钎焊超硬磨料工具的研究进展
1 概述
由金刚石和立方氮化硼(CBN)制作的超硬磨料工具被广泛应用于各类金属材料的磨削加工,石材、陶瓷、光学玻璃等硬脆材料的加工,以及公路养护、地质采矿、油气钻探等众多工程领域,市场需求量很大。目前生产中使用的超硬磨料工具一般是利用多层烧结或单层电镀工艺来制作,磨粒只是被机械地包埋、镶嵌在结合层中,把持力不大,在负荷较重的加工中容易因把持力不足而导致磨料过早脱落,造成浪费。另一方面,在烧结和电镀工具中磨料为随机分布,磨粒的出露高度不大,容屑空间较小,在磨削加工时容易产生磨屑的粘附堵塞,降低工具的加工性能和使用寿命。
由于多层烧结和单层电镀磨料工具存在上述缺陷和弊端,使其在高效磨削和高速/超高速磨削中的应用受到较大限制。为此,近十几年来国内外许多学者开始研究采用钎焊工艺来制作单层超硬磨料工具,其出发点是希望借助高温钎焊时在磨料、钎料和基体界面上发生的熔解、浸润、扩散、化合等相互作用(即通常所说的化学冶金作用),从根本上改善基体和钎料合金对磨料的把持强度。图1所示为钎焊金刚石单颗磨粒与结合剂界面的微观形貌。可以看出,钎料对金刚石磨粒表现出很好的浸润性,结合紧密,无间隙和沟槽存在。金刚石磨粒晶粒完整,表面无裂纹,出露高度大。与传统的多层烧结超硬磨料工具和单层电镀超硬磨料工具相比,钎焊超硬磨料工具具有以下特点:①磨料、钎料和基体三者之间能实现冶金化学结合,从而提高了结合强度,工具使用寿命长;②磨粒的出露高度大(可达磨粒高度的70%~80%),容屑空间大,不易堵塞,磨料的利用更加充分;③磨削力、功率消耗和磨削温度更低;④具有环保意义,符合当今倡导的绿色制造发展趋势。
钎焊超硬磨料工具因具有独特的优越性而成为当今超硬磨料工具研究的一个热点。本文从钎焊的钎料、工艺及方法等方面概述了国内外钎焊超硬磨料工具的研究现状和研究成果,分析了不同的钎料、工艺及方法对磨粒结合强度和界面微观结构的影响。在此基础上,讨论了磨粒的优化排布问题以及在单层钎焊超硬磨料工具表面实现磨粒有序排布的方法。
2 钎焊金刚石工具的研究现状
金刚石与一般的金属、合金之间有很高的界面能,其表面不易被熔化的金属或合金所浸润。根据理论分析及文献报道,在一定的条件下,某些过渡族元素如Ti、V、Cr、Zr、Mo、W等,在一定条件下可与金刚石的碳元素在表面形成碳化物,而通过这层碳化物的作用,金刚石、钎料和钢基体三者就能通过钎焊实现牢固的冶金结合,这就是金刚石高温钎焊的原理。金刚石钎焊的质量在很大程度上取决于所使用的钎料、钎焊工艺及方法。因此,提高对金刚石磨粒把持力的关键就是寻求与之相适应的活性钎料、钎焊方法和钎焊工艺。
2.1 镍基合金钎料钎焊金刚石的工艺及方法
瑞士的A K Chattopadhyay采用的钎焊工艺为:先用火焰喷镀法(氧-乙炔焊枪)将钎料合金(主要成分为72%Ni、14.4%Cr、3.5%Fe、3.5%Si、3.35%B和0.5%O2)镀于工具钢基体上,并将金刚石排布于焊料层面上,然后在1080℃、氩气保护下高频感应钎焊30秒实现金刚石与钢基体的结合。钎料合金中的Cr作为一种强碳化物元素,在钎焊过程中向金刚石表面富集而实现金刚石的表面金属化。
