游离磨粒加工技术的研究现状及发展
1 引言
游离磨粒加工技术是历史最久而又不断发展的加工方法,它是不切除或切除极薄的材料层,用以降低工件表面粗糙度值或强化加工表面的加工方法,多用于最终工序加工。近年来,在这些传统工艺的基础上,出现了许多新的游离磨粒加工方法,如磁性研磨、弹性发射加工、流体动力抛光、液中研抛、磁流体抛光、挤压研抛、磨粒喷射加工等。
2 游离磨粒加工技术的分类
2.1 传统的研磨和抛光
研磨是一种常用的光整加工方法,研磨加工的机理是利用附着或压嵌在研具表面上的游离磨粒,以及研具与工件之间的微小磨粒借助于研具与工件的相对运动,切除下微细的切屑,以得到精确尺寸和表面粗糙度值很小的加工表面。研磨加工的切削作用一般分为两种情况,一种是滑动切削,即两体加工,镶嵌粘附在研具上的磨粒,与工件相对运动而产生推挤作用,使工件留下带有擦痕的光滑表面;另一种是由研具与工件之间的磨粒旋转作用而产生的滚动切削,即三体加工,研磨开始仅有少数大颗磨粒切削,效率并不高,且比压大,随后很快被压碎变为许多小磨粒一起参加工作。磨粒一方面切削工件,另一方面继续被压碎,研磨效率基本上不变。持续一段时间后,由于磨粒愈益细化,研具与工件之间的间隙变窄,切屑堵塞于磨粒之间的缝隙,研磨效率急剧下降,工件表面变得非常光滑。
抛光也和研磨一样,是将研磨剂擦抹在抛光器上对工件进行抛光加工。但是,抛光使用的磨粒是1 以下的微细磨粒,而抛光器则需使用沥青、石蜡、合成树脂和人造革等软质材料制成,即使抛光硬脆材料也能加工出一点裂纹也没有的镜面。
2.2 浴法抛光
浴法抛光(Bowl-Feed Polishing)早在六十年代就已出现,当时美国为发展深紫外波段的光学,需要平面度和粗糙度很好的光学元件。采用这种方法在熔石英平面上获得了0.5nmRMS的光滑表面,而当时使用的常规方法,只能获得1-4nmRMS的表面。在浴法抛光中抛光液浸没了磨盘与工件的交接面,与传统的常规抛光类似,工件在旋转的沥青盘上水平摆动,并绕自身旋转,保证工件上每点与沥青盘上每点随机接触,使工件被均匀去除。由于离心力及重力的作用,抛光液中的磨料颗粒被甩到边缘并沉到桶底。抛光过程分两个阶段:抛光开始时使用搅拌棒,让磨料在溶液中均匀分布,这样就不断有磨料颗粒沉淀在沥青盘上。磨料有自锐性,研磨破碎后露出新的锋利边缘,仍有磨削作用,但粒度更小了;此时,工件与沥青盘已很好地吻合,磨料粒度已足够小。移去搅拌棒,使抛光液中磨料沉入桶底,沥青盘上的磨料逐渐减少,有效抛光液浓度不断降低,由于抛光中磨料颗粒不断被研碎挤入沥青中,沥青盘表面变得越来越光滑,嵌入其中的磨料微粒不断锐化并变得越来越小,尤如一把把极小的车刀,持续微量地车削工件表面,使其粗糙度降低。由于工件浸于液体中,工作时液体的作用使磨盘与工件的接触更柔和;大量液体的存在保证了磨盘表面局部温度的均恒,使磨盘不易变形,抛光小环境相对稳定,这样就有希望获得高面形精度的表面。
2.3 磁力悬浮研磨
磁力悬浮研磨是基于磁性流体中非磁性磨粒受磁场作用时,会产生向低磁场方向悬浮的现象而研究出的光整加工方法。借助活性剂的作用,使铁氧体微细粒子稳定地分散在油和水等溶液中而构成胶态流体。在受磁场作用时,由于磁性流体中铁氧体的强磁性微细粒子的作用,磁性流体显示出被吸向高磁场一侧的性质。如果在磁性流体中存有非磁性体,在受磁场作用时,非磁性体则与磁性流体相反,产生趋向低磁场一侧的现象。研磨加工通常使用的磨粒是非磁性体的。应用这种磁力悬浮现象进行的研磨就是磁力悬浮研磨法。它有以下几个特点:由于磁悬浮力的作用,使作用于研磨面的磨粒数量增多;由于磨粒由流体支承,因此磨粒的支承富有弹性。另外,加工压力是由磁悬浮力所赋予,故作用于每个磨粒的加工压力与磨粒的数量无关;由于磁性流体的热传导率很大,因此可以控制加工点的温升; 越接近磁铁,作用于磨粒的磁悬浮力越大。因此,对工件形状还有修正效果。
