计算机化产品定义及其在模具CAD中的应用研究
1. 引言
随着计算机及其相关技术的迅猛发展,计算机辅助技术CAD、CAPP、CAM、CAE(计算机辅助工程分析)等得到了模具行业的普遍重视,在一定程度上提高了产品及模具设计的效率和质量,促进了行业的进步。但是从总体上来看,传统的模具计算机辅助设计软件存在着下列不可忽视的不足:
(1)CAD软件没有真正将模具设计人员从繁重的绘图工作中解放出来,设计效率的提高不理想;
(2)CAD、CAE、CAM集成度差,总体效果不明显;
(3)市场需求分析、制品设计、模具设计、模具制造相互独立,生产管理缺乏全局观念。现代市场竞争日趋激烈,从90年代到下个世纪,使满足用户需求的新产品尽快上市而赢得市场竞争将成为制造业的第一要旨,新产品投放市场的速度决定了生产厂家的生死存亡。传统的各自为政的模具计算机辅助工具已无法适应当前的这种需要,提高产品与模具质量、缩短产品开发周期、降低成本的根本途径是简化设计过程,采用基于各个单项计算机技术的计算机集成制造(Computer Integrated Manufacturing,CIM)和并行工程(Concurrent Engineering,CE)。集成制造与并行开发都是以各应用子系统之间的有效数据传递和产品数据交换为基础的,产品信息集成与计算机化产品定义(Electronic Product Definition,EPD)是实现CIM与CE的基础技术之一。计算机化产品定义?EPD是继特征造型之后的新一代产品建模方法。(所谓产品,在EPD中是指具有相对独立功能的零件或零件集,如一个成型的制件、一副模具的装配整体等。)
2. EPD的发展
产品造型与建模技术是计算机辅助设计技术中最为基础、同时也是最为关键的技术分支,CAD系统的发展与产品CAD系统的发展与产品建模技术的发展紧密相关。近30年来,产品数据建模技术经历了线框建模、表面建模、实体建模等过程,发展至80年代中期,为了实现CAD与CAPP的集成,基于特征的造型方法成为产品建模研究的热点。但是,这些产品建模方法对于计算机集成制造和并行工程而言,还存在很大的局限性,主要表现在:
(1)产品数据不完备:只涉及产品的几何形状数据,而反映设计意图和工艺要求的信息,如公差、粗糙度、材料、热处理、装配信息等没有表达或表达不充分,数据的抽象层次低,难以满足产品数据交换和信息集成的需要,不利于工程设计的数据表达;
(2)产品数据未考虑整个产品生命周期: 建立产品模型必须考虑到产品整个生命周期中各个过程所需要的信息,如设计过程、工艺规划、加工过程、装配过程等,这是当前市场需求变化多样、产品迅速更新换代的需要。一个完整的产品信息模型不仅是产品生命周期中各阶段数据的集合,还应反映出各类数据的表达方式及相互间的关系,传统的产品建模方法只考虑了产品的设计阶段;
(3)只考虑单个零件:传统的建模方法只考虑了单个零件的设计,但是机械产品(如模具)大多是多个零件的复杂装配体。这样,采用面向零件的设计方法就有很大的局限性:工程师可以设计产品的某个特定零件,例如顶杆,但是这个工程师不知道这个零件能否起到理想的顶出效果;建好实物模型以后,如果检查出这个顶杆不合理,极有可能要重新设计它。
由于传统产品建模方法在CIM及CE中应用的局限性,面向装配与产品生命周期的新型产品建模方法?计算机化产品定义应运而生。EPD将一个新产品从概念设计到制造成最终产品及销售的整个过程在计算机上用统一的数字化模型给予全面的描述。所有相关的设计部门及设计者、组织管理部门和最终的生产者,即使这些部门在不同地区工作都能够依据自身的权限对同一产品的计算机化模型进行并行的设计、修改和验证工作。EPD是目前最先进建模技术的综合体现,其发展的支撑技术主要有:
