绿色干切削技术及应用
前言
环境和资源问题是当今和未来人类社会实现可持续发展需要解决的问题。随着高速加工技术的迅猛发展,加工过程中使用的切削液用量越来越大,虽然切削液有利于降低切削温度、延长刀具寿命、提高断屑和排屑能力,但若将未经处理的切削液直接排入江河湖海,就会破坏生态环境。此外,由于切削液的润滑剂中含有大量亚硝胺、多环芳香烃和细菌分解产物,直接接触将导致多种皮肤病、眼疾、呼吸系统疾病等,直接影响到操作者的身体健康。另据美国企业对加工成本的统计,在零件加工总成本中,切削液费用约占16%,而刀具的费用只占总成本的4%。近年来,世界各国为了贯彻环保政策、降低加工成本,大力研发及推广应用干式切削加工技术。到2003年德国制造业将有20%以上采用干切削技术,据测算:它的总制造成本就可降低1.6%以上,干切削技术已成为金属切削加工的重要发展方向。本文在分析干切削加工特点的基础上,提出了干切削对刀具、机床等工艺过程的具体要求,讨论了干切削的具体应用。
1 干切削加工中的刀具技术
干切削加工是在没有切削液的条件下创造具有与湿切相同或基本相近的切削条件。因此,刀具是否能承受干切削时巨大的切削热是实现干切削的主要问题,一般可采取的措施有:
1.1 选择适合干切削加工的新型刀具材料
刀具在切削加工过程中,要承受很大的压力,同时,由于切削时产生的金属塑性变形以及在无切削液的情况下刀具、切屑、工件相互接触表面间将产生更强烈的摩擦,使刀具切削刃上产生极高的温度和受到很大的应力,在这样的条件下,刀具将迅速磨损或破损,因此干式切削刀具材料应具备更高的耐热性和热韧性,良好的耐热冲击性、抗粘结性及高的耐磨性。常用的有高韧性和高硬度兼备的纳米级细颗粒硬质合金,耐热性和高耐磨性好的粘结硬质合金,涂层硬质合金,陶瓷及金属陶瓷,立方氮化硼(CBN),聚晶金刚石(PCD)等。近年来,还在Al2O3基体中添加20%~30%的SiC晶须,它能阻挡或改变裂纹发展方向,使刀具的韧性大幅度提高,是一种极具发展潜力的干式切削加工用刀具材料。
1.2 采用涂层技术
对刀具表面进行涂层处理实际上类似于冷却液的功能,它可产生隔热层,使热不会或很少传入刀具,从而能在较长的时间内保持刀尖的锋利和坚硬。一般应采用多层涂层,以达到最佳的热防护,在常规涂层中TiAlN是干式加工中改善热绝缘的首选涂层,但是常规采用的单层TiAlN涂层的附着性差,不具备最优性能,在干式加工的动应力下,单层TiAlN有产生裂纹破碎的倾向,会从刀具上剥落。多层TiAlN涂层,其组织可抑制表面层从刀具基体面上碎裂,对改进性能非常有效。德国Guhring公司的Firex多层硬涂层由不同的TiN和TiAlN的超薄涂层交替构成,可得到很好的结果。
目前,滑性“软”涂层的研究和使用是干切削刀具涂层技术的另一主要发展趋势。第一,采用新的沉积技术将硬质合金、钢甚至铝作为涂层来降低摩擦系数。第二,采用“超软”涂层,如德国的Guhring公司开发的“Movic”软涂层工艺,它实质上是固体润滑剂(MoS2)和刀具相结合后在刀具表面形成了良好的滑动表面,因此具有较好的润滑功能,在切削加工中可使切屑与刀具排屑槽之间产生的摩擦最小(一般只有0.01左右)。可有效避免积屑瘤的产生并能减小切削力和降低切削温度,提高刀具耐用度。试验表明:无涂层丝锥只能加工20个螺孔:采用TiAlN涂层的丝锥可加工1000个螺孔:用MoS2涂层后可加工4000个螺孔。第三,采用软/硬组合涂层,即先在刀具上涂上“硬”涂层(如TiN)后再在其上涂上“软“涂层(如MoS2),采用这种组合涂层的钻头在钻削灰铸铁发动机缸体上的深孔时,刀具寿命高达1600min,而硬涂层钻头,如TiN和TiCN涂层的钻头寿命只有19.6min和44min。另一种很有前途的涂层新工艺叫等离子注入,它是用“射入”金属离子的办法有效地形成点阵结构,并可深入刀具基体内部,这种方法能提高刀具硬度但不会改变其尺寸,这一点对精细刀具的干式切削尤为重要。
1.3 合理选择和刃磨刀具几何的形状
干切削加工中,由于缺少了切削液的润滑和冷却的主要作用,因此,有效散热是实现干切削要解决的主要问题,优化刀具几何形状时应满足:第一,减小刀具和工件的接触面积,如,麻花钻要减小倒锥度、刃带及螺旋角。第二,为防治和阻断积屑瘤的产生要在可能形成积屑瘤的表面有最充分的润滑。
此外,干式切削使刀具切削刃承受着很大的机械应力和热应力,为增加切削刃强度在刃磨时一般宜采用油石珩磨,这可避免在干式加工的应力作用下刀具可能出现的裂纹,磨损及崩刃。但对于刀具基体能产生较锋利的切削刃的刀具,如:超细晶粒硬质合金及金刚石刀具只应少量珩磨。
2 合理选择配置机床
