中国模具制造企业可持续发展战略
近年来随着模具企业对先进设备的引用、先进管理理念的实施、技术水平的提升、人才培训机制的健全,使得中国模具企业的发展速度大大提高,国内模具企业要想可持续发展还必须坚持三步走战略。
模具企业要走专精特路线
定位准确是发展的基础,根据企业的技术、资金、设备等条件,准确确立自己的产品定位和市场定位是当前模具企业需要重视的问题。我国模具企业多数是自产自配的工模具车间(分厂),专业模具厂也大多数是“大而全”、“小而全”的组织形式。为了达到经营的目的,什么样的模具订单都可能接。模具专家罗百辉认为,现在国内模具企业的发展要明确自己的方向和目标,不要盲目发展,也不要注重形式主义,要做“小而专、小而精”的企业。外资模具企业大多围绕汽车、电子、医疗等产业的模具需求,确定自己的产品定位和市场定位。为了在市场竞争中求生存、求发展,每个模具厂家都有自己的优势技术和产品,并都采取专业化的生产方式。许多小企业,由于坚持走小而专、小而精、小而特的专业化生产之路,取得了良好的效益。
模具企业要发展,硬件是关键。国内很多企业为了迅速发展,购买了很多先进昂贵的设备。投入很多,但不一定会有人用。先进设备的使用不仅需要高素质的人才,同时为了达到物尽其用的目的,还要有足够的订单,否则进口设备会被闲置成为“累赘”。在条件不成熟的时候,模具企业没有必要投入太多成本在购买设备上,设备够用就可以。目前很多企业在购买ERP系统,但是这些企业必须是具备一定规模的模具企业,例如南京南汽模具装备有限公司、苏州汇众模塑有限公司等,并不是所有的模具企业都需要这样的系统。无锡国盛精密模具有限公司就曾学习外资企业先进管理理念,结合企业实际,与南京航天航空大学联合开发,研制出以PDM为核心的CAD/CAE/CAM/CAT的C4P集成系统,进一步实现了CAD/PDM/ERP的集成,提高了模具设计与制造的速度和控制能力,提高了产品的研发能力。
进入一个地域前应充分了解市场再行动。很多外资模具企业在进入中国市场前进行了详细、全面的调查和分析,以科学的数据作基础,而不是人云亦云地跟风。他们企业的选址、价格的设置都非常的科学,由此可见,成功的企业不是跟着感觉走,而是感性和理性的结合。在竞争日趋同质化的今天,产品的配套服务是企业软实力的体现,模具企业更要注重销售人员培训,注重售后服务,提供个性化服务,以创造美誉度,巩固开发市场。
模具企业要实施全方位质量管理与品牌经营
在模具行业市场竞争日异激烈的情况下,模具企业应积极主动找准占据市场的切入点,提出了“造精品模具,树民族品牌”的经营理念。为提高模具加工精度,提升产品质量,加快产出效率,模具企业要适量投资购置进口数控设备,使加工效率成倍增长,产出速度明显加快,产品质量得到提高。硬件的投入到位,为保证质量创造了有利的条件。模具企业要在全公司范围内实施“精品模具”工程,倡导“狠抓质量造精品、深化改革求发展”的质量管理理念,广泛开展并全面贯彻落实以“产品设计、数控编程、加工制造、装配调试”为主要内容的“精品模具、精品检具、精品模型”展评活动,为综合质量管理水平提高奠定了坚实基础。
模具企业还应严格执行产品质量考核制度,抓现场工序质量问题,使产品实物质量有大幅度上升。模具企业在加强现场质量控制过程中,要注重发挥下级单位质量控制的积极性、主动性、创造性,引导职能部门在质量控制方面“抓大事、干实事、多干事”。同时,现场质量检查人员要认真做到“坚持巡检、堵漏堵错、严格把关、帮助过关”,并实行“检查盖章(签字)责任追究制”,确保了加工过程中的质量。模具企业应该将产品当作一种趋势来做。这就要求企业快速、标准化并且制造流行。而要达到这些就需要企业能够建立快速的反应链,进行企业的优化管理,并能以客户为导向实现对市场的敏锐把握,练好内功,达到内外兼修。
模具企业要走联合发展道路
注重联盟的力量。中国很多企业喜欢单打独斗,但在当下的竞争环境下,一个人或者一个企业的能力是有一定局限性的。要扩大生产,要规模化,就要构筑全球化的网络,扬长避短,与供应商、渠道商、同行联盟。为适应企业发展和市场竞争的需要,模具公司还积极寻求国际合作,尝试由单纯的生产型工厂走向资本运营型企业。这是未来发展的一种趋势,已在目前产业集群(模具产业园)快速发展的过程中得到了印证。在这方面国外的一些企业做得很好,例如葡萄牙的模具企业,通过和波音公司的合作,借此提升整个国家模具品牌的传播力,同样,对于中国企业来说,这也是可以借鉴的一种方式。我们可以让国外出订单和图纸,由我国模具企业来完成设计及加工制作的具体操作,并在此过程中不断学习他们的先进技术及管理理念,加快工业化进程的改造,努力提高企业自身的核心竞争力。
一是在技术领域要加强分工协作。
近年来,国内模具尽管出口在增加,国际竞争力水平有所提升。但大多集中于中低档领域,模具的技术水平偏低,附加值偏低,部分高精模具还要依赖进口,所以国内的模具制造业在各自的领域要加强整合,没有必要过度竞争,技术开发方面要实行分工协作,相关行业及企业要登高望远,潜下心思,狠抓新技术、新工艺方的研究,逐步形成有分工、有协作、多领域、全方位的科研开发格局,推出具有自主知识产权的模具产品,在研究的过程中,我们必须克服关门主义和单打独行的做法,因为在今天全球经济一体化的条件下,我们完全可以站在前辈和同行们所积累的经验基础上做一些前瞻性的研究,而不必埋头重复做一些别人已经作过的技术工作,导致人才和资源的浪费。
