模具企业数字制造技术的现状与发展
在现代工业生产中,60%~90%的工业产品需要使用模具,模具工业已经成为工业发展的基础。根据国际生产技术协会的预测,21世纪机械制造工业零件粗加工的75%,精加工的50%都需要通过模具来完成,其中汽车、电器、通信、石化和建筑等行业最为突出。
模具作为一种高附加值的技术密集产品,它的技术水平已经成为衡量一个国家制造业水平的重要评价指标。早在CAD/CAM技术还处于发展的初期,CAD/CAM就被模具制造业竞相吸收应用。目前国内的模具制造企业约20000家,并且以每年10%~15%的速度高速增长。在约400亿元的模具工业产值中,自产自用模具的企业约占2/3,50%~60%的企业较好地应用CAD/CAE/CAM/PDM技术。模具相关的CAD/CAE/CAM技术一直是研究开发、教育培训和推广应用的热点。
一、模具CAD/CAM系统专用化程度不断提高
随着模具工业的飞速发展以及CAD/CAM技术的重要性被模具界的广泛认可,近年来CAD/CAM开发商投入了很大的人力和物力,将通用CAD/CAM系统改造为模具行业专用的CAD/CAM系统,针对各类模具的特点,推出了宜人化、集成化和智能化的专用系统,受到了广大模具工作者的好评。例如以色列Cimatron公司推出的Quick系列产品,能在统一的系列环境下,使用统一的数据库,完成产品设计,生成三维实体模型,在此基础上进行自动分类,生成凸、凹模并完成模具的完整结构设计,能方便地对凸、凹模进行自动NC加工。又如英国DELCAM公司推出的PowerSHAPE系统,包括PSMoldmaker模块,是面向模具制造的模具总装设计专家系统,可自动为复杂注塑模、吹塑模创建模具结构及抽芯机构、自动产生分模面,加工信息被自动封装,并可直接输出到PowerMILL模块,自动产生加工程序。日本造船信息系统株式会社的三维CAD/CAM系统SpaceE中也增加了专用于注塑模的设计模块。日本UNISYS株式会社推出的专用于塑料模设计和制造系统的CADCEUS也颇具特色,该系统综合了塑料产品设计从产品形状设计、模具设计到模具生产所需要的全部功能,重点放在三维设计与二维视图的关联,体现了宜人化和集成化方面的技术进步。
二、面向模具企业的CAD/CAE/CAM技术的系统集成方案
随着模具工业的科技进步和国际竞争的日益激烈,模具业对CAD/CAM系统的要求也从单纯的建模工具变为要求支持从设计、分析、管理和加工全过程的产品信息管理集成化系统。近几年来,有不少研究单位和公司都开发了面向模具企业的CAD/CAE/CAM系统集成方案,表现出较高的实用水平。如上海交通大学国家模具工程中心在数字化制造、系统集成、反向工程、快速原型/模具以及计算机辅助应用技术等方面已形成了全方位解决方案的能力,能够提供模具开发与工程服务的业务,全面地提高模具企业的水平和产品质量。又如浙江大学旭日科技开发公司,能为企业提供产品设计、三维造型与NC编程、逆向工程、三坐标测量、模具设计与分析、技术培训以及模具CAD/CAE/CAM技术开发的全方位技术支持。北航海尔软件有限公司推出的CAXA品牌系列CAD/CAE/CAM软件也能够为用户提供有关模具工程的全方位解决方案。
值得注意的是,国际著名的CAD/CAM技术集团正在努力把数字化分析产品集成到CAD/CAM平台中。由于数字化分析产品广泛应用于航空航天、汽车、电子、医疗设备和重型机械等领域,因此仿真软件主要面向这些增长的CAE市场。根据全球领先的产品全生命周期管理(PLM)市场的资深分析公司Daratech的预测,到2007年,CAE市场的年增长率将保持在10.3%。
制造商要求通过减少物理样机,提高产品质量来降低成本并加速产品上市,这种需求在模具制造业中尤为突出。因此在设计过程中加强前期的分析仿真,将有助于缩减对物理样机的需求量,并提高数字化设计的灵活性。例如,将NXNastran集成到EDSCAE产品软件包中,将进一步加强分析驱动设计技术的重要地位,有助于用户不断开发新产品,同时降低成本,缩短将产品推向市场的时间。另一个例子是,达索集团已经将MSC公司的NastranCAE技术产品,集成到CATIA系统中,并获得了日本丰田公司的青睐。
因此,在模具CAD/CAM技术中集成数字化分析技术,获得完善的CAD/CAE/CAM解决方案,是目前的一个重要发展方向。
三、塑性成型过程计算机模拟技术取得显著进步
