机械与模具
目前,中国正在迅速成为世界工厂。不过,当前“中国世界工厂”乃是中国迅速成为跨国公司“世界性生产基地”的同意语,中国离真正世界工厂还道路漫长。要建立真正意义上的世界工厂,必须以划时代的新技术革命为基础,把自身工业化和引进工业化结合起来,实现自身工业化和引进工业化的同时发展,这既是中国世界工厂的捷径,也是中国世界工厂的新发展道路。
当今企业的竞争集中表现在产品款式、新产品开发周期及产品生产规模方面。模具作为新产品生产的关键工装,其设计与生产日益成为新产品开发周期的决定因素。在汽车工业中,过去新车型的开发周期一般为十年,现在缩短为二到三年,福特及丰田新车型的开发周期仅为一年半,尤其是手机等电子行业, 开发周期有的仅为3个月。这就要倚赖企业提高模具设计与制造水平的能力。
精密模具高速加工技术随着数控加工设备与高性能加工刀具技术的发展而日益成熟,极大地提高了模具加工速度,减少了加工工序,缩短甚至消除了耗时的人工打模磨甚至抛光的工序,,从而大大地缩短了模具的生产周期。模具的高速加工技术逐渐成为提高模具品质的最主要的手段之一 。
高速加工技术在我国刚刚起步,众多企业非常关注高速加工的发展及在模具行业的应用,以及高速加工的工艺特点,高速加工对设备、刀具的特殊要求以及高速加工对CAD/CAM系统的特殊要求。故将MAZAK精密模具高速加工技术研讨会暨现场加工展示会的资料整理成文,希望与我国从事模具高速加工的工程技术人员交流。
关于高速加工的定义
高速加工是缘起自航空铝合金材料零件的加工,高水平合金涂层刀具的寿命不是主要的限制因素。高速加工主要受设备主轴速度及材料熔点的限制,一般主轴速度为50000~60000r/min或更高。本文主要关注塑料模具、压铸模具、冲压模具及锻模等用的合金模具钢的高速加工,这种材料的硬度一般超过洛氏50度,故高速加工的限制因素主要是刀具寿命,而非铝加工中的主轴速度。对于小型模具细节结构的加工,主轴速度可达40000r/min以上,而大型汽车覆盖件模具的加工,一般主轴速度12000r/min以上的加工即可称为高速加工。
高速加工的分类及优势
高速加工按其目的而言应分为两类,即以实现单位时间去除材料量最大为目的的高速加工,和以实现高质量加工表面与细节结构为目的的高速加工。任何模具的高速加工都是这两类技术的综合运用。相对而言,后者因极大地减少了钳工抛光、修复时间,减少甚至消除了部分工序,因而大大缩短了模具的生产周期。与传统加工方式相比,高速加工(HSM)的优势如下:
◎ 高速加工提高了模具加工的速度
对于精加工,从材料去除速度而言,高速加工比一般加工快四倍以上——尽管高速加工采取了非常小的进给速度与切深,对粗加工而言高速加工可理解为45m3/min的切削量。
◎ 高速加工可获得高质量的加工表面
因高速加工采取了极小的进给量与切深,故可获得很高的表面质量,有时甚至可以省去钳工修光的工序,因表面质量的提高又省去了修光及火花机加工等工序所需的时间。
◎ 简化了加工工序
传统铣削加工只能在淬火之前进行,因淬火造成的变形必须要经手工修整或采用电加工最终成形。现在则可以通过高速加工完成,省去了电极材料、电极加工编程及加工,以及电加工过程所需所有费用,而且不会出现电加工所导致的表面硬化。另外,由于高速加工切削量减少,便可使用更小直径的刀具对更小的圆角半径及模具细节进行加工,节省了部分加工或手工修整工艺。减少人工修光时间及工艺的简化对缩短生产周期的贡献甚至可超过高速加工速度提高而产生的价值。
◎ 使模具修复 过程变得更加方便
模具在使用过程中往往需要多次修复,以延长使用寿命,过去主要是靠电加工来完成,如果采用高速加工可以更快地完成该工作,而且可使用原NC程序,无需重新编制,且能做到精确无误。
MAZAK高速模具加工机
MAZAK高速模具加工机于问世以来一直受到市场的好评,在今年更是对外发布了最新型号的u级设备SMM2000U及SMM2500U。
◎ 高速加工对机床的要求
MAZAK高速模具加工机SMM2000U及SMM2500U以下功能都是标准配置:
● 主轴速度应能达到20000~40000r/min;(MAZAK标准配备25000RPM 主轴)高刚性的机械结构;(龙门结构)
● 高稳定、高刚性、冷却良好的高速主轴;
● 精确的热补偿系统;(冷却液温度管理)
● 采用全闭环系统(采用德国制分辨率达0.05U的高分辨率的光栅尺)
● 高速处理能力的控制系统(采用高追踪性能的伺服放大器);
