CAE技术是汽车模具设计的最好手段
目前,汽车模具企业大量采用线切割、激光切割、CAD/CAE/CAM/CAPP等多种数字化技术手段,已完全从依靠主模型为加工依据的传统加工方式,转变为以数字化模型为加工依据的现代汽车模具加工方式,大大提高了模具的加工精度和效率。但同数控加工设备所能达到的最高精度水平相比,模具的加工精度并不理想,设备的水平没有得到真正的发挥。
这有两方面的原因:一是设计技术的原因。目前,对于冲压产品的开裂、起皱等问题,利用人的经验和CAE板料模拟分析,通过多次模拟并对模拟结果进行解析、修正、完善,可以在计算机上实现模具调试。但对于修边后的变形、翻边后的回弹以及纵梁的扭曲、翘曲等缺陷,目前还无法实现计算机数字化模拟调试。要解决这类问题,需要CAE软件的进一步发展以及有经验的冲压工艺人员做深入的研究。另一方面是制造技术的原因。数控机床每年校准两次,加工精度和加工基准一致性是没有问题的。但依据同一数字化模型进行加工,加工后的上模定心冲头与下模凹模存在间隙偏差,上、下模合模以及刃口间隙也有偏差;另外,斜面冲孔,凹模镶入式沉孔由五轴数控铣加工出来,检验夹具也采用同样的加工依据加工,但冲压后的零件孔位有时上检具检查就是有偏差。采用统一的加工依据,设备的精度也没有问题,加工工艺流程又多次规范,但问题仍不断出现。所以说,在对加工参数的优化、各工序基准传递的把握以及每次上工件的找正方面,存在很大的提升空间。如何让数字化加工后的模具,经得起数字化检查?如何让数字化加工设备发挥出最高效能?这些是今后汽车模具制造技术研究的重要课题。 首先提高冲压工艺分析能力,通过3D DL图设计的三维冲压工艺模型可直接用于有限元分析(CAE)和编程,为模具结构的三维实体设计提供了工作型面曲面造型依据,为检查用的C/P点、S面等提供了坐标尺寸,由此实现了CAD/CAM/CAE一体化。值得一提的是,我们利用有限元分析技术在设计阶段预测和解决模具调试阶段可能出现的诸如起皱、拉裂、回弹、暗坑、冲击线、滚线等缺陷,使模具调试成功率显著提高。
其次,采用模具结构三维实体设计,进行FMC模型的整体加工,极大地缩短了铸件准备周期。为了进一步做好FMC模型的整体加工,我们订购了一台高速模型数控铣床。 第三,实现模具型面粗、精加工的高速化,缩短了加工周期。 第四,由于采用了精细加工工艺,显著地提高了一次调试合格率,极大地缩短了调试周期。 目前,在CAE分析方面,还存在回弹不好解决的问题。此外,CAE技术除了被用于成形模拟以外,在其它方面的应用较少。 汽车模具制造的最大风险来自于:制件工艺的变更和冲压工艺的失效。
CAE技术是目前解决这些问题的最好的技术手段。CAE技术可以实现快速工艺设计。同时,还可以数学模拟代替模具试模工作,最大程度地降低风险。例如:利用CAE软件作制件的冲压工艺快速设计,一般不超过2~3天。通过CAE分析的设计方案,可以保证冲压试模工作的成功率在85%~90%以上。
针对缩短汽车模具交货周期而采用的快速设计CAD技术,是另一项关键技术。现在大部分模具企业都已应用了CAD技术,但一般都只是应用通用软件进行设计。快速设计技术是在现有CAD 技术基础上发展起来的一项新技术。例如:专用模具设计软件、模板化设计、自动、半自动设计软件等。不管是哪种快速设计软件,都可以大大缩短设计周期,把以周为单位的设计周期变成以天和小时计算。 对汽车模具制造来说,一般要经过设计、制造、调试三个主要阶段。其中占用时间最长的是设计和调试两个环节。采用CAD快速设计技术,可以缩短设计周期40%~60%;通过CAE技术可以缩短调试周期30%~50%。更重要的是,对汽车模具设计和制造的把握性的提高,其意义则超过了缩短周期本身。
现代化的生产管理方式很重要 对于汽车模具制造这种单件订单式生产方式而言,能提高生产效率的有效管理方法主要包括以下三个方面:一是企业的信息化建设;二是模具设计、制造过程中的并行工程;三是模具制造过程中的“一个流”生产。
