高速加工和高效加工推动生产技术的不断进步
20世纪80年代末兴起的高速加工(HSC),由于显著提高了切削速度和进给速度,从而大大缩短了加工时间,提高了工件表面质量和加工精度。并因此而实现减少加工工序和简化生产工艺流程,以及促使一些行业生产方式的转变,有力地推动了整个生产技术的发展。
高速加工使“生产率”和“柔性”两个相互矛盾的特征参数融合到一起,从而用高速加工中心组成的柔性生产系统替代传统的刚性自动线,推动了汽车等中、大批量生产行业中生产模式的转变。
高速加工导致工艺替代,从而简化生产工艺流程。在模具制造中用高速硬铣替代电火花加工是一个十分典型的例子,淬硬后的工件可在一次装夹下通过粗铣和高速精铣加工成成品。高速硬铣的应用,为模具制造实现CAD-CAM-HSC的集成创造了条件,高速硬铣工艺无疑给模具制造技术带来了一次重大变革。
自高速加工兴起的十多年来,高速加工技术获得了广泛推广和应用。在生产中,通过高速加工,显著缩短了基本时间,也相应地提高了辅助时间相对于基本时间的比例(从过去的7%:93%到目前的35%:65%,对于铝合金材质工件的加工,这种比例更达到了50%:50%)。从目前的技术状况看,通过高速加工进一步降低基本时间的潜力已不是很大。
近年来,为进一步提高生产效率,愈来愈多的则是采用高效加工(HPC)——提高单位时间材料切除量和显著减少辅助时间——来进一步降低切削过程中的基本时间和辅助时间。
高效加工(HPC)与高速加工(HSC)不同的是,它并不只是限于提高切削速度和进给速度,而是把优化材料切除率放在首位,旨在通过提高单位时间的材料切除量和降低加工时间(基本时间和辅助时间)来进一步降低加工费用。
材料切除率(Q)决定于侧吃刀量(ae)、背吃刀量(ap)和进给速度(vf)。对于铣削加工,进给速度(vf)又取决于每齿进给量(fz)、刀齿数(z)和铣刀的转速(n)。
单位时间的材料切除量可用Q=ae·ap·vf /1000=ae·ap·fz·z·n /1000 (cm3/min)来表示。
我们从这个表达式可以看出,材料切除率与5个切削参数有关,所以,高效加工可以但并不是必须包括高速加工,这意味着高效加工和高速加工之间不存在明显的界限。
航空工业是最早应用高速加工和高效加工新工艺的部门。飞机的梁、框架和大型壁板等承力构件采用的是整体结构件,加工时其毛坯75%~95%的材料将被切削掉,对于这种特别高的切削量,无疑采用高效加工是最合适不过的。在德国奥格斯堡(Augsburg)的EADS(欧洲航空防御和航天公司)在20世纪90年代采用HSC工艺加工军用飞机某一铝合金整体构件,主要目的是为了简化生产工艺流程,以较少的工序获得高的表面质量,而不是提高材料切除率,加工时使用了54把刀具,共花了25个小时完成加工。为进一步挖掘生产率的潜力,后来就很自然地转向采用高效加工,采用了40把刀具,加工时间仅为12个小时,减少了一半多。
特别是对于铣削加工,铣刀所能达到的材料切除率已成为衡量铣刀加工经济性的一个重要指标。近年来,许多刀具制造厂相继开发出了众多高进给速度的铣刀。这些铣刀虽然结构形式不尽相同,但一个共同特点是具有适合于实现高速进给的刀刃几何形状。这种几何形状的特点是切削刀刃具有一个很大的圆弧半径,这就稍许限制了铣刀的背吃刀量(ap),而且由于较小的主偏角使作用于铣刀上的径向切削力大大减小,从而有利于采用很高的每齿进给量进行加工。
