注塑模的设计流程的研究
在中国制造业得到空前发展,尤其是中国家电、汽车等产业异军突起的今天,塑料制品的产量、品种日益增多,而且形状日趋复杂,精度要求也越来越高,更新换代的周期也越来越短,这对注塑模具的发展亦是提出了更高的要求,因此对于在模具生产的关键环节——模具设计,就显得尤为重要。总结模具设计工作经验,制定合理的设计流程,并遵照执行,无疑可以提高整体模具设计水平。
1.注塑模设计流程
1.1 接收任务书
塑件任务书通常由塑件设计者提出,其内容主要包括:
1)经过审核、会签的正式塑件图纸,并注明塑件采用塑料的牌号、表面粗糙度和尺寸精度等技术信息。
2)塑料说明书或技术要求(对于常规工程塑料可通过查阅相关技术手册获得)。
3)塑件预期产量情况。
4)塑件样品(改进型或仿制类制品可提供)。
模具设计任务书由塑件工艺员根据塑件任务书提出,模具设计人员则根据塑件任务书和模具设计任务书来进行模具设计。
1.2 收集、分析、消化原始资料
收集整理有关塑件设计、成型工艺、所用设备、机械加工及特殊加工方面的资料,为模具设计做准备。
1)消化塑件图,了解塑件的用途,分析其工艺性、尺寸精度等技术要求。如塑件的形状、颜色、透明度、使用性能、几何结构、斜度、有无嵌件等;熔接痕、收缩等成型缺陷的许可程度;有无涂装、电镀、胶接、机械加工等后加工工序。对塑件图中精度要求最高的尺寸进行分析,估计成型公差是否低于塑件的公差,可否成型出合乎要求的塑件来。此外,还要了解塑料的塑化及成型工艺参数。
2) 消化工艺资料,分析工艺任务书所提出的成型方法、设备型号、材料规格、模具结构类型等要求是否恰当。成型材料应当满足塑料制件的强度要求,具有好的流动性、均匀性和各向同性、热稳定性。根据塑件的用途,成型材料应满足染色、电镀的条件、装饰性能、必要的弹性和塑性、透明性或者反射性能、胶接性或者焊接性等要求。
3)选择成型设备,了解要采用的注射机的注射量、锁模压力、注射压力、模具安装形式及尺寸、顶出装置及尺寸、喷嘴孔直径及喷嘴球面半径、主流道浇口套定位圈尺寸、模具最大厚度和最小厚度、模板行程等。初步估计模具外形尺寸,判断模具能否在所选的注射机上安装和使用。
2.3 模具详细结构方案
1) 型腔布置。根据塑件的特点,考虑设备条件,决定型腔数量和分布形式。
2) 确定分型面。分型面的位置要有利于模具加工、排气、脱模及成型操作,有利于保证塑件的表面质量。
3) 确定浇注系统。即主流道、分流道和内浇口的形式、位置、大小。
4)排气系统。排气方法、排气位置、尺寸。
5)选择顶出方式。顶杆、顶管、顶板、组合式顶出等。
6)决定侧凹处理方法,即抽芯方式。
7)决定冷却、加热方式及加热冷却沟槽的形状、位置、加热元件的设计或选用及安装部位。
8)模具材料,进行强度计算或查阅经验数据,确定模具各部分厚度及外形尺寸、结构及所有连接、定位、导向件位置。
9)确定主要成型零件的结构形式。
10)计算成型零件的工作尺寸。
2.4 绘制模具图
2.4.1绘制总装图
尽量按比例绘制,并由型腔部分开始。模具总装图包括如下内容:模具成型部分结构;浇注系统、排气系统的结构形式;分型面及脱模方式;外形结构及所有联接件、定位、导向件的位置;模具的总体尺寸即:长、宽、闭合高度;按顺序编出全部零件序号,并填写明细表;标注技术要求和使用说明;塑件图。
2.4.2 绘制零件图
一般来说,由总装图拆绘零件图的顺序为:先内后外;先复杂后简单;先成型零件,后结构零件。图纸表达的各种信息要完整、准确,原则上按比例绘制,视图选择要合理,投影正确,使加工者容易看得懂,给装配人员提供尽量准确有用的信息,零件图尽可能与装配图一致;标注尺寸要统一、集中、有序、完整。尺寸标注时应按照先主要零件尺寸和脱模斜度,再配合尺寸,最后其它尺寸的顺序;其它内容如:零件名称、模具图号、材料牌号、热处理和硬度要求、表面处理、图形比例、自由尺寸精度等级、技术要求等均要填写完整;校对、审图,校对的内容包括:复算主要零件、成型零件尺寸和配合尺寸;检查总装图上有无遗漏零件,总装图与零件图有无矛盾;检查零件图有无尺寸遗漏;材料、热处理等要求是否恰当。
3.模具设计的标准化
一副模具从设计到制造完成的时间过去需要三个月左右的时间,目前最短也需要一个半月到两个月,其制造工时从几百小时到几万个小时不等,如何设法减少繁重的设计和制造工作量,缩短生产准备时间,以降低制造成本,最大限度地推行标准化设计是实现上述目的的有效途径。标准化工作的内容包括以下几个方面:
1) 模具整体结构标准化。根据生产设备的规格,定出若干种标准结构和外形尺寸,在设计模具时,仅绘制部分零件图,标准部分可以预先制造,这样一来可以大大缩短设计和制造周期。
2) 常用模具零件标准化。凡是能够标准化的模具零件和部件,应尽量标准化,使模具零件具有一定的互换性。
3) 模架的标准化。对于生产批量小、品种多、形状简单、生产急用的模具,尽量采用标准模架,不仅缩短设计和制造周期,而且能够降低成本。
4.结束语
模具设计是一项技术含量很高的工作,不仅要求设计人员具备相当的理论知识基础和丰富的实践经验,而且要求他们养成认真细致的工作习惯,如果按照设计流程来展开工作,一定会减少不必要的技术失误,进而对提高设计工作效率,缩短整个模具周期,降低生产成本产生积极的影响。
声明:本网站所收集的部分公开资料来源于互联网,转载的目的在于传递更多信息及用于网络分享,并不代表本站赞同其观点和对其真实性负责,也不构成任何其他建议。本站部分作品是由网友自主投稿和发布、编辑整理上传,对此类作品本站仅提供交流平台,不为其版权负责。如果您发现网站上所用视频、图片、文字如涉及作品版权问题,请第一时间告知,我们将根据您提供的证明材料确认版权并按国家标准支付稿酬或立即删除内容,以保证您的权益!联系电话:010-58612588 或 Email:editor@mmsonline.com.cn。
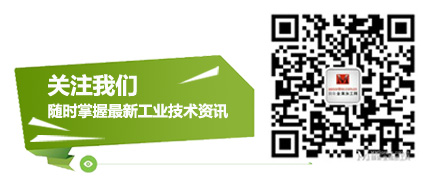
- 暂无反馈