用好热模钢的体会
因为中国模具工业的迅猛发展,世界各国的优秀模具用特种钢在中国都有很好的巿场。但由于使用时操作工艺存在问题,往往出现使用最合适的高级钢种,取得的效果却与使用中碳钢差不多的现象。
最近几年,国外在中国定制压铸模具及压铸件的势头很猛。但在制造过程中,有些压铸模具的型腔钢材甚至仅使用千把模,就出现了开裂。这就造成好钢没有用好。
如何让优质特种钢发挥其本身优势,提高模具寿命和产品质量呢?
压铸模具的型腔基本上采用镶嵌的方法进行制造,可以节省特种钢。但在设计时务必要计算好刚性平衡点,以免为节省特种钢而模具刚性不够,造成模具寿命大幅下降。在设计时应优先考虑冷却系统的设计和滑块的工作可靠性,以保证模具使用寿命。其次是进行模流分析,选择最合适的流向、进料口方案。在设计型腔时应尽量避免在压铸时型腔内应力汇聚在相对薄弱的部位。
在加工过程中,首先是粗加工与半精加工。在此过程中,要注意加工过程的内应力积累。尤其是加工到后期,工件不应有严重摔、砸,以免引发内应力造成潜在的裂纹。
然后送去热处理。在真空炉内应该有较平缓的升温过程,当达到500-550℃时,有一个保温过程;一般为第一段升温时间的1.5倍。然后进入第二段升温,达到750-800℃时,应有第二段升温过程二倍的保温时间,以确保加工过程中内应力的较好消除。接下来,在第三段升温至1000-1050℃时,应有第三段升温的二倍的保温时间以确保被加工钢材的通体温度均衡。淬火后风冷至常温,然后进行第一次回火。当然,最好是油冷,其金相状态会适当增加使用寿命。油冷时淬火件应在不停流动的淬火油内冷却,以使其硬度均匀。
回火在二级升温后至600℃时保温,时间视工件大小及厚度而定。一般全过程为24小时或以上,出炉后油冷至常温。此时的材料硬度应该在HRC46-HRC52之间。
接下来是半精加工和精加工。完毕以后进行第二次回火,此时材料硬度应该在HRC44-HRC50之间。
压铸模具型腔应该不允许焊接,因为即使预加温后,用同种材料焊接,焊接后保温,该部位的使用寿命不到正常寿命的三分之一。有时因为设计变更,不得不进行型腔焊接,最好是退火、重新淬火后回火。即使这样,其寿命最多达到正常寿命的一半。
滑块。一般滑块应采用与型腔本体材料不同的材料,且硬度与型腔本体材料不同,以保证使用过程中只更换损耗的那一件。若能够使用铜基石墨摩擦片则更好。此种工艺已迅速普及,因为滑块与型腔一般不会损坏,只需更换摩擦片。
试模。试模时许多工厂为图省事,往往不给模具接冷却水,这是绝对不允许的。试模不接冷却水将直接导致压铸模具使用寿命的严重降低。即使当时看不见裂纹,在正常使用时必定会提前出现型腔裂纹。
在试模时,一定要注意,模温不到时,只能逐步加压。待模温均匀达到规定时,注射压力才能到位。
铝或锌液的温度要按照规定参数,擅自提高液温也会损害模具。
使用期回火。一般新模具投入使用5000模后(包括试模次数),要将型腔拆下进行一次回火以消除内应力。然后正常使用至15000模左右再去回火。如果型腔表面出现裂纹后就别去回火了。
模具的养护。在模具使用后进入库存状态时,应放尽油和水后,在型腔内涂防锈油,在滑动部位涂耐高温机油,封闭冷却系统和型腔以防锈蚀。
随着模具工业的快速发展,许多新工艺也被使用到模具制作中来。例如真空喷涂陶瓷材料在进料口所对的型腔部位,可以使该部位的寿命大大提高,保持型腔形状和尺寸的精度,使模具整体寿命更加保持一致。我所知的有涂层为0.01毫米和0.001毫米两种,也有型腔整体喷涂的。如果采用此工艺,型腔钢材用一般热模钢就可得到高级热模钢的使用效果,大家不妨试用后再推广。
声明:本网站所收集的部分公开资料来源于互联网,转载的目的在于传递更多信息及用于网络分享,并不代表本站赞同其观点和对其真实性负责,也不构成任何其他建议。本站部分作品是由网友自主投稿和发布、编辑整理上传,对此类作品本站仅提供交流平台,不为其版权负责。如果您发现网站上所用视频、图片、文字如涉及作品版权问题,请第一时间告知,我们将根据您提供的证明材料确认版权并按国家标准支付稿酬或立即删除内容,以保证您的权益!联系电话:010-58612588 或 Email:editor@mmsonline.com.cn。
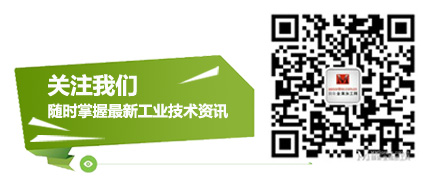
- 暂无反馈