闭合复动挤压成形模具的液压缓冲装置
引言
快速、直接、无切削(即净形Net Shape)或少切削(即近净形Near Net Shape)加工,一直是机械工业追求的目标。近年来,随着工业的飞速发展,特别是汽车工业的不断发展,对复杂形状零件和高精度零件的成形提出了更高的要求。采用冷挤压技术无疑是解决上述问题的最有效的方法。但传统的冷挤压工艺已经不能满足上述要求,因此新的冷挤压技术应运而生,如出现了闭合成形、FCF工艺、复动成形复合成形等。这些新工艺、新方法的应用,较好地解决了工业发展对复杂形状零件和高精度零件的直接、少无切削的需要。这些技术的应用不但解决了成形质量问题,而且也解决了传统工艺中,工艺路线长,需要工序间的软化和润滑等问题,从而不但保证了加工质量,而且还大大节省了费用,因此应用前景非常乐观。闭合复动挤压成形是冷挤压新技术中应用较广泛的一种。采用闭合复动挤压成形技术的模具不同于传统的模具结构,而模具的缓冲装置是这类模具设计的关键。
1 闭合复动挤压成形原理
所谓复动挤压成形,即在同一工位,具有两个或两个以上工序动作的冷挤压成形过程称作复动挤压成形。复动挤压成形可以按模具型腔是否闭合,分为闭合复动挤压成形和非闭合复动挤压成形两种状态。由于采用闭合复动挤压成形工艺可以获得较好的成形质量,因此得到了较广泛的应用。鼓形零件采用传统墩挤成形过程和采用闭合复动挤压成形过程的比较。通过比较可以看出,采用传统墩挤方式不可避免会产生飞边,尺寸入的数值会根据料的多少产生变化,从而影响到鼓形:的数值,而:在这里代表着复杂型面,一般应由模具保证,不再加
工,这样便直接影响了成形零件的成形质量。采用闭合复动挤压成形的工作过程。工作过程中,上下模子先进行合模,然后下模芯轴向上运动将材料挤压成形。可以看出,图中表示的尺寸h被严格控制,从而保证了复杂型面的成形质量。
2 液压缓冲装置结构
鼓形零件闭合复动挤压成形过程,驱动下模芯轴需要有强大的动力,这样对压力机和模具设计带来了许多困难。同样的原理,采用图2所示的运动方式,即可以在普通压力机上实现零件的闭合复动挤压成形。当工作开始后,随着压力机滑块下行,上下模子闭合,然后,随着滑块的继续下行,上下模子一起相对下模芯轴运动,完成闭合复动挤压成形。这种设计方式,上下模子的闭合和芯轴对毛坯材料的挤压,都是通过滑块的强大动力来完成的。因此可以直接在普通的液压机和机械压力机中进行。需要解决的问题是如何解决模具相对芯轴运动时的缓冲问题。由于液压具有自动过载保护的功能,因此采用液压缓冲装置较好地解决了这一问题。当毛坯材料过多或过少情况下,闭合复动挤压成形的零件状况。可以看出,料少会直接影响零件的成形质量,因此适当增加材料,在易加工面留点加工余量,将不会影响成形质量。
单缸缓冲闭合复动挤压成形模具液压缓冲装置。整个模具是由液压柱塞缸来支撑的。下模座实际上是一个柱塞,下模子通过压紧螺母固定在下模座上,而下模芯轴直接固定在下模板上。当具有上下两个芯轴驱动的闭合复动挤压成形过程,上下两个模座均应设置缓冲缸。
3 液压系统工作原理
单缸缓冲闭合复动挤压成形模具缓冲装置的液压系统原理图。系统由缓冲液压缸7,蓄能器8,单向顺序阀6,辅助液压泵1,单向阀3,溢流阀4,两位两通电磁阀2和安全阀5等组成。油泵启动后,油液经两位两通电磁阀卸荷;工作开始后,电磁阀通电,压力油经单向阀输入液压缸,与此同时,蓄能器中的压力油亦经单向顺序阀输入液压缸,实现快速充油,将下模顶起。上下模下行时,缓冲液压缸内压力急剧上升,单向阀关闭,油液通过打开顺序阀排入蓄能器。
工作完成后,随着滑块上升,模具型腔内压力迅速释放,蓄能器内的油液立即通过单向阀向液压缸充油,并将下模子顶起。
4 结语
闭合复动挤压成形是冷挤压技术中较先进的金属成形方法,其关键是模具缓冲机构的设计,采用液压缓冲装置无疑是一种优选的方法。在具体设计时,应尽可能选择较大的柱塞面积,这样,可以选择较小的液压系统工作压力,同时根据系统工作压力来选择顺序阀的调定压力,一般顺序阀的调定压力应比系统工作压力高出2-3MPa,安全阀的调定压力应大于顺序阀的压力;并应精心设计蓄能器的容量、最低和最高工作压力等。对于闭合成形模具还应选用高精度的导套导柱进行导向。
声明:本网站所收集的部分公开资料来源于互联网,转载的目的在于传递更多信息及用于网络分享,并不代表本站赞同其观点和对其真实性负责,也不构成任何其他建议。本站部分作品是由网友自主投稿和发布、编辑整理上传,对此类作品本站仅提供交流平台,不为其版权负责。如果您发现网站上所用视频、图片、文字如涉及作品版权问题,请第一时间告知,我们将根据您提供的证明材料确认版权并按国家标准支付稿酬或立即删除内容,以保证您的权益!联系电话:010-58612588 或 Email:editor@mmsonline.com.cn。
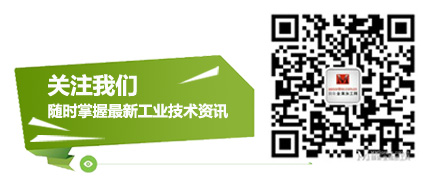
- 暂无反馈