WorkNC在模具自动化加工编程中的应用
在欧美、日本等发达国家,模具产业从20世纪80年代就开始发展无职守自动化数控加工技术,到目前已有20余年的历史,技术较成熟。一些日本的模具企业自动化数控加工比例已能达到50%以上。 在我国,由于模具产业起步晚,人工费用低,在自动化数控加工方面起步也晚。如今,汽车工业的快速发展带动了中国模具产业的进步,国内的一些模具企业也开始追求并尝试“无人职守”自动化数控加工技术,以求达到少人化操作,节省大量人工成本、降低劳动强度,同时通过追求可无人职守的自动化加工,提升NC程序质量和数控加工水平,让模具加工更可靠、高效、实物质量更高。 1 覆盖件模具NC自动化加工对程序的要求 1.1 模具数控加工工艺流程 数控编程首先要根据零件的几何形状、表面粗糙度、加工精度、同时考虑零件的刚性、变形以及机床、刀具、夹具等因素,选择合理的工艺流程,如图1所示。 图1 工艺流程 1.2 自动化加工对NC程序的要求 自动化加工对程序的安全性、可靠性、工艺性和准确性提出了更高的要求。 1) 首先要保证程序本身的准确性,做到加工到位,并做好模拟仿真,避免错误的发生。 2) 保证程序的安全性、可靠性,规划合理的加工顺序,保持加工余量均匀。结合机床刀库数据做好碰撞检测,避免碰撞扎刀等现象的发生。 3) 工艺性要考虑加工效率、刀具磨损和机床震动等因素。选用刀具情况及程序提供的F(r/min)、S(mm/min)等设置参数必须与加工机床相匹配。 要设计出满足上述要求的NC程序,除了编程人员具有高超的技能和丰富的经验外,加工方案的实现和程序质量的保证还需要先进的CAM软件平台。 如:为了实现无人职守自动化加工,传统的开粗工艺多采用大刀径球头刀沿面开粗,此种工艺加工效率高,但由于吃刀量大、毛坯变形和加工余量不均匀等因素很难做到机床负荷持续稳定。另外,机床满负荷运转,不确定性高,难以保证加工质量和高效率的要求,不适合无人职守加工。一些专业的编程软件提供的编程方法,能满足“小吃刀、轻切削”的高速加工,极大程度上保证程序安全性,减小提刀浪费,保证无人职守技术对机床、刀具、负荷等方面的要求。 2 自动化加工的NC程序设计 2.1 WorkNC软件 WorkNC软件是法国Sescoi公司面向加工制造业的全自动化计算机辅助制造(CAM)软件。有多种数据转换接口,有专门针对CAM的CAD模块,能完成零件分析、曲面填补、边界线的建立和简单曲面的建立等功能,非常实用。WorkNC能产生良好的走刀路线,同时它还具备完善的模板调用功能,强大的刀具路径编辑功能,残余毛坯计算,防过切功能等,都为编程人员提供了方便。 2.2 加工工艺实现(利用WorkNC软件实现) 图2为某车型前车门内板的拉延凸模。此零件型腔深、结构复杂,为了尽量降低钳工手工修研的工作量,要求加工精度高,属于较难加工的零件。该拉深凸模采用的材料是HT300。 下面以此拉深凸模为例,介绍WorkNC软件在无职守自动化数控加工中的应用。 图2 某前车门内板拉深凸模 WorkNC编程的流程是,加载工件、毛坯及边界曲线,察看工件读入的正确性,调用加工模板,给必要的路径选择合适的边界线及驱动线并运算,生成刀轨。 2.2.1 粗加工方案 WorkNC毛坯的建立有铸件毛坯、矩形毛坯、复合型毛坯和CAD模型等方式,复合型毛坯适用于铸铁或者铸钢件中间镶锻件工具钢的情况。 此工件是铸件,采用铸件毛坯,生成等高层切的刀具路径,如图3所示。WorkNC的层切开粗和二次开粗功能非常强大,几乎能将干涉碰撞的可能降为零。只有这样,才能在开粗的过程中实现无职守加工。 图3 一次开粗和二次开粗刀具路径 程序每层切削1 mm,刀具路径是由高到低,这样既保证了程序的安全性,又能最大程度上避免毛坯余量不均匀造成机床负荷的变化。同时因切削力小,也有效保护了机床。体现在自动化上的优势,操作者不再需要随着机床负荷的变化而随时调整进给速度。 2.2.2 中加工及精加工方案 中加工与精加工一般采用相近的走刀方式。WorkNC有多种精加工工艺方案,如:3D沿面精加工、等高精加工和最佳化等高精加工、投影精加工和最佳化投影精加工等,可以根据实际工件的需要灵活运用。