5大产业决定15年差距 锻造业18项技术待破
“总体来说,我们的锻造行业落后发达国家15~20年。”日前,中国锻压协会常务副理事长兼秘书长张金抛出了上述言论。
尽管“十一五”期间,我国在精密锻造技术领域取得了不少成果,但精密塑性成形技术的发展还与工业发达国家存在较大差距,尤其是许多基础应用技术和关键技术还需要进一步研究解决。
差距达15~20年
为什么是“15~20年”?张金告诉本报记者,该数据是从工艺、装备制造、基础理论研究和生产管理等方面综合评价得出的。
目前,国际的先进塑性成形技术正在向数字化、精密化、轻量化和高效化以及节材、节能和环保方向发展;而先进塑性成形设备则向自动化、柔性化和集成化方向发展。
与之相比,我国锻造产业的现状则是:企业数量多,但生产规模小;设备数量多,但先进设备所占比例小,特别是高精、高效专用设备更少,例如高速镦锻机、数控冷温热锻压力机生产线、径向锻造机等,国产的基本上是空白;还有数字化设计技术应用不广,专家型专业人才力量薄弱等。
以冷锻技术为例。该技术成形精度比温锻和热锻都要高,在精密成形领域有其独特优势。它在我国的起步时间不算太晚,但发展速度却与发达国家有较大差距。到目前为止,我国生产的轿车上的冷锻件重量不足15千克,只相当于发达国家的三分之一。
同时,面对市场对大型锻件的旺盛需求,我国相关大锻件生产企业的准备也明显不足,技术积累、科研投入、生产管理、知识传承和创新严重落后。
据介绍,2007年我国对300兆瓦以上机组的汽轮机、电机的低压转子需求约在210根左右,但国内能提供的还不到16根,其余只能依靠进口解决。近年来,形势虽有所好转,但总体趋势未变。而进口的大型铸锻件不但交货期长,价格一般也比国内的高30%~50%。
有数据显示,与工业发达国家相比,我国锻造行业单位产值的能耗为其4倍,单位产值耗钢量为其1.3~1.5倍。
“强化该领域的应用基础技术、共性技术、关键技术和前沿技术的研发创新,大力推进技术转移和试验验证工作,凝聚和培养一批拔尖人才,创新管理体制和方法是缩小差距并进入国际先进行列的主要途径。”张金表示。
关键技术尚需突破
在张金看来,我国锻造领域内许多基础应用技术和关键技术还需要进一步研究解决。
比如,缺少具有自主知识产权的先进塑性成形技术及装备;基于模拟仿真的数字化成形技术还需进一步深入研究,特别是材料塑性变形特性的物理研究处于停滞状态;精确量化无损检测理论和设备落后;装备—工艺—模具分离现象严重;联合创新机制缺乏;人才队伍建设不适应技术发展和技术创新要求等,在《锻压行业“十二五”发展规划》(以下简称《规划》)中列出的、需要进一步解决的关键技术和问题足有十八项之多。
由于我国的先进塑性成形技术与装备开发能力比较弱,缺少具有自主知识产权的先进技术,致使关键产品的制造技术依赖进口,尤其是新材料塑性成形技术发展速度缓慢。如高合金化的难变形合金,其钢锭开坯难度大,而现有的锻造装备成形条件已不能胜任,国外普及的非调钢开发和应用国内才刚刚起步,这就严重制约了我国制造业的市场竞争力,迫切需要提高先进塑性成形技术与装备的水平。
与此同时,锻造行业模具寿命低也制约着生产效率的提高。我国模锻模具的平均寿命仅为国外先进水平的二分之一甚至三分之一。业内分析认为,主要是模具材料、模具热处理与国外有较大差距,另外,使用不当、操作不规范也是原因之一。因此,《规划》提醒说,锻压行业的发展需要坚持“装备—工艺—模具”一体化同步发展的途径。
在通用模锻设备方面,国内目前仍以能耗高、效率低的摩擦压力机、老式模锻锤为主,大吨位的热模锻压力机、离合器式螺旋压力机、全自动锻造线等绝大多数从国外引进,特别是冷(温)锻机械压力机目前仍处于研发、试制阶段。