● 纳米补偿功能
● 具有预处理能力的控制系统。
◎ 高速加工对刀具及装夹的要求
● 刀夹、刀具的加速度小于3g;
● 刀具的径向跳动小于0.015mm;
● 刀长一般小于刀具直径的4倍。
高速加工(HSM)对CAM系统的要求
高速加工有着不同于传统加工的特殊的加工工艺要求,而数控加工的数控指令包含了所有的工艺过程,故应用于高速加工的数控自动编程系统——CAM系统必须能够满足相应的特殊要求。
◎ CAM系统应具有很高的计算编程速度
高速加工中采用非常小的进给量与切深,故对NC程序的要求比对传统系统的NC程序要求要严格得多,要求计算速度要快且方便、节约编程时间等。另外,快的编程速度使操作人员能够对多种加工工艺策略进行比较,以便采取最佳的工艺方案,并对刀具轨迹进行编辑、优化,以达到最佳的加工效率。
全程自动防过切处理能力及自动刀柄干涉检查
高速加工以高出传统加工近10倍的切削速度加工,一旦发生过切, 其后果不堪设想,故CAM系统必须具有全程自动防过切处理能力。传统的曲面CAM系统是局部加工的概念,极容易发生过切现象,一般都是靠人工选择干预的办法来防止,很难保证过切防护的安全性,只有通过新一代的、智能化的、面向对象的CAM系统,才能实现防过切处理全部由系统自动完成,才能真正保证其安全性。
高速加工的重要特征之一就是能够使用较小直径的刀具加工模具的细节结构。系统能够自动提示最短夹刀长度并自动进行刀具干涉检查,这对于高速加工非常重要。
进给率优化处理功能
为了能够确保最大的切削效率,并保证在高速切削时加工的安全性,应根据加工瞬时余量的大小,由CAM系统自动对进给率进行优化处理。
符合高速加工要求的丰富的加工策略
与传统方式相比,高速加工对加工工艺走刀方式有着特殊要求,因而要求CAM系统能够满足这些特定的工艺要求:
● 应避免刀具轨迹中走刀方向的突然变化,以避免因局部过切而造成刀具或设备的损坏。
● 应保持刀具轨迹的平稳,避免突然加速或减速。
● 下刀或行间过渡部分最好采用斜式下刀或圆弧下刀,避免垂直下刀直接接近工件材料。
● 行切的端点采用圆弧连接,避免直线连接。
● 除非情况必须如此,否则仍应避免全力宽切削。
● 残余量加工或清根加工是提高加工效率的重要手段,一般应采用多次加工或采用系列刀具从大到小分次加工,直至达到所需尺寸,避免用小刀一次加工完成。
● 刀具轨迹编辑优化功能非常重要,应避免多余空刀,可通过对刀具轨迹的摄像、复制、旋转等操作来避免重复计算。
● 刀具轨迹裁剪修复功能也很重要,可通过精确裁剪减少空刀提高效率;也可用于零件局部变化编程,仅需编辑修改边际,无需对整个模型重新编程。
● 高速加工对编程人员的要求与编程方式的改变
采用高速加工设备之后,对编程人员的需求量将会增加,因高速加工工艺要求严格,过切保护更加重要,故需多花时间对NC指令进行仿真检验。一般而言,高速加工编程时间比普通加工编程时间要长得多,然而却大大缩短了加工时间。为了保证高速加工设备足够的使用率,需配置更多的CAM人员。
传统CAD/CAM中,NC指令的编制是由远离加工现场的CAD/CAM工程师来完成的,因编程与加工地点分离,往往因编程人员对现场条件及加工工艺不够清楚而需要对NC指令进行反复检验与修改,影响正常使用。随着CAM系统智能化水平的提高,已经出现了新一代独立运行的智能化的CAM专业系统,其主要特点是面向对象的实体加工方式,而非传统的曲面局部加工方式。只需输入并选择加工工艺,即可自动完成编程操作。编程的复杂程度与零件的复杂程度无关,只与加工工艺有关,因而非常易于掌握,只需短时间培训即可掌握使用。在欧美发达国家,为了充分发挥NC设备操作人员的优势,缩短加工时间间隔,机侧对话式编程已经成为逐渐流行的发展趋势。
声明:本网站所收集的部分公开资料来源于互联网,转载的目的在于传递更多信息及用于网络分享,并不代表本站赞同其观点和对其真实性负责,也不构成任何其他建议。本站部分作品是由网友自主投稿和发布、编辑整理上传,对此类作品本站仅提供交流平台,不为其版权负责。如果您发现网站上所用视频、图片、文字如涉及作品版权问题,请第一时间告知,我们将根据您提供的证明材料确认版权并按国家标准支付稿酬或立即删除内容,以保证您的权益!联系电话:010-58612588 或 Email:editor@mmsonline.com.cn。
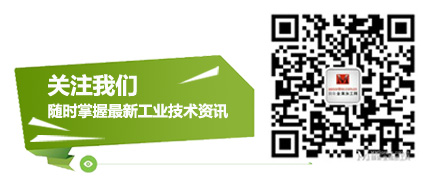
- 暂无反馈