铸铁发动机缸体曲轴孔的精加工方案
曲轴孔的加工质量对发动机的工作性能具有重大影响,奇瑞公司发动机事业部根据实际加工情况,对铸铁发动机缸体曲轴孔的精加工方案不断进行研究和持续改进,收效显著,使加工质量和效率都得到了有效提升。
缸体是发动机重要的基础件,其主要功用是将各机构、各系统组装成一体,而发动机最主要的运动部件——曲轴、活塞和连杆都与缸体有着非常密切的关系。目前,我们常见的汽油发动机最高转速达6 000r/min以上,曲轴在发动机缸体的曲轴孔中与轴瓦之间形成油膜,以滑动轴承的方式支撑和润滑高速运转的曲轴,这就对曲轴孔的精加工提出了较高的工艺要求。
由于曲轴孔的加工质量对发动机的工作性能具有极大的影响,所以我们对发动机曲轴孔工艺的要求一般比较严格,包括直径、位置度、圆度、各档曲轴孔中心的直线度及表面粗糙度等。为了满足这些要求苛刻的工艺指标,精加工一般采用精镗或铰珩两种加工方式。
精镗加工方式分析
精镗方式精加工曲轴孔相对于铰珩方式而言,初期投入成本较低,可在加工中心或专机上与其他部位的精加工共同安排在一道工序。因考虑到特殊的工艺要求,目前我们采用的精镗方案是两把精镗刀组合,第一把精镗刀进行引导镗1、2档曲轴孔,第二把精镗刀在1、2档曲轴孔的支撑下精镗剩余的各档曲轴孔。由于曲轴孔各档之间需要保持较高的同轴度,所以精加工时必须在同一个方向进刀加工,但这么长的曲轴孔镗刀在加工第1档曲轴孔时会出现因缺少支撑而跳动过大的情况,所以采用一长一短两把精镗刀组合的方式精加工曲轴孔。
目前,精镗曲轴孔的镗刀一般采用硬质合金或CBN材质的刀片。硬质合金的刀片成本较低,但加工工件的表面粗糙度不好,且刀片的耐用度较低。针对这一问题,我们协同刀具供应商共同收集了业内较为普遍的刀片涂层材料以及在刀片切削角度上的经验技术,对16款硬质合金刀片进行切削实验,并尝试了对各种合适的加工参数进行优化。通过大量验证,硬质合金刀片在满足粗糙度等工艺要求的前提下最好的实验结果为一次性加工80件,仍不能满足大批量生产的要求。
随后,我们对精镗刀的刀片材质进行了另外一种方案的验证,即更换现有的硬质合金刀片材料为CBN刀片材料。我们依靠刀具供应商开发出了10多款不同的CBN刀片对曲轴孔进行切削验证,测试结果显示:在粗糙度的控制方面,CBN刀片明显优于硬质合金刀片,加工寿命能够突破200件。但同时也产生了一些新的问题:用CBN材质的刀片加工约150件时,开始在孔侧出现轻微毛刺,严重时将会出现翻边现象。此处的毛刺甚至翻边成为影响发动机性能的质量隐患,严重时会造成轴瓦划伤及曲轴抱死等质量事故。在曲轴孔毛刺问题的处理方面,我们增加了曲轴孔的毛刷,在一定程度上缓解了毛刺的存在,但仍存在较大的质量风险。
此外,曲轴孔精镗方案的质量稳定性相对铰珩而言较差,且因为换刀频繁会极大地增加质量控制的风险。精镗刀加工出的工件表面粗糙度变化趋势随刀具耐用度的减少而下降较快。
铰珩加工方式分析
对镗削精加工的曲轴孔方案我们做了大量的探索工作,并开发出多种新型刀片进行加工验证,但仍然未达到理想的加工效果,因此我们再次考虑曲轴孔铰珩方案。从成本方面考虑,曲轴孔铰珩的一次性投入较大,德国某知名珩磨机厂商的初步报价为40万欧元(因配置要求不同,价格会有差异),但后期加工成本比精镗低很多,且加工质量稳定。
曲轴孔的铰珩采用卧式珩磨机进行加工,因为卧式珩磨机的工作行程较长,适用于像曲轴孔这类的深孔珩磨,深度最大可达3 000mm。在加工过程中,珩磨头的油石在胀缩机构作用下作径向进给,把工件逐步加工到所需尺寸。珩磨头外周镶有2~10根长度约为孔长1/3~3/4的油石,在珩孔时既旋转运动又往返运动,同时通过珩磨头中的弹簧或液压控制而均匀外涨,所以与孔表面的接触面积较大,加工效率较高。
