车铣复合加工的关键技术与应用前景
加工效率与精度是金属加工领域追求的永恒目标。随着数控技术、计算机技术、机床技术以及加工工艺技术的不断发展,传统的加工理念已不能满足人们对加工速度、效率和精度的要求。在这样的背景下,复合加工技术应运而生。一般来说,复合加工是指在一台加工设备上能够完成不同工序或者不同工艺方法的加工技术的总称。目前的复合加工技术主要表现为2 种不同的类型,一种是以能量或运动方式为基础的不同加工方法的复合;另一种是以工序集中原则为基础的、以机械加工工艺为主的复合,车铣复合加工是近年来该领域发展最为迅速的加工方式之一。
目前的航空产品零件突出表现为多品种小批量、工艺过程复杂,并且广泛采用整体薄壁结构和难加工材料,因此制造过程中普遍存在制造周期长、材料切除量大、加工效率低以及加工变形严重等瓶颈。为了提高航空复杂产品的加工效率和加工精度,工艺人员一直在寻求更为高效精密的加工工艺方法。车铣复合加工设备的出现为提高航空零件的加工精度和效率提供了一种有效解决方案。
与常规数控加工工艺相比,复合加工具有的突出优势主要表现在以下几个方面。
(1)缩短产品制造工艺链,提高生产效率。
车铣复合加工可以实现一次装卡完成全部或者大部分加工工序,从而大大缩短产品制造工艺链。这样一方面减少了由于装卡改变导致的生产辅助时间,同时也减少了工装卡具制造周期和等待时间,能够显著提高生产效率。
(2)减少装夹次数,提高加工精度。
装卡次数的减少避免了由于定位基准转化而导致的误差积累。同时,目前的车铣复合加工设备大都具有在线检测的功能,可以实现制造过程关键数据的在位检测和精度控制,从而提高产品的加工精度。
(3)减少占地面积,降低生产成本。
虽然车铣复合加工设备的单台价格比较高,但由于制造工艺链的缩短和产品所需设备的减少,以及工装夹具数量、车间占地面积和设备维护费用的减少,能够有效降低总体固定资产的投资、生产运作和管理的成本。
复合加工的关键技术
尽管复合加工具有常规单一加工无法比拟的优势,但实际上目前在航空制造领域里车铣复合加工的利用率并未得到充分发挥。其关键原因在于车铣复合加工在航空制造领域的应用时间还比较短,适用于航空零件结构工艺特性的车铣复合加工工艺、数控编程技术、后置处理以及仿真技术尚处于摸索阶段。为了充分发挥车铣复合加工设备的效能,提高产品的加工效率和精度,必须全面攻克和解决上述关键基础,并实现集成化应用。
1 车铣复合加工的工艺技术
与常规加工设备不同的是,一台车铣复合加工中心实际上相当于一条生产线。如何根据零件工艺特性和车铣复合加工的工艺特点制定合理的工艺路线、装卡方法和选用合理的刀具是实现高效精密加工的关键。
工序集中是复合加工最为鲜明的工艺特点。因此,科学合理的工艺路线是提高车铣复合加工效率和精度的关键因素。瑞士宝美公司的S192F 铣车复合加工中心为例,该机床具有五轴铣、车削、镗削、钻孔、锯断以及自动进料等功能,采用FANUC 31i 数控系统,具有刀矢平滑、超强前瞻、高速插补等功能,特别适合轴类、回转类等零件的高速精密加工。在航空叶轮加工中,该加工中心具有突出的优势。当采用棒料作为叶轮毛坯时,常规的叶轮加工工艺路线首先利用数控车床车削叶轮外部轮廓,然后精车加工基准;在此基础上利用五轴数控加工中心进行开槽、粗加工、半精加工以及型面和轮毂的精加工;最后在五轴加工中心或钻孔设备上进行孔加工。而采用S192F 铣车加工中心不仅可以通过一次装卡完成上述工艺的全部加工,而且当采用棒料进行加工时还可以通过锯断、自动送料等功能实现叶轮的批量加工,整个过程无需人工干预可以全部自动完成。其工艺路线的设置可采用如下方式:主轴装卡棒料→粗车叶轮外部轮廓→精车外部轮廓→五轴铣削开槽→流道粗加工→流道半精加工→流道精加工→钻孔→背主轴装卡→车削叶轮底部平面→钻孔。可以看出,一次装卡即完成全部叶轮加工工序,加工效率及精度可以得到大幅提高。
