飞机钣金零件的计算机辅助设计和制造
将计算机辅助设计与制造应用于飞机钣金加工,促进了航空制造业的快速发展。从钣金零件的设计与展开,坯料排样、数控指令编写等三个方面分析CAD/CAM技术在飞机钣金零件设计与制造过程中的应用。
在航空产业中,钣金零件是组成现代飞机机体的主要部分,占飞机零件总数目的70%,制造工作量约占整架飞机劳动量的15%,并有品种多数目少,结构复杂、外廓尺寸大、刚性小等特点,直接影响飞机整机质量和生产周期。伴随航空制造水平的进步,现代加工方法及设备的不断涌现,飞机钣金零件加工的概念、方法和手段也在发生深刻的变化。将计算机辅助设计与制造(CAD/CAM)运用于飞机钣金加工已成为航空企业加快产品开发,进步产品质量的有力措施。
计算机辅助设计和计算机辅助制造,简称CAD/CAM,是指以计算机为主要技术手段来天生和运用各种数字信息,以进行产品设计和制造。用计算机辅助设计制造飞机钣金零件,从零件的设计开始,经过展开、排样,到剪切、冲压、折弯,其中最主要的是制件的设计展开以及数控指令编制。
1计算机辅助钣金零件设计与展开
飞机钣金零件一般可分为三类:平板类,即一般的平面冲裁件;弯曲类弓即板料弯曲或弯曲加工成形构成的零件;成形类,即板料由拉伸等成形方法加工而成的规则曲面类或自由曲面类零件。对于各种规则外形或复杂飞机钣金零件的设计、展开,可划分为基于模型的方法和造型方法两种方法。
传统的钣金零件下料方法有作图法和计算法两类,作图展开的基本方法有平行线法、放射线法、三角线法等;计算法是用解析计算代替作图法中的放样和作图过程,计算出展开图中特征点的坐标、线段长度,再由计算结果绘制出图形。用计算机来完成这些计算机来完成这些计算工作就是最基本的急于模型的钣金零件CAD方法。对于常用的接头、门板类钣金件,基于模型的钣金件设计展开方法构造模型时需要一定的工作量,使用时十分可靠、高效。
针对现金飞机钣金零件特点而提出来的几何造型方法有2D钣金件的几何造型和3D钣金件的几何造型。前者包括编码法、面素拼正当和交互尺寸输人法等;后者原有弯曲交换拼正当、体素拼正当等方法。各种CAD/CAM系统的造型功能和方式不尽相同,简单的造型方法只用规则的面、体造型;复杂的造型方法具有高级的曲面造型和实体造型功能,如零件设计应用全参数化及基于特征造型的技术,提供如扫描、提拉、肋板、螺旋、切割等功能,饭奔设计可自动折弯工艺孔、自动展开和回折。
1.1拼合造型操纵方法
利用薄片立方体、空心圆柱体等基本体元,逐形体生长成制件几何模型,是钣金件造型的基本方法。拼合造型方法所用的元素可以是无厚度的面元素,也可以是有厚度的体元素。很多钣金件都由等厚度的板料制成,这就有可能在造型过程中使用无厚度的面块,构造出钣金零件的基本结构后再指定长出厚度的方向,生长出制件,这种先设计出无厚度的结构框架再生长出有厚度的制件的方法也适用于覆盖件等复杂钣金零件。
1.2特征造型操纵方法
特征是产品描述信息的集合,它不仅具有按一定拓扑关系组成的特定外形,而且反映特定的工程语义,适宜在设计、分析和制造中使用。特征可以分为:外形特征、精度特征、材料特征等,其中外形特征是关键,是其他特征的载体或基体,也是实现参数化特征造型的核心,它可以定义一定工程意义的几何形体或实体。飞机钣金零件都可以分解成一个或多个外形特征,从特征构型的角度来看,钣金件是由一系列特征构成,它们之间的相互联系便构成一个完整的零件。根据钣金件特点,可以回纳出如下主要特征:平面特征,构成零件的平面外形,是零件的基本部分,是连接弯曲的部分,也是局部成形和冲孔的母体;弯曲特征,是由弯曲加工工序产生的外形,最简单的弯曲特征是由圆柱面表示的弯曲区;孔特征,作为一般子特征而依附于其他特征,如在平面或弯曲特征上冲孔;局部成形特征,由局部成形工序在冲压件上产生的外形,通常外形和特征参数类型固定,数值变化,因此可以用参数来表达。
1.3展开操纵方法
飞机钣金零件展开方法的基本原理是在设计过程中,纪录下各面块与其相连面块之间的拓扑关系,以此为依据进行展开。功能较简单的系统可以先指定一个基准面,再逐个指定待展开的面,一步步展开整个钣金零件。高级的CAD/CAM系统可以一次操纵展开多个表面。
2计算机辅助坯料排样
飞机钣金零件的生产本钱主要包括材料费、设计费和模具费等,其中材料费占很大的比例,计算机辅助排样系统是降低材料用度的重要途径。
目标函数优化排样法是现金航空钣金应用范围比较广泛的一种排样方法。其基本原理是以同类坯料块复制时的参数△x(X方向平移△x)、△y(Y方向平移△y)、△φ(旋转△φ)为变量,再根据参加排样的坯料块类型、轮廓外形和数目关系等得到函数关系式,构造一定的目标函数。围绕目标函数按一定的算法进行迭代,当目标函数达到设定的精度目标时,即停止,按停止迭代时的参数进行排样。为了进步工作效率,可以限定部分参数的变动范围。