德国的A Trenker等采用真空炉中钎焊的方法,在高温钎焊过程中分别采用了活性钎料和镍基钎料来实现金刚石与基体的结合。在加工玻璃的实验中,与电镀金刚石工具相比,高温钎焊金刚石工具的性能更为优异,钎焊工具的起始磨削性能是电镀工具的3.5倍以上,寿命是电镀工具的3倍以上。
南京航空航天大学的肖冰等利用高频感应钎焊方法,用Ni-Cr合金钎料真空感应钎焊30秒,钎焊温度1050℃,将金刚石牢固地钎焊在钢基体上。经X射线衍射分析发现,合金钎料与金刚石在界面生成Cr7C3和Cr23C7,因此这种钎焊工艺可以确保合金钎料层与金刚石之间的高强度结合。在后续的大负荷磨削实验中,未发生金刚石整颗脱落,说明钎料对金刚石具有较高的把持强度。姚正军等利用Ar气保护炉中钎焊的方法,以Ni-Cr合金粉末作为钎料,控制钎焊温度1050℃、保温时间6min和冷却速度30℃/min,实现了金刚石与钢基体的牢固连接。利用扫描电镜和X射线能谱,结合X射线衍射结构分析,发现钎焊过程中Ni-Cr合金中的Cr元素分离出来在金刚石界面形成富Cr层,并与金刚石表面的C元素反应生成Cr3C2和Cr7C3,这是实现合金层与金刚石的较高结合强度的主要因素。重负荷磨削实验表明,金刚石为正常磨损,无整颗金刚石脱落,能够适用于高效磨削加工。卢金斌等利用真空炉中钎焊的方法,以Ni-Cr合金作为钎料,金刚石直接排布在Ni-Cr合金上,适当控制钎焊工艺,实现了金刚石与钢基体之间的牢固连接。通过对金刚石与钎料界面微观结构的分析,发现钎焊过程中钎料会在金刚石界面形成富Cr层并与金刚石表面的C元素反应生成Cr3C2和Cr7C3,其中Cr7C3呈笋状生长,Cr3C2呈片状生长。最后通过磨削对比实验验证了金刚石与钎料有较高结合强度。马伯江等利用高频感应钎焊的方法,在相同的钎焊工艺条件下,采用两种不同成分的Ni-Cr钎料钎焊镀Ti金刚石和无镀膜金刚石。试验使用了两种镍基活性钎料,两者相差4%Cr(质量分数),在Ar气保护下进行高频感应钎焊,钎焊温度小于1100℃,保温数秒。结果表明,钎料成分不同、金刚石镀Ti与否,使金刚石表面生成的碳化物成分和形态各异,影响了它们与金刚石结合强度的高低。在此基础上,分别采用真空炉中钎焊和氩气保护下的高频感应钎焊工艺制作了单层钎焊金刚石工具。结果表明,这两种工艺制作出来的工具都可在金刚石-钎料界面上生成对提高金刚石把持力起关键作用的碳化物,但其界面结构存在差异。在电阻炉中钎焊条件下,生成物有两层结构,内层产物是Cr3C2,外层产物是Cr7C3;在高频钎焊条件下,仅有单层产物Cr3C2。
第四军医大学的马楚凡等利用真空炉中钎焊的方法,以NiCr13P9合金作为钎料,同时加入少量Cr粉,在高温(950℃)加压及真空度为0.2Pa的条件下进行钎焊,实现了金刚石与钢基体间的牢固结合,研制出用于牙科CEREC CAD/CAM系统的专用单层钎焊金刚石砂轮。扫描电镜观察显示,银白色的合金包绕在金刚石周界,钎料在金刚石磨粒间分布均匀,金刚石已被牢固钎焊,金刚石出刃高度大。X射线衍射分析能观察到Cr3C2衍射峰,表明有Cr3C2生成。正是通过金刚石界面上的碳化物层,合金材料实现了对金刚石的高把持力。磨削实验证实了金刚石确有高把持强度,钎焊金刚石砂轮的耐用度及磨削效率较普通电镀砂轮明显提高。