2.4 磁粒光整加工
所谓磁粒光整加工(Magnetic Abrasive Finishing,简称MAF),就是利用磁场通过强磁性介质产生的磁作用力作用到磁粒上,使磁粒对工件进行微切削加工的方法。圆柱表面磁粒光整加工原理,将工件放置在由电磁铁N极和S极构成的磁场中,在电磁铁与工件之间填充磁性磨粒,当对电磁铁通以直流电时,在N、S两极之间便产生磁场,磁性磨粒被磁极吸引,在磁力的作用下,磁粒沿磁力线整齐地排列成刷子状,并对加工工件表面形成一定的压力,当磁极与工件之间产生相对运动时,磁刷扫过工件表面,从而对工件待加工表面进行研磨、去毛刺、提高工件表面硬度等过程的光整加工。该加工方法改善了工件表面的应力分布状态,延长了工件的使用寿命。磁性磨粒由纯铁粉(Fe)作为载体,加入一些Al2O3或SiC等磨粒混合制成。
2.5 磁流变抛光
八十年代中期由Kordonski发明的磁流变抛光(Magnetorheological Finishing MRF)是使用磁场改变磁流变液体的粘度,磁流变液体不断地在泵之间循环,电磁使液体中的固相之间不断交替,磁流变抛光液加到旋转轮边缘并被带进抛光区,工件装夹在数控机床上并浸在液流里,和弹性发射加工及其它数控加工一样,材料去除量是由给定位置的驻留时间决定的。砂轮边缘和抛光表面形成楔形间隙暴露在磁性域中,在砂轮边缘产生磁性变粘的磁流变抛光液通过楔形间隙,这种抛光液在接触区产生剪切压力并去除工件表面材料。
由于去除率和流体粘度有关,因此去除率是很稳定的。通过监测和控制使流体粘度保持在±1%以内。通过改变砂轮速度,零件在磁流体中位置和磁场强度来调整去除率,产生光滑无损伤表面的同时得到相对较高的稳定的材料去除率。不同于传统抛光,磨粒法向载荷能划伤工件表面,磁流变抛光依靠剪切模式去除材料,磨粒在法向方向不受任何力的作用。
2.6 磨粒喷射加工
磨粒喷射加工(Abrasive Jet Machining)是一种使用游离磨粒以运动方式进行的磨料去除加工。其工作机理是用高速射流(气体、液体或气体与液体的混合物)喷射磨粒,磨粒以很高的速度冲击或抛磨工件表面,从而去除工件表面材料。磨粒喷射光整加工设备是由四部份组成:存储、混和和输送磨料的装置;工作室;吸尘器;供应干燥清洁气体的气源。经过干燥和油水分离的压缩空气到达混和室与来自磨料喂入装置的磨料相混和,压缩气体的压力和流量通过调压阀控制,磨料喂入量通过调节振动器的振幅和频率控制,经混和后的磨料流由喷嘴喷出,直接作用到被加工工件表面。真空吸尘器与工作室相连,以吸除废屑及加工后的磨料流尘埃。气源的压力至少要 700~900Kpa,气体含水量要小于万分之五,可以用瓶装二氧化碳或氮气作为干燥气体的气源。喷嘴端部通常用碳化钨或蓝宝石制造,其寿命与所用磨料的种类及压力有关。磨料微粉必须干净、干燥和仔细分选,磨料不能回用。
喷射加工的特点:磨粒喷射加工是冷切削,不影响和改变热敏感合金的特性,在加工过程中,工件表面不产生加工应力和热损伤;磨粒喷射光整加工后的表面有散乱的纹理,表面粗糙度 值在0.15~1.6之间,为防止在加工表面形成弯月形洼坑,喷嘴必须作不停的运动;磨粒喷射所用磨料粉末应仔细分级筛选,以保证形成合适的射流;压缩气体不能用氧气替代,因为氧气与工件碎屑或磨料相混和时可能发生强烈的化学反应,此外,压缩气体要经过过滤和干燥,以除去油和水分;喷射加工要在防尘罩内或在吸力足够的吸尘器附近进行。
