基于数控技术的多孔类复杂壳体高精密加工方法研究
从航空液压壳体的结构特点、加工难点着手,阐述了通过数控加工技术保证液压壳体加工质量,提高加工效率的数控加工技术。
航空壳体零件加工难点分析
以某型号飞机的壳体为例,复杂的外形需要保证的尺寸近千余,纵横交错排列着各类孔近百个,孔与孔之间的位置关系非常复杂,需要通过不同的加工工艺完成零件的最终加工。因此,由于壳体零件复杂的结构设计,造成加工难点主要表现在以下几个方面:
外形结构复杂精度高
为了保证功能和零件自身需求,液压壳体类零件外形设计非常复杂,有些壳体设计既要承担油路分配又要完成部分驱动功能。因此各种型面之间的形状位置度要求高,如平面度、平行度、垂直度等往往要求达0.02mm。高精度的设计需求与零件的应力变形和加工效率形成矛盾,给机械加工造成非常大的难度,需要靠各种工艺手段去保证。
孔系相交关系复杂精度高
航空液压壳体零件对于液压油路控制非常严格,包含了绝大多数孔的类型:直孔、斜孔、相交孔、复合角度孔、台阶孔、沉孔、细长孔、异形孔等。按精度等级分:一般精度要求孔、高精度孔、形状位置要求精密孔系、精密柱塞孔系、标准堵头孔、异形电加工孔等。不同精度和功效的孔需要定制截然不同的工艺方法和加工手段。这些孔的直径范围跨度大,分布在Φ0.5mm至Φ120mm之间,其中孔径小于Φ5mm的孔径比多为1:30,如此深度的细长孔系已经远超出了标准刀具的加工范围。这些孔不仅要求精度高,而且相交关系复杂,除电火花沟通孔外,其余各孔有的是平面正交、斜交,有的是空间正交、斜交,有的同直径孔相交,也有不同直径孔相交。要想保证各孔的精度要求,加工顺序的安排就会受壳体结构的约束。某些加工部位的加工工艺性不好,需要采用特殊的刀具和加工方法来实现。
去除毛刺难度大
去除毛刺的工艺技术,通常在传统加工工艺中被忽略。但随着复杂壳体设计能力的提升和高精度设备的普及应用,去毛刺技术被越来越多的工艺技术人员所掌握。复杂的相交孔系毛刺往往用肉眼无法观测,液压壳体内如果存在加工残余物,对整个系统是致命的危害。这就需要借助于各种辅助工具和去毛刺工艺来完成。有时一道去毛刺工序就需要十余种工具。因此,如何有效去除相交孔毛刺,将成为保证壳体零件产品性能的一个关键点。
如上所述,如果在普通机床上按传统方式加工航空液压类壳体零件,一次定位装夹,仅可以加工一个型面或一个孔系,而且重复定位误差大,人为因素影响零件的质量的因素大,生产周期长和效率低,所以应将部分工作通过高精度的数控设备来完成。
壳体加工应尽量由数控设备来完成,对可以进行数控加工的部分再进行具体的分解,即根据各数控机床的加工精度、设备特点再进一步细化数控加工。如位置精度要求不高,但自身的形状、位置公差要求严格的孔、型面都可以在加工中心上完成。而相互之间有严格位置要求的孔系,型面可在精密数控机床上完成。同时为了减少精加工的余量,降低切削力对零件变形的影响,粗加工、半精加工可以由加工中心完成。
声明:本网站所收集的部分公开资料来源于互联网,转载的目的在于传递更多信息及用于网络分享,并不代表本站赞同其观点和对其真实性负责,也不构成任何其他建议。本站部分作品是由网友自主投稿和发布、编辑整理上传,对此类作品本站仅提供交流平台,不为其版权负责。如果您发现网站上所用视频、图片、文字如涉及作品版权问题,请第一时间告知,我们将根据您提供的证明材料确认版权并按国家标准支付稿酬或立即删除内容,以保证您的权益!联系电话:010-58612588 或 Email:editor@mmsonline.com.cn。
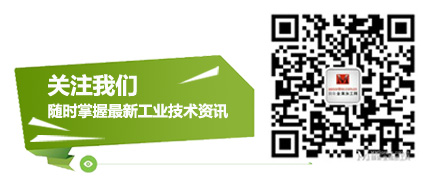
- 暂无反馈