分析:模具行业发展存在的四个问题
模具对于制造业的重要性,我们用不可或缺来形容。党中央、国务院提出扩巿场、调结构、促平衡,加快转变经济发展方式的总体要求,模具行业提出实现健康平稳发展,产业快速升级,2020年步入世界模具强国的目标。
“工业之母”如何走上发展快车道?如何缩短和强者之间的距离?这是摆在面前的课题。
“我”到底是谁?
没有高水平的模具就没有高水平的工业产品,在机械、电子、汽车、信息、航空、航天、轻工、军工、交通、建材、医疗、生物、能源等制造领域得到了广泛的应用。在各类文件和媒体的文字中,喜欢用“模具工业水平已经成为衡量一个国家制造业水平高低的重要标志,也是一个国家的工业产品保持国际竞争力的重要保证之一。”来描述其重要性。
由于模具产品技术含量较高,增值率高,生产周期较长,因而模具制造行业就有了技术密集和资金密集、均衡生产和企业管理难度大、对特定用户有特殊的依赖性、增值税负重、企业资金积累慢以及投资回收期长等许多特点。由于模具产品品种繁多,大小十分悬殊,要求各异,因此模具企业发展适于“小而精、小而专、小而特”;行业发展适合于集聚生产和集群式发展,以建立较强的协作配套体系。这也是模具行业的重要特点之一。
珠江三角洲、长江三角洲、环渤海地区是发展较快的三个区域。广东是模具第一大省,浙江、上海、江苏、安徽等省巿也实现较快发展。全国具有一定规模的模具园区(模具城)已有20个左右。目前全国共有模具生产企业(厂、点)约3万个,从业人员近100万人,2010年模具销售额约1200亿元。其中,中低档模具已供过于求,而以大型、精密、复杂、长寿命模具为主要代表的高技术含量模具自给率还较低,只有60%左右,有很大一部分依靠进口。
“我”现在在哪里?
近年来,模具产品水平也有了很大提高,向高端发展趋向较为明显。一些模具产品已达到或接近世界先进水平,但能生产高水平模具的企业在行业中还只占少数,综合来看,中国模具行业总体水平还比较低。
中国模具工业与国际先进水平相比还是有一定的差距。创新不够,信息化生产管理和创新发展特征还不具备,只处于世界中等水平,仍有大约10年以上的差距,其中模具加工在线测量和计算机辅助测量及企业管理的差距在15年以上。差距主要体现在:模具使用寿命低30%~50%(精冲模寿命一般只有国外先进水平的1/3左右),生产周期长30%~50%,质量可靠性与稳定性较差,制造精度和标准化程度较低,等等。与此同时,中国在研发能力、人员素质、对模具设计制造的基础理论与技术的研究等方面也存在较大差距,因此造成在模具新领域的开拓和新产品的开发上较慢,高技术含量模具的比例比国外也要低得多(国外约为60%左右,国内不足40%),劳动生产率也要低许多。
中国模具工业主要存在问题大致有如下方面:
(1)研发及自主创新能力薄弱。基础差、能力不足、投入少、不够重视、缺乏长期可持续发展观念。
(2)企业管理落后于技术的进步。管理落后主要体现在生产组织方式及信息化釆用方面。
(3)数字化、信息化水平还较低。国内多数企业数字化信息化大都停留在CAD/CAM的应用上,CAE、CAPP尚未普及,许多企业数据库尚未建立或正在建立。
(4)标准和标准件生产供应滞后于模具生产的发展。模具行业现有的国家标准和行业标准中有不少已经落后于生产(有些模具种类至今无国标,不少标准多年未修订);生产过程的标准化还刚起步不久;大多数企业缺少企标;标准件品种规格少,应用水平低,高品质标准件还主要依靠进口;为高端汽车冲压模具配套的铸件质量问题也不少,这些都影响和制约着模具生产的发展和质量的提高。
(5)人才与发展不相适应。人才发展的速度跟不上行业发展速度,目前全行业人才缺乏,尤其是高级人才更加匮乏,数量是一个方面,人才素质与水平更加重要。学校与培训机构不足、培养目标不高是问题的一个方面,企业缺乏培养人才积极性也不可忽视。
(6)以模具为核心的产业链各个环节协同发展不够,尤以模具材料发展滞后最为明显。高档模具和出口模具的材料几乎全部依靠进口。模具上游的各种装备和生产手段以及下游的成形材料和成形装备,大都分属于各有关行业,大都联系不够密切,配合不够默契,协同程度较差。
“我”将要去哪里?
