全新加工策略为航空零件提供先进加工模式
目前,全世界大约有17000架客机和货机在运行之中,天空似乎变得更加拥挤。专家猜测,到2025年,还需要25000架新的飞机。尽管发展迅速,但航空制造业仍然面临着原材料价格上涨、难加工材料的应用日益增加,以及生产能力有限等题目,为了提供新的、加工过程可靠的解决方案,就需要采取新的加工策略。
钛合金、Inconel镍基合金和其它高强度耐热合金以及碳纤维增强型复合材料正在替换传统的铝合金,成为航空工程使用的主要材料。航空零件制造商经常需要对复合在同一个零件上的多种材料进行加工,由于一种金属(如钛)可能被夹在多层复合材料之间,以增强复合结构的稳定性。
随着航空公司寻求大幅度降低燃油消耗,轻质结构正在变为标准和规范。例如,德国汉莎航空公司希看飞机的人均耗油量达到1.25加仑(即每位乘客飞行100英里的耗油量为1.25加仑)。然而,要实现这一目标,对于零件制造商而言却是一个昂贵的命题,由于轻质材料的加工需要对新的机床和切削加工方案进行大规模投资,这可能包括从由大型龙门式机床(具有六个或更多个轴)组成的生产线转换为在采用加工中心的单台设备上加工零件,以进步加工柔性。不过,这些本钱可以通过采用独创的加工新概念而得到补偿。
在如今的飞机制造业,延长刀具寿命和使加工可靠性最大化至关重要。除了需要加工富有挑战性的工件材料,还需要实现高达90%的加工率。换句话说,加工机床必须将90%的时间用于切削加工。
挖掘符合经济原则的加工潜力
很多航空零件仍然需要用整块毛坯加工而成,这样做是有理由的,由于这些零件不仅要受到极端环境条件的影响,而且通常需要承受极高的机械应力,为了消除这些零件发生碎裂和其它损坏的可能性,必须在很大程度上开释应力,而这可以通过用整块毛坯加工零件来实现,但是,要完成这种零件的加工,往往需要耗费大量工时。
那么,有什么进步生产率的方法吗?考虑到切削速度与刀具负荷密切相关,零件制造商必须在一定的速度限制内进行加工。他们不能期看对大多数难加工材料的加工速度有突破性的进展,例如,加工钛合金时,将切削速度从150sfm(45.7m/min)进步到200sfm(61m/min)就已经被以为是高速切削了。
因此,对于用户而言,挖掘新的潜力的唯一途径就是改变加工策略。就在几年以前,航空产业中的机械加工还是以使用高速钢刀具为主,其适用的切削速度要低于硬质合金刀具。但是,随着传统高速钢刀具材料的让位,整体硬质合金刀具和可转位刀具凭借可进步生产率的上风,正大举进进航空制造业。但这需要投资新机床或花大价钱对现有机床进行升级改造,以提供使用脆性更大的硬质合金刀具所需的刚性,以及采用适合硬质合金刀具的更高切削参数进行加工。这就对制造商提出了一个重大课题,他们发现,实现投资回报需要花费太长的时间。
简单地换用更高档的刀具可能已经不足以解决这一题目。因此,刀具制造商正与机床制造商和终极用户协作,从生产发展进程的出发点出发,对整个制造流程进行通盘问虑。
以较低本钱保证飞行安全
在汽车制造业,刀具制造商从产品开发的早期阶段就已涉足其中。与此不同的是,刀具制造商的航空产品加工专家通常是在产品开发完成后才被要求参与,这在很大程度上是由该行业的固有传统所决定的。
在过往几十年里,航空公司都很少关注本钱,由于飞行安全是必须不惜一切代价确保的重中之重。但随着全球化的发端以及廉价空中旅行的急剧增长,不计本钱的时代已经终结。航空业正逐步熟悉到,尽管飞行安全是最重要的因素,但也应该以可承受的较低本钱来实现。这就给飞机制造商及零部件供给商带来了巨大的定价压力,他们迫切希看鉴戒其他行业(特别是汽车制造业)的经验,其中最大的挑战就是与低本钱的亚洲制造商进行竞争。
例如,通过将制造业务大规模分包给不同的供给商,汽车制造业的原始设备制造商可在开发项目中与其一、二级供给商分担风险。然后,由这些供给商为总装线交付已加工好的零部件。
终极用户应该在生产计划的各个阶段向刀具制造商提供所需的数据,让刀具制造商的研发团队可以确定最优化的刀具切削刃几何结构,并通过一系列标准化测试使其与涂层相互匹配。这些工作的重点就是要进步刀具寿命。
在飞机制造中,由于存在大量复杂结构零件(如金属锻件或以众多凹腔为特征的平板件),因此涉及到数目巨大的凹腔铣削加工。因此,找到正确的凹腔高效加工策略(包括切屑控制和排屑策略)至关重要。在使用高效刀具铣削凹腔时,天生大小适当(厚度0.15-0.20mm)的切屑的经验方法是以1.5-2.0mm的切深、0.38-0.50mm/齿的进给量进行加工。确定正确的加工策略不仅涉及到工件材料,而且涉及到机床、刀具和工装夹具等。