塑性成型过程计算机模拟技术在近两年来也取得了突飞猛进的发展,华中科技大学模具技术国家重点实验室研制的注塑成形模拟软件和湖南大学研制的薄板冲压成形模拟软件,在数学建模、算法、前后置处理以及实验验证、工厂运用等方面,两校都有显著的进步,这标志着我国在注塑成型、板料成型过程计算机模拟方面已接近国际先进水平。这两项成果均被评为2002年度中国机械工业科学技术重大进展项目。
1.塑料注射成型过程仿真系统的开发和应用
塑料注射成型过程仿真属于机械、力学、材料和计算机相交叉的新兴学科,由于塑料熔体的非牛顿性以及注射流动过程的非稳态、非等温性,采用计算机模拟熔体成形过程具有很大难度。虽然世界各国研究的单位很多,但最终形成有影响的商品化系统的只有两家:澳大利亚Moldflow公司和美国ACTech公司。华中科技大学模具技术国家重点实验室在国家自然科学基金和其他课题基金的资助下不断地改进、应用和推广,经历了从二维分析到三维分析,从局部试点到大面积推广应用的历程。经过10余年的努力,开发出独具特色、具有当前国际先进水平的三维注塑成型仿真系统。
传统的注塑成型仿真软件基于制品的中心层模型,而模具设计多采用三维实体模型,由于两者模型的不一致,二次建模不可避免。但是从三维实体中抽象出中心层面是一件十分困难的工作,提取过程繁琐费时,因此设计人员对仿真软件有畏难情绪,这已成为注射仿真软件推广应用的瓶颈。该系统能直接在三维实体模型上划分网格,通过表面配对和引入新的边界条件保证对应表面的协调流动,实现了基于三维实体模型的分析,并显示三维分析结果,突破了仿真系统推广应用的瓶颈。解决了用三维实体模型取代中心层模型的关键性技术难题。
注塑制品大多是薄壁制品,制品厚度方向的尺寸远小于其他两个方向的尺寸,温度等物理量在厚度方向的变化又非常大,若采用单纯的有限元或有限差分方法势必造成分析时间过长,无法满足模具设计与制造的实际需要。该系统在流动平面采用有限元法,厚度方向采用有限差分法,分别建立了与流动平面和厚度方向尺寸相适应的网格并进行耦合求解,在保证计算精度的前提下使计算速度满足工程需要,并采用控制体积法解决了成型中的移动边界问题。对于内外对应表面存在差异的制品,划分为两部分体积并各自形成控制方程,通过在交接处进行插值对比保证两部分的协调,实现了有限元/有限差分/控制体积方法的综合运用。
输入参数的合理性是数值分析获得正确结果的前提,该系统通过人工智能技术获得了注射时间的优化和分级注射的优化,保证了输入参数的合理性,并采用专家系统技术自动生成分析结果报告,缩短了用户需求与分析结果之间存在的距离,将仿真软件由传统的“被动式”计算工具提升为“主动式”的优化系统。
在仿真中流道系统一般采用圆柱体单元,而制品采用的是三角形单元,该系统采用半解析法解决了混合单元的集成求解问题,不仅能分析一模一腔大型复杂的制品,而且能够分析一模多腔小型精密制品,大大拓宽了系统的使用范围,实现了制品与流道系统的三维流动保压集成分析。
熔合纹对制品的强度、外观等有重要影响,准确预测熔合纹位置也是仿真软件的难题,该系统通过采用节点特征模型方法大大提高了熔合纹预测的准确性和效率,其准确度高于国际上同类产品的先进水平。并利用神经网络方法对熔合纹的影响程度做出定性评价,为用户对成型质量的评估提供了直接的判据。
该系统的开发与应用,为注塑制品与模具的虚拟制造奠定了坚实的理论和技术基础,构成了注塑制品成形质量全面控制的核心技术。目前,该系统已形成商品化软件产品,并在海尔、科龙等60多家用户中推广应用,产生了可观的经济效益。
2.薄板冲压工艺与模具设计理论、计算方法和关键技术在汽车车身制造中的应用
薄板冲压技术在汽车、轻工、航空等领域应用广泛,特别是在车身覆盖件成形上,更是意义重大。薄板冲压过程包含以大位移、大变形为特征的几何非线性,以塑性变形为特征的材料非线性和以接触摩擦为特征的边界非线性,其设计计算极其复杂。
经过对薄板冲压工艺与模具的设计理论、计算方法和关键技术深入和系统的研究,湖南大学以开发先进冲压CAE技术为突破口,强调CAD/CAE/CAM的系统集成,创建了一套从基础理论与方法到CAE冲压分析,到冲压工艺的实验研究,再到冲压工艺设计和模具设计制造的具有自主知识产权的系统技术与装备。该项研究成果的主要内容包括:
(1)提出了薄板冲压工艺过程设计和分析的具有创新内容的系统理论和方法。包括显式加载隐式卸载的混合计算方法、基于级域概念的冲压成型一体化算法、基于弹塑性理论的摩擦模型、显示仿真算法中接触力计算的质量密度因子法、三维应力状态板壳理论与混合单元理论、板壳的交叉降阶积分法、基于试验与仿真材料的参数反求理论、超大规模计算中的计算任务动态分配方法和多CPU间的定时通讯理论。
