高速干切削的技术及发展趋势
高速干切削技术是在高速加工和干切削技术的基础上发展起来的一项先进制造技术,是绿色制造在金属切削领域的具体实施。高速干切削加工所要求的刀具、机床和辅助工艺具有一定的特殊性,是影响高速干切削技术能否得到广泛应用的三个重要方面。 高速切削(HSC)加工作为一种先进的切削技术,自二十世纪八十年代以来得到了日益广泛的应用。高速加工采用远高于常规加工的切削速度和进给速度,不仅可提高加工效率,缩短加工工时,同时还可获得很高的加工精度。随着高速主轴技术的发展,与其配套的新型刀具不断出现,同时对高速加工工艺参数的优化研究也在不断深人,使得高速切削技术的理论研究和应用都得到了长足的发展。
高速加工的主要优点有:1、切削力降低03%左右,特别适合刚性差的零件,2、由于加工时对刀具和工件进行了冷却润滑,减少了切削热对工件的影响,特别适合加工易热变形的工件;3、激振频率远远高于机床和工艺系统的固有频率,加工平稳,振动小,加工表面质量好4;、能极大地提高生产效率。但是,高速切削采用的高压大流量冷却方式会增加环境污染、提高生产成本、减少刀具的耐用度、加大机床腐蚀等一系列问题。
为了解决上述问题,目前采用的方法一种是改变切削液的使用参数和用量,研制新型的无污染的绿色切削液;另一种是在切削过程中停止使用切削液,采用干切削,它能从根本上彻底解决切削液带来的问题。干切削技术是上世纪九十年代为适应全球日益高涨的环保要求和可持续发展战略而发展起来的一项绿色切削加工技术,目前欧美、日本等工业发达国家非常重视干切削的研究,干切削技术已经成功应用到了生产领域,并且取得了良好的经济效益。
高速切削因具有降低切削力,工件热变形小等特点,为实现干切削提供了有利条件,高速干切削的目标不仅要限制或停止使用切削液,而且要保证高的加工效率和加工质量。但在高速干切削中,因缺乏切削液的冷却润滑和排屑作用,会导致切削区刀具与工件的摩擦加剧,切削力增大,切削温度上升,切削振动增强以及排屑不畅等情况,会影响机床加工性能和刀具使用寿命,降低加工质量。因此,需要从刀具、机床和辅助工艺等方面来进行研究并优化,使高速干切削技术能得到更广泛的应用。
1 高速干切削的刀具技术
高速干切削的刀具要承受比湿切削更高的温度,刀具与切屑和刀具与工件接触面上的摩擦系数也要尽可能的小,而且还要求刀具有利于断屑、排屑和散热,这就需要从刀具材料、刀具涂层以及刀具结构的优化等几个方面来解决。
1.1刀具材料
刀具材料的迅速发展是高速干切削得以实施的工艺基础。高速干切削时要求刀具材料与被加工材料的化学亲和力要小,必须具有良好的耐热性,极高的红硬性和热韧性。目前适用于干式加工的刀具材料有超细高的切削温度,具有较高的强度和冲击韧度,适用于制作干切削的钻头和铣刀。PCD(聚晶金刚石)和CVD金刚石涂层刀片有很高的硬度和热导率,适合高速干切削有色金属(如铜合金,铝合金)以及钦合金和耐磨的高性能复合材料,但不能加工黑色金属。CBN(立方氮化硼)的硬度和耐磨性仅次于金刚石,有优良的红硬性、化学稳定性和低摩擦系数,是高速干切削HRC50以上淬硬钢和冷硬铸铁等黑色金属的理想刀具材料。
金属陶瓷的硬度和冲击性好,热硬性差,故多用于精加工和半精加工。陶瓷具有硬度高、化学稳定性和抗粘结性好、摩擦系数低等优点,是相对廉价的干切削刀具材料,但其强度、韧性和抗冲击性能差,适用于灰铸铁和钢的高速干切削。
1.2刀具结构的优化
干切削刀具的失效形式主要是月牙洼磨损,所以一般都采用较大的前角以减少切屑与前刀面的接触面积。为弥补大前角对刃口强度的削弱,常配以加强刃甚至前刀面上带有加强筋。较大的正前角、锋利而强有力的切削刃有利于断屑。总之,干切削刀具的结构设计必须考虑断屑和排屑的问题。对韧性材料的加工来说,断屑非常关键,目前车刀三维曲面断屑槽方面的设计制造技术已经比较成熟,可针对不同的工件材料和切削用量很快设计出相应的断屑槽结构与尺寸,并能大大提高切屑折断能力和对切屑流动方向的控制能力。
