中国模具行业“十一五”发展重点
在国民经济快速发展的拉动和国家产业政策的正确引导下,“十五”期间中国模具工业发展迅速,产需两旺,渐入佳境。与此同时,行业综合水平落后的面貌未得到根本性的改变,一些深层次的问题尚待解决。现在,中国可以说是世界模具生产大国之一,但还远远不是生产强国。“十一五”期间,应该向生产强国这目标迈进。
行业存在的主要问题
中国模具生产总量虽然已位居世界第三,但设计制造水平在总体上要比德、美、日、法、意等工业发达国家落后许多,也比英国、加拿大、西班牙、葡萄牙、韩国、新加坡等国落后。其差距主要表现在下列六方面。
1. 国内自配率不足80%,其中中低档模具供过于求,中高档模具自配率不足60%。
2. 企业组织结构、产品结构、技术结构和进出口结构都不够合理。中国模具生产厂中多数是自产自配的工模具车间(分厂),专业模具厂也大多数是“大而全”、“小而全”的组织形式。国外模具企业大多是“小而专”、“小而精”。中国模具自产自配比例高达50%以上,国外70%以上是商品模具。国内模具总量中属大型、精密、复杂、长寿命模具的比例只有30%左右,国外在50%以上。2003年模具进出口之比为4:1,进出口相抵后的净进口为10.3亿美元,是净进口量最大的国家。
3. 模具产品水平和生产工艺水平总体上比国际先进水平低许多,而模具生产周期却要比国际先进水平长许多。产品水平低主要表现在精度、型腔表面粗糙度、寿命及模具的复杂程度上;工艺水平低主要表现在设计、加工、工艺装备等方面。
4. 开发能力弱,经济效益欠佳。中国模具企业技术人员比例较低,水平也较低,不重视产品开发,在市场中常处于被动地位。国内每个职工平均每年创造模具产值约合1万美元左右,而模具工业发达国家大多是15~20万美元,有的甚至达到25~30万美元。由此而来的是中国模具企业经济效益差,大都微利,国有企业总体亏损,缺乏后劲。
5. 模具标准化水平和模具标准件使用覆盖率低。国外先进国家模具标准件使用覆盖率达70%以上,国内模具标准件使用覆盖率只有45%左右。
6. 与国际先进水平相比,模具企业的管理落后更甚于技术。管理落后易被忽视,国内大多数模具企业还沿用过去作坊式粗放经营管理模式,真正实现现代化企业管理的还不多。
造成上述差距的原因很多,除了长期以来未将模具作为产品得到应有的重视之外,还有下列几个主要原因:
第一,体制不顺,基础薄弱。
“三资”企业虽然已经对中国模具工业的发展起了积极的推动作用,私营企业近年来发展较快,国企改革也在进行之中,但总体来看,体制和机制尚不适应市场经济,再加上国内模具工业基础薄弱,因此,行业发展还不尽如人意,特别是总体水平和高新技术方面。
第二,人才严重不足,科研开发及技术攻关方面投入太少。
模具行业是技术密集、资金密集的产业,随着时代进步和技术发展,能掌握和运用新技术的人才异常短缺,高级模具钳工及企业管理人才也非常紧缺。由于模具企业效益欠佳及对科研开发和技术攻关不够重视,因而总体来看模具行业在科研开发和技术攻关方面投入太少,民营企业贷款困难也影响许多企业的技术改造,致使科技进步不大。
第三,工艺装备水平低,且配套性不好,利用率低。
虽然国内许多企业采用了先进的加工设备,但总的来看装备水平仍比国外企业落后许多,特别是设备数控化率和CAD/CAM应用覆盖率要比国外企业低得多。由于体制和资金等原因,引进设备不配套,设备与附配件不配套现象十分普遍,设备利用率低的问题长期得不到较好解决。装备水平低,带来中国模具企业钳工比例过高等问题。
第四,专业化、标准化、商品化的程度低、协作差。
由于长期以来受“大而全”“小而全”影响,许多模具企业观念落后,模具企业专业化生产水平低,专业化分工不细,商品化程度也低。目前国内每年生产的模具,商品模具只占45%左右,其馀为自产自用。模具企业之间协作不好,难以完成较大规模的模具成套任务,与国际水平相比要落后许多。模具标准化水平低,标准件使用覆盖率低也对模具质量、成本有较大影响,对模具制造周期影响尤甚。
