提高冷挤压凸模寿命的方法
1.引言
随着机械工业的迅速发展及对外经济的日益扩大,尤其是中国加入WTO后,深入研究及发展少切屑新工艺的趋势已非常重要。因为冷挤压工艺给套筒类产品带来了很多优点,即提高力学性能、减少机械加工工时,提高材料利用率及生产率、降低产品成本等。但从冷挤压套筒零件的生产情况来看,因冷挤压凸模不仅承受轴向冲击力的作用,同时又不可避免地承受径向力的作用(这里所指径向力是指作用于凸模侧壁各力的总称),由于各种原因引起,如坯料端面的不平行度、坯料在凹模中的位置有偏移、左右导柱与导套之间的间隙不一样造成模架窜动、上模板上平面与下模板下平面之间的平行度超差等。冷挤压凸模的破坏形式及预防措施介绍如下:
凸模是冷挤压模具中最重要的部分。凸模必须能承受很高的抗压负荷,而且又要有足够的冲击韧度,以防因任何一个微小的弯曲而引起侧向压力使凸模突然断裂。同时凸模还要具有良好的耐磨性,以防发热时可能发生的软化,避免可能产生的刮痕和咬伤,并防止可能出现的永久变形。
冷挤压凸模的破坏主要是由于工作应力过大,偏心载荷和应力集中引起短期疲劳而破坏。
从目前的各种零件冷挤压生产情况来看,凸模最主要的破坏形式是:永久变形、折断、断裂、裂纹和破损。
2.凸模永久变形破坏及其预防措施
凸模在挤压过程中,发生镦粗、变形和弯曲等永久变形,称为塑性变形。引起凸模变形的主要原因是:
(1)挤压力过大,超过凸模材料的屈服强度。
(2)凸模的强度和硬度偏低。
(3)毛坯材料的硬度过高。
(4)坯料体积过大,多余材料无法排除。
(5)凸模材料选择不当。
为了防止凸模弯曲和变形,应采用热硬性较好、抗压强度较高的高速工具钢制造凸模,淬火回火后硬度在61HRC以上。提高坯料精度,使坯料两端面平行,并将坯料硬度控制在110HB以上。此外,还应提高模具的导向精度和安装精度,以保证挤压时凸凹模同轴。
3.凸模折断、断裂、裂纹破坏及其预防措施
断裂是直接影响凸模寿命和危害最大的一种破损形式。凸模的断裂常常从一个极微小的切痕或划痕开始,逐渐扩大形成环状裂纹,严重时出现开裂和突然折断。引起裂纹的主要原因是由于反复交变应力作用和周期性温度变化的结果。在挤压过程中,短时间产生大量的热量,使模具温度升高,每挤一次就是一个热冷循环。在这种热冷交替的作用下,模具表面的应力符号也交替变化,因而导致热疲劳裂纹的产生。可见,疲劳是导致凸模开裂的主要原因之一。还有,承受偏心载荷时常常在圆角与直线部分交接位置(即截面或形状变化的部位)发生裂纹、甚至断裂。尤其是这些过渡部位处的圆角很小或相接不圆滑时,开裂更为严重,这是因为这些部位是应力集中区,是产生裂纹的发源地。因此,将这部分设计成带有适当的圆角,仔细加工并进行抛光,使其圆滑相接,避免应力集中,是防止裂纹的有效办法。
凸模的断裂,按其破坏性质和断裂部位的形态,分为横向裂纹、纵向裂纹和径向裂纹3种类型。横向裂纹又有2种情况,折断大多数发生在过渡处,有时也在挤压件的口部作用部位和凸模与固定板连接的部位发生折断。折断主要是由于偏心负荷造成的弯曲应力引起的,受应力集中的影响较小。在反挤压杯形件时,若凸模的圆角R处过分限制反挤,则该处将发生横向裂纹。当反挤压杯形零件的口部偏斜较大,即一面高一面低,在退料时由于侧向力引起的弯曲力矩,常使凸模折断。
另一种拉断,多半是在润滑条件变坏的情况下,发生在截面变化的部位,拉断的主要特征是其断口平整。改善润滑条件,减小摩擦,是防止凸模被拉断的有效措施。
