中国核电发展规划不变 机床的挑战与机遇
即使近邻日本由于此次百年不遇的地震与海啸引发了福岛核电站的故障,让世界核电产业顿时沦为惊弓之鸟。但日前已有不少官方人士对外表示,中国的核电产业发展规划不会改变,核电建设仍将继续高速稳定推进。
这无疑对上游的机床工具行业而言,是颗重要的定心丸。尤其是我国正在大规模推进的第三代核电AP1000的建设热潮,其需要的高质量的大型铸锻件及为数众多的精密零件对高端数控机床的需求或将迎来井喷。
核电进入快速发展期
我国核电从上世纪70年代起步,目前已运营商用核电机组13台,装机容量1080万千瓦。经过近40年探索,我国在核电技术研发、工程设计、设备制造、工程建设、运营管理等方面,积累了丰富经验,培养了一大批具有较高业务水准和实践经验的技术与管理人才,为核电进一步发展创造了有利条件。
2003年,全国核电建设工作会议提出,核电要统一组织领导,统一技术路线,引进国外先进技术,加快自主化建设。“十一五”规划提出“积极发展核电”的方针。为加强对核电建设的统一领导,成立国家核电自主化工作领导小组。
通过开展三代核电技术国际招标,我国决定从美国西屋公司引进AP1000核电技术、建设4台核电机组。同时,成立国家核电技术公司,作为引进、消化、吸收和再创新的平台,开发具有自主知识产权、中国品牌的先进核电站。
近年来,我国核电呈现加快发展势头。三代核电技术引进消化吸收再创新进展顺利,大批核电项目开工建设,核电设备国产化率不断提高。为了适应新的核电发展形势,能源主管部门提出对核电中长期发展规划进行较大幅度调整,比刚刚执行4年的规划目标翻了一番多。尽管如此,仍不能满足地方和企业加快发展核电的要求。
例如,东中西部地区都提出要上核电,不少省份甚至由省委、省政府主要领导“挂帅”抓核电项目,不断向能源主管部门提出,希望将本省项目纳入规划,已经纳入规划的省份都要求提前开工。
截至目前,国家已核准核电机组32台,在建核电机组23台,占世界在建机组的40%。其中,已开工25台,装机容量2773万千瓦。已运营和核准的核电机组达4393万千瓦,原规划2020年中国实现核电装机4000万千瓦,但为了减少二氧化碳排放量并考虑现实可能,即将出台的核电中长期规划预计将把这一指标调整到7000万千瓦以上。而全国已完成核电厂址初步可行性研究,准备新上的核电项目总规模为2.26亿千瓦。“十二五”期间将成为中国核电建设的高峰期,每年核电建设投资规模将超过700亿元。
机床的挑战与机遇
机床作为现代复杂生产工具,是人类生产力发展三大要素中至关重要的工具之一,机床的“先进性”决定人类的生产效率和劳动生产率。
能源结构的调整,为能源装备制造业拓展了市场空间的同时,也为机床工具行业创造了新的市场机遇。
我国能源装备制造业至“十一五”末已有较大投入,但随着核电、风电等清洁能源的投资力度加大,大型铸锻件、环形本体(如汽轮机壳体)、大型复杂件、大型平面加工和半圆体加工、叶片、叶根加工以及各种泵体、泵阀制造等,对重型立车、大型落地铣镗床、超重型的龙门镗铣床、五轴联动机床、数控拉床及各种高档立、卧加工中心,以及相应的数控刀具、量仪都将提出新的需求。
而目前的现状是,核电装备制造水平不高。据核电装备企业反映,经过多年努力,我国已拥有每年制造多套百万千瓦核电机组装备的能力。但实际情况是,由于产品质量不稳定,技术标准不统一,设备拖期现象十分严重,每年连完成一套百万千瓦机组的成套装备都很困难。我国现在的核电装备企业以往主要制造常规电力设备,制造核级装备时质量保证体系不够健全,因为赶工期,导致质量问题屡有发生。
这对作为工作“母机”的机床而言,既是机遇,也是挑战。
其挑战在于,我国机床行业较发达国家起步稍晚,对于高精尖的机床产品仍存明显差距。而摆在眼前的核电“蛋糕”是否有能力吞下,将取决于我国机床行业克难攻坚的意志与能力。
而机遇在于,核电对于机床行业不仅意味着巨大的市场和丰厚的回报,更在于能否突破瓶颈借机实现跨越发展。
国家能源局局长张国宝曾在AP1000核电技术装备自主化第二次工作会议上指出,推进核电技术装备国产化是国家战略,今后国家能源局将进一步加强AP1000核电技术装备国产化的组织协调。
他强调,AP1000首次在中国建造,对国内装备制造业是一次严重的挑战,更是千载难逢的历史机遇。一旦实现了国产化,中国将成为三代核电技术的示范基地,也将成为AP1000设备的主要供货商。
他同时表示,国家能源局将进一步加强AP1000核电技术装备国产化的组织协调,加强产业政策的引导、国产化依存工程管理、进出口政策的调整、科研攻关组织,加大重要技改资金支持力度。加强核电产业和制造企业发展的科学规划,统筹国内制造能力的提升,实现核电建设与设备制造的协调发展。