2.7 弹性发射加工
弹性发射加工(Elastic Emission Machining)是由日本Mori Y.在1976年发明的"原子级尺寸加工方法"。其加工系统是由旋转轮、加工液和工件组成,工件和旋转轮都浸漬在加工液中,旋转轮通常是由聚氨脂或橡胶等软质材料制成。加工液由水和微细磨料(亚微米或几十个纳米)混和而成,通过控制法向载荷使旋转轮和工件之间的间隙在1左右,当旋转轮旋转时,旋转轮与工件之间的楔形间隙就形成了类似于流体动压润滑现象。微细磨粒与水的混合物在流体动压力、旋转轮旋转所产生的高速气流及离心力的作用下,进入旋转轮与工件之间。微细磨粒与工件在狭小的空间内接触,产生一种原子结合力,当磨粒在流体剪切应力的作用下离开时,使工件表面产生原子级的极微量的弹性破坏,实现工件表面层原子的分离,从而去除工件表面材料。由于微细磨粒冲击工件表面所产生的能量不足以使工件表面材料产生塑性变形,而只是原子间结合的微小弹性破坏,所以得到了原子级的精度和没有缺陷的表面。微细磨料在旋转轮的约束下和工件表面接触,通过控制旋转轮的运动就可以得到十分理想的加工精度。弹性发射加工利用游离磨料和工件表层材料原子相结合,然后在加工液动压力和剪切应力的作用下,磨粒离开结合表面,从而实现对工件的微去除加工。弹性发射加工和传统的加工方法相比有以下两个显著的特点:加工机床的刚度比传统的加工方法要求低;加工过程不受温度变化和机床振动的影响。根据加工条件(磨料尺寸、硬度、介质黏度、旋转轮速度、加工液剪切应力、加工时间、法向载荷大小)和工件材料的不同,可获得纳米级精度和表面粗糙度值,没有热损伤和表面变质层。
3 游离磨粒加工技术的发展趋势
随着技术的进步和对精密表面需求的增加,游离磨粒加工技术获得了长足的发展,原子级超光滑表面获得已不再困难。在众多加工方法中,依赖于精细磨粒的抛光技术仍是主流,其特点是加工效率高,设备简单,成本低。如采用浸液抛光方式、使用高精度的抛光模、采用软质材料抛光液、重视抛光液的化学作用和抛光粉的弱机械作用,实现化学机械抛光等。当今超游离磨粒加工技术应用领域的迅速扩大,其正向降低制造成本、提高加工效率的方向发展。随着材料科学的发展,采用特殊材料的机床将具有更高的精度和稳定性。电子学的进步则使机床控制技术得以极大提高。这些都使材料的去除量达到纳米级成为可能。利用场效应辅助抛光是游离磨粒加工的另一发展趋势。通过控制工件所受的加工压力来操纵材料的去除,最终达到弱力乃至微力加工是提高超光滑表面加工效率的一条重要途径。
4 结束语
随着科学技术的进步,开发出越来越多的新型材料,对材料的加工精度要求也越来越高。游离磨粒加工技术作为一种精密加工技术,其具有的独特优势使其可以在各种难加工材料的加工中发挥作用,尤其是微磨料喷射加工技术的发展,对抛光技术的研究和工艺的成熟将起到推动作用。
声明:本网站所收集的部分公开资料来源于互联网,转载的目的在于传递更多信息及用于网络分享,并不代表本站赞同其观点和对其真实性负责,也不构成任何其他建议。本站部分作品是由网友自主投稿和发布、编辑整理上传,对此类作品本站仅提供交流平台,不为其版权负责。如果您发现网站上所用视频、图片、文字如涉及作品版权问题,请第一时间告知,我们将根据您提供的证明材料确认版权并按国家标准支付稿酬或立即删除内容,以保证您的权益!联系电话:010-58612588 或 Email:editor@mmsonline.com.cn。
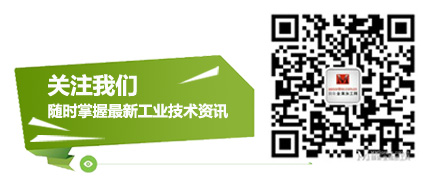
- 暂无反馈