华侨大学的黄辉等利用高频感应钎焊的方法,以Ni-Cr合金为钎料,尝试在空气中直接进行金刚石磨粒的钎焊。通过适当控制钎焊电流和钎焊时间,实现了金刚石与钢基体的牢固焊接。磨削实验表明,采用该方法制造的金刚石工具在金刚石磨粒与基体之间有着较高结合强度,金刚石磨粒在整个加工过程中未出现脱落,金刚石磨粒的磨损过程为正常磨损。另外,还尝试在自制真空炉中利用高频感应钎焊金刚石节块。通过调整加热时间与加热功率来控制钎料加热温度,实现金刚石与基体的牢固连接,并制作了金刚石磨盘。在磨削加工花岗石的过程中,对金刚石磨粒的出露高度、磨粒的磨损状态进行了跟踪,揭示了钎焊金刚石工具在加工过程中的磨损性能。
2.2 银基合金钎料钎焊金刚石的工艺及方法
南京航空航天大学的肖冰等利用高频感应钎焊的方法,以添加Cr粉的Ag-Cu合金作为钎料,在空气中感应钎焊35秒,钎焊温度780℃,实现了金刚石与钢基体间的牢固结合。经X射线能谱及X射线衍射分析,发现金刚石界面上有Cr3C2生成。与不加Cr粉的Ag-Cu合金钎料的对比试验表明,合金钎料正是通过金刚石界面上的这一碳化物层而强有力地把持住金刚石。
哈尔滨工业大学的孙凤莲等利用真空炉中钎焊的方法,以Ag-Cu-Ti活性钎料合金箔作为填充材料,对CVD金刚石厚膜进行了钎焊实验。实验参数:真空度5×10-3Pa,钎焊温度920℃,升温和降温速度为30℃/min,保温时间20min。经X射线衍射分析,确定了金刚石与钎料结合界面处的新生化合物为TiC层。正是该碳化物层使钎料与金刚石之间产生了冶金结合,使金刚石厚膜与基体金属之间形成牢固连接。在此基础上,讨论了不同的钎焊温度(850℃、880℃、910℃、940℃和970℃)对金刚石结合强度的影响。试验结果表明,在940℃时剪切强度最大,达133MPa。可见,钎焊温度直接影响到钎料、金刚石与基体之间的结合强度。
哈尔滨理工大学的李丹等利用真空炉中钎焊技术对Ag-Cu-Ti钎料在金刚石表面的润湿状况进行了试验研究。使用了3种Ag-Cu-Ti钎料,Ti的质量分数分别占5%、10%和15%。钎焊工艺参数:真空度6.65×10-3Pa,升温和降温速度30℃/min,钎焊温度950℃,保温时间25min。试验发现,Ti占10%的Ag-Cu-Ti钎料对金刚石具有较好的润浸性能,结合强度较高。关砚聪等利用真空感应钎焊的方法,对Ag-Cu-Ti钎料钎焊金刚石磨粒进行了钎焊工艺试验研究,探讨了钎焊温度和钎料状态对结合强度的影响。钎焊工艺:采用二级加热工艺,钎焊温度分别为890℃、910℃和940℃,真空度为0.2Pa。试验结果表明,钎焊温度比钎料熔化温度高50℃(940℃)时,结合界面的结合强度最大,X射线衍射分析表明,在金刚石与钎料结合界面间新生的化合物为TiC。在钎焊温度为940℃时真空钎焊无镀膜金刚石,用Ag-Cu-Ti钎料合金箔的结合强度比用Ag-Cu共晶合金箔与Ti箔的结合强度更高。
广东工业大学的王成勇等利用高频感应钎焊的方法,在空气中或局部气体保护下高频钎焊金刚石。主要钎焊工艺:在基体上放置钎焊片(主要为Ag-Cu-Zn、Ag-Cu-Ti或其它Ag-Cu基合金)和102焊剂,再将金刚石包裹上金属粉(铬粉和钛粉)放置在钎焊片上,或在放置了金刚石磨粒的钎焊片上均匀撒上金属粉,然后进行高频钎焊,实现了金刚石、钎料与基体之间牢固的化学冶金结合。
