冲模制造提高冲模寿命
冲模制造工艺就是指冲模主要工作零件;凸模、凹模、凸凹模等的加工制造方法。目前国内在冲模制造中,普遍采用的制造工艺如下:
1、电加工制模工艺
以电火花线切割和电火花穿孔成形加工为主的冲模制造工艺。
2、专用设备机械加工制模工艺
以锉锯机、仿型刨、仿型铣、成型磨与光学曲线磨加工为主的冲模制造工艺。
3、精密磨削制模工艺
以通用与专用设备进行粗加工与半精加工,用高精磨削设备完成精加工,包括使用高精度平面、内名圆磨床、座标磨床、CNC光学曲线磨床与成型磨床、NC与CNC连续轨迹座标磨床等进行精加工。
4、高效高精度组合制模工艺
以电加工法进行半精加工,用成型磨、CNC光学曲线磨、座标磨及NC与CNC连续轨迹座标磨进行精加工。
除上述四种外,还有完全用普通机床加工配以钳工锉研制模、压印法制模以及浇铸法制模工艺等,多用于一些简易、经济冲模制造。在普通全钢冲模制造中这些制模工艺已趋于淘汰。
用电加工制模工艺制作冲模是国内目前应用最广的冲模制造工艺。在高精度、高寿命、高效率的“三高”冲模制造中,精密磨削工艺占据较大优势。而高效高精组合制模工艺在国内目前使用尚不广泛,尽管其优点很多,是精密冲模制造技术的发展方向,普及尚待时日,还要一个过程。
1、冲模的电加工制造工艺
电火花穿孔是利用工件与电极之间脉冲放电产生的电蚀现象,进行模孔和模腔加工。即当电极与工件间的间隙小到一定程度时,瞬间电压升高,击穿间隙,产生脉冲火花放电。此时,能量集中,电流密度很大,产生10000℃以上高温,使金属熔化、汽化,并脱离模体,如此不停循环往复,达到加工的目的。
线切割加工原理亦相同,其主要优点如下:
(1)用金属丝作为工具电极,无需像电火花穿孔成形加工那样需要专门的工具电极。
(2)电极丝直径仅0.04~0.2 mm,现在已开发使用0.03~0.1 mm直径的电极丝,可以切割0.05~0.07mm的窄缝、R≤0.03mm的圆角以及细微的结构形状,故可加工复杂形状的凸、凹模。
(3)加工中电极线以一定速度运动,既不必考虑电极丝损耗,又可将加工中残留在切割缝中的屑末排出,有利于连续切割加工。
(4)加工效率较高且可不必采用拼块结构而能在整体模块上加工。同时,还可将凸模固定板、导板(卸料板)、凹模板等三板叠齐一次切割出所有相应模孔,孔的同轴度极好。
(5)可对淬硬模板切割加工,既可消除热处理变形,又能对各种硬金属、模具钢进行切割。
电加工制模可以大幅度缩短制模周期,能节省大量机加设备及工时,但目前,多数国产电穿孔与线切割机的加工精度、加工表面粗糙度等都达不到冲模制造的技术要求。国产线切割机与国外同类产品的技术性能相比还有较大差距。
2、电加工与精密磨削法制模的比较
采用精密磨削法加工的凸、凹模,表面粗?度值Ra可达0.025μm,通常为Ra≤0.1~0.05μm,而电火花线切割加工的凸、凹模表面粗糙度Ra值可达0.4μm,一般Ra≥1.0~2.0μm。因此,前者加工的模具工作零件精度更高,质量更好,寿命更高。
精密磨削时可通过强制冷却、控制进给量来减少磨削温升对工件表层金相组织的影响。同时,经过对磨削工具的合理选择达到最佳的相对速度,可获得镜面磨削的理想表面粗糙度。而线切割加工则不然,由于其切割的坯件已经淬硬,尽管采用微精加工回路即慢走丝切割或二次切割精加工,可以减少加工表面的电蚀层厚度,但线切割加工过程中产生的高温造成加工件表层金相组织的变化及烧蚀是难免的。此外,在电荷传递范围内的局部发热及热扩散,必然在工件加工表层出现有害金相组织。据金相显微观察,线切割加工表面不仅有肉眼可见的锯齿状痕迹,且表层约0.03~0.05mm厚为高温烧蚀的残余树枝状奥氏体组织,硬度高达HRC67~70,有显微裂纹。这样的模具在冲压加工时,多数情况下凸、凹模磨损加大、加快,冲件毛刺大。解决这个问题的办法是加强线切割后续加工的清理及研磨工序。如能用精磨除去线切割有害表层则更理想。