例如,在粗加工40CrMnMoS86材质的玻璃瓶吹模时,德国Franken刀具厂对采用装有三个圆刀片的铣刀和装有3个Time-S-Cut刀片的高进给速度铣刀进行铣削效果比较。前者采用的切削用量为Vc=250m/min, fz=0.3mm, ap=0.75mm和ae=18 mm,加工时用冷压缩空气进行冷却,加工所需时间为9分钟。后者在切削用量方面,将ap减小为0.5 mm,而fz则提高到1.0 mm,结果加工时间仅用了4分钟。在时间节省上达到了55%,也就是机床每小时使用节省了55%。
从这里可以看出,通过采用较高的切削参数,高效加工可以获得很高的材料切除率,显著地缩短加工时间。但是高效加工,并不只是采用很高的切削参数,还可以通过能显著减少辅助时间的其它加工战略来实施高效加工。例如采用复合刀具(如复合阶梯钻、钻铣螺纹刀具和其它用于综合加工的复合刀具)、圆周进给铣削的多功能立铣刀等各种先进刀具可以显著减少换刀次数和降低辅助时间,由此显著地提高生产效率。
复合刀具是在一把刀具上集成多个加工工序,往往在一次加工行程中实现多个加工部位的综合加工,采用这种刀具不仅免去了换刀而且有利于提高加工精度,并可省去工序间的精度测量,从而可显著提高生产效率。
采用多功能立铣刀在加工中心上进行铣孔时,同样可以减少换刀的次数。铣孔时,旋转的铣刀绕Z轴作螺旋插补运动,在一次工作行程就可加工出所需大小的孔。例如加工直径为285 mm的孔,采用直径160 mm的铣刀,在一次工作行程中即可完成加工任务,这比常规工艺可五道扩孔工序和节省73%的加工时间。
近年来,高效深孔钻头的问世,显著提高了深孔钻削的效率,一种由德国Gühring公司开发的双刃整体硬质合金麻花钻,在钻孔径比(l/D)为20的深孔时,采用微量润滑(6~8ml/h),不仅采用比传统大流量湿式钻孔高10~12倍的进给速度,并且在钻孔过程中不需要进行排屑循环,由此大大提高了加工效率。并且,在钻孔时钻头的径向偏移特别小,能获得较好的表面质量。
在生产中,高速加工和高效加工工艺已获得广泛推广和应用,这两种工艺的共同特点是能显著降低加工时间和缩短生产工艺流程,而不同的特点是高速加工是采用高的切削速度,目的在于获得高的表面质量和简化工艺流程,因此高速加工更多的是适用于精加工;而高效加工主要是采用高的切削参数,以获得高的单位时间的材料切除量,从而显著缩短加工时间。对于以获得高的材料切除率的高效加工则适用于用来进行粗加工。在实际生产中,这两种加工工艺可以同时应用来加工一个工件,例如,加工模具时可采用高效加工进行粗铣(以达到高的材料切除率),而在精铣时则采用高速加工(以获得较好的表面质量和高的加工精度)。
目前,无论是流行的高速加工还是刚兴起的高效加工,都应归根于刀具技术不断发展的推动,尤其是在刀具材料、刀刃几何形状和涂层方面的不断发展和优化组合,实现不断开发多种不同结构的高效刀具提供了基础。生产实践表明,为显著缩短加工时间、提高生产效率和降低零件的制造成本,关键在于采用高速加工和高效加工新工艺。
声明:本网站所收集的部分公开资料来源于互联网,转载的目的在于传递更多信息及用于网络分享,并不代表本站赞同其观点和对其真实性负责,也不构成任何其他建议。本站部分作品是由网友自主投稿和发布、编辑整理上传,对此类作品本站仅提供交流平台,不为其版权负责。如果您发现网站上所用视频、图片、文字如涉及作品版权问题,请第一时间告知,我们将根据您提供的证明材料确认版权并按国家标准支付稿酬或立即删除内容,以保证您的权益!联系电话:010-58612588 或 Email:editor@mmsonline.com.cn。
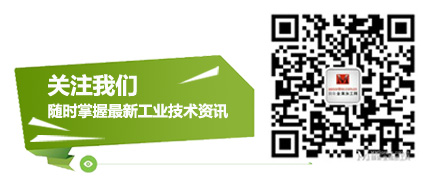
- 暂无反馈