2.1 混合建模技术(Hybrid Modeling) 混合建模将传统的线框、表面、实体造型与参数化技术融合为一体,使得所有的模型基于同一的数学模型。混合建模具有的主要特点有:集成参数化线框、曲面和实体造型;约束管理;变量几何和智能化草图设计:用数学方法提供尺寸驱动,在草图设计过程中,几何关系以图形方式传递给设计者并被定义为维持分布与几何关系的新的约束;双向关联性:参数化实体与二维工程图有机结合,任何一方的修改可自动反映到另一方;基于特征的造型:基于特征的造型允许设计者用工程或制造专用名词(如孔、螺栓、槽)代替几何名词(如柱体、盒),允许用户快速地把设计意图汇合到产品设计中;NURBS曲面设计:由于NURBS本身独到的优越性,NURBS方法已成为曲线曲面设计的主流,应用NURBS能完成大型复杂曲面的造型。
混合建模技术结合当今流行的设计手段,将不同种模型形态集成到一起,以提供高度复杂的计算机化产品模型方案(如能生成以精确曲面为壳的实体),使得工程师可以设计更复杂、更精确的零部件,并相应减少产品的零件数量,加快建模速度和有助于自动化制作。同时混合建模技术大大加强了包括供应商和承包商在内的更宽广范围内的CAD数据共享,设计数据得以自由传递。
2.2 并行装配(Concurrent Assembly) 并行装配采用先进的多用户并行技术,允许工程项目全体设计人员同时操作装配数据库,完成各自的设计和修改工作,并用权限锁定方法保护共享资源,极大地提高复杂产品的开发设计速度。EPD强调以装配为中心,提供的图形化的装配树能直观显示大型复杂产品的装配链接关系,并支持零部件间的参数与装配约束。同时,通过为群组工作提供网络通讯环境,能支持异地的电子评审,并提供在计算机上实时召开CAD/CAM会议的能力。
2.3 产品数据管理(Product Data Management,PDM) 面向装配意味着面向关联信息,面向产品生命周期意味着面向过程信息,对复杂的产品数据和工作流程管理技术的迫切需求使得PDM成为EPD的支撑技术之一。PDM的功能包括:① 文档管理:PDM的文档管理取代人工方式的档案管理,使用户能够方便、快捷、安全地存取、维护及处理各种有关产品的文档。从调研阶段的市场报告,到设计阶段产生的图形数据文件、CAE分析报告,制造阶段可能产生的变更单等都是文档管理的对象。② 基于装配的产品管理:产品管理主要是建立产品装配树、对产品本身装配结构及其相关支持数据的管理、对零件族及产品配置的管理。数据管理软件允许用户在装配树的节点上,在权限许可的范围内访问和修改数据,不必考虑数据存放的具体位置,这样,就能将异地分布的设计队伍完全结合在一起。③ 工作流程管理:工作流程管理是对已建立的工作流程进行运行、维护、控制工作状态以及对工作历史过程进行记载的管理方式,使产品数据与其相关的过程有机地结合起来,实现对产品生命周期的多用户的分布式管理。④ 其它功能:项目管理、电子协作、组织与资源管理等。
3.基于EPD的模具CAD系统的特点与优势
由于EPD方法与传统的产品建模方法比较具有的无比优越性,基于EPD的模具CAD系统具有如下的显著特点:
3.1 面向装配 传统的模具CAD/CAM局限于模具单个零件的设计,虽然目前有些模具CAD系统在单个零件建模的基础上通过建立装配模型来考虑装配,但是由于其零件建模本身的局限,其应用效果不如人意。EPD的基本数学模型就是面向装配体的产品(在模具CAD系统中就是模具整体)而非单个零件,它集成了零部件和装配的全部可用信息,形成了一个包括各种信息的全局的电子化产品模型,这一模型可被不同设计环节的众多工程师使用。
3.2面向产品生命周期 所谓面向产品生命周期建模意味着从产品开发、制造到发布的信息的集成,产品生命周期中各个环节的信息均被统一到模型中并得到相应的管理维护。模具的设计制造通常是单件少批量,缩短其设计制造周期的关键是采用基于产品生命周期的设计。
3.3具有统一的数学模型 传统产品设计方法中的同一产品在设计过程的各个阶段具有多种定义模式,且相互独立,绝少参考。同一产品在不同设计阶段的重复定义使得最终产品的设计复杂程度不断累加和放大,增加了额外的协调与组织过程。其结果将导致最终产品品质的降低、研制费用上升和开发时间的延迟。EPD摒弃了传统的产品重复定义模式,建立从概念设计到制造的单一计算机化产品定义,覆盖了整个设计制造及管理过程。
