大厚度网格状机翼整体壁板的工艺特点
大型固定翼硬壳式飞机机翼翼盒原来都是由蒙皮、长桁、肋、对接接头组成,再加上前、后梁等许多处于分离状态的零、组件装配而成的。随着用户对飞机的飞行品质及其使用的安全性、耐久性和低成本等方面的要求越来越严格,作为飞机最大承载部件的机翼翼盒需要首先满足这些要求,必须进行综合改进以提高其在强度、疲劳、重量、密封等各方面的结构设计水平,故现代大型飞机机翼翼盒的结构设计已越来越多地采取了整体结构形式,而整体壁板就是其中的典型代表之一。
所谓整体壁板其实是蒙皮本身的改进或蒙皮与上述各分离状的零、组件的一种有机集合体。由于存在有多种不同的组成方式,故整体壁板也呈现为多种结构形式。目前在世界上流行的方式有变厚度(或变截面)整体蒙皮式壁板、带长桁壁板、带长桁与对接接头的壁板以及既带长桁和肋又带对接接头的壁板等。本文所指的大厚度网格状壁板则属于上述的最后一种形式。
大厚度网格状机翼整体壁板的结构特点及成形工艺简介
1结构特点
此类壁板是把机翼蒙皮与长桁、肋、对接接头(俗称梳状接头或梳状件)以及其他可附带上的结构件(如工艺或维修口框、注油口框等)集合为一体。由于飞机越大,机翼对接接头的厚度尺寸越大,因此必然会使壁板厚度增加而成为大厚度,同时既带长桁又带肋必然使壁板成为网格状。这种壁板应该是目前世界上所有大飞机中集成度最高的整体壁板。机翼翼盒的组成方法一般是将若干块这种壁板搭接(涂密封胶)后用过盈螺栓密封连接组成机翼上、下两壁,再通过与机翼前、后梁(均为组合件)及端肋的密封连接而形成盒体,其翼肋的装配一般是在此过程后用壁板上已有的肋墙为根基进行装配连接。机翼翼盒同时也是整体油箱。
由于此类整体壁板的整体化水平很高,故可大大减少结构零件的项目和数量,且结构紧凑、协调环节少、工艺路线短、密封性好、装配简单。目前此类壁板多用于乌克兰安东诺夫设计局的“安”系列大型运输机,如安-70,国产运8飞机也已开始采用。俄制苏-27也部分采用类似结构形式的壁板,但厚度均不超过40mm,只能属于中厚度。
2成形工艺
由于此类壁板的厚度一般都超过60mm,重型运输机的壁板厚度可达100mm~120mm或以上,同时又是网格状,故刚性很强,是常用的喷丸成形工艺无法成形的。直到目前为止,安系列大型运输机仍采用渐进式机械压弯为主、喷丸成形为辅的生产工艺,苏-27则完全采用压弯工艺。
渐进式机械压弯是在对壁板进行平面铣切后,经光整加工,再用压力机对壁板进行缓进式压弯(分粗压和精压),使其获得指定的弯曲型面。其基本原理是有效利用材料的σb和σs的强度余量,在未达到断裂之前完成塑性变形。为达到此目的,除材料的σb应较高、σs应较低之外,其延伸率应较大。故“安”系列大型飞机的上、下壁板均采用上述特性较好的1973T2和1161T铝合金。同时为保证压弯成型的质量安全性,安东诺夫设计规范规定壁板的厚度与其曲率的比值为:h/R≤1%(h为厚度,R为曲率半径)。
压弯成形工艺的主要缺点
虽然压弯成形已是安东诺夫的一种成熟工艺,但属于一种落后工艺,是不值得继续仿效和推广应用的。因此我们必须顺应现代航空制造技术发展的潮流,以创新的思维另辟蹊径,努力创造出一种新的、更为先进的工艺取而代之。其主要缺点如下:
·风险较大,质量安全系数低。
·型面的流线较差。
·壁板的直线度较差。
·残余应力较大。
·成形质量的一致性差,难以受控。
·生产效率低,劳动强度大,难以形成自动化生产。
铣切与压弯两种成形工艺的优劣对比
铣切成形和压弯成形的优劣性,除材料利用率和工序成本外,铣切成形工艺均占有绝对明显的优势。另外,由于压弯成形工序完成后还要进行喷丸或校形工序,加上铣切成形工艺生产的壁板能大大提高装配效率,故铣切成形的综合成本也不一定高于压弯成形。因此,无论从何角度分析,铣切成形均优于压弯成形工艺。
铣切成形工艺所显示的各种优点正好纠正了压弯成形工艺的大部分缺点,其产品质量稳定,生产效率较高,成效十分显著。事实证明,“以铣代压”创新之路是非常正确的,它既是替代压弯成形工艺的有效途径,也完全符合现代航空制造技术的发展方向。
铣切成形存在的工艺难点及解决措施
1铣切加工的难点
为确保大厚度机翼整体壁板的研制,重点从以下几方面对加工工艺性进行了分析:
