应用制造技术制造模具的几种方法(2)
( l )用化学粘接陶瓷浇注陶瓷型腔。用快速成型技术制作塑料原型,然后浇注硅橡胶、环氧树脂、聚氨醋等材料,制成软模。移去原型,在软模中浇注化学粘接陶瓷( CBC ,陶瓷基复合材料)形成型腔,之后在 205 ℃ 以下固化 CBC 型腔并抛光型腔表面,加人浇注系统和冷却系统后便制得小批量生产用注塑模。
( 2 )用陶瓷或石膏型浇注钢型腔。利用快速成型系统制作母模的原型,浇注硅橡胶、环氧树脂、聚氨醋等材料,制成软模。然后移去母模,在软模中浇注陶瓷或石膏,结合铸造技术制成钢型腔。最后对型腔表面抛光后加人浇注系统和冷却系统等便得到批量生产用注塑模。 ( 3 )用覆膜陶瓷粉直接制造钢型腔。 SLS 技术以覆膜陶瓷粉为原料,通过激光烧结成型,可以将壳型的三维 CAD 模型直接制出陶瓷壳型,再配以冒口浇注系统进行精密铸造,制成钢型腔。这种方法最为直接,但每次只能制造一个型腔,生产率较低。另外一种方法是用 SLA 、 LOM 、 FDM 或 SLS 等快速成型工艺制造出母体的树脂或木质原型,并在原型表面直接涂挂陶瓷浆料制出陶瓷壳型,焙烧后用工具钢作为浇注材质进行铸造,即可得到模具的型芯和型腔。该方法制作周期不超过 4 周,制造的模具可生产 25000 个塑料产品。
3 .用化学粘接钢粉浇注型腔
用快速成型系统制作纸质或树脂的母模原型,然后浇注硅橡胶、环氧树脂、聚氨酷等软材料,构成软模。移去母模,在软模中浇注化学粘接钢粉的型腔,之后在炉中烧去型腔用材料中的粘结剂并烧结钢粉,随后在型腔内渗铜,抛光型腔表面,加入浇注系统和冷却系统等就可批量生产注塑模。
4 .砂型铸造法
使用专用覆膜砂,利用 SLS 成型技术可以直接制造砂型(芯),通过浇注可得到形状复杂的金属模具。美国 DTM 公司新近开发的材料 SolildForm Zr 是一种覆有树脂粘结剂的错砂,用该种材料制成的原型在 100 ℃ 的烘箱中保温 2h 进行硬化后,可以直接用作铸造砂型。
5 .电火花加工法
用电火花( EDM )技术加工模具正成为一种常规的方法,但是电火花电极的加工往往又成为“瓶颈”过程。电火花加工法是利用 RPM 原型制作 EDM 电极,然后利用电火花加工制作钢模,其制作过程一般为: RPM 原型~三维砂轮一石墨电极~钢模。
Keltool 方法是用来直接从母模制造模具的方法,该项技术原由美国 3M 公司开发,后转让美国 Keltool 公司。到目前为止, Keltool 方法主要用来制造长寿命(数百万次)的注塑模和电火花加工( EDM )用的电极。制得的 Cu-EDM 电极的耐磨性要比石墨电极高 4 一 10 倍,但加工速度却下降近 1 倍。
Keltool方法与常规的机加工方法相比有三大优点:
l )速度快,从母模到制成一套模具一般在 3 周内完成。由于快速自动成型能在数小时或几天内完成母模制作,与传统方法相比,整个模具制造过程可节省数月时间;
2 )多套模具和一套模具一样容易制造,且重复性好;
3 )可以制造形状复杂、具有精细结构的模具。
这种方法的缺点是可制造的模具尺寸受限制,一般在 100mmx100mmx100mm ,但精度随着尺寸增大而下降,在未引人快速成型机前母模制作是这种技术的瓶颈过程。
Keltool 方法主要用金属基复合材料,一般由另外一种金属和铜粉组成。详细的技术细节属于Keltool公司的保密内容。但一般来说,制造过程包括首先用零件或模具的母模做一个负型,将金属复合粉填入这个负型中,然后在高温下烧结,再渗人熔化的铜填补空隙,这样就制得坚硬的高密度模具,一般还需经机加工后才能投入使用。
在烧结过程中,零件有些收缩,但这种收缩是线性的,并且可以预测。比如 Cu-w 材料收缩在10mm / m ( 10mils / in ) ,这种收缩通常可以在做母模时进行修正,快速成型技术很容易实现这一点,只需在 CAD 设计时将尺寸考虑进去,快速成型的母模的尺寸就会达到 Keltool 的要求。因此, Keltool 方法与快速成型技术结合后,消除了其母模制作的瓶颈过程,威力大增。
6 . NCC 制模法
NCC 方法首先在 SLA 方法生成的快速成型上镀上一层厚约1~5mm 的镍,然后在镍质镀层上用化学反应凝固陶瓷材料( CBC , Chemically Bond-ed Ceramic ) ,原型分离后得到最终模具。这一方法适于制作较大的工件,具有与 SL A 工艺同等的精度,制造的注塑模可以生产上万件产品。这一方法要解决电镀工序时间长和需处理废液污染的问题。目前cemcom公司和 PitneyBowes 公司、伊士曼柯达公司、福特汽车公司合作,正在继续完善该项技术,主要解决尺寸精度、易操作性和加工速度等问题。
