电铸镍合金模具
经过加工和蚀刻的钢制注塑模是用于生产中、低档汽车内饰件和外饰件的主要模具,然而,在许多高档汽车生产中,电铸镍合金被选作为生产软接触内饰件的模具,因为它可以用于复制中空模塑中轻质模具的微细晶粒,可用于模压加工很深的隐窝和深槽,以便于安装内饰件、AC空调通风管、收音机、平视式投影仪和隐蔽式气囊展开门。PVC聚氯乙烯材料具有优良的脱离镍合金模具的性能。而比较新型的氨基甲酸乙酯材料从镍合金模具中的脱离比较困难,而且其费用要比PVC高5倍以上,之所以使用这种材料是因为汽车报废后,是因为其具有很好的绿色环保性能。
电铸镍合金模具的制造
这一工艺主要包括一个电镀槽,里面有玻璃纤维基板和环氧电镀心轴,通过电镀使镍金属表面不断在玻璃纤维基板的顶部成长。心轴是按照汽车制造厂审批的CAD文件设计图开发的。对于各种用途的镍合金模具而言,其电镀层厚度为2mm~6mm,以独立的形式安装于钢铁框架内,周围填铸环氧树脂,以作为负荷之需。作为仪表板中空模具的镍金属外壳平均重量约为68kg。用于A级卡车车顶的全套RTM模具需要两套互相匹配的镍金属外壳,各重454kg,而整个复合模具的重量为6800~9080kg。
主动轮侧向模具的凹洼和隐窝处A级表面近视图
选用电铸工艺的目的是利用它的特殊加工能力,它可以在多种形面上复制微细的晶粒,因为,在某些情况下这类形面是无法加工和蚀刻的。如果能够,那也不可能生产出在同一处带有完全一样微细晶粒的多种模具,让门心板晶粒线与仪表板和“A”立柱一起流动。一个典型的非机加工零件应该是一个360°、纹路细腻的抓柄式扶手门板,不带任何分型线。
选用镍金属的目的是因为其具有承受热震的能力。对于仪表板壳体的中空制模,模具必须经受每隔3~4min的110℉-475℉高温。然而,只有使用镍金属,在300℃~350℃的高温下,给以适当的负荷支持,才能经受900 psi的压力周期。
对于使用量不大的模具来说,采用电铸工艺制造模具在制作成本上可以与金属机加工模具一争高下,因为生产象RTM“A”级卡车罩那样的零件需要切削大量的金属。然而,在引进新型CNC高速、4轴加工头铣床以后,这一优势就消失了。对于要求生产形面复杂的细晶粒多模具而言,采用电镀镍金属工艺仍然有一定的优势。
电铸工艺也用于生产咖啡过滤器、印花网筒、直升机螺旋桨叶片耐磨尖端的电镀、高压锅模具、吹塑模和拷贝印鼓。在高压应用领域不经常使用镍金属,但小型注塑模使用镍金属,并用低熔点金属浇铸支持,然后加工,安装到标准的模座内。易于翻转或易于加工的简单浅薄形状可以比采用电铸工艺更加快速和更加便宜的生产。如果公差规格低于±0.25mm,就不宜使用电铸镍金属。
仪表板模具
在生产仪表板模具前,应事先在木模车间加工一个REN WOOD木模。OEM原始设备制造商负责检验和审查木模的形状和表面质量。OEM也需在木模重复位置和模型上的晶粒方向引导下,规定0.5mm粒度的乙烯基材料或一种较新的凝固工艺。包覆的模型样式由OEM审核批准。然后,包覆的模型用硅树脂浇铸复制。玻璃纤维和环氧主心轴在硅树脂模中制造。在模型上切割或安装包覆材料时会引起主心轴造成缺陷,不过可以采用手工方式加工(抛光纹理),沿着任何表面不完善的地方修正纹理流向。主心轴的样式需经审核批准。
生产用的硅树脂模由正确的经过审批的主心轴浇铸而成,而玻璃纤维和环氧电镀心轴则由硅树脂制成。硅树脂一般将在丢弃延伸、损毁或时效收缩前的6个月期限内用于三根心轴的电镀。心轴必须经过稳定化处理,这样,就可以用于生产新的模具,其使用期至少可达10年(模具使用寿命加更换零件时间),而包覆模型也可达到它的服务目的,因为包覆材料会在一年内逐渐变质。
由于电镀心轴是不导电的,如果不使用特殊的导电涂层,它就无法接受电镀。电缆线与整流器连接,而整流器安装在一个座架上,然后放置到电镀槽之中。平均厚度5.5mm的壳体需要6周的电镀时间。在电镀期间,应将模具从电镀槽中拿出来以检查其电镀层的厚度,凡是厚度已经达到规定要求或已超过要求的地方应一一标记出来,然后再放回到电镀槽内。以外面的直角作为避雷针,电镀跟随着形面继续动作,使电镀层很快达到所需的厚度。直角内部的电镀速度较慢,狭窄的隐窝处电镀最为困难。一般来说,里面的圆角半径最低为0.2mm;狭窄的隐窝和凹洼处宽度与深度之比应该是2:1。
当壳体的电镀层厚度确定合适以后,需要将其从电镀工艺中取出,通过磨削“B”表面,将厚度调整到±0.3mm。电镀心轴从镍金属模取出时,因模具锁住、隐窝缝隙太窄或太深而常常被损坏。导电涂层一般会遗留在镍金属上,需要用化学方法从“A”表面或晶粒化表面上清除。
壳体将在这一点上按照规定的要求准备加热,例如“B”表面上的铜焊钢管热油加热,或安装在钢架内,然后安装到充满油的油室内加热,或安装在热浴槽的框架上浸渍加热,或安装到一个框架上用加热炉加热或火焰冲击加热。镍金属安置在座架上,并配有可分离的支座组件,用于聚合体干燥搅拌以制造仪表板外壳。