(2)冲压仿真CAE自动建模系统CADEMI在国内外最先利用模具表面NC数控轨迹数据作为网格生成的几何数据源,不仅可避免发生几何信息丢失与失真,而且建模效率可提高数倍至数十倍。实现结构化四边形网格自动优化,对常用汽车冲压件成型,在同样精度下可将仿真模型网格单元减少近20%~40%,有效减少了计算工作量。冲压仿真CAE系统CADEMII采用交叉降阶积分法,消除了国内外仿真算法常用的人为沙漏控制参数,从理论和算法上保证了冲压件大变形计算的可靠性。采用独特的基于虚拟接触块的一体化全自动接触搜寻法,局部质量密度因子法和非线性摩擦定律,使冲压计算中的接触边界条件计算不仅有理论上的重大创新,而且在保证精度的前提下提高了速度。
冲压并行仿真系统CADEMP采用基于最小边界的优化方法进行仿真模型的初始化分区,实现了不同CPU上的计算量平衡,以及CPU间通讯量的最小化。基于CAE的冲压工艺分析与设计系统CADEMIII在国内外最先采用壳体失稳理论预测冲压中的起皱趋势,从而消除有限元网格尺寸对起皱预测准确性的影响,显著提高起皱预测的可靠性。采用基于仿真的毛坯反算技术,实现复杂零件的毛坯形状和尺寸迭代反求。在国内外最先实现冲压成型参数反求与标准测试实时联机,计算出材料本构特性参数和摩擦特性参数。
(3)研究结果表明,仿真技术只有与试验技术有机结合才能产生最好效果。开发研制的冲压工艺综合试验技术与装备,实现了与仿真方法匹配的材料本构特性参数的获取、冲压件与模具间摩擦特性参数的获取、不同形状和尺寸的拉延筋的特性参数获取以及仿真考题的试验验证。
(4)为解决冲压工艺方案中常出现的起皱或拉裂等成型缺陷,除在压边圈的压料面上设置有传统的直线或环线拉延筋外,还在压边圈的压料面上创新性地设置有斜拉延筋。发明的斜拉延筋与传统拉延筋区别在于传统拉延筋主要提供板材在冲压中的具有被动性质的流动阻力,而斜拉延筋除提供流动阻力外,还可提供具有主动性质的引导材料流动的作用力,从而提高成品率和成品质量。
(5)该项目成果已在湖南大学汽车技术研究与开发中心、上汽五菱汽车股份有限公司等企业建立起应用示范点,选择企业最迫切需要解决的最有代表性的问题进行CAD/CAE/CAM一体化技术应用示范,从而促使该技术较快投入实际工程应用。
四、基于知识的材料成形过程模拟仿真
中国是仅次于美、日、德,居世界制造业的第四大国。材料成形加工业是制造业的重要组成部分,新一代材料加工技术也是先进制造技术的重要内容。随着计算机技术的发展,材料加工制造过程的模拟和仿真,已经成为新兴的交叉学科,它是除实验方法和理论方法以外的第3个解决材料成形加工的重要研究方法。
产品设计制造开发系统是以设计制造过程的建模为核心内容的,在产品零部件的设计过程中同时要进行影响产品和零部件性能的成形过程的建模及仿真。它不仅提供产品零部件的可制造性评估,而且可提供产品零部件的性能预测,注塑成形过程模拟、板料冲压成形模拟系统的应用很好地说明了这一优势。
在现有的研究中,基于CAE的成型工艺优化主要是采用数值分析的方法,但是由于成型工艺本身的特点,很难给出连续和规则的优化求解空间。并且,数值分析方法还存在计算量大、效率低、优化目标单一等缺点,这在很大程度上影响了CAE技术的普及。知识工程的方法和技术是解决数值分析固有不足的有效途径。20世纪90年代以来,知识工程的研究异常活跃,相关的方法与技术层出不穷,随着知识工程研究的深入与扩展,通过建立包括产生式规则、实例、样本等集成多知识表达方式的知识库和规则推理(RBR)、实例推理(CBR)、人工神经网络(ANN)等集成多处理方式的多智能主体,建立全面支持CAE应用过程的智能化系统,应用人工智能与专家系统技术,在数值分析结果的基本上自动对成型方案进行分析和评价,并提出方案的优化建议,是当前材料科学与制造科学的前沿领域和研究热点。
在模具CAD/CAM的基础上,结合人工智能技术深入应用材料成形CAE技术,是我国企业能够尽快地登上现代数字制造技术新台阶的捷径。
声明:本网站所收集的部分公开资料来源于互联网,转载的目的在于传递更多信息及用于网络分享,并不代表本站赞同其观点和对其真实性负责,也不构成任何其他建议。本站部分作品是由网友自主投稿和发布、编辑整理上传,对此类作品本站仅提供交流平台,不为其版权负责。如果您发现网站上所用视频、图片、文字如涉及作品版权问题,请第一时间告知,我们将根据您提供的证明材料确认版权并按国家标准支付稿酬或立即删除内容,以保证您的权益!联系电话:010-58612588 或 Email:editor@mmsonline.com.cn。
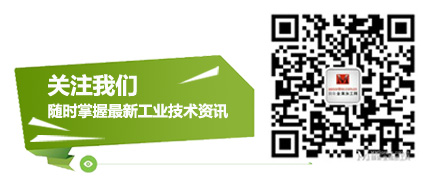
- 暂无反馈