微、小型模具的电火花加工
复型技术基础上的微型或小型零件的大规模生产越来越多,如热压成型,微注射成型,块体成型。这些技术主要依靠高温并在加工工具上加载,尤其是对整体的微小产品更实用。本文对应用微电火花加工技术在微/小型模具制造领域的技术发展现状提出了一些观点。
关键词:微制造;微电火花加工;模具制造
微电火花加工(µ-EDM)是应用电火花加工技术制造微型和小型零件和结构件。也就是采用加工技术和机床满足微型产品生产的需求[1-3],其次是工具电极的小型化,对比传统的电火花加工,单放电能量可减小到小于We =100μJ。现代机床一般使用静态脉冲发电机,它能产生低于1A的放电电流、近似正交的脉冲和0.2秒的放电时间,因此产生一个最小放电能量大约在We =5μJ。
进一步减少放电量是受电器元件和整流率限制的。因此,使用有10Pf电容的张弛振荡器,在放电电流100mA时,能够产生只有40 ns脉冲持续时间的脉冲。在最小放电量We =0.1μJ时,单次放电造成非常小的材料损失,弧坑半径小于2.5μm,,形成一个极小的带宽,带宽范围从SL=1.5到5μm。为了得到适宜的材料去除率,保证加工的经济性,必须使用能够产生非常高的脉冲频率的火花发生器。因此最新的微放电加工发生器能产生fp达到10MHz[4]的脉冲频率。微型电器加工的另一个重要的特点是电极的反向极性。由于传统的长脉宽电火花加工极性的作用,通常是工具电极阳极充电去增大材料去除率,以减少电极磨损。微电火花加工时脉宽短,必然因为有热量和构件的机械稳定性的限制,这一效应正好相反,因此在微放电加工中,工具电极通常阴极充电。
根据被加工件的几何形状,微放电加工采用不同加工变量。下面介绍这些加工方法的可能性和局限性。
1 微丝电子放电加工
微丝电子放电加工(电火花线切割机)的特点是应用直径较小的电极导线。为了加工最小的切割宽度或者内角,导线的直径dW= 0.1mm到dW=0.02mm。这种方法是最常用的直接生产微型机械装置和微型冲压工具的方法。为了保证足够的热和机械稳定性,通常导线电极使用钨或拉伸强度在2000n/mm以上的镀层钢。另外,导线电极热和机械稳定性限制了可加工构件的高度,也就是当使用直径dW=0.03导线电极时允许的最大工件的高度大约在5mm。
由于金属丝电极只能在一定范围内进行机械预拉伸,那么金属丝的振动就很容易导致加工精度或表面质量不够,因此,应减少裂口的公轴冲洗甚至应完全避免,将高精度加工系统和超水平电火花发生器相结合,在加工精度±0.001mm和大于100比率之间完成最小裂缝宽度0.04mm,构件宽度15um时能够利用金属丝电导加工方法反复加工,表面粗糙度小于Ra = 0.1um的仅可能采用精整技术,因为它只有一个相对较高的释放能量的切口和一些减少释放能量的连续整齐的切口。
2 显微压渗
用显微电极进行显微压渗主要用于制备进行微注射铸模或热雕刻,此法可复制大量微小机械部件,所获得的构件的尺寸不仅受腐蚀方法的限制而且受到电极的设计和制造的限制。时下,不同的显微加工技术像EDM显微模具,电极制造,甚至LIGA技术被用来生产成型电极,与传统的电火花压渗相比,尤其使用松弛发生器时,相对磨损能达到30%以上,因此,尽管在耐火材料像钨铜或者硬质合金基础上的高耐磨复合物都难于加工,但很适合进行显微电火花压渗。总之,由于尺寸小,电极冲洗不太可能,传统的冲洗办法不能应用在显微冲压模型EDM中。加之极小的裂口宽度,恶劣的冲洗条件对进给控制要求特别高。
3 显微电导钻孔
为了旋转加工对称钻孔和通孔而使用旋转轴销电极是电火花加工压渗技术的一个特例。这个所谓显微电导钻孔被广泛应用在加工注射喷嘴和为微丝电火花加工开孔。由于轴销电极最小电极直径小于25um,尤其可用在电极生产、电极处理和电极定位上。为确保足够的机械稳定性和耐磨性能,使用硬质合金、钨或者钨铜等作主导材料。
