改善线切割加工表面粗糙度的措施
电火花线切割加工表面粗糙度超值的主要原因是加工过程不稳定及工作液不干净,现提出以下改善措施。
(1)保证贮丝筒和导轮的制造和安装精度,控制贮丝筒和导轮的轴向及径向跳动,导轮转动要灵活,防止导轮跳动和摆动,有利于减少钼丝的振动,促进加工过程的稳定。
(2)必要时可适当降低钼丝的走丝速度,增加钼丝正反换向及走丝时的平稳性。
(3)根据线切割工作的特点,钼丝的高速运动需要频繁地换向来进行加工,钼丝在换向的瞬间会造成其松紧不一,钼丝张力不均匀,从而引起钼丝振动,直接影响加工表面粗糙度,所以应尽量减少钼丝运动的换向次数。试验证明,在加工条件不变的情况下,加大钼丝的有效工作长度,可减少钼丝的换向次数,减少钼丝的抖动,促进加工过程的稳定,提高加工表面质量。
(4)采用专用机构张紧的方式将钼丝缠绕在贮丝筒上,可确保钼丝排列松紧均匀。尽量不采用手工张紧方式缠绕,因为手工缠绕很难保证钼丝在贮丝筒上排列均匀及松紧一致。松紧不均匀,钼丝各段的张力不一样,就会引起钼丝在工作中抖动,从而增大加工表面粗糙度。
(5)X向、Y向工作台运动的平稳性和进给的均匀性也会影响加工表面粗糙度。保证X向、Y向工作台运动平稳的方法:先试切,在钼丝换向及走丝过程中变频均匀,且单独走X向、Y向直线,步进电机在钼丝正反向所走的步数应大致相等,说明变频调整合适,钼丝松紧一致,可确保工作台运动的平稳。
(6)对于有可调线架的机床,应把线架跨距尽可能调小。跨距过大,钼丝会振动,跨距过小,不利于冷却液进入加工区。如切割厚40mm的工件,线架跨距在50~60mm之间,上下线架的冷却液喷嘴离工件表面6~10mm,这样可提高钼丝在加工区的刚性,避免钼丝振动,利于加工稳定。
(7)工件的进给速度要适当。因为在线切割过程中,如工件的进给速度过大,则被腐蚀的金属微粒不易全部排出,易引起钼丝短路,加剧加工过程的不稳定;如工件的进给速度过小,则生产效率低。
(8)脉冲电源同样是影响加工表面粗糙度的重要因素。脉冲电源采用矩形波脉冲,因为它的脉冲宽度和脉冲间隔均连续可调,不易受各种因素干扰。减少单个脉冲能量,可改善表面粗糙度。影响单个脉冲能量的因素有脉冲宽度、功放管个数、功放管峰值电流。所以减小脉冲宽度、减小峰值电流,可改善加工表面粗糙度。然而,减小脉冲宽度,生产效率大幅度下降,不可用;减小功放管峰值电流,生产效率也会下降,但影响程度比减小脉冲宽度小。因此,笔者认为减小功放管峰值电流,适当增大脉冲宽度,调节合适的脉冲间隔,这样既可提高生产效率,又可获得较低的加工表面粗糙度。
(9)保持稳定的电源电压。因为电源电压不稳定,会造成钼丝与工件两端的电压不稳定,从而引起击穿放电过程不稳定,增加表面粗糙度。
(10)线切割工作液要保持清洁。工作液使用时间过长,会使其中的金属微粒逐渐变大,使工作液的性质发生变化,降低工作液的作用,还会堵塞冷却系统,所以必须对工作液进行过滤,使用时间长,要更换工作液。最简单的过滤方法是,在冷却泵体抽水孔处放一块海绵。工作液最好是按螺旋状形式包裹住钼丝,以提高工作液对钼丝振动的吸收作用,减少钼丝的振动,改善表面粗糙度。
总之,只要消除了加工过程的不稳定及保持工作液清洁,就能在较高生产效率下,获得较好的加工表面粗糙度。
声明:本网站所收集的部分公开资料来源于互联网,转载的目的在于传递更多信息及用于网络分享,并不代表本站赞同其观点和对其真实性负责,也不构成任何其他建议。本站部分作品是由网友自主投稿和发布、编辑整理上传,对此类作品本站仅提供交流平台,不为其版权负责。如果您发现网站上所用视频、图片、文字如涉及作品版权问题,请第一时间告知,我们将根据您提供的证明材料确认版权并按国家标准支付稿酬或立即删除内容,以保证您的权益!联系电话:010-58612588 或 Email:editor@mmsonline.com.cn。
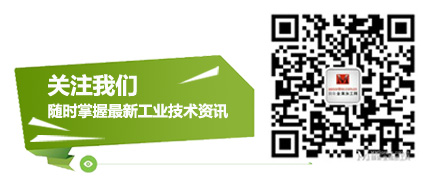
- 暂无反馈