我国注塑模CAE技术的应用现状分析
注塑模CAE技术的应用在国外已相当普遍,而在我国注塑模具设计仍停留在以经验为主导的设计模式,成熟的注塑模CAE用户屈指可数。主要原因在于以下几方面:
1)注塑模CAE系统对工程师的综合素质要求较高。注塑模CAE系统是一个很好的工程分析工具,但它只能帮工程师了解产品存在的问题,提供解决问题的思路,而并不能提供解决问题的方案。要充分发挥注塑模CAE技术的作用,关键在于对分析结果的正确评价与最佳解决方案的确定。而分析结果的评价又涉及到高分子材料、产品结构、模具、注塑成型工艺等方面的相关理论和经验,这就对工程师的综合素质提出了较高的要求。
2)还未正确认识注塑模CAE技术对模具设计的指导作用。注塑模CAE技术是多学科相互交叉的产物,既包含了科学的数理计算方法也加入了诸多资深工程师的经验。注塑模CAE分析是了解和优化模具设计与制造工艺的最佳途径,但在求解与有效运用分析结果之间仍有相当大的差距。有些企业虽然购买了CAE软件,但软件使用人员不懂如何有效的应用分析结果来指导模具设计,使企业并不能从CAE技术的应用中带来经济效益,造成资源的巨大浪费,也影响了注塑模CAE软件的进一步推广应用,因此要缩短这一差距主要还是要靠CAE分析工程师自身的素质不断提高。值得注意的是,注塑成型CAE分析是一种理想状态下的理论分析,并不能完全取代试模,晒Φ淖⑺艹尚头治霾坏扔诔晒Φ氖导首⑺苌
3)目前主流算法的局限性是CAE软件推广应用的瓶颈。注塑模CAE软件的发展经历了从中面流技术到双面流技术再到实体流技术的三个重要的里程碑。目前由于实体流和双面流技术算法的不完善,三种分析技术仍然并存。
中面流(Midplane)技术的应用始于20世纪80年代。所谓中面就是提取的位于模具型腔和型芯中间的层面来简化3D模型。用一维和二维的耦合算法和来代替三维计算。基于中面流技术的注塑流动模拟软件应用的时间最长、范围最广。但实践表明,基于中面流技术的注塑模CAE软件在应用中具有很大的局限性:(1) 专业的注塑模CAE软件造型功能较差,采用手工操作直接构造中面模型十分困难,建构过程往往需要花费大量的时间;(2)由CAE软件根据产品三维模型自动计算生成中面模型的效果不理想,网格修补工作量大;(3)由于CAD阶段使用的是产品的物理模型,而CAE阶段使用的是产品的数学模型,两者的不统一,使得二次建模不可避免。由此可见,中面模型已经成为了注塑模CAE技术发展的瓶颈。
20世纪90年代后期双面流(Fusion)技术诞生。双面流是指在制品的内外表面产生有限元网格,而不是在中间面。双面流技术所应用的原理与中面流没有本质上的差别,所不同只是将沿中面流动的单层料流演变为沿上下表面协调流动的双层料流。目前基于双面流技术的注塑模CAE软件均可以将CAD系统输出的三维模型的STL文件格式转化为有限元网格模型。因此与中面流技术相比在模型处理上却大大减轻了用户建模的负担,提高了有限元建模的效率。因此,基于双面流技术的注塑模CAE软件在全世界拥有了庞大的用户群,得到了广大用户的支持和好评。但由于上下表面网格无法一一对应,造成上下对应表面的熔体流动前沿存在差别,使得双面流技术分析的准确性受到一定的限制。此外双面流技术也只是一种从中面流技术向实体流技术过渡的手段。实体流技术最终必将取代双面流技术。
实体流(Solid)技术在实现原理上仍与中面流技术相同,所不同的是数值分析方法有较大差别。 在实体流技术中熔体的厚度方向的物理量变化不再被忽略,这时只能采用三维有限元网格,依靠三维有限差分法或三维有限元法对熔体的充模流动进行数值分析。因此,与中面流或双面流相比,基于实体流技术的注塑模CAE软件目前所存在的最大问题就是计算量巨大、计算时间长,例如电视机前壳这样的塑料制品,用现行的注塑模CAE软件,用目前配置最好的计算机仍需要数百小时才能计算出一个方案。这与目前的模具开发周期相违背,成为制约注塑模CAE技术全面推广的瓶颈。因此要真正推广基于实体流技术的注塑模CAE软件仍有待软件算法的改进和计算机硬件设备速度的提升。由于中面流技术久经考验,计算速度快,分析准确性高,至今仍然是注塑成型CAE分析的主流。
声明:本网站所收集的部分公开资料来源于互联网,转载的目的在于传递更多信息及用于网络分享,并不代表本站赞同其观点和对其真实性负责,也不构成任何其他建议。本站部分作品是由网友自主投稿和发布、编辑整理上传,对此类作品本站仅提供交流平台,不为其版权负责。如果您发现网站上所用视频、图片、文字如涉及作品版权问题,请第一时间告知,我们将根据您提供的证明材料确认版权并按国家标准支付稿酬或立即删除内容,以保证您的权益!联系电话:010-58612588 或 Email:editor@mmsonline.com.cn。
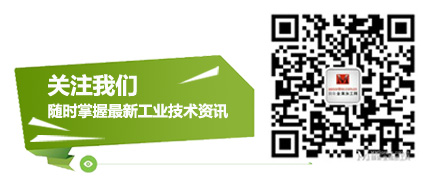
- 暂无反馈