由于制造模具的工艺各不相同,因此,模型必须能反映出各工艺步骤中发生的变化。对于一个设有热油管路的模具,其制造时的收缩率一般为0.6%,PVC的聚合体处理器收缩率一般为1%,总计为1.6%,当模型加工时,应扣除0.5mm的包覆层厚度。
一般来说,这些系数需要在原型制造(通常100~300辆汽车)和正式投产周期之间确认和调整。由于OEM急于要降低开发一辆新款汽车所需的总体时间,他们要求制造一套直接用于生产的模具,也就是说要跳过原型模具的制造,直接将第一套模具应用与实际生产之中。与生产厂共同合作的模具制造商在他们制造模型前或利用模具制造一个新产品的零件前,必须正确地确定这些系数。
面临的挑战
目前,汽车模具工业的最大问题是将新几何形状的晶粒结构引入市场。OEM原始设备制造商对氨基甲酸乙酯和PVC材料结合应用到同一辆汽车时的光泽不甚满意。有些晶粒钢板可以用新的激光和CAD程序加工生产用于包装,但不能在模具中用酸蚀刻。当新的木模被包覆到电铸镍金属模具模型时,电铸机就能够困难地生产晶粒,但它们不能永远维修晶粒。
零件生产商业也发现,以标准的方法清洗模具会引起圆角细微处的过量磨损,实际上它们就是透镜。将这个模式想象成是一系列的透镜,以不均匀的模式方向将光线反射出来。清洗和生产过程中的侵蚀改变了这些透镜的几何形状—引起成品的反射不同,出现黑点或暗点。在某些情况下,包覆过程会重复8次或更多的次数,以获得OEM原始设备制造商的批准。
当曲面被直线晶粒包覆时,整个汽车上下的曲面会引起切割处直线的弯曲或不相匹配,无法适应形面的晶粒模式。有些欧洲的厂商报道说,由于磨损、损坏或光泽的变化,几何模式的模具平均寿命为每个只能生产1万个零件,而且这些损坏所造成的一切缺陷无法修复。如果将这一寿命与老式的动物晶粒(晶粒任意排列)模式相比,后者每个模具可生产85000个零件,而且技术人员可以修复损坏的晶粒结构。汽车客户也报道说,有些模型很难清洗,因为灰尘和纤维屑积聚在几何模型的隐窝处。
凡是退回到模具制造商返修的模具,也许需要进行多次的试验来填补这些损坏的区域,然后用手工细化处理或酸洗蚀刻处理。每次经过返修以后,模具被送回到生产厂审批,以再次用于生产壳体。这一过程需要重复多次,需要很多的工作时间、发运时间和试用时间,费用很高,这种经过修复的模具能够通过质量控制的百分比机率很少。修理区的面积越来越多,每次试验和所需的费用接近更换一个模具的费用。
漫长的维修时间会造成生产线停产,车间内作为后备库存所需的模具量将大幅度上升,这是目前所面临的主要风险。这会造成模具制造商不能及时交货而无法立即满足模具的需求。最终的结果将是:模具制造商因维修潜力不足而无法提供保修期,因而无法避免电铸机上的经济损耗。在与汽车制造厂签订合同前,模具制造商和相关的一家或两家供货商必须审核晶粒要求、可维修性和预期的模具使用寿命,保证对所需的模具数量和费用有一个清醒的认识,以达到所预测的销售目标。如果模具的寿命因晶粒结构而降低,可能会要求模具制造商和/或供货商提供新的模具而不再偿付附加的费用。而且必须注意,从主心轴上更换模具需要花费整整14~16周的加工时间(每周7天、每天24h工作,从收集CAD数据开始,生产第一个模具不少于21~26周,尽管如此,但这样做既耽误时间,又浪费资金)。汽车装配线停产所造成的损失可达到每分钟3万美元。
采用旋铸镍金属模具制成的门板小手把
应吸取的教训
总的来说,显然,由于电铸法的成本较高、应用范围特殊、模具所需的总体费用较高以及成品的费用也较高,因此在今天的模具制造市场中,它只占很小的百分比。然而,由于电铸法具有独特的重复生产能力,它可满足其他模具制造工艺所不可能达到的要求。在及时供货生产气候条件下,每天受到紧迫的利润责难压力,因此,在时间和费用上的考虑导致这一行业面临一系列的问题,最近由于在样式设计方面的需求趋势,使这些问题进一步恶化。由于电铸槽内的工艺时间、镍金属的费用和设计者的梦想不能适应变化,因此,惟一的解决方法是:在与汽车制造厂签订合同时,小心谨慎,专心一致。但这是一个属于律师和会计师们研究的课题,而且也是属于一个新的讨论课题。
声明:本网站所收集的部分公开资料来源于互联网,转载的目的在于传递更多信息及用于网络分享,并不代表本站赞同其观点和对其真实性负责,也不构成任何其他建议。本站部分作品是由网友自主投稿和发布、编辑整理上传,对此类作品本站仅提供交流平台,不为其版权负责。如果您发现网站上所用视频、图片、文字如涉及作品版权问题,请第一时间告知,我们将根据您提供的证明材料确认版权并按国家标准支付稿酬或立即删除内容,以保证您的权益!联系电话:010-58612588 或 Email:editor@mmsonline.com.cn。
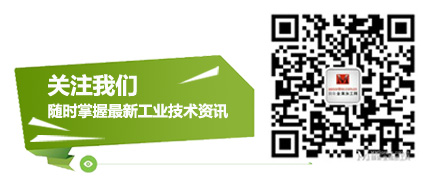
- 暂无反馈