7 . RSP 制模法
美国爱达荷国家工程与环境试验中心采用快速凝固工艺(即 RSP )技术实现了注塑模具的快速经济制造。该方法采用快速成型技术制作的样件作为母体样板,通过喷涂到母体样板的金属或合金熔滴的沉积制造模具。其工艺过程为:熔融的工具钢或其他合金被压人喷嘴,与高速流动的隋性气体相遇而形成直径约0.05mm的雾状熔滴,喷向并沉积到母体样板上,复制出母样的表面结构形状,借助脱模剂使沉积形成的钢制模具与母样分离,即可制出所需模具。
此方法可制作注塑模具和冲压模具。但是为提高制件的表面质量和力学性能需要进行时效处理,增加了制模时间。
直接模具与间接制模的比较
直接快速模具制造指的是利用不同类型的决速成型技术直接制造出模具本身,然后进行一些必要的后处理和机加工以获得模具所要求的力学性能、尺寸精度和表面粗糙度。目前能够直接制造金属模具的 RP 工艺包括激光选区烧结 ( SLS)、三维打印( 3 DP )、形状沉积制造( S DM )和三维焊接( 3 D-Welding )等尽管直接决速模具制造具有其独特的优点,制造环节简单,能够较充分地发挥 RP 技术的优势,特别是与计算机技术密切结合,决速完成模具制造,对于那些需要复杂形状的内流道冷却的模具与零件,采用直接 RT 有着其他方法不能替代的独特优势。但是它在模具精度和性能控制方面比较困难,特殊的后处理设备与工艺使成本提高较大,模具的尺寸也受到较大的限制。与之相比,间接决速模具制造,通过决速成型技术与传统的模具翻制技术相结合制造模具,由于这些成熟的翻制技术的多样性,可以根据不同的应用要求,选择不同复杂程度和成本的工艺,一方面可以较好地控制模具的精度、表面质量、力学胜能与使用寿命,另一方面也可以满足经济胜的要求。因此,目前工业界多数使用间接决速模具制造技术。这类技术包括喷涂模具、中低熔点合金模具、表面沉积模具、电铸模、铝颗粒增强环氧树脂模具、硅胶模以及快速精密铸造模具等。
3)快速模具技术的发展趋势
堆积金属(钢铁材料、非铁金属及其合金等)的难度决定了直接 RT 技术在未来的五六年内无法在 RT 领域中占据统治地位。这一期间内,主要还是间接 RT 技术占统治地位。但是,随着大功率激光烧结、激光同轴送粉、三维焊接、均匀微滴喷射( UPS )以及其他激光净成型技术的完善,估计 10 年内直接 RT 技术将逐渐成为 RT 技术的主流,直接 RT被许多专业人士看好还有如下 3 个原因:
l )模具公司都希望取消制造模具原型( Pattern)以及原型后处理的过程,以提高快速性;
2 )通过原型转换将损失精度,使精度的补偿控制复杂化;
3 )间接 RT 生产的模具寿命往往较低,这也是它在竞争中处于不利地位的一个原因直接 RT 与间接 RT 的竞争是 RT 技术发展的内部驱动力,在这种驱动力推动下,将会涌现出更多的 RT 技术与装备。目前约有 20 多种 RT 技术,其中多数为间接 RT ,已经成功地商业化的约占一半。在全球化市场经济和各种高新技术的迅猛发展形势下,快速经济模具被赋予了新的使命和全新的内涵,向着多品种系列化迈进,不断有新的工艺创新和突破,与之配套的设备相继问世服务领域在不断地拓宽,创造的经济效益越来越显著。今后快速模具制造技术的发展趋势是:
l )基于快速成型原理的直接制模法在表面及尺寸精度、力学性能等方面尚难以满足高精度、耐久模具制造的要求,且成本高、尺寸规格受限制。采用低成本且适于精细加工及多种材料成型的成型能量,利用熔他效应将是提高直接制模法的实用性、材料适应胜和表面精度的可能途径;
2 )以决速成型和铸造、熔射等技术相结合的间接制模法与直接法相比实用化方面占有优势,但因工序增加和受材料性质和制造环境的影响导致控制精度难度大。开发尺寸稳定性好的制模材料,实现制模过程的短流程化和工作环境的安定化是提高模具精度的有效方法。
声明:本网站所收集的部分公开资料来源于互联网,转载的目的在于传递更多信息及用于网络分享,并不代表本站赞同其观点和对其真实性负责,也不构成任何其他建议。本站部分作品是由网友自主投稿和发布、编辑整理上传,对此类作品本站仅提供交流平台,不为其版权负责。如果您发现网站上所用视频、图片、文字如涉及作品版权问题,请第一时间告知,我们将根据您提供的证明材料确认版权并按国家标准支付稿酬或立即删除内容,以保证您的权益!联系电话:010-58612588 或 Email:editor@mmsonline.com.cn。
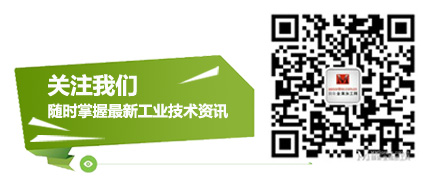
- 暂无反馈