“为实现节能减排、可持续发展的目标,国内现有锻造设备急需更新、改造。”张金表示,“提高国内热模锻压力机、离合器式螺旋压力机、电动螺旋压力机、冷(温)锻机械压力机、特种锻压设备以及加热炉和全自动锻造线的研发、制造水平是当务之急。”
此外,当前我国锻压行业专业化水平低,“专、精、特”不足,重复投入、低水平建设现象严重。在业内看来,这种产业结构及管理模式,造成企业只注重近期市场和局部利益。当前的许多新技术仅仅局限于科研院所研究人员的试验模拟,同企业的实际生产结合不力,导致基础数据积累不足或不可靠。
“这就需要院校与企业配合起来,使研究成果与现场控制相结合,加快研究成果向产业的转移,加强基础研究与批量生产的紧密结合,加速先进技术在产业环境下的推广应用。”张金称。
链 接
张金:五大指标决定产业差距
在中国锻压协会常务副理事长兼秘书长张金看来,衡量产业差距有五大指标:
1.人均产出,包括重量、数量和销售指标。
他举例说,“在机床行业领域,我国锻压机床行业的人均销售额约为60万~100万元人民币,而日本的人均销售额则达到了300万~500万元人民币。”
2.设备使用年数。他告诉记者,现在部分企业还在使用上世纪五六十年代、没有经过任何更新改造的加工设备。“我国锻压产业的设备淘汰时间(包括改造)是30年,而国外则是15年左右就淘汰,设备更新换代的速度很快。”
3.观念,即理念。“不得不承认,我们的很多理念并不符合工业发展的需要。”张金说,资本主义工业化已有200多年的历史,而我们从1978年改革开放到现在,工业化历程还不到40年,很多观念上的差距自己是感觉不到的。
“比如根深蒂固的‘差不多’理念。”他表示,这是农耕文化粗、散、慢特点的集中体现,而工业文化则是精、准、快,强调精确率和精准度,与农耕文化是格格不入的。
4.消费观念。在消费过程中,“过分强调高档”和“丝毫都不讲究”这两种走向极端的理念,都是不正常的,而在锻压产业内也是如此。
张金告诉记者,目前国内锻压企业出现了人才危机,高档人才和一般员工都很多,但却缺少中坚力量,导致人才培养比例不当。“在欧美的锻压工厂里,150多名员工中,只有3~5名技术人员,更多的是经过培训的高素质劳动者即中坚力量。”
他解释说,这种“中坚力量”,包括销售、车间班组长、调度、检验分析师以及受过系统正规教育、培训的劳动者。“如果这部分力量占70%以上,那么企业的发展就会不错,如果占70%~30%,那么企业还能生存,但若不到30%,企业发展就很危险了。”
在金属塑性成形专业领域,培养博士、硕士人才固然必要,但更多的需求是工程技术人员和技师,以及一大批既有一定技术理论又有实际操作技能的技术工人队伍。
5.专业化。在张金看来,这是最重要的一个指标,即工艺专业化、产品专业化和产业集中度。
“产业上的差距跟企业的产品没有关系,而取决于过程、手段,因为他们才最终决定产品质量能达到什么水平。”他说,我们现在的产品质量之所以等同于发达国家上世纪七八十年代的产品质量,就是因为我们的管理和过程控制没有做好。
声明:本网站所收集的部分公开资料来源于互联网,转载的目的在于传递更多信息及用于网络分享,并不代表本站赞同其观点和对其真实性负责,也不构成任何其他建议。本站部分作品是由网友自主投稿和发布、编辑整理上传,对此类作品本站仅提供交流平台,不为其版权负责。如果您发现网站上所用视频、图片、文字如涉及作品版权问题,请第一时间告知,我们将根据您提供的证明材料确认版权并按国家标准支付稿酬或立即删除内容,以保证您的权益!联系电话:010-58612588 或 Email:editor@mmsonline.com.cn。
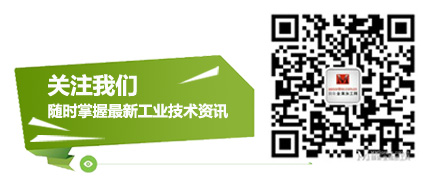
- 暂无反馈