(1)由于每块壁板的毛坯内应力存在较大差异,采用同样的设备、刀具、加工程序和切削参数加工出来的壁板,其变形部位和大小差异性较大,难以完全符合设计数模。
(2)因生产现场温度控制困难,受生产季节、时段温差影响,其线形尺寸(尤其是长度方向)会因热胀冷缩影响而参差不齐,对长近11m的机翼来说,影响很大。在这种情况下,为了满足装配要求,不得不在装配时留出足够的余量,从而降低了装配效率。另一方面,由于无法保证翼肋的同面性,使得结构设计不得不放弃带翼肋的方案,而采用角盒连接,不但使翼盒装配难度加大、效率下降并且增加了重量。虽然压弯成形工艺同样存在这一问题,但对铣切成形工艺而言,优点则未能充分发挥,也难以实现精确制造和无余量装配的目标。
(3)零件腹板为双曲面变截面,厚度沿长度方向渐变,壁板内“工”字长桁筋高沿高度及厚度渐变,且长桁法向于外蒙皮,角度变化复杂,结构形式使尺寸不易保证。
2优化目标与解决方案
为实现整体壁板的精确制造,满足翼盒的积木化无余量装配,从现实性和可行性方面分析宜采取以下解决方案:
(1)进行必要的技术改造,以实现对壁板铣切成形现场的环境温度控制,为降低技改成本也可考虑局部改造,起码应使其精加工能在恒温下进行,从而保证壁板在铣切成形后的几何尺寸一致及肋的同面性。此举可极大地提高壁板的互换性,并为实现精确制造和翼盒的无余量装配创造必要条件。如生产现场温控问题实在无法解决,也可考虑采用带温度自适应控制的机床进行精加工,或在同一机床上同时配对精加工横向肋的方法。
(2)在上述问题得以解决的情况下,可对中外翼全部采用带肋的设计,即将所有壁板设计为网格状。这样,一是可以提高壁板的刚性,便于铣切成形的装夹与加工;二是可以大大减少铣切变形以及喷丸强化带来的变形;三是可以取消所有角盒连接方式,即便于装配又可起到减重作用。
(3)进一步改进工艺流程,合理调配设备产能宜采用3坐标机床粗加工,5坐标机床精加工,有利于提高加工效率,表面质量并降低成本。
(4)解决零件变形问题。开应力释放槽,在零件粗加工前沿宽度方向铣出应力释放槽,使零件在粗加工时由于大量去除材料而产生的内应力得以充分释放,解决零件粗加工时产生的变形。
层优先加工,粗加工采用层优先的加工策略编程方式,使零件沿Z向均匀去除材料,避免因应力集中而产生的变形。
选用大直径刀具及高速切削,粗加工使用大直径刀具并采用高速切削加工技术,可以快速将切削热通过铝屑带走,最大限度的防止整体壁板切削加工时的热变形。
(5)有效保证零件尺寸。毛料上沿零件长度方向均匀钻制3-φ20的工艺孔,用于监控零件的马刀弯变形及沿长度方向的伸缩变形。分别在初始状态、粗铣完槽腔、精铣槽腔前、槽腔面精加工完、外型面精加工前、外型面精加工结束,6个阶段记录工艺孔孔位及零件的平面度变形情况。这些工作就是确保零件的变形量在工艺余量的包容范围内,为加工出合格的产品提供技术保障。
为保证零件外形面的平稳加工以及腹板厚度尺寸,在零件的长桁上间隔1000mm~1500mm留10mm×10mm的支撑块,在加工外型面时起支撑作用,最后由钳工去除并与零件面修平。
本方案若能顺利实施,必将全面提升运8飞机机翼整体壁板及中央翼、中外翼翼盒的制造技术水平,为实现数字化生产、精确制造和无余量装配创造有利条件。同时也可为我国大、中型飞机研制中可能遇到的大厚度网格状整体壁板的成形制造提供一种新的技术储备。此外,该工艺方法还可以用以解决采用压弯、喷丸等成形方法难以完成的其他曲面零件的加工难题。
声明:本网站所收集的部分公开资料来源于互联网,转载的目的在于传递更多信息及用于网络分享,并不代表本站赞同其观点和对其真实性负责,也不构成任何其他建议。本站部分作品是由网友自主投稿和发布、编辑整理上传,对此类作品本站仅提供交流平台,不为其版权负责。如果您发现网站上所用视频、图片、文字如涉及作品版权问题,请第一时间告知,我们将根据您提供的证明材料确认版权并按国家标准支付稿酬或立即删除内容,以保证您的权益!联系电话:010-58612588 或 Email:editor@mmsonline.com.cn。
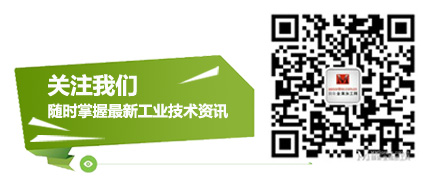
- 暂无反馈