3、冲模工作零件表面的精加工
(1)冲模工作零件精加工与模具寿命的关系
模具费用占冲压件生产成本的比重较大,一般可超过20%~30%。因此,提高模具寿命、降低模具费用对降低冲压件生产成本有重大意义。多年来,通过使用各类模具标准,集中预制模架、模板和标准零部件、提高模具标准化、专业化与商品化的程度来压缩制模成本,已取得明显成效。但提高模具寿命,尤其通过选择和完善制模工艺来提高模具寿命,还有很大的潜力。分析制模工艺与冲模寿命的关系,可以看出选用合理制模工艺的重要性。
通常新冲模投产至失效报废要进行20~25次刃磨。冲模刃口的磨损与其表面的粗糙度有密切关系。Reihle在其著作中论证,摩擦系数μ值主要受摩擦表面平均粗糙度Ra的影响。μ值的大小与摩擦力、摩擦强度以及摩擦副产生的磨耗成正比。用精密磨削法所得刃口件的表面粗糙度Ra值可达0.025μm,一般为0.05~0.1μm;用线切割加工的刃口件表面粗糙度Ra值可达0.4μm,一般为1.0~2.0μm。目前国产线切割机仅达到Ra=1.6~3.2μm,所以,线切割加工的刃口件表面的摩擦系数μ值约为精密磨削加工的2倍以上。精密磨削可以获得镜面磨削的理想表面粗糙度,而线切割电火花放电产生的高温会造成加工件切缝表层金相组织的变化和烧蚀。此外,在电荷传递范围内的局部发热及热扩散的进行,必然在工件加工部位表层产生有害的金相组织。
由于线切割加工表面粗糙度差,在冲压加工过程中产生强烈摩擦,使粗糙波峰部位局部应力提高。线切割加工的刃口件经长期冲压工作后,由于疲劳及摩擦剪应力达到其剪切强度极限,会产生微裂纹或促使已有的显微裂纹扩展,这就是用线切割加工的冲裁模冲件毛刺大、刃口易崩裂、寿命较低的根本原因。表2是德国学者H.Becker和J.Cammann为同一冲件以线切割和精密磨削工艺制造了相同结构的冲裁模,在相同的生产条件下进行试验性生产后获得的数据,其试验研究的结论是:用电火花线切割工艺制造冲模冲出的冲件毛刺高度平均比用精磨工艺制造冲模冲出的冲件毛刺高30%,由于冲件毛刺大而使冲模的刃磨寿命及总寿命降低了约20%~30%。
(2)模具工作零件表面的精加工
按模具工作零件表面的作用可分为:自由表面、配合面、与工件的接触面三类。自由表面无精度要求;配合面既要求尺寸精度,公差控制也很严且其表面粗糙度Ra值要小,模具工作时不产生划伤。配合面绝大多数为规则的几何形体表面,以平面和圆柱面居多,用国产通用切削机床加工即可满足要求;而同工件的接触面,除了平面、圆柱面等规则的几何形体表面外,还有各种成型圆弧面、任意曲面、任意形状的三度空间体等等。由于这些表面决定了加工制件的形状、尺寸与形位精度、表面质量,故对其加工的技术要求很严,只有采用先进、合理的制模工艺才能保证模具刃口与型腔达到符合要求的形状、尺寸与形位精度,热处理硬度及表面粗糙度。
声明:本网站所收集的部分公开资料来源于互联网,转载的目的在于传递更多信息及用于网络分享,并不代表本站赞同其观点和对其真实性负责,也不构成任何其他建议。本站部分作品是由网友自主投稿和发布、编辑整理上传,对此类作品本站仅提供交流平台,不为其版权负责。如果您发现网站上所用视频、图片、文字如涉及作品版权问题,请第一时间告知,我们将根据您提供的证明材料确认版权并按国家标准支付稿酬或立即删除内容,以保证您的权益!联系电话:010-58612588 或 Email:editor@mmsonline.com.cn。
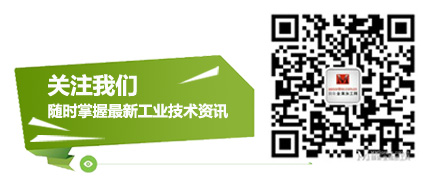
- 暂无反馈