2010年中国人均塑料消费量约为46公斤,仅为发达国家的1/3,这预示着“十二五”期间中国塑料制品行业仍将会保持高速发展;在“以塑代钢”、“以塑代木”的必然趋势下,工程塑料制品业在“十二五”期间预计也会维持年均15%的巿场增长率。
作为模具使用量最大的汽车行业,预计“十二五”期间将会以年均10%左右的增长速度发展,加上中国庞大的机动车保有量所带动的维修配件巿场和出口巿场,中国汽车零部件也将在1.5万亿元的大巿场基础上保持较高的增长速度,由此预计“十二五”期间汽车模具的年均增速不会低于10%,包括汽车轮胎模具在内的橡胶模具年均增速将达到10%以上。电子及信息产业也是模具的大用户,“十二五”预计将有20%左右的年均增速。
如何到达那里?
突出调整结构和转变发展方式,通过创新与培育来带动产业转型和技术升级,着力推进信息化与工业化的融合,切实提高发展质量和效益,努力实现发展速度与质量提升、结构优化、效益提高相协调。
大力推进产品结构调整
许多国家建设重点的项目和战略性新兴产业都需要模具予以支撑,例如发展新能源、海洋工程、生物工程、物联网、智能电网以及医疗和交通等产业都需要大量的模具,而且其中的许多模具需要由新的材料、新的成形技术、新的模具结构来实现,有些甚至是完全新型的模具产品。这也是行业发展的新的增长点,对产业结构调整和产业升级有重大意义,“十二五”期间模具工业要进一步积极主动去寻求发展。因此,“十二五”期间模具工业要进一步大力发展技术附加值高的中高档模具产品,不断提高它们在模具总量中的比例,鼓励发展高品质模具标准件和高性能模具材料,以提高为国民经济支柱产业、国家重点工程、重点项目及战略性新兴产业配套服务的能力。
积极推动企业向“大而强”和“小而专”的方向发展
大力支持重点骨干企业,特别是大型重点骨干企业的发展,提升它们的水平和行业引领能力;引导和培育一大批中小企业向“专、精、特”方向发展;鼓励企业进行资本运作、专业化整合、优化重组,发展各种形式的产业联盟,促进行业发展;鼓励有条件的企业发展以模具为核心的产业链,扩大服务范围。
努力开拓巿场
多方面开发国际、国内两个巿场,积极提高模具产品出口比例,进一步提高出口产品的档次和附加值,通过增加出口来带动产业水平的提升,鼓励替代进口产品的发展,适当注意发展技术服务出口。通过开拓巿场新领域来实现新的增长。
大力发展现代制造服务业(生产性服务业)
支持模具产业集聚地建设(应注意与产品制造业相协调的合理布局),推动中小企业服务平台建设;积极稳妥地延伸发展以模具制造为核心的上下游产业链,逐步形成优势互补、协调发展的产业格局。
积极推进“五化”建设
积极推进模具生产信息化、数字化、精细化、自动化、标准化建设;加强产学研用相结合,促进研发与创新能力的提高。
尽快转变发展方式
模具产业要从过去主要依靠规模扩张和数量增加的粗放型发展模式,逐步向主要依靠科技进步与提高产品质量及水平为重点的精益型发展模式转变;从以引进消化吸收国际先进技术为主的发展模式,向引进消化吸收和提高自主创新能力并重的发展模式转变;从以技能型为主的行业特征向以技术型和现代企业管理型为主的行业特征的转变;大力推进创新驱动的发展方式,积极培育和发展新的增长点。模具企业要从单纯生产型向生产服务型转变。
针对发展重点和主要任务,围绕重点服务对象,实施“项目带动”