二是要加快信息技术的应用。
要倾心打造柔性专业化制造平台,在不断满足顾客个性化需求的同时,提高自身的规模和专业化制造水平。大规模定制是对传统的生产模型的一种突破,它克服的单件、小批量与规模效益的两难课题,为我国模具的市场竞争能力的提升创造了条件。ERP技术的成功应用,已经在部分模具制造企业产生明显效果,为大规模定制生产提供了可能。ERP不仅对制造企业本身进行控制,而且还将管理延伸到客户和供应商,将有可能带动模具相关产业共同发展。
三是加强与供应商、协作生产厂家的合作。
必须实施全过程供应链系统管理方法,改变以往那种大而全,甚至是小而全的生产作业方法。国内模具企业传统的制造方法一般是大至型芯、型腔,小至一个螺钉、销钉都要自己设计、生产,结果造成阵线过长,批量太少,既浪费了精力和资源,也无法保证在每一个环节都能拥有高级专业化水准。现在,我们是否可以换一种思想方法,我们的模具制造商从市场上接到模具加工业务之后,不必每一个零部件都自己去做,完全可以去市场上找那些专业厂家去做模板、模架、导柱、导套、销钉、螺钉,自己只加工最专业的模具的型芯、型腔组件,甚至,就是在核心技术中,也只做专业技术要求最高的一部分,可以想象,由于动员了社会的力量和资源,我们的规模更大了,我们专业化水平更高了,随着竞争力的加强,我们市场份额也会扩大,我们分流部分零部件加工所造成的损失将会在更大的市场空间内得到补偿,所以,我们的模具加工业,千万不要再做那种事必亲躬、老死不相往来的闭塞型生产研制之路,后工业化时代更大规模的社会化生产为我们分工合作创造了极为便利的条件,我们必须通过更加细致的社会分工来提高效率和专业化水平,从而提高模具制造业的整体经济效益和竞争能力。
四是要加强行业协会的指导和服务功能。
我国模具制造业在制造理念、制造方法、设计水平、生产装备、新材料以及工艺学等诸多方面与国际先进水平相比较还存在相当大的差距。由于模具制造过程既涉及到高技术工艺的运用,又涉及到新材料应用研究,这些都是跨行业、跨地区,专业技术要求非常高的研究领域,如果仅仅靠某一个模具制造企业甚至单单依靠模具行业本身都是无法得到有效解决的难题。要解决这些难题,我们的行业协会必须要发挥见多识广、联系广泛,具有宽泛视野和强大影响力的优势,集中听取各模具生产企业反映的一些技术难题,组织行业内部集体攻关或者委托其他科研院所加紧研究,为企业生产经营活动提供必要的帮助和指导。目前的状况是竞争使企业在技术上处于一种无序的研发状况。很多企业热衷于新产品的开发而忽视了一些基础研究工作,譬如新材料应用、热处理工艺以及表面处理工艺。新加坡一个制造商在江苏办了一家合资企业,模具加工在国内生产,但最后却要空运到国外进行离子注入表面处理,成本增加了,但模具的利润却可以提高十几倍甚至几十倍。由此可见,我们不能在低水平领域过多的相互倾轧,而是要在行业协会引导下,开展跨地区、跨部门、跨行业的合作,共同把我们模具制造业的基础夯实。
五是要放大技术附加值在报价策划中的比重。
模具与其他产品在生产制造过程中存在差异,首先它是一种工作“母机”,是一种特定的工艺装备,生产过程中表现出典型的差异化特征,既需要现代化装备作保证,又需要大量具有特殊经验的人员的手工劳动,所以,它的技术附加值理应是较高的。我们国家出口的模具目前在欧美市场具有较强的市场竞争力,总体上是基于价格偏低优势。据相关报道称,美国正在对我国的模具出口业务进行反倾销调查,尽管,我们国内的模具企业可以坦然接受反倾销调查,因为我们国内销售的模具比出口模具价格更低,但是,从另外一方面也反映出,我们在与国际接轨过程中可能在技术附加值报价策略上过于保守,我们国内模具制造厂商完全可以对这种既有技术含量,又有大量手工劳动的特殊商品价格定的更高一些。
目前中国模具工业已进入了高速的发展时期,中国模具市场前景广阔,模具制造企业要有信心把握机遇,在寻求差异化的路上不断创新,迅速提升中国模具的价值和影响力,通过国内外模具技术交流与经贸合作,促进发展、实现共赢。
声明:本网站所收集的部分公开资料来源于互联网,转载的目的在于传递更多信息及用于网络分享,并不代表本站赞同其观点和对其真实性负责,也不构成任何其他建议。本站部分作品是由网友自主投稿和发布、编辑整理上传,对此类作品本站仅提供交流平台,不为其版权负责。如果您发现网站上所用视频、图片、文字如涉及作品版权问题,请第一时间告知,我们将根据您提供的证明材料确认版权并按国家标准支付稿酬或立即删除内容,以保证您的权益!联系电话:010-58612588 或 Email:editor@mmsonline.com.cn。
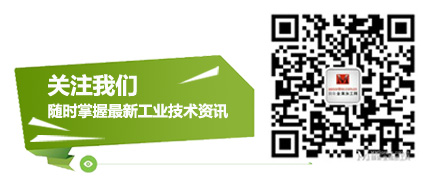
- 暂无反馈