在企业的信息化建设方面,近几年,企业的CAD/CAM技术有了很大的提高。但在汽车模具制造这种单件订单式生产方式中,模具技术开发中的数据管理问题、设计过程中的标准化建立和重复应用问题、加工工艺的优化和重复应用问题、生产制造过程中信息传递问题、生产计划均衡性问题等,都制约了企业生产效率的提高。为了解决这些问题,2002年我们实施了PDM/CAPP/ERP工程。通过实施CAD/CAM/PDM/CAPP/ERP,依靠并行工程的思想,将全厂的信息资源集成起来,建立了一套信息化的管理系统。相信随着试运行的完善,这套管理系统对生产效率的提高将具有极大的促进作用。 在并行工程方面,虽然目前很多企业对其有了一定认识,但对各环节的把握程度、计划制定的科学性、合理性、均衡性、以及实际运行中的现场监测等,不能根据不同的情况进行调整,管理工作不到位,使并行工程的实施效果不好。
模具制造过程中的“一个流”生产是模具行业发展的一个趋势。它需要对生产加工工艺进行优化,形成标准化作业,根据优化的加工工艺进行加工设备资源的规划,使之匹配,充分利用企业信息化系统的生产信息,按优化的加工生产工艺流,合理进行人力资源分工。最终,减少各环节工人的等待时间,实现“一个流”生产的作业方式,提高模具的生产效率。“一个流”生产,说起来简单,做起来不易,它需要打破以往传统的生产组织方式。
快速经济模具的应用
快速经济模具的类型很多。就型面材料来分类,曾经出现过低熔点合金型面、中熔点合金型面、树脂型面模具。我们公司在20世纪90年代末,曾将树脂型面冲压模具技术应用于红旗“世纪星”轿车的试制,开发了左右前后翼子板、发动机罩内外板、行李箱盖内外板等10个主要外覆盖件的模具,并用其生产出冲压件,组装了6辆高质量的样车以及1辆简易匹配螺钉车。其中的3辆接受了海南40000Km的可靠性试验,1辆接受了MTS实验,不仅验证了整车设计的合理性,也验证并改善了覆盖件产品的工艺性,完善了冲压工艺,为汽车定型和大批量生产提供了可靠的依据。此后,我们还利用树脂型面模具技术制造了大客车蒙皮件模具。通过应用树脂型面模具技术,大大缩短了模具制造周期,而且成本低、精度高,不仅可用于汽车的试制阶段,还可用于汽车的小批量生产上。
值得我们关注的是,90年代开始出现的RP技术,最初是用来制造原型的,现在已发展到通过金属粉末直接烧结或熔射沉积直接制造模具的研究阶段。我们很有必要跟踪这类技术的发展情况。如果这类技术走向实用化阶段,那么,很多用于小批量生产的冷冲模具的制造就可不必再采用传统的制造工艺了。迅速发展的RP技术将对传统的模具制造技术产生深远的影响。或许,受RP技术理念的影响,大批量生产的传统模具的结构及其制造工艺将发生重大变化。 过去,国外汽车模具公司在新车型的开发过程中,普遍将快速模具制造技术用于样车制造和小批量生产中,并对新车制件的工艺性进行验证,以缩短开发周期并降低模具制造风险。
现在,这种方式基本上已被淘汰。其主要原因是:
● 汽车产品的生命周期在大大缩短,基本取消了小批量生产这一生产模式;
● 随着人的经验积累和CAE技术的发展,新产品模具制造的风险已经大大降低,再采用快速模具做工艺验证显得多此一举;
● CAD技术的应用以及车身设计和模具制造中大量采用并行工程,使汽车模具的制造周期大大缩短,所谓的快速模具技术并不比正常模具快多少;
● 目前快速模具制造成本太高。作为一次性使用的模具,从经济上考虑是不合算的。
快速模具一般只用来做拉延成型模。对于拉延成型模而言,即使是制造正式的模具,其生产周期也很短,唯一制约生产周期的是铸件的交货周期;快速模具通常采用塑料或低熔点合金做基体,大部分还需要数控加工,其成本和正式模具相差不多。
快速模具现在已不是解决车身开发周期的好办法。当然,如果有现成的技术不妨也可以用,但发展这项技术是受累不讨好。 总之,只有通过提高CAE/CAD/CAM技术、采用适合于单件生产方式的管理技术,才能大大缩短汽车模具的开发、制造周期。由于模具生产本身就是车身开发的一部分,所以开发周期的合理性非常重要。将车身开发拖期的原因都归结为汽车模具设计、制造能力的不足,这是不客观的,也无助于问题的解决。
声明:本网站所收集的部分公开资料来源于互联网,转载的目的在于传递更多信息及用于网络分享,并不代表本站赞同其观点和对其真实性负责,也不构成任何其他建议。本站部分作品是由网友自主投稿和发布、编辑整理上传,对此类作品本站仅提供交流平台,不为其版权负责。如果您发现网站上所用视频、图片、文字如涉及作品版权问题,请第一时间告知,我们将根据您提供的证明材料确认版权并按国家标准支付稿酬或立即删除内容,以保证您的权益!联系电话:010-58612588 或 Email:editor@mmsonline.com.cn。
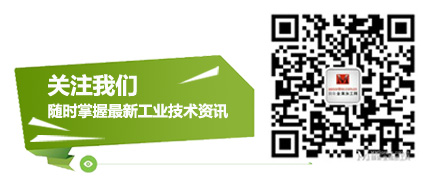
- 暂无反馈