气体辅助注塑成型的原理及优点
气体辅助注塑成型具有注射压力低、制品翘曲变形小、表面质量好以及易于加工壁厚差异较大的制品等优点,近年来发展很快。它在发达国家用于商业化的塑料制品生产差不多已有20多年。气体辅助注塑成型包括塑料熔体注射和气体(一般采用氮气)注射成型两部分。与传统的注射成型工艺相比,气体辅助注塑成型有更多的工艺参数需要确定和控制,因而对于制品设计、模具设计和成型过程的控制都有特殊的要求。
气体辅助注射成型过程首先是向模腔内进行树脂的欠料注射,然后把经过高压压缩的氮气导入熔融物料当中,气体沿着阻力最小方向流向制品的低压和高温区域。当气体在制品中流动时,它通过置换熔融物料而掏空厚壁截面。这些置换出来的物料充填制品的其余部分。当填充过程完成以后,由气体继续提供保压压力,将射出品的收缩或翘曲问题降至最低。
气体辅助注塑成型的优点
低的注射压力使残余应力降低,从而使翘曲变形降到最低;
低的注射压力使合模力要求降低,可以使用小吨位的机台;
低的残余应力同样提高了制品的尺寸公差和稳定性;
低的注射压力可以减少或消除制品飞边的出现;
成品肉厚部分是中空的,从而减少塑料,最多可达40%;
与实心制品相比成型周期缩短,还不到发泡成型的一半;
气体辅助注塑成型使结构完整性和设计自由度大幅提高;
对一些壁厚差异较大的制品通过气辅技术可以一次成型;
降低了模腔内的压力,使模具的损耗减少,提高其工作寿命;
减少射入点,气道可以取代热流道系统从而使模具成本降低;
沿筋板和凸起根部的气体通道增加了刚度,不必考虑缩痕问题;
极好的表面光洁度,不用担心会像发泡成型所带来的漩纹现象。
运用气体辅助注塑成型技术后允许设计人员将产品设计得更加复杂,而模具制造商则能够简化模具结构。制品功能不断增加和制品组件的减少使得生产周期缩短,无须进行装配和后期修整工作。在成型CD托盘和机动车电子中心压配层板的生产中表明气体辅助注塑成型能够应用于薄壁制品的生产制造。尺寸稳定性的提高,制品残余应力的减少以及翘曲量的降低是气体辅助注塑成型技术的一个主要优点。气体辅助注塑成型技术的应用将变得越来越复杂多样。现在,可用气体辅助注塑成型技术生产质量从30g~18kg的制品。
声明:本网站所收集的部分公开资料来源于互联网,转载的目的在于传递更多信息及用于网络分享,并不代表本站赞同其观点和对其真实性负责,也不构成任何其他建议。本站部分作品是由网友自主投稿和发布、编辑整理上传,对此类作品本站仅提供交流平台,不为其版权负责。如果您发现网站上所用视频、图片、文字如涉及作品版权问题,请第一时间告知,我们将根据您提供的证明材料确认版权并按国家标准支付稿酬或立即删除内容,以保证您的权益!联系电话:010-58612588 或 Email:editor@mmsonline.com.cn。
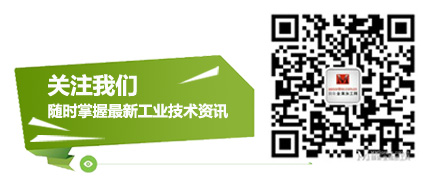
- 暂无反馈