珩磨余量一般不超过0.2mm。对铸铁或有色金属进行加工,珩磨的圆周速度可达50m/min以上;珩磨的往复速度不宜超过15~20m/min。油石对孔壁的压力一般为0.3~0.5MPa,粗珩时可达1 MPa左右,精珩可小于0.1 MPa。由于珩磨时油石与工件是面接触,每颗磨粒对工件表面的垂直压力只有磨削时的1/50~1/100,加上珩磨速度低,故切削区的温度可保持在50℃~150℃范围内,有利于减小加工表面的残余应力,提高表面质量。为了冲刷切屑,避免堵塞油石,同时降低切削区的温度和表面粗糙度,珩磨时采用的切削液要有一定的工作压力并经过过滤。切削液大都采用煤油或煤油加锭子油,也可采用极压乳化液。
其铰珩的加工稳定性非常高,并且珩磨头一次更换砂条的耐用度可加工1万余件,生产效率大幅提高。采用CBN刀片的精镗加工方式,每200件需要换刀一次,平均每次换刀和首件检测需要42min。如果将频繁换刀所花费的时间折算到每个工件上,将损失12.6s/件。按照现有某生产线的加工节拍为120s/件,生产纲领为16万件/年来计算,全年将损失加工时间201.6万s,利用这段时间每年可以多加工出1.68万件。
表为曲轴孔不同精加工方式所产生的刀具损耗成本对比,从表可以分析出,单件的刀具成本差距较为明显。按照理论分析计算,当生产103万件工件时,铰珩方案相对于CBN精镗方案的刀具损耗节约381.1万元左右,略同于铰珩设备的价格,并且铰珩方案的质量控制难度和风险都小得多。
两种方案的对比
经过大量的实验和生产实践,我们认为铰珩方式与镗削方式各有优势,具体归纳如下:
1. 成本投入
镗削方式成本投入较少,只需定制专用刀具,与精加工其他部位共用机床即可;铰珩方式一次性投入较高,但可考虑与缸孔珩磨共用珩磨机,以适当减少投资。
2. 占地面积
采用镗削方式不需要单独新增设备;采用铰珩方式需要单独的区域布置铰珩设备,如果与缸孔珩磨共用设备需要增加珩磨机占地面积。
3. 加工质量
镗削方式能够满足加工质量的要求,但稳定性相对较差;而铰珩方式不仅能满足加工质量的要求,且质量稳定性较好。
4. 生产效率
虽然镗削方式的切削效率不低,但频繁换刀造成时间的损失较大;铰珩设备一次调整好后,可持续稳定加工,生产效率较高。
5. 单件刀具成本
由于工艺要求高且刀片耐用度低,使得镗削方式的单件刀具成本较高;采用铰珩方式,由于铰珩设备的珩磨头砂条耐用度高,单件刀具成本也较低。
综上所述,虽然目前这两种方式在各企业的曲轴孔精加工中都有较大范围的应用,但根据各自的优缺点分析,精镗方式更适合产量较小时使用;如果产量大、质量要求高,建议还是采用曲轴孔铰珩的方式进行加工,以提高产品的加工效率和质量稳定性,降低发动机的加工成本。
声明:本网站所收集的部分公开资料来源于互联网,转载的目的在于传递更多信息及用于网络分享,并不代表本站赞同其观点和对其真实性负责,也不构成任何其他建议。本站部分作品是由网友自主投稿和发布、编辑整理上传,对此类作品本站仅提供交流平台,不为其版权负责。如果您发现网站上所用视频、图片、文字如涉及作品版权问题,请第一时间告知,我们将根据您提供的证明材料确认版权并按国家标准支付稿酬或立即删除内容,以保证您的权益!联系电话:010-58612588 或 Email:editor@mmsonline.com.cn。
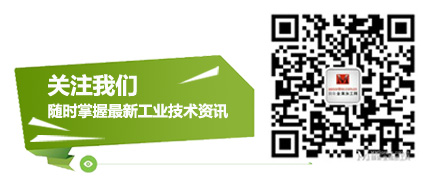
- 暂无反馈