模具的设计制造具有单件少批、复杂装配的特点,特别适合于应用EPD建模方法,采用EPD将产生的优势主要表现在:
3.3.1 EPD结合了先进的基于计算机的自动化设计软件和数据管理技术,通过缩短产品研制周期和降低成本,为长期生产效率的巨大提高奠定了基础。
3.3.2 EPD允许产品设计在制造实物模型(即真实下料生产)之前,在计算机屏幕上完成设计和验证工作。一项设计工作可由多个设计队伍在不同的地域并行分头设计、共同装配,形成一个完整的数字化模型,该模型不仅可完成强度、可制造性、成本和功能测试,而且还能展示给用户和买主。
3.3.3 EPD在计算机上定义完整的抽象产品模型,将大大节省生产实物模型的资金投入,由于设计原型能被反复引用,部件装配在系统中的干涉在计算机上能及时发现并予以解决,产品研制费用将降低,并减少由于设计问题出现的工程反复,加速产品上市。
3.3.4 EPD是面向装配的,它能够使工程师们在整个产品的装配环境下进行各自的设计,显示给工程师和项目管理者层次化的树状结构的装配模型,描述零部件之间面向大型装配的相互关系。EPD可跟踪查寻高度复杂的零部件和大型装配之间的内部关系,例如:项目经理可在任何时候查寻并显示那些超过设定重量的零件,并且在早期的产品设计周期内,不花费什么代价就可方便地更改设计。在模具中,各个零件之间的相关因素比较多,考虑装配是模具设计的基本特点。
3.3.5 面向产品生命周期的产品模型由于信息的完备性而有助于实现产品的设计兼容性分析(Design Compatibility Analysis,DCA)及以此为基础的考虑装配的设计(Design for Assembly,DFA)、考虑制造的设计(Design for Manufacturing,DFM)、考虑维修的设计(Design for Serviceability,DFS)和考虑注塑成型的设计(Design for Injection Molding,DFIM)等的DFX设计,而DFX的设计在提高模具设计的质量与速度方面具有重要的意义。
3.3.6 EPD能够使设计者用最少的零件实现产品的设计目标,极大地提高了企业针对市场情况变化的反应速度。因为设计者可设计单个复杂零件来代替中等复杂程度的子装配从而简化了产品设计复杂程度。有调查结果显示,一个大型装配件的零件数量从9250减少到3700,相应的工作量可从445000个工作日减少到60000个。更为重要的是,零部件减少意味着在无附加值的繁杂工作上花费的时间相应减少。
4.结束语
制造业发展的需要和计算机辅助技术的进步使得先进新型的产品建模方法。EPD将得到迅速地发展和应用,并将显示其显著的优越性。目前,EPD方法仍在研究之中,CAD/CAM领域著名的软件供应商CV公司已经开始向用户提供基于EPD技术的CAD软件。图1所示是CV公司的用户Shorts公司使用过的各种产品建模方法及工作效率的对比图。模具作为一种制造产品的工具,一直是制造业中的高技术基础和最有生命力的一个分支,在模具计算机辅助设计制造系统中应用EPD技术将有助于整个模具制造业竞争优势的提高,真正实现模具设计制造的高速、高效、高质。
声明:本网站所收集的部分公开资料来源于互联网,转载的目的在于传递更多信息及用于网络分享,并不代表本站赞同其观点和对其真实性负责,也不构成任何其他建议。本站部分作品是由网友自主投稿和发布、编辑整理上传,对此类作品本站仅提供交流平台,不为其版权负责。如果您发现网站上所用视频、图片、文字如涉及作品版权问题,请第一时间告知,我们将根据您提供的证明材料确认版权并按国家标准支付稿酬或立即删除内容,以保证您的权益!联系电话:010-58612588 或 Email:editor@mmsonline.com.cn。
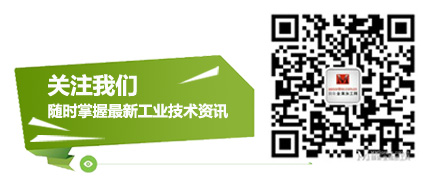
- 暂无反馈