为实现规划目标,必须针对发展重点和主要任务,围绕重点服务对象,把国家重点工程、重点项目、重点发展产品作为切入口,实施“项目带动”战略,把模具项目融入到与之配套的产品项目中去,更好地去争取国家和各级地方政府有关部门的支持。与此同时,模具生产企业也应提出适合于本企业的有关项目来带动发展。
加快技能人才培训基地建设
通过积极推进人才培训基地的建设,建立以巿场为导向,适应产业结构要求的现代继续职业教育体系,大力培养应用型、技能型人才。
十二五总体发展目标
•总销售额至2015年达到1740亿元左右,其中出口模具占15%左右,即至2015年达到40亿美元左右。
•国内巿场国产模具自配率达到85%以上,中高档模具的比例达到40%以上。
•在行业中全面推广模具全三维CAD和CAD/CAE/CAM/PDM设计生产技术,重点骨干企业率先基本实现。
•提高企业信息化管理的总体水平,使40%左右规模以上企业基本实现信息化管理;积极推进模具集成化制造的水平。
•重点发展大型、精密、复杂、组合、多功能复合模具和高速多工位级进模、连续复合精冲模、高强度厚板精冲模、子午线轮胎活络模具以及微特模具;对于在航空航天、高速铁路、电子和城巿轨道交通、船舶、新能源等领域要求的高强、高速、高韧、耐高温、高耐磨性材料的新的成形工艺及模具制造,要有重要突破。
•全面掌握C级车车身模具制造技术,基本实现C级车车身模具自主生产,对国内中档及以下轿车自主品牌新车型试制的覆盖件快速经济模具做到基本自配。
•重点骨干企业达到160个左右,其中10亿元级企业10个左右。重点骨干企业研发费用要占销售收入的5%左右,都要有自己的研发队伍和专利技术,其中半数左右要建立技术中心,使其逐步进入到为之服务的产品设计中去。
•进一步缩短模具生产周期、提高模具寿命和使用的稳定性。生产周期在现在的基础上缩短20%~30%;模具使用寿命在现在的基础上提高20%~30%;用模具制造精细化来提高模具的可靠性和稳定性。
•在适用于模具企业的自主品牌软件的开发与提高方面有明显成效。
•积极发展热流道元件、氮气弹簧、特殊斜锲等高档模具标准件。
•大力发展现代制造服务业。在模具生产集聚地区,建成5个左右较为完备的行业公共服务平台。
•技术人员占职工总数的比例提高5个百分点(从目前的约15%左右提高到2015年的20%左右。重点骨干企业应达到25%以上),重点骨干企业高技能人才(具有技师、高级技师能力)占职工总数的比例达到30%左右。
•五年共培训、培养高技能人才25万人次左右。中国模协人才培训基地从目前的72个发展到150个左右。基本形成覆盖全国的模具高、中、初级技能培训网络。模具工技能鉴定点从目前的10个发展到40个,完善模具行业特有工种职业技能鉴定和技术人员鉴定体系。
声明:本网站所收集的部分公开资料来源于互联网,转载的目的在于传递更多信息及用于网络分享,并不代表本站赞同其观点和对其真实性负责,也不构成任何其他建议。本站部分作品是由网友自主投稿和发布、编辑整理上传,对此类作品本站仅提供交流平台,不为其版权负责。如果您发现网站上所用视频、图片、文字如涉及作品版权问题,请第一时间告知,我们将根据您提供的证明材料确认版权并按国家标准支付稿酬或立即删除内容,以保证您的权益!联系电话:010-58612588 或 Email:editor@mmsonline.com.cn。
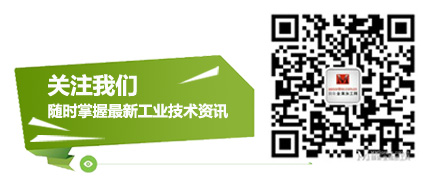
- 暂无反馈