纵向裂纹的几种常见形式,纵裂是发生在工作环带的圆周上。这是疲劳性质的裂纹,是由周期性、热冷的交变应力作用引起的,还与坯料润滑好坏,凸模硬度大小有关。为了减少这种微小的纵向裂纹的发生,首先要选用韧度较好的高速钢材,采用软氮化处理,以增加表面的耐磨性、耐疲劳性。其次,应选用合适粒度的砂轮,严格控制磨削时的进刀量。在磨削后加以抛光。同时改善润滑质量、减小摩擦,提高凸模的表面硬度,保证在61HRC以上。
由工作端面开始沿纵向向上发展的纵向裂纹和中心开裂,多数是由于材料缺陷引起的,如碳化物分布不均匀,材料偏析过大等。因为碳化物分布不均匀会增加钢的脆性,降低钢的强度。生产中,一般将材料的偏析控制在三级以下,对于小直径棒料,这基本上是可以达到的,对于大直径棒料,必须通过严格的锻造工艺,才能消除过大的碳化物偏析。两种纵向裂纹,是由于连接部位的圆角过小或相接不圆滑引起的。因此,将连接部位设计成圆角,仔细加工抛光,使其圆滑过渡且无应力集中,是防止角部开裂的有效措施。
在凸模工作和尾部端面上沿径向所发生的裂纹,在凸模工作圆角处所发生的裂纹,是位于表层的轻微裂纹。这种裂纹常常从一个极微小的磨痕、划痕或金属粘连拉伤开始,由极细的条纹逐渐扩展成微裂纹。因此,降低圆角部位的表面粗糙度和提高其硬度,采用优质润滑剂以防金属粘连,便可避免这种裂纹的发生。凸模工作端面上的网状裂纹,是一种由于挤压时的热效应而引起的热疲劳造成的。有时,当磨加工的磨削量过大,进给太快时,由于表面过热所引起的龟裂,在挤压时也会发展成为网状裂纹,因此,在磨削成形端面时,应选用粗粒度的砂轮,接近成品时,每次磨削量要小,同时应检查回火处理以及软氮化和镀铬等表面处理情况。在凸模尾部端面上,有时类似网状裂纹的端部开裂。这种表面为网状,向纵向发展的开裂现象,是由于端面不平,材质不均匀,或由于凸模垫块不平、中心压塌变形,而使端面接触不良引起的。所以,凸模的尾部端面应平坦,且与工作端面平行,并采取足够厚度和强度的凸模垫块,以增加其刚性,防止变形。
4.凸模磨损破坏及其预防措施
在冷挤压成形过程中,由于坯料沿着模具表面既滑动又流动,因此,模具工作表面必然会发生磨损。根据摩擦表面发生的现象,冷挤压凸模的磨损有磨料磨损、氧化磨损、机械咬合磨损和疲劳磨损4种。
凸模磨损现象的产生是由于本身表面硬度低、润滑不良、变形抗力大所引起。
预防措施应根据其破坏的原因,采用相应的方法,如碳化物偏析小、组织均匀的优质材料、高强度、高硬度钢种或硬质合金,多次回火热处理工艺、优良润滑剂等。
折断
(1)断口倾斜。
(2)断口处有明显撕裂条纹。
(3)断裂发生于过渡部位
(4)突然产生
形 成 原 因
(1)坯料端面不平,挤压时产生的侧向力,使凸模弯曲而折断。
(2)坯料与模腔的间隙大,挤压时不均匀的金属流动,使凸模承受不均衡的偏心载荷而折断。
(3)凸模安装偏心、倾斜,与凹模不同轴。
(4) 凸模过渡处圆角半径过小或相接不圆滑,由于应力集中,使凸模折断。
(5) 凸模过渡处存在刀痕磨痕、划伤和淬火裂纹。
(6) 凸模细长,工作部分的长径比过大。
(7)模具材料选择不当,热处理硬度偏高,回火不足使脆性增大。
(8)设备精度差,刚性低。
预 防 措 施
(1)采取校形工序,提高坯料精度。
(2)将坯料与模腔间隙控制在0.1mm以内。
(3)提高安装精度,采取有效的导向方法。
(4)加大圆角半径,仔细加工并抛光至Ra0.4μm以下。
(5)精加工并抛光,去除加工痕迹和划痕。
(6)尽量缩短凸模长度,尤其是工作部分有效长度与其直径之比,应控制在4以下。
(7)选择强韧性极好的高速钢制作凸模,采取低温淬火充分回火,增加凸模的韧性。