为提高冲洗和园整度,旋转轴的旋转速度应在2000转/min以上。通过CFD技术研究和大量模拟显示,仅靠电极旋转冲洗缝隙仅能在一定范围改善加工的稳定性。仅仅一个叠加的进给过程中的平移振动就能有效地将裂口中碎片去除掉。利用这种技术可以加工成型系数为50的孔洞
4 微电火花造型
例如应用在平面展台的玻璃压花过程中的带有各种显微组织的大型模具,由于其尺寸要求,不能利用导线电火花加工或压渗进行加工。其工作面过高限制了微电火花加工中电极热稳定性和机械稳定性,或者由于冲洗效果差和大的活泼电极表面所引起的加工过程不稳定而使外廓尺寸可以允许使用压渗电极。作为一种选择,显微电导造型可以在旋转工作电极和工件之间进行单路径控制、大量轴线进给。这种几何单旋转电极的使用明显地降低了电极生产浪费和成本。而且可以使用商用电极或者通过电火花打磨加工电极。就像在电火花钻孔中使用耐磨材料一样。综上,在路径控制运动中根据校正算法通过接入技术来补偿电极磨损。由于电极的相对运动和敞口造型,与电导钻孔相比,电火花冲洗不是很关键。由于没有上述提到的局限性,与电火花显微刻模和金属丝电导加工相比,造型的复杂性相对较高。由于至今没有可行的粗轧和精加工的技术标准,可以承认显微造型获得的表面质量与其它显微电导加工方法相比较低。
显微电导造型的两个不同的变量是可以进行区别的。当旋转盘电极的路径控制运动与电火花加工进给过程重叠时,可以加工直线。这种运动学接近蠕变进给摩擦,这种方法叫显微电导摩擦(u-EDG)。电极盘剖面形成槽钢截面,在成型系数为15时,可加工的最小槽宽为50um。对生产稳定性做了一系列的技术调查研究,尤其是对像在显微射流应用中一样的微槽成型工具的加工中[5-6]。如果工件造型是通过旋转销轴电极进行加工的,这个过程叫做显微电火花铣磨。它几乎可以用作生产任何三维尺寸的构件[7],通过销轴电极尺寸和缺口宽度可以确定构件的最小尺寸。目前,可以使用通过电火花打磨加工的最小直径0.1mm的销轴式电极,因此,适当的路径控制运算法则、进给控制方法和磨损补偿技术的发展是目前调查研究的核心。
5 显微电导压铸
电导钻孔和电导铣磨的先决条件是几何定义电极的可行性。因为电极造型和电极夹具偏离与真正运行精度有关,而使用这种电导压铸技术直接生产电极可以避免这个问题,
可以使用硬质合金块进行电导压铸,在旋转电极上使电极极点交换倒置形成磨损。使用这种技术,可以减少压铸时间,因为接触区域较大并且有较高的电导能量。另一方面,复杂剖面的电极不可使用这种技术加工。而可供选择的方法是金属电导摩擦,也就是通过旋转电极在无线圈金属电极上来加工。这种技术与大块电极相比,缺点是金属丝电极产生有限的热稳定性和加工稳定性而使电导能量较小。接触面积小也会导致压铸速度较低,因此,普遍使用多步压铸方法。首先,用硬质合金大块电极用于进行粗磨,其次,通过无线圈金属丝电极进行电极成形。目前,用这种技术可以加工最小直径为20um 的成型系数(高宽比)为30的销轴式电极,相似的技术也可以用来生产形成微小圆柱件成型工具。
6 结合语
本文研究了各种微电火花加工方法。主要研究的是它的实际运用部分,而不是理论研究。结果表明,微电火花加工是一个非常具有潜力的加工技术,尤其对微型件复制的小型模具的加工。
声明:本网站所收集的部分公开资料来源于互联网,转载的目的在于传递更多信息及用于网络分享,并不代表本站赞同其观点和对其真实性负责,也不构成任何其他建议。本站部分作品是由网友自主投稿和发布、编辑整理上传,对此类作品本站仅提供交流平台,不为其版权负责。如果您发现网站上所用视频、图片、文字如涉及作品版权问题,请第一时间告知,我们将根据您提供的证明材料确认版权并按国家标准支付稿酬或立即删除内容,以保证您的权益!联系电话:010-58612588 或 Email:editor@mmsonline.com.cn。
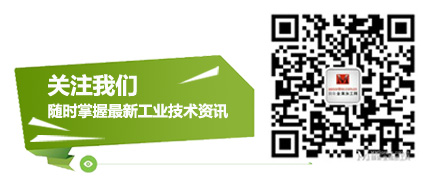
- 暂无反馈