RYOBI 使用 WorkNC Auto 5 将加工时间缩短 30%
世界级的压铸冲模
RYOBI 有限公司是压铸冲模产品生产商,总部位于日本广岛,生产厂房设于日本静冈县。该公司成立于 1943 年,为诸多应用提供高质量压铸冲模部件,包括电气用品、办公自动化、工业设备、建筑行业及汽车行业工具,生产齿轮箱体及气缸体。此外,公司还生产电动工具和印刷设备等成品,整个集团有 5,500 余名员工。
<< 使用 Auto 5,加工时间降低了约 33%,编程时间缩短了20%。 >>
Ono 先生,RYOBI 有限公司冲模组
5 轴加工消除了电极的使用
静冈厂压铸冲模科的冲模组自 2001 年起使用 WorkNC 用于冲模生产的 3 轴加工和定位 5 轴加工。由于型腔深度和曲面质量的要求,精加工操作需要大量使用电极。由于担心创建 5 轴联动刀具路径及可能产生的曲面精加工会带来困难,以前一直未能采用 5 轴联动加工。然而,生产电极所需的大量时间促使公司对直接加工更多刀具,以削减整体生产时间的方法进行了检视。
通过评估,公司选择了 WorkNC Auto 5
冲模组的 Ono 先生对现有流程进行了解释:“生产流程由四个加工操作组成:先是热处理,然后是进一步的精加工操作,包括 EDM 开模、型腔加工和坐标镗削,总共有 12 项操作。”要实现所追求的节约目标,RYOBI 对不同的生产方法,包括限制刀具长度、改善曲面精加工、缩短加工时间及通过更多地在加工中心切削型腔以减少电极使用次数的方法进行了评估。Ono 先生补充说:“根据研究,我们最终认定采用 WorkNC Auto 5 作为解决方案。”
使用 Auto 5,流程由 12 个缩减到 8 个
WorkNC Auto 5 自动将 3 轴刀具路径转换为 5 轴联动刀具路径,同时考虑到有效刀具长度、刀架几何形状及机床刀具旋转限制等因素。为获得最佳效率,Auto 5 在可以接触到零件时,保持 3 轴刀具路径不变,优化了加工速度、刀具刚度和曲面精加工。使用 Auto 5,生成 5 轴刀具路径的过程非常简单,因为软件对要转换的 3 轴路径进行评估、执行碰撞检查,然后对生成的路径进行后处理,只需要最低程度的操作员干预,消除了与 5 轴编程相关的大多数复杂性。Ono 先生说:“采用 Auto 5,让我们将五个曲面精加工流程缩减到三个,由于可以使用 3/5 轴刀具路径加工大多数型腔,因此电极生产和 EDM 开模得到大幅度缩减,流程最终由 12 个缩减到 8 个。”
加工时间减少 33%
RYOBI 现在从重复粗加工阶段开始使用 Auto 5,在粗加工操作后用小型刀具挖剔。Ono 先生评论说:“可以从顶部进行重复粗加工的零件仅使用 Z 轴加工,接触不到的区域使用 5 轴同步切削。该操作程序改善了工作效果。我们在精加工操作中使用相同方法,必要时使用 5 轴刀具路径切削更多的模具。”他继续道:“由于操作次数降低,停工时间显著减少,缩短了我们的交付周期。总体来看,加工时间缩减了约 33%。不用说,劳动成本也大幅度降低了。”
编程速度提高 20%
在引入 Auto 5 以前,所有冲模均使用 3 轴技术加工。以前编程需要 55.5 个小时,其中 35.5 个小时用于为热处理后的操作准备程序,另外是电极生产编程的 20 个小时。使用 Auto 5,以现有 3 轴刀具路径作为起点,准备 5 轴联动刀具路径的时间仅为 8 个小时。结果总编程时间为 35.5+8=43.5 个小时,与只使用 3 轴编程相比,节省了约 20%。为进一步试验可取得的优势,RYOBI 使用 5 轴联动和定位 5 轴相结合的方法对相同冲模进行编程。准备时间为 46 小时,表明 Auto 5 可以达到更快的速度。
Sescoi 为 5 轴技术提供合作
Ono 先生总结说:“我们通过部署 WorkNC Auto 5 展示了模具和冲模行业可成功使用 5 轴联动加工。新的 5 轴机床和控制系统逐渐进入市场,让编制程序更容易了。我们将与商业伙伴和 Sescoi 合作,努力增加 5 轴加工在 RYOBI 的使用。
(西思科尔)
声明:本网站所收集的部分公开资料来源于互联网,转载的目的在于传递更多信息及用于网络分享,并不代表本站赞同其观点和对其真实性负责,也不构成任何其他建议。本站部分作品是由网友自主投稿和发布、编辑整理上传,对此类作品本站仅提供交流平台,不为其版权负责。如果您发现网站上所用视频、图片、文字如涉及作品版权问题,请第一时间告知,我们将根据您提供的证明材料确认版权并按国家标准支付稿酬或立即删除内容,以保证您的权益!联系电话:010-58612588 或 Email:editor@mmsonline.com.cn。
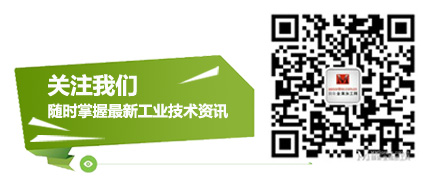
- 暂无反馈