EDM新技术在LED模具制造中唱主角
电火花加工(EDM)在金属加工中属于另类,通常在专业模具厂拥有十几台就足矣。最近听说南方有一个单位为制作LED(一种半导体固体发光器件,它是利用固体半导体芯片作为发光材料,当两端加上正向电压,半导体中的载流子发生复合引起光子发射而产生光,可直接发出红、黄、蓝、绿、青、橙、紫、白色的光)所需塑封模、镜片注塑模、引线模架模,一次采购了数控电火花成形机(NCSEDM)、数控电火花线切割机(NCWEDM)和加工中心(MC)约150台之多,其中大多是高档EDM,尤其是SEDM居多。
高、精、尖模具的大批量生产的确是一件值得关注的产业新闻,这给我们传达了什么信息呢?
1. EDM在高精尖加工领域已从可以达到精度,上升到保证达到精度的境界
硬质合金引线框架级进模曾经有IC芯片的成功经验,但如此高要求的型腔模批量生产实属首例。例如:连续加工32个L ED塑封模的点浇口锥孔(φ 0.3±0.002 5)mm,孔距公差±0.002 5mm。L ED塑封模尺寸精度<0.002mm,表面粗糙度值R a=0.1μm,底角R <0.02mm,最关键的LED镜片注塑型腔尺寸仅为1.9mm×0.84mm×0.848 8mm,呈长圆球面, 一次加工1 2 个, 轮廓度0.01mm,表面粗糙度值R a=0.06μm。此类指标无疑都处于金属加工前沿水平,尤其是为LED服务,这是一种量大面广惠及千家万户的商品,需满足严格的性价比要求。所以,此项EDM加工工艺有很高的价值,它再一次提升了EDM在金属加工中的地位,说明EDM还是一种很有潜力的创新工艺,应该在我国科技研发立项中给予更多的关注。
2. 形成以EDM为核心的柔性生产体系
形成了以EDM为核心,与加工中心、电极和工件机下调整检测仪、电极和工件库组成生产线,并由丰富的工艺管理软件串联起来的柔性生产体系。
因为LED应用面很宽,品种非常多,这样复杂的高、精、尖项目,以往是靠一群精英技术攻关,慎之又慎才能有个眉目;如今这样庞大的机群,没有一种智能的体系运作,将是无法想象的。
3. EDM的自主和智能化有极大的提升
机床可以一次采购150台,但这庞大的操作人员队伍,很难保证质量的一致性和运行的节拍。所以,这批高档EDM一定是可以自主运行,其加工性能很大程度上是不受人为因素制约的。
4. 为发展LED模具,EDM技术更上一层楼
小能量脉冲电源的脉冲生成,微能量的传递,传递过程中不变形、不掺杂,能量和火花间隙的适应,使到达工件表面的脉冲能量高度一致,才能加工出均匀的放电坑;再小的能量伺服系统和适应控制系统都能使之稳定放电,保持精确的火花间隙;在如此狭窄的火花间隙内,丰富的抬刀功能都能完成匀屑、溶屑、排屑的任务,使镜面加工可靠实施,并有一定效率。
上述难题每一项都要做深入细致的研究,尤其要真正实施等能量放电更是难上加难。能量的传输中不可能没有寄生参数,电极间隙中的电容更是无法避免的,加工越精,间隙越小,电容值越大,储能及随后的释放能量很自然会产生二次放电,就会打出一批本不需要的大坑,破坏了表面质量。这与研磨工艺一样,各档研磨粉粒度要超高一致,只要混入少许粗粒子,就会拉坏表面,使之前功尽弃。
