车床加工间隙、加工精度和表面质量
1.加工间隙
电解加工的加工间隙是决定加工精度的主要因素,车床也是设计工具阴极和选择工艺参数的主要依据。机床电器在电解加工过程中,当工作电压和进给速度恒定时,随着工具阴极的不断进给,底面加工间隙逐渐趋进一个稳定值——平衡间隙。初始间隙不同,则达到平衡间隙所需的时间也不同。平衡间隙的大小一般在0.1—0.5mm之间。平衡间隙小,则加工精度高;平衡间隙大,则加工精度低。但加工间隙过小则易发生短路。因此平衡间隙的范围以0.2—0.5mm为宜。电解加工间隙除了底面间隙外,还有侧面间隙和法向间隙。
2.加工精度
加工精度包括复制精度(加工表面相对于工具阴极型面的尺寸偏差)和重复精度(同一加工条件下,一批工件间同一加工表面的尺寸偏差)。
加工精度与被加工表面的几机床电器何特征有关,可达到的精车床度范围大致如下:型孔加工或套料为±(0.02—0.05)mm,锻模型面为±(0.05~0.20)咖,扭曲叶片型面约为0.2mm。提高加工精度的措施主要有以下几点:
(1)机床及工艺装备方面。提高机床刚性;提高机床进给系统的平稳性;采用有足够稳压精度的直流电源;采取有效的过滤方法,保证电解液的洁净;采用合理的夹具,保证足够的定位精度。
(2)电解液方面。采用以硝酸钠等为基体的钝化电解液,或适当降低电解液浓度;严格控制电解液温度、浓度及pH值的变化;采用混气加工方法,改善电解液的工艺特征。
(3)工艺参数方面。适当提高进给速度,实现小间隙加工;适当提高电解液压力和流速,使之与电流密度相匹配。
(4)工件方面。工件毛坯余量应力求均匀;工件材料组织要均匀、致密。
(5)工具阴极方面。正确设计工具阴极型面车床;合理安排出液槽及排气孔,使机床电器流场尽可能均匀分布。
(6)直流电源方面。提高稳压精度;采用脉冲直流方式且频率容易调整;适当提高加工电压。
3.表面质量
影响电解加工表面质量的因素很多,主要有工件材料及其热处理状态,电解液成分与浓度、温度,加工参数(电流密度、加工电压)等。这些因素将会给加工表面造成各种缺陷,如选择性腐蚀(工件材料各相溶解速度不均匀所致)、晶间腐蚀(电解液选择不当,某些材料的晶间机床电器处被优先溶解,产生微小裂纹)、流纹(电解液流场不均匀而产生的)等。晶间腐蚀和选择性腐蚀大多发生在靠近加工区附近的工件表面,即电流车床密度较低的表面上。这类缺陷将使工件的疲劳强度降低。
为了防止加工表面产生上述缺陷,可采取以下措施:
(1)根据不同的工件材料,选用合适的电解液。必要时应考虑选用多组分电解液,使工件材料均匀溶解。
(2)工件应选用合理的热处理方式,使其金相组织均匀,晶粒适度细化。
(3)合理设计工具阴极上冲液孔位置,必要时应做模拟试验,力求加工区流场分布均匀。机床电器同时,电解液流速与电流密度要合理匹配。
(4)对阴圾上非加工表面进行绝缘处理(喷涂环车床氧树脂等),对已加工表面尽可能采取屏 蔽措施,以避免杂散电流的腐蚀。
(5)合理选择加工参数,以缩小底面间隙和侧面间隙,提高电流密度。
1.电解液的作用
电解液的作用大致有以下几方面:与车床被加工材料组成进行电化学反应的电极体系,以实现电解加工;将加工区产生的电解产物及时排出,使加工得以正常进行;将加工过程中产生的热量带走,控制加工区的温度。
2.对电解液的要求
对电解液的要求为:能使工件材料高速、均匀溶解;电解质溶液中的金属离子不得在阴极表面沉积或镀覆;具有一定的电导率,黏度较低,在小间隙中流动性好;安全、无毒、腐蚀性小,对人体应无伤害;成分稳定,价格低廉。
在实际生产中,要同时满足上述要求是十分困难的,车床只能根据加工对象的表面质量和尺寸要求来做出选择。
声明:本网站所收集的部分公开资料来源于互联网,转载的目的在于传递更多信息及用于网络分享,并不代表本站赞同其观点和对其真实性负责,也不构成任何其他建议。本站部分作品是由网友自主投稿和发布、编辑整理上传,对此类作品本站仅提供交流平台,不为其版权负责。如果您发现网站上所用视频、图片、文字如涉及作品版权问题,请第一时间告知,我们将根据您提供的证明材料确认版权并按国家标准支付稿酬或立即删除内容,以保证您的权益!联系电话:010-58612588 或 Email:editor@mmsonline.com.cn。
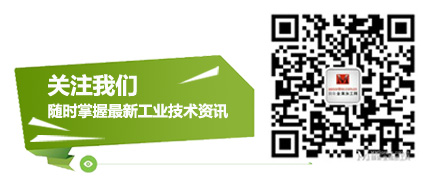
- 暂无反馈