冲压工艺的新发展:材料、工艺、测控一体化
冲压是一种传统生产技术,可考历史已超过千年。
传统冲压技术主要是模具和工艺设计问题,以铜及铜合金、钢铁、铝和铝合金为主要材料。由于这些材料的发展和应用历史很长,性能掌握成熟,因此冲压工艺主要依赖模具配合实现,对材料的依赖性不是很明显。
近年来,随着汽车、航空航天等工业的发展,很多新材料得到越来越多的应用,例如一些难变形冲压材料:钛合金、镁合金、复合材料和高强铝合金等。材料科学和塑性力学的发展带动了冲压技术的进步,计算机技术和控制技术的发展,也使过去难以实现的工艺成为可能。进入21世纪以来,冲压技术逐渐发展为一门技术科学,呈现出工艺、材料、控制一体化的发展特点。工艺、材料、控制一体化就要求通过物理测试、模拟和数值模拟掌握材料与工艺的优化匹配,并根据具体工艺要求实现工艺控制或在线测控。
(1)材料性能量化控制。物理模拟技术是掌握材料性能获得量化规律的必要手段。较早的物理模拟技术是使用一些与成形材料性能相似的模拟材料和测试方法,主要用于解决工艺可行性问题。近年发展起来的一些Gleeble等试验设备为测试材料性能提供了更广泛的可能性。可进行压缩、扭转等试验,模拟各种不同温度、不同摩擦条件、不同变形速度条件下的变形加工,获得材料的各种性能数据;并根据这些数据获得材料成形极限和材料本构关系的定量表达式,使计算或模拟的材料塑性变形过程更加准确可靠,为冲压加工的定量控制提供了材料基础。
(2)冲压生产智能控制技术。近年来,冲压生产智能控制技术也是发展很快的一个领域。它在材料、工艺一体化的基础上,依据已有材料和工艺数据库实现冲压加工过程的在线控制或智能控制(也称为自适应控制)。首先对材料或工艺参数建立在线检测系统,当材料性能或工艺参数发生变化或产生波动时,由自动检测系统(传感器和信号转换系统)在线确定相关参数的瞬时量值,并通过计算机模拟分析和优化软件(例如人工神经网络方法、专家系统)确定参数变化后的最佳工艺参数组合。自动控制系统调整工艺参数后,可以实现冲压工艺过程的自适应控制。新的生产数据逐渐积累,可进一步成为后续加工过程的工艺优化基础。
(3)科学的冲压生产技术是多种场量的耦合控制。复杂件冲压成形要求对冲压工艺参数进行场量控制,有些材料要求场量实现梯度分布,这是塑性力学原理与材料性能结合的需要;温度场、变形速度场、摩擦润滑场、材料流动趋势、材料变形顺序(屈服顺序)及变形路径等。
这些场量也不是恒定的,是过程变量,因此加热冷却措施、润滑方法与润滑剂、模具结构、压边方式(变压边力与多点压边)、拉深筋和加载方式都是控制场量的重要措施。温度场的控制可实现差温冲压成形;摩擦梯度场(润滑梯度场)也是控制冲压变形的重要手段。摩擦可以为冲压变形材料流动提供一定阻力,一般要求尽量减少摩擦力,然而有时摩擦力也有助于提高材料成形极限。而且还可以通过模具结构、圆角半径、压边方式、模具间隙、拉深筋和模具分块控制坯料的受力状态,进一步改变坯料内部应力状态、材料流动趋势和材料屈服顺序、材料变形顺序和材料应变历史。例如拼焊板冲压时,为减小坯料焊缝移动,使坯料变形均匀,一般通过模具凹模凸台和变压变力方式控制冲压变形过程;而汽车覆盖件冲压采用拉深筋已是很普遍的措施。作者提出的可动凹模液压成形技术因凹模采用分体结构,使坯料各部位变形顺序得到改变,避免了局部变形过大,显著提高了成形极限,可以一道次成形非常复杂的冲压件。
声明:本网站所收集的部分公开资料来源于互联网,转载的目的在于传递更多信息及用于网络分享,并不代表本站赞同其观点和对其真实性负责,也不构成任何其他建议。本站部分作品是由网友自主投稿和发布、编辑整理上传,对此类作品本站仅提供交流平台,不为其版权负责。如果您发现网站上所用视频、图片、文字如涉及作品版权问题,请第一时间告知,我们将根据您提供的证明材料确认版权并按国家标准支付稿酬或立即删除内容,以保证您的权益!联系电话:010-58612588 或 Email:editor@mmsonline.com.cn。
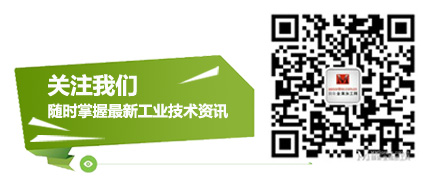
- 暂无反馈