用于干切削的机床应主要考虑切削热的散发及热切屑和灰尘的排除。一般应尽可能采用超高速机床,这种机床95%以上的切削热会被切屑带走,并可降低约30%左右的切削力,工件可基本保持在室温状态下进行加工。除此之外,机床结构应有利于吸尘和排屑,在保证主轴、导轨等精密运动部件有良好的密封情况下,最好能采用真空吸尘装置将悬浮颗粒及烟气排出。若考虑到导轨防护盖板和机床结构,斜角朝上的方法或许是更有效。
3 采用合理有效的冷却方法
干式切削就是不用切削液,利用特定的刀具及其相关加工技术获得理想加工效果的一种加工方法。就这从根本上解决了切削液造成的负面影响,但在有些加工场合排屑极为困难,刀具和工件难以充分冷却,润滑条件差,严重影响已加工表面质量。为解决上述问题,必要时还可采用准干式切削方式,即在加工中采用风冷或微量冷却润滑等方法。干式切削时,可采用喷气冷却系统,它是一种低温切削方法,它所使用的冷却气体是由液态氮或其他方式在热交换器中冷却过的,其温度可低达-45℃,冷却气体直接喷射到切削区,并可根据加工要求调节气体的温度、流量参数以满足加工要求。利用液氮的另外一种方法是间接利用,美国标准和技术国际研究所Evans利用液氮冷却刀杆或夹具,用金刚石刀具切削不锈钢时,加工表面粗糙度低于Ra0.025,并且大大减少了刀具的磨损。除此之外还可采用“切削液最小量”技术,即给切削过程很少量的切削液以达到降低切削温度、及时排出切屑的目的。一般当机床工作在最佳条件时,切削液消耗量应在50mL/h以下,而采用正常射流冷却时的切削液耗量可能会超过6L/min。
准干式切削技术的最大好处在于,如果使用恰当,刀具、工件和切屑可保持干燥,这就避免了废物处理的麻烦。目前,此技术多用于铸铁、钢、铝合金上进行钻孔、铰孔和攻丝加工以及深孔钻削和铝合金的端面铣削等。
4 干切削加工技术的应用
随着刀具材料、涂层技术、刀具结构和工艺装备的发展及对环境管理和监测有严格规定的ISO和JIS14000系列标准的出台,美国、德国、日本等国家已对干切削进行了大量的研究并应用于实际生产,取得了明显的经济效益和社会效益。为了在今后国际机械行业竞争中立于不败之地,我国一些科研所也已经开展并取得了一定的成果。目前,干式切削已应用于铸铁、铝、镁及钢、高合金和钛、铝合金等材料的切削加工。
铸铁材料是典型的干式切削加工材料,美国LeBLond MaKino公司研发的“红月牙”(Red Crescent)铸铁干式切削技术就是利用陶瓷和CBN刀具进行高速加工。由于其切削速度和进给量很高,产生的热量很快聚集在刀具前端,使该处的工件材料达到红热状态,其屈服强度下降,可将金属切除率由16cm3/min提高到149cm3/min,极大地提高了切削加工效率。
德国Guhring公司的M-涂层钻头,即在硬涂层外面再加一层软涂层的钻头与采用TiAlN涂层的钻头在相同切削条件下寿命可提高近一倍。
日本坚藤铁工所开发的KC250H型干式滚齿机,采用硬质合金滚刀,冷风冷却,微量润滑剂润滑,进行了高速滚齿,与传统的高速钢滚刀的湿式滚齿机(KA220型)相比,加工速度提高了2.3倍,齿轮精度也得到了明显提高。
我国哈尔滨理工大学机械系对干式切削GCr15材料进行了一定的研究,并通过对不同硬度GCr15的切削力、切削湿度、已加工表面质量的切削试验研究,得到了被加工材料硬度对上述各量以及切屑形态、硬度、变形系数的影响规律,提出了临界硬度的概念,并得到了50HRC为区分硬态切削与普通切削GCr15的临界硬度。
5 总结
干式切削加工是一种理想的绿色制造工艺方法,虽然目前干式切削加工的应用范围不是很广泛,但对于它的研究已成为目前的热点之一。干式切削技术是一项系统工程,并不是简单地停止使用切削液就能实现的,而必须从刀具、机床和工件等各方面采取一系列合理、有效的措施,才能得以顺利实施。我国对于干切削技术的研究尚属于开始阶段,但从长远的发展角度去看,干式切削的应用将是必然趋势。
声明:本网站所收集的部分公开资料来源于互联网,转载的目的在于传递更多信息及用于网络分享,并不代表本站赞同其观点和对其真实性负责,也不构成任何其他建议。本站部分作品是由网友自主投稿和发布、编辑整理上传,对此类作品本站仅提供交流平台,不为其版权负责。如果您发现网站上所用视频、图片、文字如涉及作品版权问题,请第一时间告知,我们将根据您提供的证明材料确认版权并按国家标准支付稿酬或立即删除内容,以保证您的权益!联系电话:010-58612588 或 Email:editor@mmsonline.com.cn。
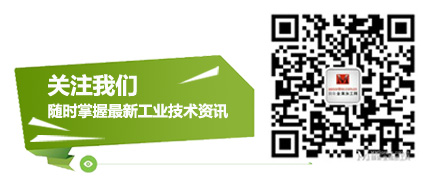
- 暂无反馈