该件型腔复杂,平坦处与立壁处刀具的切削状态是不一致的。平坦处刀具的切削点在球头刀的刀尖点附近,而立壁处则是用球头刀的侧刃处切削,同样的转速侧刃比刀尖点附近线速度要高很多。因此这个件的中加工与精加工都采用平坦区与侧壁处分开的程序。平坦区域采用WorkNC的投影精加工,从R弧切线处提取边界,采用平行于座标轴X轴方向加工,采用转速4 500 r/min,进给4 000 mm/min。而立壁区域使用从R弧处提取的驱动线,使用3D沿面精加工,采用转速3 500 r/min,进给4 000 mm/min,刀具路径由高到低,一层一层加工下来(见图4)。 图4 中加工和精加工的刀具路径 2.2.3 清根方案 由于自动化数控加工的实施,清根方案采用留余量单刀清根配合多刀清根使用。 由于小刀相对较短,起伏大的型面,经常有刀具加工不到的地方,这就需要把较深部位的刀路轨迹单独划分出来。在WorkNC软件中,引入了刀具碰撞检测功能,其功能设置界面如图5所示。具体流程如下: 第一步:计算最短安全刀长。选中需要计算最短安全刀长的刀具路径,并点选刀具碰撞检测按钮,在执行模式中选择“只计算推荐的安全刀长”,并在参数设定中输入有效刀长、刀把和曲面预留等参数。通过计算,如果有效刀长大于推荐的安全刀长则用此刀长数据,否则,进行第二步。 第二步:依照有效刀长来分割程序。选择“分别存储碰撞与没有碰撞部分”,计算生成各自的刀路轨迹,如图6所示。没有碰撞部分可实施自动化加工,有碰撞部分需要更换长刀或机床调头加工。 图5 碰撞检测功能界面 图6 无碰撞与有碰撞部分的刀具路径 2.2.4 轮廓加工方案 用WorkNC生成的轮廓程序可实现三维层切,并且可根据设定的参数,控制不同刀具每一层的切削量,从而在保证安全的前提下实现自动化加工。WorkNC所做的轮廓层切程序刀具路径如图7所示。 图7 轮廓刀具路径 2.3 加工过程仿真 仿真模拟功能可观察切削加工的全过程,检测设置的工艺参数是否合理,零件在数控加工过程中是否干涉,加工是否过切等,是程序编制过程中一个至关重要的环节。 WorkNC内部提供的仿真模块比较完善,分为渐进式模拟和3D模拟。渐进式模拟使用起来不需要制作毛坯,只需将包含机床及刀具参数的程序打开,执行刀轨路径模拟即可。3D模拟需要建立方形毛坯,仿真速度慢些,但仿真结果更加直观。3D模拟时将比例设成1:1,如有加工不到位或加工表面质量问题,基本上都能提前预知。 3 结论 采用WorkNC软件编程一定程度上优化了数控加工工艺,提高了加工效率,保证了加工安全性并使加工精度大大提升,尤其是残料毛坯的计算及防碰撞功能上,都为自动加工的实现提供了保障。随着CAM技术和数控加工水平的提高,人工成本的不断增加,追求少人化的自动化加工技术及排产方式将逐渐成为模具行业的发展趋势。 参考文献: [1]范钦武。模具数控加工技术及应用[M]。北京:化学工业出版社,2004。 [2]蒋建强。模具数控加工技术[M]。北京:电子工业出版社,2005。 [3]王丽洁。数控加工工艺与装备[M]。北京:清华大学出版社,2006。 (李冬兰(1978-),女,工程师) |
声明:本网站所收集的部分公开资料来源于互联网,转载的目的在于传递更多信息及用于网络分享,并不代表本站赞同其观点和对其真实性负责,也不构成任何其他建议。本站部分作品是由网友自主投稿和发布、编辑整理上传,对此类作品本站仅提供交流平台,不为其版权负责。如果您发现网站上所用视频、图片、文字如涉及作品版权问题,请第一时间告知,我们将根据您提供的证明材料确认版权并按国家标准支付稿酬或立即删除内容,以保证您的权益!联系电话:010-58612588 或 Email:editor@mmsonline.com.cn。
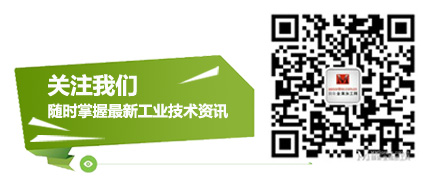
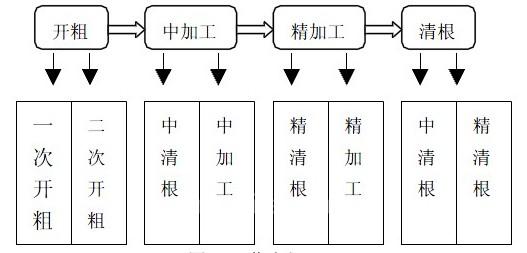


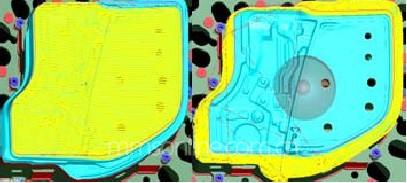

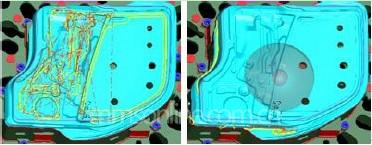

- 暂无反馈