模具超精密研磨抛光与焊接
近年来,在世界范围内制造业的竞争变得越来越激烈,企业在尽可能短的时间内高效率,低消耗的为顾客提供个性化高品质产品的能力,已成为企业竞争能力的一个标志。模具品质的高低将直接影响到产品的质量、产量、成本、新产品投资及老产品更新换代要求。那么,如何才能更有效的提高模具品质呢?也就是说,如何才能让模具在高精度、低成本、高效率条件下,生产出高品质的合格制件?这与模具表面处理有很大关系,也日益成为各企业关注的焦点。模具表面处理并不是一个简单的话题,它包括模具抛光与模具焊接等。
模具抛光
众所周知,塑料模具钢需要一个很好的抛光技能来体现材料本质的性能,但抛光问题一直是企业无法根本解决的一个难题。桥本工业已达到高品质顾客企业所认同的研磨技术的要求。日益精进的技术,创造出无法仿效的镜面精加工效果,从对使用钢材的建议到微小孔的解决等问题,及各种形状复杂的精密零件。
抛光中遇到的最大问题就是“抛光过度”,抛光过度是指抛光时间越长,模具表面质量越差。发生抛光过度时有两种现象,即“桔皮”和“微坑”,抛光过度多发生于机械抛光。
“桔皮”
不规则、粗糙的表面被称为“桔皮”,产生“桔皮”有许多不同的原因。最常见的原因是由于抛光压力过大及抛光时间过长,以及抛光方法不当等.
发现表面质量不好,许多人就会增加抛光压力,并延长抛光时间,加上抛光流程的不当,往往会使表面质量变得更差。
“微坑”
“微坑”或“砂孔”的形成是由于钢种的非金属夹杂物(杂质),通常是硬而脆的氧化物;在抛光过程中从钢材表面被拉出,形成“微坑”或“砂孔”。主要影响因素如下:
1、抛光压力和抛光时长;
2、钢材的纯净度,特别是硬性夹杂物(杂质)的含量;
3、抛光工具;
4、研磨材料。
抛光操作的流程
如何选择研磨和抛光的操作次序,完全取决于抛光操作者的经验及其使用的工具与设备。材料的特性对操作程序也有影响。
抛光流程1
考虑加工效率首先要确认加工品的粗糙程度,这个作业要谨慎进行不能有错误,根据粗糙程度也有不能作业的可能,确认加工品的粗糙程度然后根据形状选定油石进行抛光,抛光方法的次序是根据油石的粒度由粗至细进行。
油石抛光方法,这个作业是最重要的高难度作业,根据加工品的不同规格,分别约70度的角位均衡的进行交叉研磨。最理想的往返范围约为30毫米~60毫米。油石作业也会根据加工品的材质而变化。
抛光流程2
油石作业结束后是砂纸作业,砂纸作业时,要注意模仁的圆边、圆角和桔皮的产生。所以油石流程尽量做到最细加工。
砂纸抛光的重点。砂纸配合较硬的木棒像油石作业一样约70度角交叉地进行研磨,一面砂纸研磨次数约10次~15次。如果研磨时间过长,砂纸的研磨力会减低,这样就会导致加工面出现不均匀现象(这也是产生橘皮的原因之一)。
砂纸作业时一般都采用竹片进行研磨,实际使用材质弹力小的木棒或硬度低的铝棒约45度角进行研磨是最为理想的。研磨面不能使用橡胶或者弹性高的材料,不能用45度角研磨的形状可以用锐角。砂纸有很多种类,最重要是要选择适用的。
抛光流程3
用钻石膏进行镜面加工,砂纸作业后取适当的钻石膏和稀释液进行混合,用电动回转工具马毛刷慢慢的来回研磨。注意点:马毛刷研磨面要保持水平线。从6µ~3µ进行研磨,然后用泡棉配合1µ钻石膏就可以完成镜面加工。
抛光的最后一个程序有两种方法:一是电动工具和气动工具的抛光方法;二是手工抛光方法。但是对于平面形状和球面形状也有不同的情况。
镜面抛光的要点
超镜面抛光时最重要的一点是抛光的尺寸,油石研磨到镜面抛光的距离是10µ。(最理想是#1500油石开始进行研磨)最基本的原则,在进行下一步作业之前,一定要将模仁彻底清洗干净,才会达到好效果。要非常慎重不要重复修改(反复修改会影响品质问题)。
纳期的期限、时间上的压力、过度疲劳、集中力下降,这些因素都容易影响工作,这一点要非常注意。
抛光操作是一项耗费时间和费用昂贵的工序,遵照一定的守则可以降低抛光操作的成本。抛光的每一个步骤都必须要保持清洁,这一点最重要。
