浅谈国内药用丁基胶塞模具的发展
药用丁基胶塞在我国开始使用和发展的时间并不长,在1983年以前,我国药用包装使用的是天然胶塞,而日、美等发达国家均在二十世纪,六七十年代实现了药用胶塞的丁基胶化。出现这一更替的主要原因是:丁基胶塞在很多性能上比天然胶更能满足药品包装的要求;实践证明,丁基胶塞的气密性好,是天然胶塞的20倍;丁基胶塞的防水性能好,能有效的防止由于水份的存在,导致药品的霉变或失效;丁基胶塞的稳定性好,对所包装药品的侵蚀性小。由于天然胶塞存在影响药品质量并对人体健康造成隐患等多方面的问题,所有发达国家早已淘汰天然胶塞,广泛使用丁基胶塞。特别是近几年,我国医药产品的出口,由于封装达不到要求,而被其他国家拒之门外。1979年,我国开始研制开发丁基胶塞,1983年研制成功并通过鉴定。
我国研制丁基胶塞模具是从1985年左右开始的,当时,湖北华强从意大利引进了全套的丁基胶塞生产线,包括成型模具。引进时,一套普通的抗生素硫化模价值8万美元。随着华强丁基胶塞的全面投产和模具的更新,进口模具昂贵的现实逐步影响到正常的生产。此时,以国营红林机械厂为代表的一些厂家,开始研制、试生产丁基胶塞模具。丁基胶塞模具生产的难点在于:尺寸精度,一致性要求高,同时要求模具在硫化时高温、高压下有较高的使用寿命。由于丁基胶塞模具是一种新型行业,国内没有现有资料和经验可以借鉴。红林厂只能从材料的选用,加工工艺的探索等方面逐步摸索。到1990年,红林厂完成了抗生素模芯的小批量生产,并到丁基胶塞厂家试生产,试生产的结果表明,完全可以替代进口模芯。而且由于采用了特殊的真空淬火工艺,使模芯硬度达到HRC45-50,提高了模芯的使用寿命。实践证明机加工真空淬火模芯的使用寿命是进口模芯寿命的1-2倍。是国内冷挤压模芯使用寿命的3-4倍。但其价格只有进口模具的1/10。到1991年,红林厂生产的模具全面替代进口模具。1990年,国内丁基胶塞行业开始生产冻干类胶塞,其模具全部依靠进口,而且价格更加昂贵。一套硫化模高达20万美元,由于冻干模芯形状复杂,国外采用电火花加工,加工周期特别长,成本昂贵,国内由于设备及技术限制,无法形成批量生产。红林模具厂,结合国内实际情况,另辟奚径,探索采用镶拼结构生产冻干模芯,经过两年探索,克服了镶拼冻干模芯漏胶的顽症,使生产合格率达到95%,而其价格仅为进口模芯的十五分之一。红林模具生产的冻干模芯在短短两年时间内被国内冻干胶塞的主要生产厂家江阴兰陵与湖北华强广泛使用。2002年,红林模具生产的冻干模芯占国内市场的80%。极大地推动了国内丁基胶塞产业的发展。
随着2004年底,国家医药包装协会要求用丁基胶塞全面取代天然胶塞。国内丁基胶塞行业迅速发展,同时也带动了丁基胶塞模具的迅速发展,现在,国内丁基胶塞模具已完全国产化。但是应清楚地看到,我国丁基胶塞模具仍处于发展阶段,形状复杂的丁基胶塞模具仍需从国外进口,国内丁基胶塞模具也没有自己的行业标准,这样既不利丁基胶塞产业的发展,同时也制约了丁基胶塞模具产业的发展,在今后的工作中,丁基胶塞生产企业与模具生产企业应相互沟通和联系,共同发展,为我国胶塞与胶塞模具产业的发展共同奋斗。
声明:本网站所收集的部分公开资料来源于互联网,转载的目的在于传递更多信息及用于网络分享,并不代表本站赞同其观点和对其真实性负责,也不构成任何其他建议。本站部分作品是由网友自主投稿和发布、编辑整理上传,对此类作品本站仅提供交流平台,不为其版权负责。如果您发现网站上所用视频、图片、文字如涉及作品版权问题,请第一时间告知,我们将根据您提供的证明材料确认版权并按国家标准支付稿酬或立即删除内容,以保证您的权益!联系电话:010-58612588 或 Email:editor@mmsonline.com.cn。
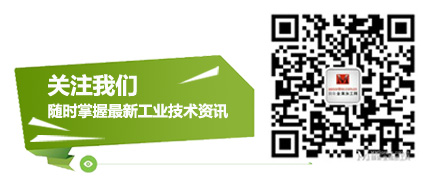
- 暂无反馈