铸锻机械行业“十二五”面临转型挑战
在不久前召开的铸造和锻压机械两个分会理事会上,铸、锻机械分会理事长刘家旭表示,《国家中长期科学和技术发展规划纲要》精辟地指出,“制造业是国民经济的主要支柱。我国是世界制造大国,但还不是制造强国;制造技术基础薄弱,创新能力不强;产品以低端为主;制造过程资源、能源消耗大,污染严重。”而这些问题在我国铸造和锻压行业尤为突出。我国与德国、日本等国外先进制造国家相比,各个门类的设备普遍落后,例外寥寥,有目共睹。
存在三大不足
刘家旭指出,从行业“十一五”发展状况分析,不足之处主要存在于三个方面。
其一,有而不精,大而不强。铸造机械、锻压机械传统上被认为是简单粗放的设备,使用环境也远差于其他机床。尽管已有相当数量的产品水平高、制造精细的铸造设备、锻压设备乃至成套生产线,依然难以改变其进入门槛低、制造粗放的现状。我国铸造和锻压机械行业依然长期存在着规格品种基本齐全,但中低档产品过剩、高档产品缺乏的状况。这从2010年我国锻压机械进出口数据中得以证明:进口是出口的3.3倍,进口数控锻压机床是全部出口的1.78倍。铸造机械的进出口对比也如出一辙。这反映了市场对中高端产品需求明显增加,也反映出国产中高端产品在技术水平、产值上都存在明显不足,无法在产品质量、技术指标、用户服务等方面满足用户需求。
对中小规格、普通型的产品我们仅仅解决了有无的问题,高档产品仍然依靠进口;在大、重、特型设备方面,问题则更加凸显。我们国产数控机床国内市场占有率已达到57%,但这个占有率数据构成大部分是低档数控机床,属于中高端的部分比例较低。
对比我国自行设计制造的大型自由锻液压机和中信重工与德国合作生产的185MN自由锻液压机,不光技术指标跟不上,软硬件两方面都有差距。我们欠缺很多深层次的技术,比如,该液压机和锻造操作机程控联动技术。
其二,创新能力差,技术进步滞后,资源消耗大,产品附加值低。总体上来说,我国铸造机械、锻压机械企业创新能力不强。在技术创新投入和扩大产业规模之间,众多企业更愿意选择后者。在一个市场需求旺盛的环境下,扩大产业规模可以获得短期效益,但不一定有长远效益。这种短期行为倾向既有企业自主冲动,更有地方政府的推动。由于企业管理落后,虽然我们投入的人力物力资源比国外多,但我们的产品综合性能差、可靠性差、寿命周期短、外观粗糙,只能靠低价竞争。质量差、技术含量低的产品根本谈不上产品附加值。配置相当、主要功能基本相同的国产设备价格仅是德、意、日等国同型产品价格的1/3~1/2;尽管我们心有不甘,但国外产品在精度、可靠性、设计深入周全、做工精细等方面的确技高一筹。
在高端、特型产品方面,欧美、日本等企业的创新意识和创新能力值得我们学习和借鉴。由于企业管理能力差、人才缺乏和对人才战略重视不够,我们基本上处于模仿或模仿再创新阶段,自主创新能力很低,原创性技术严重缺乏。
其三,重规模轻内涵,重硬件轻软件,重“能做”轻“做好”。近些年来,我国铸造机械和锻压机械行业持续高速发展,大多数行业企业都取得了显着的发展成就。而伴随高速发展,企业最普遍的特点就是经营规模迅速扩张,并且成为了一种行业企业的“发展惯性”。不少企业规模越做越大,却忽视了企业的内涵发展与建设。与过去相比,我们确实能做许多过去做不了的设备,比如一些大规格、大吨位的产品,一些多工序复合的产品等。但这些产品真正达到高精尖水准的还不多,大部分产品仅仅停留在“能做”的初级阶段,距离“做好”和“做出特色”还有较大差距。我们片面重视制造能力等硬实力的扩张,而一定程度上忽视技术创新能力、市场运作能力、管理能力和文化内涵等软实力的建设。在产品开发上,重有形的功能和规格指标的实现,忽视无形的技术附加值建设;在产品制造上,重有形的装备能力建设而忽视知识积累、工艺提升和稳定的质保体系建设;在市场开发上,重视订单实现而忽视用户服务、用户体验及用户增值服务。所有这些,正是制约行业中高档产品市场竞争力提升的重要因素。
市场不容乐观
