夹具的优化设计及经济性分析研究
现代夹具(如成组夹具、通用可调夹具、组合夹具)的结构共性,大都由通用基体和可调、可换元件两部分组成。其通用基体部分是零件组中所有零件共用的主要部分;而可调、可换部分则是针对零件组中某种(或几种)特定零件而专门设计的专用或准专用部分。可调、可换元件一般是随夹具适用对象数的多少而变化的,因此,在现代夹具设计时,适用对象种数选择得是否合理,将直接关系到可调、可换元件的数量和夹具的整体经济性,以成组夹具为例进行探讨和研究。
1.优化设计分析
这种优化设计的特点:
a. 可以正确确定适用对象种数。
b. 根据优化设计的结果,对可调、可换元件和通用基体的结构设计从成本比例的角度进行调整,从而使之满足优化设计,达到整体经济性的目的。
1) 成组夹具的成本
成组夹具的成本Cc=Ct+PN (1)
式中:Ct——成组夹具上通用基体的成本,元;
P——成组夹具上可调、可换元件平均单件成本,元/种;
N——成组夹具适用零件种数,种。
式(1)中,t对整套夹具来说是一常数;PN则随着N的增减而变化(其中P为常数)。
2) 衡量成组夹具经济性的2个基本概念
从成组夹具适用对象种数所分摊的夹具成本看,可以认为:适用对象在成组夹具满负荷的范围内,对象种数愈多则夹具分摊到适用对象种数上的单位成本就愈低。
从夹具上的可调、可换元件看,随着夹具适用对象种数的增加,则夹具上的可调、可换元件也随着增加,这时,可调、可换元件的设计、制造费用以及夹具的调整次数和调整、保管费用也随之相应增加。
以上2个不同内容有些矛盾的因素,从不同的角度影响着成组夹具的经济性。下面将通过建立数学模型,进一步阐明上述这2个基本概念。
3) 建立数学模型
a. 从式(1)中得知,在1≤N≤Nx时,其中Nx为夹具在满负荷时的适用对象种数,成组夹具分摊到适用对象种数上的单位成本
P0=(Ct+PN)/N
整套夹具中可调、可换元件所需的费用PTW=PN (3)
b. 建立数学模型F
把式(2)和式(3)进行叠加,则得
F=P0+Ptw=(Ct+PN)/N+PN
4) 最优数NK的求解
假设:Ct=1,000元,P=50元/种,Nx=100种对式(4)用微分法求极小值K,即求出NK值
令 dF/dN=0
即 F=-Ct/N2+P
又令 F=0
则有 N=(Ct/P)½ (5)
式(5)中求出的N 即为NK,且1≤NK≤Nx。得 NK=(1,000/50)½≈4.5种
取整数,则NK=5种,该NK值,亦即为当Ct=1,000元,P=50元/种时,夹具适用对象种数的最优数值。
2 .优化设计的现实意义
当所设计的成组夹具,其适用对象零件种数等于或接近NK值时,可以认为这套成组夹具符合经济性的原则;反之,从经济的角度可以认为是不合理的。这时,应该从各方面采取调整措施,如修改通用基体或可调、可换元件的结构设计,使之Ct值与P值的比例关系得到调整,最终符合经济性的原则。
在成组夹具设计中,根据夹具的复杂程度,从已积累的统计资料中取得Ct值与P值的当量值,以预定成组夹具适用对象零件种数,然后对实际的Ct值与P 值进行评价,这样可以达到减少过程损失的目的。
为了使成组夹具达到优化设计,必须对NK进行求解,但当已经掌握了它们内在的数学关系之后,便没有必要在每套成组夹具设计中都逐个进行求解,为了达到提高设计工效之目的,可以通过建立速查表的办法来提高优化设计和评价效率。
按照此方法进行通用化工装设计,可大大降低工装成本,缩短产品开发周期。由于通用夹具在产品开发中的占总体工装的1/5~1/10,其制造可由本企业的机修单位来完成,工装夹具的到货周期由原来的几个月缩短为几天。
可以大大减少夹具库存量。以工装库存的最低储备量来估算,库存量为现场用量的2~3 倍,而通用工装夹具会使原来现场使用的夹具由几百种下降为几十种,库存量可降至1/2~1 倍的生产用量。
大幅度提高单机设备的通过能力,提高产品质量。现场同类设备由于工装的差异影响了设备本身较宽的工艺通过能力,通用工装使现场整体的设备通过能力得到提高,有利于均衡生产,提高了工艺质量和产品质量。
提高现场应变能力和单一品种的加工能力,有利于物流顺畅和均衡生产。
声明:本网站所收集的部分公开资料来源于互联网,转载的目的在于传递更多信息及用于网络分享,并不代表本站赞同其观点和对其真实性负责,也不构成任何其他建议。本站部分作品是由网友自主投稿和发布、编辑整理上传,对此类作品本站仅提供交流平台,不为其版权负责。如果您发现网站上所用视频、图片、文字如涉及作品版权问题,请第一时间告知,我们将根据您提供的证明材料确认版权并按国家标准支付稿酬或立即删除内容,以保证您的权益!联系电话:010-58612588 或 Email:editor@mmsonline.com.cn。
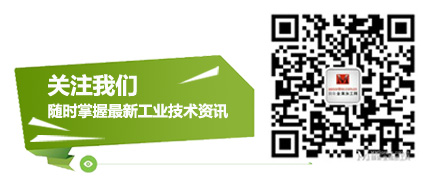
- 暂无反馈