压铸镁合金模具
在大多数情况下,压铸镁合金生产的产品与其他合金压铸件相类似。镁合金压铸模具也和铝、锌合金压铸模相似。但是由于镁合金不同于铝合金的一些特性,在设计压铸模时给予充分考虑,才能设计出合理的压铸模具,从而高效、经济地生产镁合金压铸件。
一、镁合金的特性
①质轻镁的比重只有1.8G/CM3,铝合金的比重为2.7G/CM3,镁合金比铝合金轻30%,比钢轻80%。所以,汽车及手提电子产品中镁合金已成为零件制造成理想材料。
②强度镁合金在金属及塑料等工程材料中,具有极佳的强度/重量比。
③压铸性在保持良好的结构条件下,镁合金允许铸件壁厚最小达到0.6mm,这是塑料在相同强度下无法达到的。铝合金的压铸性能也要在1.2-1.5mm以上时才能与镁合金相比。镁合金较易压铸成型,适合大批量压铸生产(生产速度可达铝的1.5倍)。此外,镁合金模的磨损也较铝为低。
④减震镁有极好的滞弹吸震性能,可吸收震动和噪音,用作设备机壳可减少噪音传递、预防冲击和防止凹陷损坏。
⑤刚性镁的刚性为铝的2倍并比大部分塑胶为高。镁有良好的抗应力阻力。
⑥高电磁干扰屏障镁合金有良好的阻隔电磁波功能,适合生产电子产品。
⑦良好的切削性能镁比铝和锌有更好的切削性,使镁成为更易切削加工的金属材料。
⑧镁合金的比热容较小,合金液的冷却速度快。
⑨镁合金和模具钢材的亲和力小,不易粘附模具。
根据镁合金的以上特性,下面将镁合金和铝合金在设计制作上作一些对比。
二、模具设计
压铸模具是一种复杂的设备,须完成多项功能。其决定零件的大体几何形状,并对每啤货之间尺寸偏差有重要影响。使用固定或移动的芯子增加了压铸的灵活性,可以压铸出复杂的较精密外形的零件。流道和水口系统的几何形状决定模具的填充性能。模具的热条件决定零件固化用及其微观结构和品质。在大量生产时,模具的导热性能决定周期时间。并且模具具有压铸件顶出系统。
三、模具材料
模具组成模穴的部分和熔化金属直接接触,必须由能经受热冲击的钢材料制成。最常用的是H13钢或和其具有相似性能的材料。为保证大量啤货以后的表面质量,必须使用含硫量的优质钢材。为改善机械加工性能,供应模具制造商的钢材通常处于具有球形碳颗粒的软化退火状态。在机械加工以后,模穴部分经过淬火及退火,使硬度在46-48HRC范围以内。
只有模具的模穴部分和特殊零件才需要使用H13钢,这些部分一般占整个模具重量的20-30%。模具的其它部分使用低碳钢的中碳钢制造。对于几何开关相对简单的较小压铸件,以常使用标准化模块的模具。
镁合金和铝合金相比具有更低的热容,其铁含量也很低。因此模具具有更长的寿命。
四、零件寿命
压铸件的质量取决于很多因素,包括合金的材料性能,生产参数,模具和零件的设计。零件设计者应该和模具设计者紧密合作,让零件设计者知道压铸生产的优势和局限。
部件厚度
较小的部件厚度容易达到所要求的机械性能,镁合金良好的填充性能,可以使压铸件的厚度少于1mm,常见的壁厚在2-4mm之间。
均匀壁厚
为避免固化时的局部热点,零件的壁厚应尽可能均匀。由于固化时的收缩,局部热点会造成气孔和气穴的形成。
容易的模具填充
模具的填充时间一般是10-100ms,零件的设计应有助于平稳填充,镁合金的填速度较高,边缘和拐角处应为圆角。
使用加强助
应使用加强助加强零件的强度,而不是通过增加零件的厚度。设计中应避免长筋,防止合金在冷却凝固过程中因收缩不一致而产生应力和裂纹。
出模斜度通常推荐的出模斜度为2-5°,也可采用度为1-3°的设计。由于镁合金与铁的亲和性较低,加之优良的热收缩特性,有时甚至可以采用零脱模斜度,当设计壁和型芯时,较小的起模斜度能够大幅度减少压铸件质量。
五、尺寸稳定性