此外,为了加速刀具的冷却以降低切削温度,也可采用热管式刀具或液氮冷却刀具。用液氮冷却刀具的方法,在车刀的前刀面倒装了一个金属帽状物,其内腔与刀片的表面共同组成一个封闭的空间。帽状物上有液氮的人口和出口。在干切削过程中,液氮在封闭的空间内不断地流动,吸收刀片上的切削热,使刀具不产生过高的温升,始终保持良好的切削性能,顺利实现干切削。
1.3刀具涂层
采用高速干切削,若仅仅使用目前已有的热稳定性好的刀具材料和优化刀具几何形状,仍不能达到很好的效果。因此,采用在刀面上涂覆隔热性好的硬涂层和具有固体润滑性能的软涂层,使刀具能承受更高的切削温度。涂层的作用一是提供了低摩擦层,减少了刀具与工件表面之间的摩擦和粘结,相当于切削液的润滑作用;二是在刀具和切削之间起到隔热作用,阻止切削热向刀具传播,相当于切削液的冷却作用。
涂层材料可分为软涂层和硬涂层。基于MoS2和WC/C的软涂层主要用于对涂层的滑动性能要求非常高的场合。硬涂层主要有TiN、TiCN、TiALN等,TiALN具有很好的耐热性和耐高温性,硬度高达HV3500,工作温度高达79℃,而且因为添加了AL,使刀具的抗氧化性能大大提高,是高速加工和干切削最常用的材料。ITN在干切削时可作为一种"通用涂层",主要用于干攻丝(铸铁丝锥除外),TiN涂层用在整体硬质合金铣刀上效果很好。
在高速干切削刀具中常常使用多层复合涂层,把硬涂层和软涂层结合在一起,即在一道涂覆工序中采用两种物理气相沉积工艺,先产生硬涂层TiALN,然后再在其上面采用溅射法产生WC/C软涂层,可以有效提高刀具的寿命。目前新的涂层技术如高硬度、高热稳定性的金刚石薄膜涂层,CBN薄膜涂层,由多种涂层材料不同组合构成的纳米级涂层等,均得到了长足的发展,其所具有的优异抗磨损及自润滑性能,使其更能适用于多种材料的高速干切削。
2 高速干切削的机床技术
由于高速干式切削加工机床不再使用切削液,必然导致其整体结构及布局的变化,主要体现在对机床的隔热性能、排屑速度、洗尘效果和机床基础构件的三刚度(静刚度、动刚度和热刚度)等方面提出了更高要求。
2.1高速干切削抓床的机构
2.1.1选用三刚度高的高速机床
由于高速干式切削加工过程中会产生更大的切削力和更多的切削热,从而导致刀具与工件之间的振动以及机床的热变形明显增大,因此选用的机床基础构件(如立柱、床身、工作台等)的三刚度要大,如采用人造花岗岩等新材料整体制造床身,不仅三刚度好,而且减振效果明显。此外,将被认为是"21世纪的新式数控机床"、"机床结构的重大技术革命"的虚拟轴机床与高速干式切削加工技术结合起来,将会获得更好的效果。
2.1.2采用快速排屑布局
应用高速干式切削加工的要点之一是要在切屑中的大部分热量传人机床之前迅速将其排出。为此,可采取以下排屑方法:①高速干式切削加工机床应尽可能采用立式主轴和倾斜式床身,工作台四周应采用倾斜的隔板,这样有助于热切屑迅速坠人排屑槽中。②借助重力排屑。以钻削加工为例,可改变机床常规布局,将工件安装在主轴下部,刀具从下向上钻削,在重力作用下,切屑可从孔中顺利排出,而无须使用带压力的切削液来辅助排屑。③利用虹吸现象排屑。在钻削加工中,可利用干燥的空气通过虹吸作用吸出孔中的切屑,而无须使用切削液。④利用真空或喷气系统改善排屑条件。如日本某公司开发的"洁净回收系统",采用将刀具部分罩住的结构,利用从内部吹出的压缩空气,使切屑顺着刀具回转方向经螺旋管道排出。
2.1.3采用热稳定性好的结构和适当的隔热措施
机床床身采用热稳定性好的结构和材料,可将切削热的影响降到最低程度。如采用均衡温度的结构,将床身的左右两侧、顶部和底部设计成四个相通的型腔并注人油液,即可保证整个床身具有相同的温度。此外,机床立柱与底座等基础构件采用对称结构并选用热容量小的材料,主轴采用恒温水冷装置等,都能提高机床的热稳定性。