对于具有双刀架的车铣加工中心,双刀塔的设备都具有双通道的控制系统,上下刀架可单独控制,同步加工可以通过代码中的同步语句来实现。为充分发挥设备的加工能力,可以在加工条件允许的前提下,通过双刀架的同步操作实现零件的多个工序同时加工。可以通过上下刀架的同步设置,在粗车外形的同时完成内孔的粗镗加工,从而进一步提高加工效率。通过上下刀架的同步运动,完成一系列孔的加工,不仅提高了加工的效率,同时还可以通过钻孔轴向力的相互抵消来减少工件变形的影响。为实现这种功能,需要在前期工艺设计的时候对工艺方案进行系统深入的研究,确定工艺路线的串行和并行顺序,并通过对加工程序的合理组合实现上述功能。
2 车铣复合加工的数控编程技术
车铣复合加工技术的发展,也对数控编程技术提出了更高的要求,这也是制约车铣复合加工设备在实际生产应用中的一个瓶颈环节。由于车铣复合加工投入实际生产的应用时间较短,在没有专业的复合加工解决方案的情况下,通常是利用通用CAM 软件规划出部分加工程序,然后工艺人员再对程序进行手工整合,以满足复合加工机床对加工程序的要求。这种解决方法对工艺人员的要求非常高。与传统的数控编程技术相比,车铣复合加工的程序编制难点主要体现在以下几个方面。
(1)工艺种类繁杂。对于工艺人员来说,不仅要能掌握数控车削、多轴铣削、钻孔等多种加工方式的编程方法,而且对于工序间的衔接与进退刀方式需要准确界定。因此在进行数控编程时,需要对当前工序加工完成后的工序模型和加工余量的分布有直观的认识,以便于下一道工序的程序编制和进退刀的设置。
(2)程序编制过程中的串并行顺序的确定必须严格按照工艺路线确定。许多零件在车铣复合加工中心上加工时可实现从毛料到成品的完整加工,因此加工程序的编制结果必须同工艺路线保持一致。同时,对于多通道并行加工也需要在数控加工程序编制的过程中进行综合考虑。可见,为实现高效的复合加工应该发展工艺- 编程- 仿真一体化的工艺解决方案。
(3)对于车铣复合加工的某些功能,目前的通用CAM 软件尚不支持。与常规单台设备加工相比,车铣复合加工具备的机床运动和加工功能要复杂的多,目前的通用CAM 软件尚不足以完全支持这些先进功能的程序编制,如在线测量、锯断、自动送料、尾座控制等。因此,利用通用CAM 软件编制出来的程序仍然需要大量的手工或交互的方式才能应用于自动化的车铣复合加工。
(4)加工程序的整合。目前通用CAM 软件编制完成后的NC 程序之间是相互独立的,要实现车铣复合这样复杂的自动化完整加工,需要对这些独立的加工程序进行集成和整合。这种整合必须以零件的工艺路线为指导,首先确定出哪些程序是并行的,然后对不同工艺方法的加工顺序进行确定,并给出准确的换刀、装卡更换、基准转化以及进退刀指令等。
可以看出,车铣复合加工数控程序编制难度非常大,而目前的通用CAM 软件用于车铣复合加工仍然存在很多缺陷和不足。为弥补这些不足,在现有通用CAD/CAM 软件的基础上开发适用于产品工艺和复合加工设备的专用编程系统是一种更为现实的解决方案。这一方面降低了软件购置的重复投资,同时也能避免由于编程平台不统一而造成的工艺知识不能重用、人员配置复杂等缺陷。
3 车铣复合加工的后置处理技术
与数控编程技术相对应,车铣复合加工由于工艺方法复杂、运动部件多等原因,从而对目前的后置处理软件及技术提出了更高的要求。与常规数控设备相比,其后置处理的难点主要体现在以下几个方面。
