叠层模具技术介绍
在数十年里,叠层模具在包装制品和其他许多小型零件生产的增长中不断获得新的发展。新颖的模具设计正给叠层模具的传统市场带来多种颜色和多种材料成型的能力。叠层模具现在也在抓住大吨位成型机上生产大型工业零部件的机会。
通常的叠层模具设计因为它们的生产效率超过普通的单面模具而闻名。它们大多用于相当小型的、浅拉伸包装制品和其他一次性制品,而很少用于除此之外的其他制品。但是在过去几年中引入的一批新模具概念拓宽了叠层模具的能力,包括了多材料成型和大型工业零部件,如汽车的前大灯棱镜和侧边修饰件。大型零部件成型意味着叠层模具首次应用在大于1000 t的成型机上。
革新的步伐在多组分成型方面一直相当活跃。通常的单面多组分模具的典型成型方式是在模具的半面注射一种材料进入型腔,再注射第二种材料进入模具的另一个半面。在一个循环之中,在水平轴上旋转模板,使模具翻面。叠层模具成倍地增加可使用的模具面,还允许整个模具表面用各自的材料成型。这种新设计有一个在垂直轴上旋转的中心模板。取决于系统,中心模板可以有或者两个或者四个面,每当模具打开时旋转90o或者180o。
四种制模概念使得这种多组分零部件的大批量生产方法得以商业化。这类新型模具的结构包括Engel公司的一种旋转模板设计,其中心模板有两个面,每个周期旋转180o。由Ferromatik Milacron欧洲公司与德国模具制造商Foboha公司合作开发的旋转叠层模具有一个四个面的中心模板,它每一周期旋转90o。丹麦的Gram技术公司的旋转叠层(Spin Stack)方法有多达四个边挨着边的小的中心叠层结构,各自又有四个面,并且每一周期旋转90o。另一种独特的结构,叫做低惯性技术(LIT)来自Caco-Pacific公司。在这种较为简单的设计中,带有两个芯组的旋转杆连接到每个模具的半边,而不是像在其他的设计中那样的单独设置。
这些新式叠层设计正在受到要求较好手感的软接触应用的促进。这类应用包括,例如,牙刷柄、阻透包装应用、带有模塑衬里的帽子和盖子、多色手机机壳,以及由不同材料,如PP和PVC组成的医用零部件。
一个实例是Foboha公司的带有PET(40g)阻透层的HDPE(70g)牙膏管式瓶肩的模具,设计能力10亿只。公司拥有加工方法和制品两方面的专利。这一新型4x64旋转叠层(Turning Stack)系统在一个8.4s的周期中吐出64只双层零件。产量估计为一年17500万只,所以将使用六个生产系统。这样的生产规模在通常情况需要21套常规的叠层模具和机器。特别的注射量控制装置允许在设备运行中调节PET层的厚度,并且可以帮助减少43%的零件重量。
消费品越来越流行,例如,手感好的软接触特点的牙刷和刮胡须刀柄,这一强势要求将对它们的批量需求推向叠层模具最为适合的水平。Ferromatik Milacron欧洲公司和Foboha公司50-60套旋转叠层模具正在运行中,其中多达20套在北美。该公司预测多组分零部件有10%的年市场占有率。
“当前,多组分零部件市场绝对处于繁荣状态,”一家奥地利包装制品模具供应商、迄今为止Gram公司的帽子和盖子旋转叠层技术的唯一专利商、公司的总经理Claus Ziegler说。“五年以前,我们的模具销售的大约1%是用于多组分应用的,现在多组分应用已经达到我们业务量的15%-20%,”Ziegler说。KTW公司有8到10套旋转叠层模具处于试验或工作状态。
旋转叠层方法
与通常的用于多组分成型的旋转模板比较,这种新型的旋转叠层模具由于旋转部分的质量较小,所以转位要快得多。在Gram公司的旋转叠层模具和Caco-Pacific公司的低惯性系统中,质量减小特别明显。“典型情况您们能节省20%到30%的周期时间,特别情况可节省达到50%到80%,”KTW公司的Ziegler说。