采取适当的隔热措施,如排屑槽用绝热材料制造,高速切削区采用绝热罩来隔断热切屑等,均可减少排屑过程中切屑传递给机床的热量。
2.2高速干切削机床的主轴
主轴应具有较高的转速和较高的刚度,特别是动刚度,以适应干切削过程中切削力增大、切削振动增强的影响,因此,通过动态优化的高速大功率的电主轴技术能有效适合高速干切削的要求,它采用内藏式无外壳伺服电机直接驱动方式,消除了中间传动链的影响,可以获得较高的主轴转速,而且还可以提高主轴的刚度和频率响应,抑制或降低主轴单元在干切削过程中的切削振动,同时采用陶瓷轴承以及先进的润滑技术,降低主轴在加工过程中的热影响。主轴的密封技术也是实现高速干切削的重要因素。目前,在高速主轴设计中,采用动态优化的电主轴结构,并结合通过热平衡设计,循环内冷却技术和轴承的油气润滑技术,提高主轴单元的动刚度和热稳定性。在防尘方面,采用迷宫式非接触结构,并结合油气润滑中高压气体(0.4MPa),能有效防止加工中悬浮颗粒的侵人。
2.3高速干切削机床的进给单元
进给单元应具有较高的刚度和较大的推力,很高的进给速度和良好的加减速特性。目前主要有"伺服电机+大导程的高速滚珠丝杠副"和"直流直线电机直接驱动"。精密高速滚珠丝杠副最大的进给速度可达到50~80m/min,进给加速度可达0.5~1.5g;直线电动机直接驱动的进给单元的最大进给速度可达到100~200min,进给加速度可达3~10g。两种进给系统均能满足高速干切削加工的要求,其中直线电动机进给单元的加减速能力较强,是高速干切削加工的理想进给方式,但直线电动机在使用中存在承载力小、易发热等问题,有待改进。
3 高速干切削的工艺技术
由于在高速切削条件下,59%~98%的切削热将被切屑带走,切削力也可降低30%,因此,采用很高的切削速度进行加工可以取得与使用切削液相同的效果。日本牧野公司提出"红月牙"干切削工艺技术,其机理是由于切削速度很高,产生的热量聚集于刀具前部,使切削区附近工件材料达到红热状态,导致屈服强度明显下降,从而提高材料去除率。
在一些机械加工中,纯粹的干切削是难以实现的。可以采用最小量润滑(MQL)技术(又称准干切削)。这种方法是将压缩的空气与少量的润滑液混合气化后,喷射到加工区,对刀具和工件之间的加工部位进行有效的润滑。MQL技术可以大大减少"刀具-工件"和"刀具-切屑"之间的摩擦,起到抑制温升、降低刀具磨损、防止粘连和提高工件加工质量的作用,使用的润滑液也很少,效果却十分明显。MQL技术使用对人健康无害的植物油或脂油,其用量极少,一般为0.03-0.2L/h,而1台典型的加工中心在进行湿切削时,切削液的用量高达20-100L/h,为MQL润滑油用量的6万倍左右。MQL润滑的准干切削效果相当好,现已十分流行。此外,还可在某些特殊气体(如液氮)氛围中进行干切削加工和低温冷风干切削加工。
4 结束语
高速干切削加工从根本上解决了切削液带来的弊端,不仅有利于工人的健康和环境的保护,而且可以降低加工成本,无疑是一种很有发展前途的绿色加工工艺。
声明:本网站所收集的部分公开资料来源于互联网,转载的目的在于传递更多信息及用于网络分享,并不代表本站赞同其观点和对其真实性负责,也不构成任何其他建议。本站部分作品是由网友自主投稿和发布、编辑整理上传,对此类作品本站仅提供交流平台,不为其版权负责。如果您发现网站上所用视频、图片、文字如涉及作品版权问题,请第一时间告知,我们将根据您提供的证明材料确认版权并按国家标准支付稿酬或立即删除内容,以保证您的权益!联系电话:010-58612588 或 Email:editor@mmsonline.com.cn。
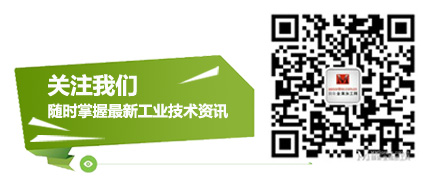
- 暂无反馈