数控编程工作与算法
科学技术的发展,使我国制造业的自动化程度越来越高,数控机床的使用也越来越普追。但是国内数控机床加工程序的编制大多采用手工编制,其效率低下,编程工作盆大且容易出错。
同时自动编程系统的研究开发在国内外己有类似技术,例如旧、出触祀等软件均可以根据三维实体数据直接生成数控加工代码,但这些软件不易掌握,较难使用,对硬件要求很高同时这些软件的价格昂贵,国内一般中小企业难以承受。
下面对如何利用这些信息来生成数控加工所孺要的数控加工程序进行探讨。基于我兄的文件中样条曲线的数控加工自动编程的讨论如下甲文件格式分析万文件的最小组成单元是组,每个组具有组代码叩伪由组值阅,组代码和组值合起来表示一个数据的含义和它的值若干个组构成一个节。
一个完整的文件由个节和个文件结束组成,其顺序为标题似曰山日幻节类节表仍妞比节块仍节实体甲节对象刀节文件结束俘在每个实体节中记录了实体图形的名称、所在图层的名称、线型名、颜色号、基面高度、厚度以及有关的几何数据。
实体节中也描述了块引用但不包括块的实体。荟干的文件中样条曲线的数控自动编程的实现在的汇中有种类型的样条曲线双圆弧样条曲线、样条曲线、非均匀有理样条曲线。双阅弧样条曲线双回弧样条曲线是拟合列表曲线的方法之一。在比中可以利用多义线伽和多义线编辑口刀命令来绘制出双圆弧样条曲线通过对刃中双圆弧样条曲线的分析发现中过两型值点、几间的双圆弧、玩的公切点位于、且垂直于、孔的连线上,同时也在样条曲线上,这样就能取得良好的通近效果。
如所示。对于双圆弧样条曲线在数控编程的处理,我们可以通过分解命令刀凡将双圆弧样条曲线炸开,得到一段一段的圆弧,然后用编辑多义线命令将其转换为场明的圆弧,通过读取叉下组码获得回弧的起点、终点、凸度值,经过处理直接生成数控代码将直线和圆弧转换成有利于数控编程这是因为为单一实体,便于选择拾取,同时中可以包含各个依次首尾相接的直线段和圆弧段,便于确定加工时的刀具运动方向,加的起点即刀具的起点,加工过程中所需的终点坐标均可由红峪各顶点的数据确定。
样条曲线样条方法具有表示与设计自由型曲线曲面的强大功能,是使用最广泛的形状数学描述的主要方法之一,已成为关于工业产品的几何定义国际标准的方法的基础样条曲线由一分段通近曲线组成,次样条曲线的数学方程可写为一妙,,为控制点,顺序连接成的折线称为样条控制多边形,,称为次规范样条基函数,其中每一个称为规范样条,简称样条,它是由一个称为节点矢量的非递减的参数的序列认而,决定的次分段多项式,也即是次多项式样条。
训比中的样条曲线是一种正算法的准均匀样条曲线,其绘制方法是首先,通过改变系统变量仁汗的值来确定生成的样条曲线的次数再用命令绘出样条曲线控制多边形的折线,最后由编辑多义线命令中的样条扭选项将其转变为样条曲线,如所示。
由于一般的数控机床只提供直线、圆弧插补功能,因此在进行数控编程时须把样条曲线按加工精度要求转化为直线、圆弧段,在中的具体做法是首先设置系统变量并绘制出样条曲线,其取值范围为,刀,正值用直线段拟和样条曲线,负值用圆弧段拟和样条曲线,的值越大,拟合糟度也越高。
要求一般情况下刀呵的值取系统默认值或一时,就足以满足数控加工精度。沉卫命令炸开多义线命令将其转换为的直线和圆弧。最后通过读取组码获得直线和圆弧的信息,经过处理直接生成数控代码。非均匀有理样条曲线伽曲戏非均匀有理样条曲线价旧邓曲均方法是一种既能描述自由型曲线曲面,又能较精确地表示二次曲线弧与二次曲面的数学方法。曲线具有几何仿射和透视变换不变性以及强凸包性等特点。
已成为的工业产品几何定义的标准将作为定义几何形状的唯一数学方法。在中是通过命令绘制曲线,给定一系列型值点和首末端点处的切矢来确定曲线,从作图过程可看出泊是以这些型值点作插值点并与首末端点处的切矢来反算出控制点,再拟合得到三次曲线,然后可用修改曲线,如调整控制点和插值点、改变权因子、增加顶点、升高阶次、改变首末端点切矢方向等,如所示。
曲线的下组码信息“组码后数字表示曲线次数般为三次曲线,对三次曲线首尾两端采用了四重结点,开始个结点矢量值均为零,中间结点之间的间隔值正好是相应两型值点之间的距离,而最后个结点矢量值相同为累计的距离之和。
由此可知曲线节点序列乃采用累加弦长法。对于曲线在数控编程中的处理,可以通过读取文件中的信息得到曲线的控制点数以及曲线次数,控制点的值,利用里森费尔德方法确定节点矢童,再利用德布尔算法的递推公式求得曲线上的点,在满足加工精度要求的前提下,用一段一段的直线通近扭曲线曲线的德布尔算法的递推公式如下“结束语由此可知先在训中绘制三种样条曲线,再利用开发工具,直接读取的文件中的直线、圆弧、曲线的信息,经过处理即可生成数控加工代码,可实现自动编程。
声明:本网站所收集的部分公开资料来源于互联网,转载的目的在于传递更多信息及用于网络分享,并不代表本站赞同其观点和对其真实性负责,也不构成任何其他建议。本站部分作品是由网友自主投稿和发布、编辑整理上传,对此类作品本站仅提供交流平台,不为其版权负责。如果您发现网站上所用视频、图片、文字如涉及作品版权问题,请第一时间告知,我们将根据您提供的证明材料确认版权并按国家标准支付稿酬或立即删除内容,以保证您的权益!联系电话:010-58612588 或 Email:editor@mmsonline.com.cn。
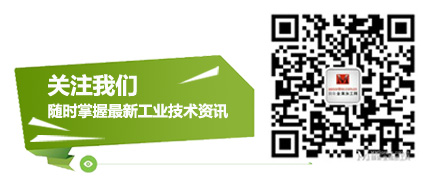
- 暂无反馈