2.3 铜基合金钎料钎焊金刚石的工艺及方法
巴基斯坦的F A Khalid等利用真空炉中钎焊的方法,以Cu-14.4Sn-10.2Ti-1.5Zr合金作为钎料,研究了金刚石界面的微观结构。钎焊工艺:真空度2×10-8Pa,钎焊温度930℃,保温时间10min,冷却速度20℃/min。扫描电镜和X射线能谱分析表明,在金刚石-钎料界面生成的碳化钛有两层结构,第一层是立方形TiC,第二层是细长形或柱形TiC。
西安交通大学的孟卫如等应用真空炉中钎焊的方法,对金刚石钎料的适应性进行了试验研究。分别采用3种含有强碳化物形成元素Cr、Ti的BNi2(NiCrSiB)、BNi7(NiCrP)及自制的CuSnNiTi钎料,在各自的钎焊温度分别为1050℃、950℃和900℃、保温时间10min及真空度0.13Pa的条件下,单层钎焊金刚石圆锯片(φ125mm)。通过扫描电镜观察形貌和X射线能谱分析成分,表明3种钎料对金刚石有很好的润湿性,钎料中的Cr、Ti元素会向金刚石表面扩散,并与金刚石中的C元素结合生成碳化物。碳化物的形成使金刚石、钎料与基体之间产生了化学冶金结合,提高了对金刚石的把持力,但结合状况及锯切性能随钎料的不同而存在差异。试验证实,自制的铜基钎料钎焊温度低,钎焊时金刚石的热损伤小,对金刚石有很好的把持力,而且钎料与所切割的石材有很好的适应性,有效提高了金刚石的利用率。
台湾大学采用Cu-15Ti-10Sn合金钎料,比较了真空炉中钎焊方法(钎焊温度925℃、保温5min)和激光钎焊方法(钎焊时间10秒)对金刚石界面微观结构的影响。在真空炉中钎焊条件下,金刚石表面形成一层连续的过渡层(TiC薄膜);而在激光钎焊条件下,金刚石表面形成的是一层不连续的过渡层。
上述研究表明,不同的钎料合金(包括钎料的成分、含量、状态等)、钎焊方法和钎焊工艺参数直接影响到钎料与基体及金刚石之间的相互作用、生成物的形态以及结合界面的微观结构,从而影响结合强度以及钎焊工具的质量和性能。
3 钎焊CBN工具的研究现状
金刚石工具只适合加工非铁族金属,而CBN工具则适合高效磨削铁族金属,二者在适用加工对象上具有互补性。但CBN的化学稳定性极高,对其进行钎焊比金刚石钎焊更加困难。目前,国内外文献资料中关于CBN钎焊研究的报道相对于金刚石钎焊要少得多。
国外有关CBN钎焊的试验研究始于20世纪90年代初,钎焊工艺通常是:首先用化学气相沉积法(CVD)在CBN磨料表面预先沉积一层TiC薄膜,沉积温度1000℃,沉积时间90min;然后采用Ni-Cr合金在1040℃下进行真空感应钎焊,Ni-Cr合金钎料能有效浸润镀膜CBN磨粒,从而将镀膜CBN成功焊接在基体上。另外,采用不含Cr的镍基钎料(如Ni-P合金:Ni90%,P10%)同样也能良好地浸润镀膜CBN磨粒。