这对机床行业来说,将是一次转型升级迈向高端制造的绝佳契机。同时,随着中国核电“走出去”战略的逐步推进,不仅将为机床行业带来长期利好,而且有望将中国机床推向世界。
相关链接: 船用配套设备将成机床消费重点
2010年,全国造船完工量6560万载重吨,同比增长54.6%;新承接船舶订单量7523万载重吨,比去年同期新接订单量增长1.9倍;截至2010年12月底,手持船舶订单量19590万载重吨,比2009年底手持订单上升4.1%。
由于船舶工业是一个技术密集、资金密集和劳动密集型产业。近十年来,中国船舶工业充分发挥了我国劳动力成本比较优势,取得快速发展。在全球市场上所占的比重正在明显上升,中国已经成为全球重要的造船中心之一。
但这个第一光环下难以掩盖的一个现实问题是,我国船用关键设备几乎80%需要进口,而日本、韩国等造船强国的设备自给率则在90%以上,因此以提高生产效率和降低制造成本是我国船舶工业的当务之急。
把一艘船拆解来看,船用配套设备是指动力装置、甲板机械、船舶锅炉以及船舶电气设备等。动力装置包括智能型柴油机,节能环保型中低速柴油机,LNG船用双燃料发动机、船舶轴系(减速箱、轴承、中间传动轴)超大型螺旋桨以及大型高效喷水推进装置等。甲板机械包括舵设备、锚设备、系缆设备以及船舶起重机械等。船用电气设备包括大功率中高压发电机以及供电设备。此外,还有船舶锅炉、制冷和空调装置以及船用泵、阀等。
对于机床制造商而言,要想在船舶行业打出名片,必须在船舶的核心配套部件,船用柴油机关键零部件上多用功夫。
作为船舶的核心配套部件,船用柴油机关键零部件主要包括机座、机架、气缸体、连杆、缸盖、缸套、活塞、凸轮轴及凸轮组件、轴瓦、进排气阀、空冷器、油泵油嘴等。
加工精度以PA6BV-280(7140kW)船用柴油机为例,除了活塞最高加工精度为IT4级、气缸体最高加工精度IT5~6级以外,凸轮轴、缸盖、缸套等部件要求最高加工精度均为IT6级。
而中低速柴油机机座和机架的主要加工设备有数控龙门镗铣床和数控立车;气缸体(机身)的主要加工设备有数控龙门镗铣床和龙门加工中心,规格以龙门宽度 2~5米居多,最大不超过8米,定位精度和重复定位精度要求分别为不超过0.016/1000毫米和0.01毫米;缸盖的主要加工设备有卧式加工中心、立式加工中心和立式车铣中心,卧式加工中心规格以500、630、800规格需求居多,630卧式加工中心要求定位精度X、Y、Z轴不超过0.008毫米,重复定位精度不超过0.004毫米;连杆、曲拐的主要加工设备有数控龙门镗铣床、大型数控立车、重型数控卧车、立式和卧式加工中心等;凸轮轴的主要加工设备有凸轮轴铣床、凸轮轴磨床等。
此外船舶另一个核心功能部件——重型曲轴的主要加工设备有卧式曲轴车床、立式车床、落地镗床、龙门铣床、曲轴铣床、卧式车铣加工中心、曲轴磨床等设备。低速机曲轴采用组装结构,曲轴与曲柄单件加工,经热装后再进行整体加工,需要重型车铣复合加工中心,数控曲柄立式车床、数控立车、数控落地镗铣床以及热装后精加工的重型曲轴旋风切削加工中心等设备。
大型船用螺旋桨的主要加工设备有五轴联动数控龙门铣床、五轴联动数控立式车铣床和七轴五联动车铣复合加工中心等。该类设备是衡量一个国家机床制造水平的标志性产品之一,目前世界上最大加工直径的螺旋桨加工设备由韩国研制,直径为11米,其次为德国和日本生产的加工直径为10.4米的数控机床。而随着我国大型船舶的发展,加工直径为11米螺旋桨的七轴五联动数控车铣床需求也将出现。
现代大型船舶要求更高的推进效率,更低的噪声,因此对螺旋桨推进器等关键零件的加工精度和表面粗糙程度也提出了更高的要求。此外,由于螺旋桨叶面加工的复杂和特殊性,对机床的功能和加工性能也有新的要求。
例如,克服大型螺旋桨加工中滑枕承受力矩过大对机床寿命的影响;七轴五联动数控车铣床防干涉碰撞功能的实现;基于三维数字化模型的加工余量快速测算,测点规划、测量轨迹自动生成以及在线质量评估功能等仍是船舶制造专用机床亟待攻克的难题。
声明:本网站所收集的部分公开资料来源于互联网,转载的目的在于传递更多信息及用于网络分享,并不代表本站赞同其观点和对其真实性负责,也不构成任何其他建议。本站部分作品是由网友自主投稿和发布、编辑整理上传,对此类作品本站仅提供交流平台,不为其版权负责。如果您发现网站上所用视频、图片、文字如涉及作品版权问题,请第一时间告知,我们将根据您提供的证明材料确认版权并按国家标准支付稿酬或立即删除内容,以保证您的权益!联系电话:010-58612588 或 Email:editor@mmsonline.com.cn。
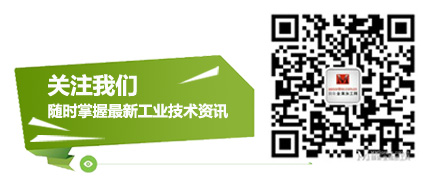
- 暂无反馈