第五,模具材料及模具相关技术落后。
模具材料性能、质量和品种往往会影响模具质量、寿命及成本,国产模具钢与国外进口钢相比,无论是质量还是品种规格,都有较大差距。塑料、板材、设备等性能差,也直接影响模具水平的提高。
发展战略与重点
在信息社会和经济全球化不断发展的过程中,模具行业发展趋势主要是模具产品向着更大型、更精密、更复杂及更经济快速方面发展,技术含量不断提高;模具生产向着信息化、数字化、无图化、精细化、自动化方面发展;模具企业则向着技术集成化、设备精良化、产品品牌化、经营国际化方向发展。
为此,“十一五”期间我们要积极培育模具大市场,以汽车、电子信息、家电和办公设备、机械和建材等模具主要用户行业为主要服务对象,以优质服务为宗旨,缩小与先进国家之间的差距,搞好模具工业的产品结构调整和创新,通过信息化和数字化来提升行业水平。
此外,还要加快模具企业,尤其是国有企业的体制改革和机制转换的步伐;加快模具生产标准化、专业化和商品化的发展,大力增加大型、精密、复杂等技术含量高的中高档模具的比例;加强国际交流与合作,实施“走出去”战略,鼓励出口;支持东北老工业基地和西部地区模具工业的发展;培育具有较强开发力量和水平的模具生产基地及能与世界一流企业相抗衡的大企业;努力提高企业管理水平,促进模具标准件上品种、上水平、上规模;逐步建立起适应中国国情的模具科研设计、人才培训和生产体系,不但要使中国进一步成为模具生产大国,更要逐步成为模具生产强国。
随着国民经济总量和工业产品技术的不断发展,各行各业对模具的需求量越来越大,技术要求也越来越高。虽然模具种类繁多,但其发展重点应该根据需要量大、技术含量高、代表发展方向、出口前景好的原则来选择。所选择的产品,必须是目前已有一定基础,并有条件、有可能发展起来的。对于技术发展重点,则要看国际发展趋势,以及中国具体情况,也应该是既代表发展方向,又可能发展起来的技术。
产品发展重点:
汽车覆盖件模具
冲压模具占模具总量的40%以上。汽车覆盖件模具主要为汽车配套,也包括为农用车、工程机械和农机配套的覆盖件模具,它在冲压模具中很具代表性;模具大都是大中型,结构复杂,技术要求高。尤其是为轿车配套的覆盖件模具,要求更高,它可以代表冲压模具的水平。此类模具中国已有一定技术基础,为中档轿车配套,但水平不高,能力不足,目前满足率只有一半左右。中高档轿车覆盖模具主要依靠进口,每年花费几亿美元。汽车覆盖件模具水平不高,能力不足,生产周期长已成了汽车发展的瓶颈,极影响车型开发。今后,中高档轿车所需覆盖件模具是重中之重,争取到2010年时中高档轿车及以下水平的汽车覆盖模具可以完全自配。
精密冲压模具
多工位级进模和精冲模代表了冲压模具的发展方向,其精度要求和寿命要求极高,主要为电子信息产业、汽车、仪器仪表、电机电器等配套。这两种模具,国内已有相当基础,并引进了国外技术设备,个别企业生产的产品已达到世界水平,但大部分企业仍有较大差距,总量也供不应求,进口较多。对于为超大规模集成电路配套、为引线脚100以上及间隙0.2mm以下的框架配套、为精度5µm以上的精密微型连接件配套、为Φ1.6mm以下的微型马达铁芯配套及为显像管和电子枪等配套的精密模具是发展的重中之重。为汽车覆盖件及其他大中型冲压件配套的大型多工位级进模也应重点发展。
大型及精密塑料模具
塑料模具占模具总量近40%,而这个比例仍不断上升。塑料模具中为汽车和家电配套的大型注塑模具,为集成电路配套的精密塑料模具,为电子信息产业和机械及包装配套的多层、多腔、多材质、多色精密注塑模,为新型建材及节水农业配套的塑料异型材挤出模及管路和喷头模具等,目前虽然已有相当技术基础并正在快速发展,但技术水平与国外仍有较大差距,总量也供不应求,每年进口达几亿美元,因此“十一五”期间应重点发展。
主要模具标准件
现时,国内已有较大产量的模具标准件,主要是模架、导向件、推杆推管、弹性元件等,但质量较差、品种规格较少。这些产品不但国内配套大量需要,出口前景也很好,应继续大力发展。氮气缸和热流道元件国内至今仍缺乏像样的专业厂生产,主要依靠进口,应在现有基础上提高水平,形成标准,并组织规模化生产。
