模具材料性能、质量和品种往往会影响模具质量、寿命及成本,国产模具钢与国外进口钢相比有较大差距。塑料、板材、设备等性能差,也直接影响模具水平的提高。
三、外部环境分析
外资企业因为核心技术不愿外流,一般不选择合资。外资企业进入一般有两种模式:一是与其配套的企业(即客户)一起进入,其特点是专业为单一客户服务,模具品种同样单一;二是自己进入中国。外资模具公司投资中国,其目的是利用中国廉价的劳动力和便宜的钢材,赚取更多利润。
在国外企业中,模具车间是“秘方车间”,外人是不能随便靠近的。在中国设厂,外资既有资金,又有自主技术,并不需要和中国企业合资。他们只是为了降低人工成本。而且,他们把设计依然放在国外,通过网络传到其他在中国的企业
四、内部环境分析
1.国内自配率不足80%。其中中低档模具供过于求,中高档模具自配率不足60%。
2.企业组织结构、产品结构、技术结构和进出口结构都不够合理。我国模具生产厂点中多数是自产自配的工模具车间(分厂),专业模具厂也大多数是“大而全”、“小而全”的组织形式。国外模具企业大多是“小而专”、“小而精”;我国模具自产自配比例高到50%以上,而国外70%以上是商品模具。国内模具总量中属大型、精密、复杂、长寿命模具的比例只有30%左右,国外在50%以上。2006年我国模具进口总额为20.47亿美元,出口总额为10.41亿美元,进出口相抵后净进口为10.06亿美元,为净进口额最大的国家。
3.模具产品水平和生产工艺水平总体上比国际先进水平低许多,而模具生产周期却要比国际先进水平长许多。生产水平低主要表现在精度、型腔表面粗糙度、寿命及模具的复杂程度;工艺水平低主要表现之设计、加工、工艺装备等方面。
4.开发能力弱,经济效益欠佳。我国模具企业技术人员比例较低,水平也较低。不重视产品开发,在市场中常处于被动地位。我国每个职工平均每年创造模具产值约合2万美元左右,而模具工业发达国家大多是20万美元。由此而来的是我国模具企业经济效益差,大都微利。缺乏后劲。
5.模具标准化水平和模具标准件使用覆盖率低。国外先进国家模具标准件使用覆盖率达70%以上,国内模具标准件使用覆盖率只有45%左右。
6.与国际先进水平比,模具企业的管理落后更甚于技术落后。技术落后易被发现,管理落后易被忽视。国内大多数模具企业还沿用过去作坊式管理模式。真正实现现代化企业管理的还不多。
声明:本网站所收集的部分公开资料来源于互联网,转载的目的在于传递更多信息及用于网络分享,并不代表本站赞同其观点和对其真实性负责,也不构成任何其他建议。本站部分作品是由网友自主投稿和发布、编辑整理上传,对此类作品本站仅提供交流平台,不为其版权负责。如果您发现网站上所用视频、图片、文字如涉及作品版权问题,请第一时间告知,我们将根据您提供的证明材料确认版权并按国家标准支付稿酬或立即删除内容,以保证您的权益!联系电话:010-58612588 或 Email:editor@mmsonline.com.cn。
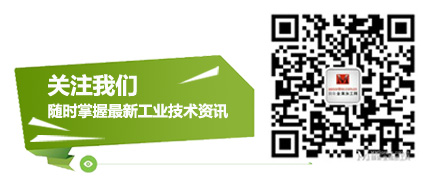
- 暂无反馈