例如,一种方法是在凹腔的转角处先钻一个起始孔,然后用方肩铣刀通过二轴铣削逐层往除工件材料。根据机床的扭矩和马力,每一层的适当切深为3.8-5.1mm。
另一种可选方法是:用户可在整个切削深度上以较小的切削宽度切除金字塔形的毛坯材料,这样,刀具的径向吃刀量和轴向吃刀量在每一次走刀中都是变化的。当工件材料(如不锈钢)轻易使刀具或刀片产生刻痕时经常采用这种加工方式。由于切深刻痕是轴向的,并分布在沿切削刃的不同位置,这种加工技术可以分隔切深刻痕并使其沿切削刃方向延伸。当刀具悬伸较长时,采用插铣通常是一种正确的加工策略。
涂层的优化设计
尽管精确设计了合适的切削刃几何外形,但在加工航空材料时,对切削速度仍然存在技术限制。大幅度进步生产率的唯一方式就是应用多齿刀具和延长刀具寿命。这就取决于选择正确的刀具涂层。最优化的涂层不仅可以减少磨损,而且还能保护切削刃免受切削热的影响。例如,PVD氧化铝涂层特别适合加工航空材料,其主要优点是优异的耐高温性能,可有效避免在切削刃上形成积屑瘤和产生微崩刃。
切削钛合金时,在切削刃上产生的热量是个大题目。由于工件材料导热性差,使大部分热量传进切削刃。可是,当在切削刃上涂覆了耐热性能极好的涂层后,热量被迫流向其他方向(如传进切屑)。加工钛合金时,PVD氧化铝涂层提供的热屏障可使刀具使用寿命进步50%,并且在很多情况下,无需换刀即可完成一个工件形貌(如凹腔)的加工,从而缩短了机床的加工辅助时间。
另一个例子是改进的Al2O3涂层。该涂层沉积在刀具上时,通常表面比较粗糙。为此,Walter公司在其Al2O3涂层上面再涂覆一层TiCN涂层,然后通过喷丸处理往除前刀面的顶层。这样,就提供了一个光滑的涂层表面,当切屑碰撞切削刃时可以减少摩擦,从而延长了刀具寿命。利用该方法,还制造出了一种看起来与众不同的双色刀片,能够很轻易地识别其后刀面磨损。
新的加工方法
在制造航空零件时,为了进步生产率,一方面可以采用适合所用机床特定需求的高效刀具,另一方面可以采用新的加工方法。采用现代加工中心,可以大幅度缩短加工周期。例如,通过改变起落架零件的加工方法,可以缩短加工周期。该零件高达3m,由10-2-3或5553钛合金材料制成(依型号而定)。过往,是采用螺旋铣刀在三轴机床上进行前后往复切削,将工件加工到要求的尺寸。而采用新型的五轴车/铣复合加工中心,工件本身可以旋转,以适应车刀、轮廓铣刀和方肩铣刀的加工要求,对于车削加工达不到的部位,可以采用车铣加工。另一种可选加工方法是用轮廓铣刀在Z轴进给平面连续往复切削,每次切除一层材料。这些在工具和模具制造业被以为相当传统的加工方法现在又在航空制造业找到了用武之地。
变革加工方法的另一个例子是飞机发动机的制造。一架飞机包括4个主要部分:机身、动力系统(发动机、发电机)、起落装置和飞行控制系统。每一部分都需要用不同的材料和不同的加工方法来制造。制造发动机需要加工钛合金、Inconel镍基合金等能够承受高动态负荷和热负荷的材料。为了制造发动机的后部零件(如高压/低压涡轮),需要加工Inconel合金。这种加工可以采用标准的大进给铣刀来完成,为了适应小功率机床的加工需要,一些刀具制造商已对这种刀具进行了改进。
考虑到飞机制造业的高速发展,机床数目完全不能满足需求的增长,因此,必然会导致交货期的延长。这种现状必须从根本上加以改变,由于来自俄罗斯和中国的竞争对手不仅在定价上,而且在创新上,都在对老牌飞机制造商施加压力。一些初步加工难度不大的航空零件(如发动机罩)已经在这些国家进行生产,这些国家的制造商早晚会获得装备和技术诀窍,生产出全部复杂零件。
目前,航空制造业面临的巨大挑战是必须具备将高质量与高生产率结合起来的能力。为了应对这一挑战,未来几年将会产生全新的加工策略,甚至有可能为其他行业提供先进的加工模式。
声明:本网站所收集的部分公开资料来源于互联网,转载的目的在于传递更多信息及用于网络分享,并不代表本站赞同其观点和对其真实性负责,也不构成任何其他建议。本站部分作品是由网友自主投稿和发布、编辑整理上传,对此类作品本站仅提供交流平台,不为其版权负责。如果您发现网站上所用视频、图片、文字如涉及作品版权问题,请第一时间告知,我们将根据您提供的证明材料确认版权并按国家标准支付稿酬或立即删除内容,以保证您的权益!联系电话:010-58612588 或 Email:editor@mmsonline.com.cn。
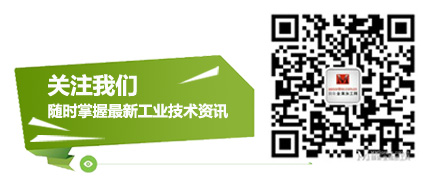
- 暂无反馈