(1)不同工序间的衔接运动要求严格准确。由于在车铣复合设备上进行的加工工艺种类繁多,因此在当前工序加工完成之后必须及时、准确地完成加工方式、刀具、运动部件的自动切换,以保证加工过程的正确和安全。为了达到这个目的,一方面要求设置合理的进退刀方式以及自动换刀、冷却液开和停的时机,另外更为重要的是在进行当前工序加工时需要设定其他非运动部件所处的位置。这样才能避免机床在换刀和加工过程中运动部件与非运动部件之间的碰撞,确保加工过程安全稳定。
(2)需要对工艺顺序和数控程序进行自动判定。由于复合加工中工艺路线相对较长,依靠人工去对后置完成后的NC 代码进行组织和集成不仅效率低而且也容易导致错误的发生。理想的解决方法是在后置处理过程中能够对加工顺序和刀位文件中蕴含的工艺方法进行自动判定,并能在后置处理完成后的NC 代码中自动保持。为此,数控编程完成后的刀位文件信息中不仅需要包含相应的工艺方法、刀位信息,还需要包含对应的加工顺序、所采用的刀具种类和编号,这样才能在后置处理的过程中达到工艺顺序、工艺方法和刀具的自动判定。
(3)不同加工方式的后置处理技术。车铣复合加工的后置处理程序不仅要求能够实现多轴数控铣削、车削、钻削加工的后置处理,还要能够实现锯断、自动进料、尾座控制以及程序循环调用等功能,车铣复合加工的后置处理算法基本上囊括了现有数控加工所有工艺种类的后置处理方法,并且还要能够实现不同加工方式之间的无缝集成和运动衔接。
(4)控制系统先进功能的充分利用。目前用于车铣复合加工中心的数控系统都是非常先进的控制系统,如宝美S192FT 采用的FANUC 31i系统、WFL 150 采用的SINUMERIK840D 系统。这些先进的控制系统大都具备进给自动优化、刀矢平滑、超强前瞻以及高速、高精度插补等先进功能。因此,必须要将这些先进数控系统的功能反映在后置处理阶段完成的加工代码中的合适位置,才能实现车铣复合加工设备效能的充分利用。
(5)非切削功能的处理和调用。复合加工机床除了具备车、铣、钻、镗等切削功能外,还具备在各工序之间过渡所需的非切削功能,如自动送料、卸料、主轴对接、尾座控制等。在后置处理中需要将这些功能作为一个公用模块供程序调用,调用的顺序和时机需要根据工艺路线来确定。这些功能目前的后置处理软件尚不能提供。
4 车铣复合加工的仿真技术
车铣复合加工由于运动部件多、功能复杂,程序编制完成后的加工仿真就显得尤为重要。由于我国航空制造厂车铣复合加工投入实际生产的时间较短,目前还没有成熟的仿真应用技术,因此大部分厂家是通过试切加工来验证和优化程序,这就导致工艺准备周期长、研制风险和加工成本高。
为了提高车铣复合加工的应用水平和编程效率,必须大力推动仿真技术的应用。目前用于车铣复合加工仿真的软件主要有TopSolid、Gibbs 等,但这些软件普遍价格昂贵,我国航空制造领域引进较少。实际上,实现车铣复合加工的仿真也可借助目前的通用数控加工仿真软件(如Vericut、NCSimul 等),根据车铣复合加工设备的结构、运动特点、特殊功能及数控系统,通过定制及宏功能开发实现加工过程的运动仿真。
利用通用的数控加工仿真软件实现车铣复合加工的仿真需要首先在仿真系统里构建相对真实的机床环境,重点在于机床各运动部件之间的相对运动关系和几何位置关系的建立。在此基础上,建立加工过程中所采用的刀具库及相应的刀具编号。然后配置机床设备的数控系统和数控程序的加工基准,并将后置完成的NC 代码载入仿真系统中,即可执行加工过程的仿真工作。与常规数控加工不同的是,有些功能(如多通道加工、尾座控制等)还需要通过宏功能的开发和定制来完成。
车铣复合加工技术的应用前景及发展建议
近年来,车铣复合加工中心在我国飞机、航空发动机以及附件厂等航空制造厂家都有引进。设备类型主要集中于奥地利WFL 公司的车铣复合系列产品和瑞士宝美公司铣车复合加工中心等。但由于投入实际应用的时间不长,普遍缺乏与产品工艺特点和设备工艺特性相适应的成熟的加工工艺、编程手段和后置处理等技术手段。因此,目前引进的车铣复合加工设备基本上处于相对较低的运行水平。