Gram公司的系统有附加的优点,它有允许叠层模具旋转所需要的最小的模具开距。管理经理Jes Gram说,为使系统转位,一个双组分的盖子模具只需打开100mm。正在开发的一种新式顶杆设计可以使模板开距减小为60mm。
“旋转叠层概念在市场上是最灵活的,” Gram补充说。“转动机构、液压装置和所有部件包括在模具内部,所以这允许该项技术
用于任何常规的成型机。”第二种材料可在机器旁边用一台补充的组合式注射装置来供给,例如,采用Windsor公司的新型PlugExpress系统,该系统在美国由它的姐妹公司Sandretto公司销售。
Gram公司将它的旋转叠层技术扩展到了一种名为双两次注射模具的系统。设计用于双组分的牙膏瓶肩模具,具有四个分型面和两对各有四个面的旋转叠层,每个面具有24个型芯,总共有384个型芯和192个型腔。周期时间短于7 s,它的生产能力达到115万件/d,即3.9亿件/a。
Gram说,这种两次注射加工过程对单一材料的厚的零部件成型也有好处。这种方法可以使用同一个热流道供给注射同一种材料的第二层。Gram又说,因为在每次注射时只要注射和冷却较小体积的熔体,这就减少了缩痕产生的可能性。
采用旋转叠层方法,不用于成型的中心叠层的(第二和第四个)面可用于装嵌件或冷却部件,而不会增加周期时间。Gram公司近来取得一种新型顶杆系统的专利,它能将制品顶到机器的侧面。该顶杆的液压系统安装在模具框架内。附加的叠层表面的另一种利用方法是成型一种三次注射制品。Gram公司制造了一种用于生产医用管道连接器的模具,第一次注射PVC,第二次注射热塑性弹性体(TPE),第三次注射PVC,以部分重叠注塑TPE。该制品在三个工位成型,并从第四个工位顶出。演示操作在一台88t的Demag公司的机器上进行,周期时间不到15s。这种8+8+8型腔的模具为丹麦的Carmo工业公司每天生产多于46000 只零件。
Ferromatik Milacron欧洲公司和Foboha公司联合开发的旋转叠层模具在去年的K 2001展览会上亮相,展示了这种系统迄今为止使用过的最多的型腔数。这一4x64系统的中心立方在其四个面的每一面有64个型芯,以及供两种材料的每一种用的64个型腔。该应用就是上述介绍的牙膏瓶肩。
虽然旋转叠层系统原来的机型有两个中心面和180°的旋转位置,新机型有一个以90°增量进行转换位置的中心立方,可允许非成型侧作冷却或嵌件用。一台液压电机以编程的加速/减速曲线使中心部分在1.3s中转换位置。
此旋转叠层系统只在Ferromatik公司的K-Tec机器生产线上运行。这些设备有一个标准化的适应叠层模具的可任选的成套构件,提供较长的拉杆,以增加闭合高度,提供一个较坚固的机器床身,以支撑可旋转的中心部分。第二注射单元位于旋转台的旁边,与机器垂直。
在K2001展览会上,Engel公司介绍了它们的旋转叠层系统,由一台Duo公司的双模板成型机和一套有一个180°转位中心模板的两种材料叠层模具组成。Engel公司只在Duo公司的机器上提供它的旋转叠层模具,这是由于它的合模装置较短,允许在可动模板的反面安装第二注射单元。那个系统大大简化了流道设计。转位速度是1.5s或更短。
迄今为止,Engel公司有一个由奥地利的High Tech塑料公司制造的这种类型的演示用模具。它表明了多组分叠层模具在汽车应用中正在出现新机会。在K2001展览会上,Engel公司生产了左右前大灯罩,由透明的聚碳酸酯(PC)和沿边的一条黑色PC框架构成。
与其他技术不同,Caco-Pacific公司的多次注射技术适用于通常的没有可旋转的中心部件的叠层模具设计。全伺服驱动的低惯性技术系统将模具型芯与模具主体分开,将它们固定在安装在一个模具面上的旋转水平杆上。两组型芯安装在杆上 — 一组向上,另一组向下。此杆借助一个导轨连接到一个模具的半边上。在成型过程中,型芯与模具面平齐。一种材料注射入上面一排型腔,而第二种材料同时充模入下面一排型腔,使用的是两个美国Caco-Pacific热流道。当合模装置打开时,型芯杆从模具表面滑离,以允许型芯杆旋转180o。一个脱模杆将成型完成的制品从下面一组型芯顶出,然后此杆滑回模具表面,模具闭合。