现在可以看到的是新型专用小巧简洁的微精脉冲电源尽可能安装在靠近加工区域,如SEDM安装在Z 轴滑枕前面,WEDM安装在工作台框架底部,浸在去离子水中,仅需要有一根短短的输出电缆,这样寄生参数减至最小。此外,尽可能控制空载脉冲,即没有不放电的脉冲输出,也就是火花间隙开路时就不发出脉冲,且在坐标轴空行程或抬刀中,代以一定伺服电压,并在脉冲停歇时对间隙实施短路,清除多余能量。同时,伺服系统性能提高,前瞻控制,智能化,加速度普遍从0.1g 提高到0.5g ,进给脉冲当量从1μm降到0.05μm,伺服电动机功率加大,丝杠加粗,这样才能有精细的微抬刀,从而抑制了集中放电,使两次高抬刀之间的间隙内有更多放电点,切屑在间隙内均匀化,从而避免局部的高浓度切屑影响放电稳定,表面粗糙、平面度差及微小的电极收缩量下都会有电极的摇动,这与一般研磨能产生网纹,以去除机加工刀痕一样,平动亦可使电极上的刀花不会复制到工件上。
对应措施还不仅如此, 这是需要在极好的基础上运作的,是经过数十年的研发积累下来的EDM精密机床结构,尤其是有好的热变形对策,精密的脉冲电源,因为两档规准之间的能量差是如此之小,所以要做准非常重要,精密和智能的伺服系统,适应控制系统,操作更柔和、更细致,丰富的工艺软件--工艺数控库和专家系统,对每一种加工对象都可找到其相适应的对策,EDM供应商已可做到其每一台机床性能都高度一致,并在相当长的时间内保持不变,这张保证质量的网是如此严密,用户才可能一次性购买150台机床。
5. 市场与技术的互动推动EDM提升
是LED帮了EDM大忙,是市场指定了EDM发展方向,而不是EDM专家的意愿可以左右的。曾几何时,对EDM铣削机床投入巨大,掀起了一阵研究开发EDM铣削技术的热潮,但最后因无法赢利而不了了之;反而是不太起眼的毫米级型腔火了一把。看来只有与用户互动,与当下高新技术的产业化结合,才有EDM的春天。同时也不能放弃EDM技术发展的主动性,要从EDM自身技术发展的思路上延伸,不断扩展其优势领域,这样在市场机会到来时才能出手一搏,否则机遇稍纵即逝,所以正确的做法要两者结合起来,外看市场动向,内看自己的技术积累,一旦机会来了,就可以借船出海,推出有生命力的新产品。
当前在金属加工领域,可以采用的加工工艺有很大选择余地,每一种加工工艺的市场取决于用户对其性价比的评估,而性价比是一个非常复杂很难拿准的指标,随着时代的前进,对性能的要求会越来越细,不同的用户各项指标又有各自的权重,甚至某项指标可以达到一票否决的程度,但即使不很主要的指标亦有红线,可谓面面俱到。而价格不仅体现在购置费用,还在运行费用上,还包括时间代价(即能否缩短加工工时)、特殊人才和耗材得到的难易程度、与上下工序的衔接能否顺当,以及使用中可能的风险等。
用户性价比的取向又受到其下游用户市场的左右,风向莫测。例如,20世纪60年代,WEDM是用煤油作工作液的,到20世纪70年代用上了去离子水,效率大幅度提高,油工作液就逐渐淡出市场。但随着IC芯片引线框架硬质合金级进模的大量需要,表面质量控制超严,水基WEDM有些吃紧时,有预见的EDM业者在20世纪90年代就重新拾起油基WEDM,因为在此类小型高档冲模中,其粗加工效率低的缺陷并不明显,而精加工表面质量好,硬质合金材料完全没有电解作用的钴析出,精加工效率,尤其是微精加工效率并不低的一系列特点非常有吸引力,加上这几年种种EDM新技术的介入,精加工的潜力进一步被挖掘出来。
由于油比去离子水电阻高1 000倍,所以放电间隙小,加工内角可以达到R 0.015mm,轮廓度当然更好,尤其是表面粗糙度值达到前所未有的0.011 4μm(切割厚度为20mm的硬质合金材料,走刀20次,顺走丝方向测量),从此一种高硬度复杂型面高质量的加工工艺诞生,这对引线框架冲模的使用寿命,冲片质量的提高大大有利,已成为高档WEDM发展的趋势,当然一直坚持油基WEDM研发的厂商拔得头筹,很快推出系列产品了。