航空产品制造过程中面临的主要问题突出表现为工艺路线长、工艺过程复杂、加工效率低、加工变形严重、加工成本高,车铣复合加工无论是在飞机制造还是在发动机制造领域都有着极为广阔的发展空间。
如飞机机身整体框的铣削加工通常要经过下料/ 毛坯制备、基准加工、粗加工内形、粗加工外形、精修基准、半精及精加工内形、半精和精加工外形、孔加工、钳工修整、检测等数十个工序、多次翻转装夹才能完成。而目前航空发动机领域的整体叶盘加工也是采用整体锻造毛坯,经过车铣、铣削、抛光、表面处理及强化、检测探伤等几十道工序才能完成。这些零件往往制造周期长,占机时间通常达到几百小时,而且加工过程中都需要使用多台不同类型的数控机床和大量的夹具、刀具、测具等。另外,装卡的反复更换不仅造成零件制造过程中的等待时间过长,影响生产周期,而且也会造成装卡误差的积累,从而影响零件的尺寸精度和加工结果。
车铣复合加工可以通过一次装卡实现上述典型航空零件的全部或大部分工序的加工,从而为复杂航空零件的高效、精密加工提供了一种新途径。其应用优势主要体现在以下几个方面:(1)装卡次数显著减少,提高加工效率的同时消除因机床和装卡方式的改变而导致的误差。(2)工序更加集中,能够明显缩短加工工艺链,减少等待时间和机床非工作时间。(3)不改变定位状态的前提下实现车削、铣削、钻孔等多种加工方式的加工过程,减少夹具数量,保证尺寸精度的一致性。(4)目前的车铣复合加工大都具有在线测量的功能,可以利用该功能对工序过程中以及工序间的加工结果进行在位测量,实现整个加工过程的精度控制。可以看出,车铣复合加工设备具有的这些优点可以有效地弥补目前航空复杂零件制造过程中的不足,能够显著提高产品的加工精度和效率。
为了充分发挥先进的复合加工装备的加工效能,进一步提高航空产品的制造效率和质量,迫切需要开展以下几方面的工作。
(1)结合航空产品零件的工艺特点,深入研究与之相适应的复合加工工艺,包括制定工艺路线,装卡方式、刀具、冷却以及切削参数等的合理选取。
(2)根据复合加工设备的运动结构和产品的工艺特点,开发和定制相应的数控编程、后置处理、切削仿真等系统,形成工艺- 编程- 后置-仿真的一体化解决方案,降低复合加工对工艺人员的要求。
(3)形成工艺规范。结合仿真、试切以及实际生产中积累的工艺经验,形成适用于车铣复合加工的固化的工艺规范,用以指导后续其他零件的加工。
(4)注重人才的培养。复合加工设备是目前机械加工领域的前沿技术的代表,无论是工艺编制还是操作维护都要比常规设备复杂,高水平的研发队伍是实现设备健康、高效运行的关键。
结束语
目前的复合加工装备正朝着更大工艺范围、更高效率、大型化以及模块化的方向发展。航空产品制造领域一直是先进制造技术发挥作用的重要舞台,随着航空产品更新换代速度的日益加快,工序分散的加工设备将逐渐被工序集中的柔性自动化装备所取代,这为复合加工技术提供了更为广阔的发展和应用空间。
声明:本网站所收集的部分公开资料来源于互联网,转载的目的在于传递更多信息及用于网络分享,并不代表本站赞同其观点和对其真实性负责,也不构成任何其他建议。本站部分作品是由网友自主投稿和发布、编辑整理上传,对此类作品本站仅提供交流平台,不为其版权负责。如果您发现网站上所用视频、图片、文字如涉及作品版权问题,请第一时间告知,我们将根据您提供的证明材料确认版权并按国家标准支付稿酬或立即删除内容,以保证您的权益!联系电话:010-58612588 或 Email:editor@mmsonline.com.cn。
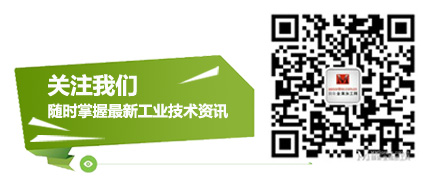
- 暂无反馈