(8)采用精度高、刚性好、大吨位的专用挤压机。
拉断
(1)断口平坦。
(2)断口似灰铁状且具有光泽。
(3)断口位于截面过渡部位。
形 成 原 因
(1)在圆角和直线的相接部位,存在粗糙的刀痕,尖锐的线状划伤,由于反复作用产生疲劳裂纹,并扩展成环状裂纹,最后拉断。
(2) 凸模承受的压力过大。
(3) 凸模材料的抗压强度不足。
(4)润滑不良,摩擦力过大,卸料时将凸模拉断。
预 防 措 施
(1)仔细加工,去除刀痕、切痕和划伤。
(2)选择优质材料,提高凸模的抗压强度和承载能力。
(3)选用优良润滑剂,以降低摩擦。
纵向裂纹
(1)在工作环带的圆柱表面上。
(2)处于表层。
(3)轻微、细小。
形 成 原 因
(1)凸模工作带表面不光洁、粗糙且有划痕。
(2)凸模表面硬度不够。
(3)凸模过热,表面发生软化。
(4)润滑不良表面摩擦大,金属粘连凸模并拉伤其表面。
预 防 措 施
(1)磨加工时,采用合适粒度的砂轮,并控制进给量,以防止加工过热产生的微裂纹。
(2)精加工并抛光至Ra0.4μm以下。
(3)选用热硬性较好的高速钢制作凸模,保证淬火后硬度在61HRC以上。
(4)选用优良润滑剂。
纵向开裂
(1)沿轴方向。
(2)或处于中心部位。
(3)明显开裂。
形 成 原 因
(1)材料严重偏析。
(2)碳化物分布不均。
(3)残余奥氏体过多。
预 防 措 施
(1)采用组织均匀的优质材料。
(2)采用锻造加工,将碳化物偏析控制在三级以下。
(3)采用冰冷处理,使残余奥氏体稳定。
径向裂纹
微裂纹
(1)工作端面。
(2)圆角半径处。
形 成 原 因
(1)热疲劳引起模具表面软化。
(2)磨削留量大,进给速度快,由于表面过热引起的微裂纹。
(3)热处理时,表面脱碳。
(4)金属粘连拉伤凸模表面、线状划伤扩展成裂纹。
预 防 措 施
(1)采用软氮化处理。
(2)选用粗粒度砂轮、接近成品尺寸时,磨削进给量相应减小。
(3)控制热处理温度。
(4)降低凸模表面的粗糙度,提高硬度,并精细加工,抛光至Ra0.4μm以下。
中心开裂
(1)尾部端面上。
(2)由中心径向放射状。
形 成 原 因
(1)材料组织不均匀,碳化物严重偏析。
(2) 凸模尾部端面不平,受力不均匀。
(3) 凸模垫块薄,且支承面积小。
(4) 凸模垫块压塌变形,使凸模尾端的中心部位悬空。
预 防 措 施
(1)采取锻造工艺,将碳化物偏析控制在三级以下。
(2)凸模尾部要平,不允许留顶尖孔。
(3)增加垫块厚度,加大其支承面积。
(4)垫块应定期检查,遇有变形时应重磨或更换。
5 结束语
上述技术措施,应综合应用,既要提高模具寿命,降低模具成本,又要使其产品质量不受影响。应以不断探索、不断更新、不断提高、不断总结的精神来完成现代模具生产。
声明:本网站所收集的部分公开资料来源于互联网,转载的目的在于传递更多信息及用于网络分享,并不代表本站赞同其观点和对其真实性负责,也不构成任何其他建议。本站部分作品是由网友自主投稿和发布、编辑整理上传,对此类作品本站仅提供交流平台,不为其版权负责。如果您发现网站上所用视频、图片、文字如涉及作品版权问题,请第一时间告知,我们将根据您提供的证明材料确认版权并按国家标准支付稿酬或立即删除内容,以保证您的权益!联系电话:010-58612588 或 Email:editor@mmsonline.com.cn。
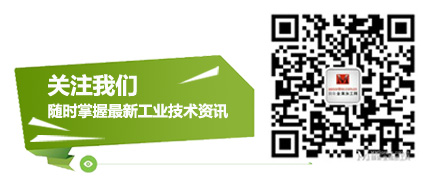
- 暂无反馈