同样峰回路转的EDM项目是柴油机喷油器微细孔加工工艺。早在EDM发明初期,就用来加工喷油器孔,20世纪50~60年代,就有系列产品,但迅速被高速钻的效率打败,一度销声匿迹,到20世纪80年代才有些抬头,亦没有多大声势,使用不多,直到今天,因为低碳节能之大限所致,喷孔由大变小,孔数由少到多,向多孔、微细孔方向发展,孔径为φ 0.08~φ 0.28mm,孔加工表面粗糙度值要达到0.8~1.6μm,而且要求直孔(顺锥<0.005mm)到最大倒锥0.05mm,孔上下口部有严格控制,在±(0.002~0.003)mm之间,并按大批量生产的工序能力指数C p值1.33要求,废品率要在十万分之六以下,即要求极高的工艺稳定性。效率当然不能打折,在孔深度0.6~1.0mm情况下少于50s/孔。各项要求很全,难度不小。
当然,这几十年来EDM小孔工艺亦有了长足的进步,每孔加工都有反拷修尖、穿孔和精修多个规准。反拷是为了用长丝电极控制多次打孔后电极出尖,若穿透深度不变,则孔会变小,穿透加大会碰到喷油器内壁。过去EDM小孔仅用一档规准打透即可,如今要达到R a=0.8~1.6μm,效率肯定大成问题,而且能量太小穿孔不易稳定,过去穿孔规准用得都比较大,R a=2.5μm足矣,至少比钻孔要强一点。现在再加上一、二档精修不费多少功夫达到R a=0.8~1.6μm是有把握的,这就是用SEDM常规的摇动方式,在提高表面质量的同时还可以消除一些锥度。
要求倒锥是金属加工的难题,尤其在这种微细孔加工中更是难上加难,现在有两种方式,都是把电极丝导向器偏斜一个角度。一种是常规的主轴旋转法,电极丝是转的,结构会复杂一点,而且电极丝在形成倒锥时仅单面放电,故电极损耗不均匀,所以费丝;另一种是导向器作锥面摇动,电极丝四周均匀放电,由于两次放电的关系,实际加工中穿透的锥孔锥度会有少许偏差,锥角小一点,故而精修要采用数控插补的方式,稍为复杂一点。
喷油器微细孔加工属于EDM零件加工范畴,这在先进国家应占EDM应用范围的30%,这一方面我们还需进一步努力。
纵观EDM技术的发展,可谓是变幻莫测。曾几何时,SEDM似乎要被加工中心挤垮了;如今,在LED模具加工中它又唱上主角了,如同坐一次过山车一样,这一切来得非常突然,与当今高新技术的大发展不无关系。这种互动,相互之间的激励必将成为常态。其实,只要你一直关注着EDM的创新就可以清楚地看到它是如何一步步走来的,一切都是循序渐进的,只不过市场机会来了,让它风光了一把。今天所有的金属加工技术都处在高度动荡之中,如果你不思进取,就会被淘汰,但大多数加工工艺都会在互动中双赢、多赢,尤其是SEDM和MC的结合是如此的完美。
可以预见:明天,EDM一定会给我们带来更大的惊喜。
声明:本网站所收集的部分公开资料来源于互联网,转载的目的在于传递更多信息及用于网络分享,并不代表本站赞同其观点和对其真实性负责,也不构成任何其他建议。本站部分作品是由网友自主投稿和发布、编辑整理上传,对此类作品本站仅提供交流平台,不为其版权负责。如果您发现网站上所用视频、图片、文字如涉及作品版权问题,请第一时间告知,我们将根据您提供的证明材料确认版权并按国家标准支付稿酬或立即删除内容,以保证您的权益!联系电话:010-58612588 或 Email:editor@mmsonline.com.cn。
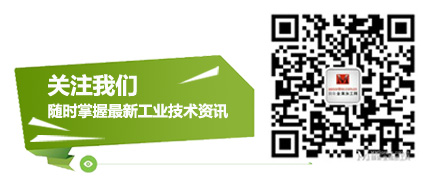
- 暂无反馈