数控机床切削加工过程的模型参考
在由机床、刀具、工件组成的系统上进行切削加工是一个动态过程,有许多因素和参数(如工件毛坯裕量不匀、材料硬度不一、刀具磨损、刀刃积屑瘤、受力变形、切削振动和热变形等)将使切削过程不能处于最佳状态,从而影响切削过程的生产效率、加工质量和经济效益,甚至还会影响切削过程的正常进行。为了解决这一问题,在20世纪60年代,提出了一种机床的自适应控制方法,在切削加工过程中采用该方法能根据随时变化的实际切削条件及时修正切削用量。
根据模型参考自适应控制(MRAC)思想,建立了数控机床切削加工过程MRAC模型,然后对模型进行动力学过程仿真。同时,分别对加工过程的反馈闭环控制和开环控制进行仿真,并将这3种仿真结果进行比较,从仿真结果可以看出,MRAC的机床切削加工性能指标最好。
数控机床MRAC的工作原理
数控机床的MRAC是以机床、刀具、工件系统所完成的切削过程作为调节对象。该控制系统的原理结构如图1所示。它除了一般数控机床的位置和速度控制回路以外,还增加了MRAC反馈回路。当系统受到各种随机因素的干扰后,切削过程的状态参数立刻发生变化,通过传感器随时检测这些参数的数值并经转换,在MRAC控制单元中与给定的评价指标或约束条件(即期望的性能指标)进行判别和比较,得到性能指标偏差,然后给主机CNC输出校正信号,对系统的输人参数进行修正,从而使切削过程向预定的指标和条件转变,以达到最佳状态。
机床切削加工MRAC模型的建立
机床切削加工过程由伺服机构、切削过程、参考模型调节机构、前馈装置和反馈装置等环节组成。
机床加工过程MRAC的切削性能
在机床加工过程中,切削性能的好坏不仅对零件的质量会有很大的影响,而且还很容易损坏刀具。而机床、刀具、工件系统的切削过程是个不稳定的过程,它经常受外界很多不确定因素干扰,导致切削过程中的状态参数随时发生变化。如果不及时调整,切削性能就会大大下降。通过MRAC调节,可以使切削性能的参数一直处于稳定状态。现以机床加工过程中切削力恒定在设定值为例来说明随外界因素(以背吃刀量的变化为例)干扰时MRAC能及时调整切削力,使之一直处于期望的切削力。背吃刀量的变化与进给速度的变化刚好相反,也就是说,如果背吃刀量增加,进给速度就降低,以保持切削力恒定在1000N上,反之亦然。所以,MRAC系统通过自动并准确调节加工过程的进给速度,来实现加工过程的恒力控制。
( 文章来源:互联网 )
声明:本网站所收集的部分公开资料来源于互联网,转载的目的在于传递更多信息及用于网络分享,并不代表本站赞同其观点和对其真实性负责,也不构成任何其他建议。本站部分作品是由网友自主投稿和发布、编辑整理上传,对此类作品本站仅提供交流平台,不为其版权负责。如果您发现网站上所用视频、图片、文字如涉及作品版权问题,请第一时间告知,我们将根据您提供的证明材料确认版权并按国家标准支付稿酬或立即删除内容,以保证您的权益!联系电话:010-58612588 或 Email:editor@mmsonline.com.cn。
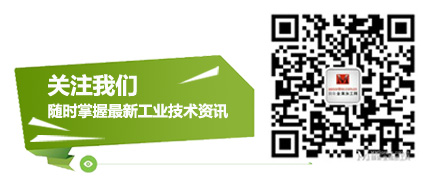
- 暂无反馈