此旋转型芯杆的质量相对较轻,由一台安装在端部的小伺服电机来转动。旋转过程短于0.5s,销售和市场副总裁John Thirlwell说。他指出,如果希望,该系统允许第二次注射,并完全包覆第一次注射材料。
Caco-Pacific公司在不到两年的时间内制造了几种低惯性技术模具。所有这些都是单面模具。但是,现在可以有叠层模具的订货了。到目前为止最大的应用是一个16+16的单面模具,用于生产具有软手感的重叠注塑的全包覆型笔杆。一种两种材料的32+32叠层模具正在设计中。Thirlwell说,低惯性技术因为它的全电动驱动适用于清洁室,所以在医用市场引起了极大的兴趣。
多种树脂的技巧
Gram公司和Ferromatik公司/Foboha公司两者都指出,可旋转叠层模具使它们发展了许多不同寻常的应用。其一是热塑性/热固性塑料,或“热/冷”成型。成型时,一种材料需要一个热模具进行塑化,而另一种材料需要一个冷模具以固化。Gram公司设计了一套2+2型腔的旋转叠层模具,用来加工带有内部硅橡胶垫圈的尼龙,用于汽车零件。虽然尼龙/硅成型的目的是在两者之间达到良好的粘接,Gram公司和Ferromatik公司/Foboha公司利用了一个四面旋转叠层元件来达到相反的效果。如果第一个制品在重叠注塑前已经足够彻底地冷却了,最终制成制品的两个组分能彼此相对地自由滑动。
Gram公司用此法演示成型一种阀门,其中一个零件在另一个零件内滑动。另一个实例是成型具有三角形顶面的果汁盒所用的连同管口的螺旋盖。首先成型果汁盒的PP共聚物盖,旋出型芯,然后LDPE管口使用一组新型芯在盖内部成型。因为盖冷却时间长了一个额外的周期,并且第二次注射的LDPE熔融温度较低,盖和管口不会粘连在一起。
打破尺寸的障碍
叠层模具技术首次突破障碍,进入在大于1000 t的机器上成型大型零部件的应用领域。Plastcoat公司正在使用一种在每个面上有一个型腔的Husky公司的双层叠层模具,为福特公司的XLT型卡车同时生产前后旋转照明灯。另一种1+1叠层模具正在为丰田公司的Camry生产线制造摇臂。这种零件各有数英尺(ft)长(1ft=0.30 m),使用300 g的热塑性聚烯烃(TPO)。这种零件在Husky公司的2200 t EWLL(加宽、加长)两板式成型机上成型。
“叠层模具的主要优点是节省占地面积,”成型操作经理Rebecca Branca说。周期时间一般讲与在两台具有相同吨位能力的不同机器上运转的成型模具相符合,她说。
此模具有一种独特的在模具下面运转的注道杆(sprue-bar)。它将熔体分配到叠层模具的托架上。托架有一个给两个模具供料的独特的热流道系统。Husky公司设计的流道使熔体系统总是处于平衡状态,即使A侧和B侧的零件不同,成型维修部门经理Roy Zinner说。
当模具打开时,注道杆分为两半,一半连接到固定模板,另一半连接到叠层模具托架上。一个“协调的”杆拉住模具所有的部分到一起进行合模。此杆可以调节,以适应两侧不同的模具高度。Plastcoat公司每个工作班约生产600只零件。
声明:本网站所收集的部分公开资料来源于互联网,转载的目的在于传递更多信息及用于网络分享,并不代表本站赞同其观点和对其真实性负责,也不构成任何其他建议。本站部分作品是由网友自主投稿和发布、编辑整理上传,对此类作品本站仅提供交流平台,不为其版权负责。如果您发现网站上所用视频、图片、文字如涉及作品版权问题,请第一时间告知,我们将根据您提供的证明材料确认版权并按国家标准支付稿酬或立即删除内容,以保证您的权益!联系电话:010-58612588 或 Email:editor@mmsonline.com.cn。
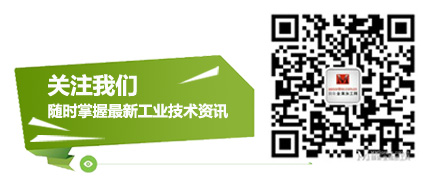
- 暂无反馈