1、抛光必须在清洁无尘的室内进行。因为硬尘粒会污染研磨材料,损害已接近完成的模具表面。
2、每个抛光工具只使用一个级别的抛光钻石膏,并存放在防尘或密封的容器内。
3、当要转换更细一级的砂号时,必须清洗双手和工件。
4、开始抛光时要先处理角落、边角和圆角等较难抛光的地方。
5、处理尖角及边角时应特别小心,注意不要形成圆角或圆边,应尽量采用较硬的抛光工具进行模具的研磨和油石打磨。
影响表面抛光性的因素
采用研磨的方法可使模具表面光洁,光洁的程度与下列因素有关:
1、钢材品质(钢材表面硬度不均匀或特性上有差异往往会增大抛光难度)。
2、热处理工艺(热处理在很多方面会影响到抛光性能)。
3、抛光技术(抛光工艺与抛光耗材的采用直接影响到抛光效果)。
通常认为抛光技术是最重要的影响因素,恰当的抛光技术、采用良好的抛光耗材、配合品质优良的工具钢材及正确的热处理工艺才能达到满意的光洁度。反之,抛光技术与耗材使用不当,即使采用最优质的钢材也不会达到高度镜面的效果。
模具焊接氩弧焊技术
模具焊接氩弧焊技术是国内外发展最快、应用最广泛的一种焊接技术。近年来,氩弧焊特别是手工钨极氩弧焊,已经成为各种金属结构焊接中必不可少的手段,所以对氩弧焊工的需求也越来越大。近些年来,氩弧焊的机械化、自动化程度得到了很大的提高,并向着控制因子越来越多的数控化方向发展,达到了一个更高的阶段。
氩弧焊之所以能获得如此广泛的应用,主要是因为有如下优点:氩气保护可隔绝空气中氧气、氮气、氢气等对电弧和熔池产生的不良影响,减少合金元素的烧损,以得到致密、无飞溅、质量高的焊接接头。氩弧焊的电弧燃烧稳定,热量集中,弧柱温度高,焊接生产效率高,热影响区窄,所焊的焊件应力、变形、裂纹倾向小;氩弧焊为明弧施焊,操作、观察方便;电极损耗小,弧长容易保持。氩弧焊几乎能焊接所有金属,特别是一些难熔金属、易氧化金属,如镁、钛、钼、锆、铝等及其合金。所以,桥本在10年前就引进了SW-V01日本原装的超高精度填充式氩弧焊接机,其特点如下:
1、极小的热度影响
本机由于工作在精密模式,可以精确的设定电流(2~200A)时间(1~500ms),保证输入的能量仅够用于焊丝与工件之间的溶合,不会有太多能量作用于工件,受热度影响降到至最低,从而达到理想修补效果。
2、极高的结合度
本焊机属于焊接时,材与基体达到冶金熔合。焊后的结合度极高。可适用各种加工方式,不会出现其它焊机焊后结合不牢固、脱落等现象。
3、精确的细小部位补焊
由于焊补电流,时间得到精确的控制,电流短时间也可稳定运行,而精密小的部位也可以得到理想的焊补。
4、焊接极薄厚度
由于焊接电流最小可在2A稳定运行,因此焊接的最小厚度也相应的降到0.1mm。
5、适用于不同部位的补焊
平面部位的凹陷、孔、洞、细缝、沟槽、棱角、棱线,尖峰部位、沙眼及普通焊机焊后周边的凹陷。补焊放电加工、渗氮及软氮化处理后的模具。
6、焊接导航
只要指定焊接场所、焊接材料的尺寸,就会自动设定和显示适当的电流、时间。
7、连续TIG模式
在进行大范围焊接时,使用连续TIG模式可获得比激光焊接更流畅的焊接性和速度性(间隔时间:0.1秒~2.0秒)。
声明:本网站所收集的部分公开资料来源于互联网,转载的目的在于传递更多信息及用于网络分享,并不代表本站赞同其观点和对其真实性负责,也不构成任何其他建议。本站部分作品是由网友自主投稿和发布、编辑整理上传,对此类作品本站仅提供交流平台,不为其版权负责。如果您发现网站上所用视频、图片、文字如涉及作品版权问题,请第一时间告知,我们将根据您提供的证明材料确认版权并按国家标准支付稿酬或立即删除内容,以保证您的权益!联系电话:010-58612588 或 Email:editor@mmsonline.com.cn。
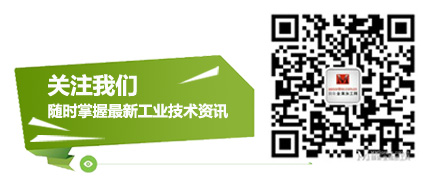
- 暂无反馈