近年来,国内南京航空航天大学也在进行CBN钎焊的研究,并取得了一些进展。采用的工艺是:以Ag-Cu-Ti合金为钎料(主要成分为:67%Ag,20%Cu,12%Ti),在真空电阻炉中加热至钎焊温度(1000℃)并保温适宜时间再随炉冷却至室温,取得了成功。用扫描电镜、X射线能谱仪及X射线衍射仪对CBN与钎料结合界面微观组织进行观察和分析,发现合金钎料中的元素Ti向CBN表面扩散富集,生成了针状TiB2和TiN,在CBN磨粒与钎料界面形成化学冶金结合,这是CBN与Ag-Cu-Ti钎料间有良好浸润性和高结合强度的主要原因。后续的磨削对比试验表明,钎焊CBN砂轮比电镀CBN砂轮具有更高的磨粒把持强度。在相同磨削条件下,单层钎焊CBN砂轮的磨削温度比电镀CBN砂轮明显降低,特别在大切深条件下其降温效果更为显著。因此,钎焊砂轮在降低磨削温度、提高磨料结合强度、延长砂轮使用寿命等方面比电镀砂轮具有明显优势。
4 超硬磨料的优化排布问题
为了更充分地发挥钎焊超硬磨料工具的优越性,提高工具的加工性能和加工效果,工具表面磨粒的排布和三维形貌设计是一个重要因素。磨料的择优有序排布能够有效改善工具的加工性能。例如,在金刚石锯片加工四川红花岗石板(莫氏硬度7~8,厚度20mm)的性能对比试验中,经过磨料择优排布的高温单层钎焊金刚石锯片的寿命分别为未经优化的单层高温钎焊金刚石锯片和多层烧结金刚石锯片的120%和81.7%,加工效率则分别为1.5倍和4.9倍。我国台湾的中国砂轮公司推出的单层均布金刚石高温钎焊串珠,在不降低工具寿命的前提下,可使金刚石用量减少一半,切割速度增加两倍。据称,如果单层钎焊技术能够应用于石材加工工具,将是金刚石加工工具设计的一次革命,其结果不仅是生产效率的大幅度提高,并且可使加工成本大幅度降低。
磨料的优化排布包括磨粒在工具表面的排布方式、磨粒的粒度和浓度、磨粒的出露高度和等高性、动态有效磨粒间距、磨粒数等一系列静、动态参数和几何参数。其中,有效磨粒间距直接决定了单颗磨粒的工作负载,不合适的磨粒间距通常会导致磨料过早失效等问题,从而降低工具的加工效率和使用寿命,因此它是需要优化的参数中对加工状态具有最大影响力的参数。在许多加工情况下,工具的不同部位需要采用不同的磨粒粒度和浓度,以便更有效地利用磨料。因此,需要根据具体应用场合和加工要求来优化磨粒排布,以制作出具有最佳使用性能的超硬磨料工具。磨料优化排布技术除可有效控制和提高加工质量,还能对工具寿命进行预估,更好地评价钎焊超硬磨料工具的性能。
目前,实现磨料有序排布的技术主要有复制技术、模板方式和激光快速成型技术等,但这些技术在工业生产中的推广应用尚需进一步深入研究。如何实现磨粒的自动、有序排布是钎焊工具发展的一个重要课题。
(1)复制技术
复制技术适用于小粒径及微粉级的金刚石工具制造。由于用该技术成型的有序排布金刚石规格同一,间隙一致,形同复制,故称为复制技术。复制技术的原理是通过制作定尺寸的压块,在Si模板上刻印出成型所需有序排布的规则模孔,然后采用CVD法在模孔内沉积金刚石薄膜,最后清除Si模板并将金刚石薄膜粘结到基体上,从而实现金刚石的有序排布,其工具基体可以为任意曲面。
(2)一次性使用壳模布料法
该方法的原理参照熔模铸造中的型壳材料及其制作工艺,先在工具的工作面上均匀挂涂一层耐火涂层(厚度控制在磨料高度的一半左右),待其固化后在涂层上加工出间距与有效磨粒间距相符的布料槽(条布)或孔(点布);然后在涂料层的槽或孔中填放调成膏状的钎料合金,并撒布磨粒,再将磨粒压实到基体表面;最后在已布有磨料和钎料的涂层上再封盖一层耐火涂料,进一步固定磨粒的位置,在充分硬化和高温焙烧后送入真空炉内钎焊;钎焊后去除和清理外层型壳,即可得到具有优化形貌的单层钎焊工具制品。该布料技术可以满足端面、圆柱面和各种任意复杂异形面工具的需要。