2010年,大重型机床市场热度率先降温。而今年二季度以来,国内机床工具市场明显整体回落。从行业统计数据看,尽管由于惯性原因,行业整体产出和增长水平仍然处于高位,但已表现出明显的下滑趋势。最突出的表现有两个方面,一是产成品库存上升幅度较大(至8月末,全行业产成品库存增加21%,其中金切机床增加24%,锻压成形机床增加34%);二是企业新增订单显着下降(8月份同比下降51%,环比下降35%)。而在国内市场需求下降的同时,一些国外竞争对手推出高性能低价格产品,其战略意图正是针对中国市场和中国的竞争对手。因此,无论目前情况还是未来的发展趋势,我们过去依赖的主要发展优势都将逐步消失和弱化,这将逼迫我们必须下决心做出战略调整。
从我们目前得到的一些情况来看,锻压行业企业中,有些因中小型、普通型机床市场阻滞而受较大影响,有些因出口受阻而陷入困境,有些则因产值数控化率较高、产品市场主要面向国内而暂时相对平稳。但总体上,行业企业普遍面临新增合同额下滑及资金紧张局面。
由于我国前期四万亿元拉动内需产生的一定提前消费,国际市场发展趋势的不确定性,一些国家出现的政治动荡,美国为解决债务问题而采取的货币政策使全球通胀压力的增大,国家宏观经济调控的初见成效等诸因素影响,使得我国机床行业市场在经过近两年的高速增长后,从今年开始出现增速趋缓迹象。
目前行业人士都在关注世界经济是否“二次探底”的问题。而若再次出现危机,各国政府再次大规模救市的可能性已经不大。而我国经济增长依赖出口和投资拉动的状况并未根本改变,目前这两方面的增长动力已经明显下滑。可以预计,今后一段时间内宏观经济增长将会减缓,随之机床工具行业的需求增长也将趋缓。
在增长速度回落和全社会调结构、转方式双重因素的作用下,目前市场需求结构正在加速升级。这一趋势将使得原本中高端市场需求不能满足、中低端市场产能过剩的产业结构矛盾愈加突出。调结构、转方式迫在眉睫。
面临严峻挑战
在当前的经济形势下,行业企业将面临新一轮的严峻挑战。企业生产成本和各项费用已经或将有所提高,主要表现在以下几个方面。
一、原材料价格上涨。截止到今年8月,黑色金属材料类上涨11.6%,燃料动力类上涨11%。二、劳动力成本上升。最近两年来我国劳动力报酬处于上涨趋势,进一步压缩了企业利润;三、人民币升值预期依然存在。汇改以来人民币已经升值30%以上,而今年以来人民币升值幅度有可能达到4%~5%。面对能源、原材料价格上涨和利率、汇率大幅波动压力,企业承接大单、长单的预期进一步减小。四、企业财务费用增加。今年以来,央行已连续6次提高存款准备金率,中小企业货款利率普遍上浮,货款难度进一步加大,企业资金链经受严峻考验;五、产成品资金占用增大。产成品资金占用和应收账款同时大幅上升,加剧了企业资金困难。据分会得到的信息,用户推迟提货,或要求合同延期的情况已有发生,甚至有的用户不惜损失定金而终止合同。这些情况都加重了企业的资金积压。
汽车行业是机床行业的最大用户,其每年的机床工具消费额约占机床工具行业总消费额的40%。从某种程度上说,汽车行业是机床工具行业经济形势的晴雨表。
我国汽车市场经历了连续十年年均25%的增长,特别是2010年“爆发式”增长后,今年开始进入新一轮调整周期。累计到8月份,我国汽车产销量分别为1186万辆和1198万辆,同比仅增长3%和3.3%。据汽车协会有关人士的预测,今年全年汽车销量将比去年增长5%。这一数据与之前的年均增长25%形成了明显对比。
除了汽车工业,高速铁路建设也进入调整周期。而国家对于房地产的调控也开始显现效力。综合各方面因素,短期内经济预期仍不明朗,预计未来几个月总体趋势仍然是缓慢回落。
与会企业均认为,应在密切关注市场的同时,要积极做好应对预案,在企业的资金、产能等各种资源上统筹安排,合理应用;在技术进步、调整产品结构上痛下功夫;充分发挥各自企业特长,形成具有差异化的核心竞争力,争取在日益变化的市场条件下,求得生存和发展的机会。
声明:本网站所收集的部分公开资料来源于互联网,转载的目的在于传递更多信息及用于网络分享,并不代表本站赞同其观点和对其真实性负责,也不构成任何其他建议。本站部分作品是由网友自主投稿和发布、编辑整理上传,对此类作品本站仅提供交流平台,不为其版权负责。如果您发现网站上所用视频、图片、文字如涉及作品版权问题,请第一时间告知,我们将根据您提供的证明材料确认版权并按国家标准支付稿酬或立即删除内容,以保证您的权益!联系电话:010-58612588 或 Email:editor@mmsonline.com.cn。
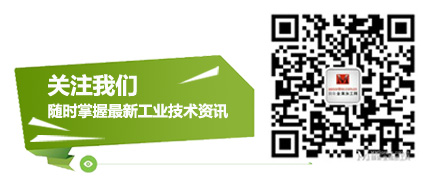
- 暂无反馈