零件精确成形技术制约我国制造业发展
零件精确成形技术是指应用先进的成形工艺、严格的几何尺寸(控形)和内在质量控制(控性)技术,生产高几何尺寸精度、高内在质量的零件或零件毛坯的先进制造技术。零件精确成形技术的先进性体现在:
(1)节约材料与能源 材料利用率一般较传统的成形工艺提高20%~40%,冷精锻精确成形可使材料利用率提高到98%以上,精确铸造成形技术也可达到90%以上。精确塑性成形技术大多数是在室温下实施的,免除了加热工序,节约了加热能量,大大减少了零件生产过程的能量消耗。
(2)免除或减少成形后续加工 净成形零件的几何形状与尺寸,已全部达到零件的使用要求,成形后即可使用,完全免除后续加工;近净成形产品,关键部位已达到使用要求,不需后续加工,一般可节约加工工时50%以上;精密成形产品,一部分尺寸已满足使用要求,其余部分留有较小的加工余量,一般可减少加工工时30%以上。
(3)提高零件的内在质量 成形过程中还同时考虑通过控制温度、压力、流体场、电磁场等外部载荷的施加,使得最终零件达到相应的性能。因此,发展零件精确成形技术,对机械工业节约资源、能源和环境友好,实现可持续发展意义重大。
工业发达国家非常重视零件精确成形技术的发展。20世纪90年代初,美国针对汽车车身生产提出了“2mm工程”目标,即一辆汽车车身所有覆盖件组装后的累积误差不超过2mm,显而易见,分配到每一个工件的误差就更小。这一工程的实施,使汽车车身制造水平上了一个新台阶。美国又提出新的目标:到2020年,塑性成形零件加工废屑减少90%,能耗减少25%,成本降低60%。日本、德国等工业发达国家也提出了相应目标。日本、德国是零件精确成形技术发达的国家,冷温精确成形件精度普遍达到8级,小型轴承环、小型锥齿轮已达到7级精度,冷温精确成形件已占模锻件的25%。我国冷温精确成形件比德国、日本两国低一级,普遍达到9级精度,少量达到8级精度,精确成形件只占模锻件的5%。德国、日本两国精确成形大多数在全自动生产线上实现,而我国全自动生产线凤毛麟角,差距较大。20世纪80年代在国外发展起来的增量制造技术(也称为快速成形技术)采用CAD数据直接驱动材料进行累加,精确制造原型或零件,使得复杂零件的制造效率大幅度提高。国外的许多企业将增量制造技术应用在复杂结构的制造上。美国通用电气公司在采用金属选区激光烧结技术制造航空发动机的复杂零部件,与传统加工方式相比,增量制造技术可以加工复杂零部件,且更省材料、时间和能源,因此,在航空航天、大型舰船复杂结构零部件制造和维护方面具有优势。
精确成形技术在汽车、航天航空、大型舰船等制造业具有广阔的应用前景,发展先进精确成形技术,对于大批量产品以及多品种、小批量、复杂性零部件的生产具有十分重要的作用,它可大大提高零件的制造水平,并且节约资源和能源。
声明:本网站所收集的部分公开资料来源于互联网,转载的目的在于传递更多信息及用于网络分享,并不代表本站赞同其观点和对其真实性负责,也不构成任何其他建议。本站部分作品是由网友自主投稿和发布、编辑整理上传,对此类作品本站仅提供交流平台,不为其版权负责。如果您发现网站上所用视频、图片、文字如涉及作品版权问题,请第一时间告知,我们将根据您提供的证明材料确认版权并按国家标准支付稿酬或立即删除内容,以保证您的权益!联系电话:010-58612588 或 Email:editor@mmsonline.com.cn。
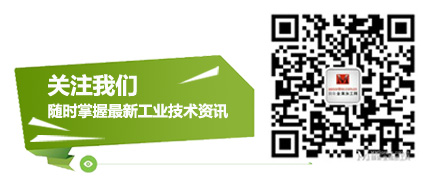
- 暂无反馈