压铸是精密的生产过程,然而很多因素却可以影响压铸件的最终尺寸变化。尺寸变化可分为线性变化,模具间的移动,分模线、铸件和模具翘曲,压铸参数,芯子和出模斜度。必须记住零件的最终变化只是部分取决于模具精度,线性尺寸变化是由下列因素引起:模具温度的正常波动,注射温度,冷却速度,铸件应力释放和模具精度。以上因素除模具精度外,和模具的设计和制造没有关系。为减少最终产品的尺寸变化,必须严格控制生产工序。
六、水口、流道、排气孔
注射系统对于压铸件质量是非常重要的,以下是设计水口系统的注意事项:
①水口系统必须和压铸机容量相适应,使模穴有必要的填充时间。
②水口可以是不同的几何形状,扇形或分枝的。为防止湍流,水口的金属流体应该是平行或分枝的。
③设计的水口应使流动距离最短。
④相反方向流动的液体金属不应在薄壁区域相遇。
⑤由多个水口填充的零件应同时填充。
⑥溢流应用来除去氧化物和残留的润滑剂,并加热模具较冷的部分。
⑦应用连通至模具表面的排气孔除去模穴内生成的气体。
⑧水口和溢流的设计应可以避免在二次加工时形成锯齿纹。
七、加热、冷却系统
模具在生产过程中维持较稳定的温度范围,有利于产品质量和生产节拍的稳定,同时也由于波动小,温度疲劳降低,延长模具寿命,因此,模具设计时要充分考虑加热、冷却系统,维持模具的热平衡。一些3C产品如手机外壳、手提电脑外壳由于薄壁,要考虑加热系统布置,使金属流动性能提高。
八、压铸参数
在压铸生产过程中,选择合适的工艺参数是获取优质压铸件,发挥压铸机最大生产率的先决条件,是正确设计压铸模的依据。压铸时,影响合金液充填成型的因素很多,其中主要有压射压力、压射速度、充填时间和模具温度等。这些因素互相影响,互相制约,调整一个因素会引起相应的工艺因素变化,因此,正确选择各工艺参数十分重要。
①压射速度:由于压铸件壁厚和复杂程度不同,工艺参数选择的变化范围很大,镁合金同锌、铝合金相比,流动性更好,惯性更小,而且由于镁的凝固潜热小,热容也小,要在金属凝固之前充填整个型腔,因此,镁合金压铸的速度要高于铝合金,镁合金压铸的冲头速度比铝合金快约30%,最大甚至超过9m/s。
②建压时间:由于镁的凝固潜热较小,镁合金在充满整个型腔后,要迅速地建压,以补充型腔内金属凝固的收缩,因为在内浇口凝固以后再增压已失去意义,所以镁合金压铸要求建压时间短于铝合金。力劲机目前的建压时间在20ms以内。
③模具温度:由于镁锭的凝固潜热较小,金属液以高速度填充型腔,快速凝固,不但能够缩短压铸循环周期,提高生产效率,而且也减少了模具的热疲劳,大大延长了模具的使用寿命。在压铸镁合金时,通常要保持模具的温度稳定。镁合金压铸时模具温度通常保持在220-280℃之间。
在镁合金压铸过程中,如果工艺参数设计得当,镁合金将表现出比铝合金更好的压铸工艺性能。
九、模具润滑
镁合金和铝合金相比更不易蚀模,原因是镁合金中铁的含量非常低。然而,当热金属高速冲击模具的某些部件时,可能产生焊接现象。使用合适的模具润滑剂可以减少这种趋势。最常用的是基于水的润滑剂。由于镁合金的热容只有铝合金的2/3,因此不需要把润滑剂用于冷却媒介,并且使用时间应尽可能的短,一般为铝合金的50%。为减少水的含量,通常使用较高浓度的润滑剂。
声明:本网站所收集的部分公开资料来源于互联网,转载的目的在于传递更多信息及用于网络分享,并不代表本站赞同其观点和对其真实性负责,也不构成任何其他建议。本站部分作品是由网友自主投稿和发布、编辑整理上传,对此类作品本站仅提供交流平台,不为其版权负责。如果您发现网站上所用视频、图片、文字如涉及作品版权问题,请第一时间告知,我们将根据您提供的证明材料确认版权并按国家标准支付稿酬或立即删除内容,以保证您的权益!联系电话:010-58612588 或 Email:editor@mmsonline.com.cn。
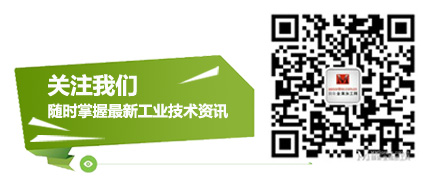
- 暂无反馈