当参加排样的坯料块类型多,对各类坯料块复制的参数△x、△y和△φ都不加限制时,排样效果将大为降低。这时可以做一些排样预备工作,如判定参加排样的坯料块的几何属性;或在搜索△x、△y和△φ的过程中包容坯料块,但是线条较简单、较少的封闭轮廓来代替原来的坯料轮廓。
不同的排样系统的具体功能操纵可能不同,基本内容包括:
(1)选择板料,从板材库中选取供排样的板料,包括标准规格的板料及以前用过一部分的剩余板料。(2)指定坯料块,从钣金零件展开后建立的坯料块库中指定要参加排样的坯料块种类和各类要复制的块数。(3)优化排样,在选定的板材上就指定的板料块及其数目排样。这一级菜单可以选择分支项,如单排、对头双排、混合套排、人们交互排样等。(4)排样编辑,对参加排样的坯料块进行预处理或对排样结果进行干涉检查、手工调整,必要时决定重新排样。(5)排样结果输出,包括输出排样结果图及相应的数据丈件、材料利用率、下料计划报表。
3数控指令编制
数控编程是目前CAD/CAM系统中最能明显发挥效益的环节之一,在实现设计加工自动化、进步加工精度和加工质量、缩短产品研制周期等方面发挥着重要作用。数控编程是从零件图样到获得数控加工程序的全过程。其主要任务是计算加工走刀点(cutterlocationpoint,简称CL点)以及决定走刀顺序、确定工艺参数等工艺路线设计,针对数控系统的具体格式编制数控指令文件,对数控指令文件的运动方针等内容。在复杂形体钣金件的CADICAM中,工艺设计工作也往往非常复杂,可以由专门的CAP系统完成。
钣金零件下料过程中,加工对象是平面的板料,采用切割、剪切、冲压等方法,工艺设计工作比较简单,可以包含在数控编程系统中。在切割、剪切、冲压三者种,数控冲压指令文件最为复杂,下面以数控冲压为例介绍钣金制件的数控编程。
3.1数控冲压指令编制中的设计信息输进
钣金件设计、展开、排样后可以提供图形、数据文件等输出,图形上可以有尺寸标注。最简单的数控指令编制的方法是手工编制,由人工阅读、分析图形和数据。
钣金制件冲压加工一般只涉及平面图形信息的处理,采用基于点、线的数控刀具轨迹天生方法,可以直接以可视化方式对图形进行编程操纵。用光标指定间隔光标位置最近的图素,由计算机确认该图素的几何信息。
3.2数控冲压指令编制中的工艺设计
数控冲压时的工艺设计的基本内容主要包括:选择冲模,确定各图素的冲压顺序,确定步冲时的步距量和板料移动速度,设置夹爪位置等。同样外形、尺寸的轮廓可能依操纵者习惯采用不同的冲压方式,如对大孔、槽的冲压,可以采用面积小的冲模,只冲出孔,槽的轮廓,然后移开冲模,暂停机床,人工取走孔中的余料,再继续加工;也可以选用面积大的冲模,不仅冲出孔、槽轮廓,而且将内部的材料全部冲压成碎片。这种方式的选择方式可以放到编程过程中选择不同的菜单分支来处理;功能较全的CAD系统中,可以有冲碎和不冲碎两种指令方式。
3.3数控冲压指令编制
计算机辅助编程就是用计算机完成原来由手工完成的那些与编程有关的工作。在钣金冲压指令编写过程中,最基本的操纵只要指定冲模、指定待编程的图素,然后就可以由编程系统自动编制出数控指令文件。
对功能较强的指令系统,编程操纵还包括是否选用成组冲压指令,是否调用子程序功能等。
3.4数控冲压指令的优化和仿真
编制出数控指令文件后,还需要进行后置处理,基本的后置处理操纵是优化和仿真。
冲压指令的优化通常包括冲模优化和轨迹优化两部分。冲模优化的目的是将同一冲模完成的冲压指令集合到一起,以减少加工过程中的模具转换;二是q对不同类型的冲模排列顺序,通常面积较小的冲模在前,面积较大的冲模在后。轨迹优化主要是为了减少冲压过程中的空行程长度。
仿真功能一般可以显示冲压指令文件的执行过程,检查冲压指令是否公道、冲模运动时是否可能与夹爪发生干涉等。还可以由冲压指令文件逆向转换为图形,将其与编程前的图形相比较,分析两个图形的一致性,从而判定冲压指令文件的正确性。
4结束语
CAD/CAM技术具有高智力、知识密集、更新速度快,综合性强、效益高等特点。CAD/CAM技术应用于飞机钣金零件的设计与制造,深刻地改变了各航空企业能够借以设计和制造钣金零件的常规方法,影响到企业的治理和市场竞争力。因此,任何航空企业要想保持发展上风,就必须在包括钣金零件的产品设计和制造过程中努力研究、开发或使用CAD/CAM技术。
声明:本网站所收集的部分公开资料来源于互联网,转载的目的在于传递更多信息及用于网络分享,并不代表本站赞同其观点和对其真实性负责,也不构成任何其他建议。本站部分作品是由网友自主投稿和发布、编辑整理上传,对此类作品本站仅提供交流平台,不为其版权负责。如果您发现网站上所用视频、图片、文字如涉及作品版权问题,请第一时间告知,我们将根据您提供的证明材料确认版权并按国家标准支付稿酬或立即删除内容,以保证您的权益!联系电话:010-58612588 或 Email:editor@mmsonline.com.cn。
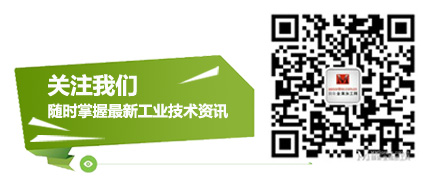
- 暂无反馈