其他高技术含量的模具
占模具总量近8%的压铸模具中,大型薄壁精密压铸模技术含量高、难度大。镁合金压铸模和真空压铸成形模虽然刚起步,但发展前景好,有代表性。子午线橡胶轮胎模具也是发展方向,其中活络模技术难度最大。与快速成型技术相结合的一些快速制模技术及相应的快速经济模具有理想的发展前景。这些高技术含量的模具在“十一五”期间也应重点发展。
技术发展重点
高新技术蓬勃发展的今天,为保证属高新技术产业的模具工业快速发展,模具行业中许多共性技术也必须更上一层楼,应不断开发和推广应用,并积极应用高新技术。它们主要是:
1. 开发拥有自主知识产权、适合中国国情,具有较高水平的模具设计、加工及模具企业管理的软件,不断提高软件的智能化、集成化程度。
2. 推广应用高速、高精加工技术并研制相应设备。
高速高精加工包括切削加工和电加工及复合加工等。在未来15年左右的时间里,中国机床行业应向模具行业逐步提供适合于模具高速高精加工的相应设备,如有可能,建议开发拥有自主知识产权、精度能达到0.0001mm的高精度模具制造设备。
3. 快速原型和快速经济模具制造新技术的进一步开发、提高和应用。
大力发展和推广信息化、数字化技术。例如逆向工程、并行工程、敏捷制造技术的研发及推广应用;包括大型级进模、高精密、高复杂性、高技术含量的先进模具三维设计和制造技术的研发;包括冲压工艺设计系统、模具型面设计系统、成形分析系统、模具结构设计系统、模具CAM系统和冲压专家谘询系统的车身模具数字化设计制造系统的研发;模具的集成、柔性及自动加工技术和网络及虚拟技术等。
4. 模具制造新工艺、新技术。模具制造的节能、节材技术,模具热处理、表面光整加工和表面处理新技术等。
5. 高性能模具材料的研制、系列化及其正确选用。
几项发展目标及措施建议
设想总目标为:经过“十一五”努力,使中国模具水平进入亚洲先进的行列,逐步向模具生产强国迈进。几项具体目标设想如下:
第一,全国(未包括港、澳、台)模具产值在2010年达到约1000亿元左右,其中大型、精密、复杂等技术含量高的中高档模具的比例达到40%左右。
第二,2010年出口目标设想为10亿美元左右。
第三,提高模具标准化、商品化和专业化水平,设想到2010年模具标准件使用覆盖率达到60%左右,商品模具达55%左右。
为搞好重点和实现目标,提出如下几点措施建议:
希望获得政府及有关部门在政策上的支持,包括在金融和税收、进出口和科研开发等方面的支持。
加快体制改革步伐,增强企业的核心竞争力,继续努力调整结构,使之趋向合理。
积极培育“龙头”企业。除了继续走“小而精”、“小而专”的道路之外,还应将“规模效应”提到议事日程上来,如有可能,对于“龙头”项目,最好能申请国家专项支持。
视乎具体情况,积极发展具有较高水平和较大能力的模具生产集聚基地(或称模具城、模具园区)。与此同时,通过市场化管理,逐步形成地区性较为配套的模具生产产业链。
进一步搞好模具标准化工作、专业化生产及人才培圳工作。
重视管理、检测、原材料及各种配套条件,使之逐步改善。
充分发挥行业协会等社会中介组织作用。
声明:本网站所收集的部分公开资料来源于互联网,转载的目的在于传递更多信息及用于网络分享,并不代表本站赞同其观点和对其真实性负责,也不构成任何其他建议。本站部分作品是由网友自主投稿和发布、编辑整理上传,对此类作品本站仅提供交流平台,不为其版权负责。如果您发现网站上所用视频、图片、文字如涉及作品版权问题,请第一时间告知,我们将根据您提供的证明材料确认版权并按国家标准支付稿酬或立即删除内容,以保证您的权益!联系电话:010-58612588 或 Email:editor@mmsonline.com.cn。
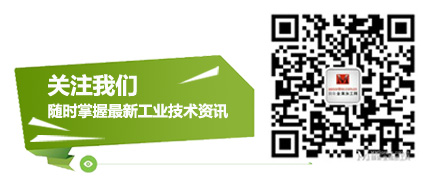
- 暂无反馈