快速成型在改革精密铸造中的应用
目前国内精密铸造生产存在问题是: ① 生产周期长、生产成本高; ② 造型不能重复使用,难以实现高效、规模生产; ③ 造型材料消耗大、粉尘严重,不仅需要较大的存放、作业场地,而且作业现场污染严重,影响工人的身体健康。因此,铸造一直被认为是生产工艺原始、生产效率低下、污染严重的行业。而精密铸造十 RP 系统能有效地解决以上问题,能有效提升国内铸造业整体的技术、工艺水平,提高产品的市场竞争力。
快速成型和精密铸造是互补的,两种方法都适合于制造复杂形状的零件。没有快速成型技术,铸模的生产就是精密铸造的瓶颈过程;而没有精密铸造,快速成型技术的应用就有了很大的局限性,将快速成型技术与精密铸造技术相结合,就产生了快速精密铸造技术。快速成型在精密铸造领域的应用主要有下面几点。
1)直接制造精铸母模
以精铸蜡为原料,直接成型精铸蜡模,再通过传统精铸过程制造金属零件。其工艺流程如图6-10所示。用这种方法来生产发动机缸体及缸盖等零部件,与传统精铸生产方法根比,既经济又快捷。
2)硅橡胶--石膏型精密铸造
用快速成型方法制作树脂或蜡质原型,用它翻制硅橡胶模和石膏型。其工艺流程如图6-11。
它尤其适合小批量的铝、镁等非铁合金发动机部件的铸造生产。
3)制造精铸型壳
用 DSPC法可以直接制造精铸用耐火型壳,省去了传统精铸中的压型制造、压制蜡模、组模及制壳等多道工序。大大缩短了熔模铸造的生产周期。同时消除了熔模变形等因素对型壳尺寸的影响,可以快速制得高精度的铸件。
陶瓷型铸造作为传统的梢密铸造工艺是最重要的精铸模具方法,其铸造模具的尺寸精度高(可达0.3~0.35mm/100mm)、表面粗糙度可达Ra3.2~1.6um、铸件抗疲劳强度高、使用寿命长、且不受金属种类和铸件大小的限制。这种精密铸造方法在国外已广泛用于制造锻模、冲压模、压铸型、玻璃模等。结合 SL 原型技术,西安交大实现了陶瓷型壳精密铸造。从铸造角度分析,以熔模铸造作比照,基于SL 原型的陶瓷型壳精密铸造有以下特点:
(1)原型与蜡模相比,高温变形温度高。 SL 原型在60~ 80 ℃ 才开始变形,而蜡模一般不能高于 30 ℃ ,所以每层挂桨撒砂后干燥时间差别很大。如都挂八层,由于对吹风式电干燥箱温度设置不同, SL 原型型壳在 55 ℃ 下干燥,而蜡模型壳在25~30℃ 下干燥。SL 原型的陶瓷型壳制作仅仅需要 6~8h ,蜡模型壳制作需要 80 ~100h 。
(2 ) SL 原型与型壳焙烧同时进行, SL 原型被汽化掉,不需要脱模。
基于 SL 原型的陶瓷型壳精密铸造实例
a精密铸造标准试样 ;
b注肥器SL 原型及铝合金铸造件;
c摩托车发动机外壳SL 原型及铝合金铸造件。
功能零件无模具快速精铸
采用光固化原型代替蜡模铸造功能零件这一工艺方法为数量较少及单件复杂精密零件成型提供了无模具的快捷制造方法。这一方法可与 CAD 技术集成起来,通过CAD-RP 原型/烧失法精铸/测量修正 CAD 数据的循环迅速获得精确的成型零件为渐产品的快速研制提供了一个非常有前景的技术途径。在复杂形状零件的单件、小批量生产时降低制造周期并节约制造成本。
基于光固化成型的功能零件无模具快速精铸技术采用光固化成型技术制造零件原型代替蜡模进行精密铸造,因此具有光固化成型与精密铸造的双重特点:
① 不受零件复杂形状的限制;
② 易实现零件的整体制造;
③ 可制造任意合金的零件;
④ 不需模具和工装可大大降低单件制造周期和成本;
⑤ 成型由CAD数据控制修正方便
鉴于光固化成型的功能零件无模具制造方法在技术上几乎没有限制。但是由于其制造方法包括 CAD 到精密铸造一系列过程对于零件的批量生产就成本和效率来看这种方法并不宜。对于制造简单形状的零件也不如传统机加工优越,综上所述,基于光固化成型的功能零件不需要棋具,快速精铸技术特别适用于复杂形状零件的单件小批量生产和新产品的开发试制过程。
快速精密铸造是快速成型技术与精确成型技术相结合的产物,充分体现了快速敏捷制造的优势。一个零件的制造从CAD 到原型再到金属零件其急时间约为7~10d 而且成本降低。另外,快速精密铸造的模型是建立在计算机的三维造型基础上修改非常方便,完全省略了制造木模或金属模的过程实现铸件的无懊制造。因此,与传统的精确铸造(如烙模铸造、低压铸造等)相比快速精密铸造在模具制造业和新产品开发领域的优势是很明显的,尤其适用于两壁复杂零件的快速开发。
声明:本网站所收集的部分公开资料来源于互联网,转载的目的在于传递更多信息及用于网络分享,并不代表本站赞同其观点和对其真实性负责,也不构成任何其他建议。本站部分作品是由网友自主投稿和发布、编辑整理上传,对此类作品本站仅提供交流平台,不为其版权负责。如果您发现网站上所用视频、图片、文字如涉及作品版权问题,请第一时间告知,我们将根据您提供的证明材料确认版权并按国家标准支付稿酬或立即删除内容,以保证您的权益!联系电话:010-58612588 或 Email:editor@mmsonline.com.cn。
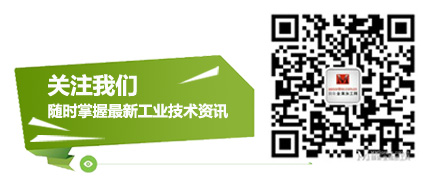
- 暂无反馈