(3)利用孔模板实现磨粒有序排布
按照优化排布要求,在陶瓷模板上加工出孔径与金刚石(或CBN)磨粒直径相当、深度为磨粒高度70%的规律排布的孔,再按孔排布好磨粒。合金钎料熔化后的厚度约为磨粒高度的30%,由于陶瓷模板不具有可焊性,钎焊后易于去除。该钎焊工艺不仅能保证磨粒的有序排布,等高性好,而且可以保证磨粒有70%的出露高度。
(4)有序阵列法
该方法是首先采用焊接或胶接方式在基体上固定一层钎料,然后在钎料上固定一层石蜡,石蜡的高度与超硬磨粒高度相同,用机械力将钢柱压入石蜡,形成比超硬磨粒稍大的孔洞,以钢柱或基体步进的方式有规律地调整钢柱位置,可在基体上得到不同密度的孔洞,将超硬磨粒刷过基体,未掉入孔洞的超硬磨粒组成“有序阵列”,钎焊时石蜡被烧掉,超硬磨粒在钎焊后即形成有序排布状态。也可采用激光束来形成有序阵列。
(5)利用激光快速成型技术实现磨粒有序排布
从优化的结果出发,借鉴激光快速成型技术的SLS法,采用CAD数据处理软件进行切片处理,激光器以一定的扫描速度对预先随机排布在工件表面结合剂层上的磨粒按给定的形貌要求进行扫描,通过有效控制激光强度、脉冲周期和光斑直径,保证一定的焊接温度和时间,使被激光扫描到的磨粒按照形貌要求有序地钎焊到基体上,将未被激光扫描到的磨粒去除后,即可得到磨粒有序排布的单层钎焊工具。
(6)点胶法
借鉴点胶机的原理,选用适当的喷嘴尺寸以形成大小合适的胶滴。控制喷嘴将粘接剂按照给定的形貌要求喷洒在基体上,再将磨料撒布在基体表面,去掉多余磨料后就可在基体上形成磨粒的有序排布,胶干后将钎料粉均匀布置于磨粒间再进行钎焊。
5 结语
高温钎焊技术可以实现金刚石(或CBN)、钎料和金属基体三者界面之间的化学冶金结合,具有较高结合强度。与电镀和烧结工具相比,钎焊超硬磨料工具具有许多优势,今后将会成为一种新的发展趋势。目前,欧洲、日本等少数国家(包括我国台湾地区在内)已经开始小批量试制单层钎焊超硬磨料工具,但要实现大批量工业化生产和在加工中推广应用,其制造工艺——无论是钎焊工艺还是磨料排布——仍存在许多需要进一步解决的难题。总之,钎焊超硬磨料工具有着很好的应用前景,可带来巨大的社会效益和经济效益,应加大研究开发力度,尽快实现产业化。
声明:本网站所收集的部分公开资料来源于互联网,转载的目的在于传递更多信息及用于网络分享,并不代表本站赞同其观点和对其真实性负责,也不构成任何其他建议。本站部分作品是由网友自主投稿和发布、编辑整理上传,对此类作品本站仅提供交流平台,不为其版权负责。如果您发现网站上所用视频、图片、文字如涉及作品版权问题,请第一时间告知,我们将根据您提供的证明材料确认版权并按国家标准支付稿酬或立即删除内容,以保证您的权益!联系电话:010-58612588 或 Email:editor@mmsonline.com.cn。
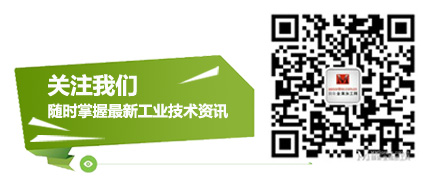
- 暂无反馈