高端装备制造低碳发展 推动机床产业快速增长
2009年我国首次成为世界机床第一大生产国,但我国机床行业大而不强的局面依然没有改变,产品质量、技术、服务较国际先进水平仍然有一定差距。目前国内所需的高档数控机床主要依赖进口,发展中高档数控机床所需的数控系统和功能部件主要来自海外。我国拥有世界上数量最多的机床制造厂家,但缺少著名的跨国机床集团和世界级的“精、特、专”机床企业。以重型机床为例,虽然经过近几年技术改造和产品自主研发的锻炼,无论是生产能力还是产品技术水平都有长足进步,但是与国外产品相比还有不足。最大的差距体现在核心运行部件的技术水平和运行速度、产品精度保持性、机床可靠性,以及整体机床制造工艺水平与质量等几个方面。可靠性是高档重型机床质量的一个关键指标。目前,国产数控重型机床的平均无故障工作时间在300小时左右,而进口的高档重型机床平均无故障工作时间在2000小时以上。
随着中国机床工具行业产品、产业结构调整力度的增强,数控机床、高端机床占比明显增强,低端产品占比持续降低,目前机床工业国产化率已提升到70%。罗百辉认为,机床行业高速增长的同时,进一步加快行业和产品结构调整,促进产业升级,仍是我国机床工业首要而迫切的任务。而低碳经济和节能减排将引发装备制造业发展模式转变,从过去粗放的追求规模的发展方式向提高自主创新能力、提高国际竞争力的发展方式转变,以此作为“十二五”装备制造业发展方向的转变和战略的突破。作为生产工具,机床产品对装备制造业生产方式转变的意义是毋庸置疑的,同时,提高自主创新能力,为发展低碳经济和节能减排作贡献,机床产业更是责无旁贷。但低碳经济也将给机床行业带来一些约束,尤其将影响到中低档机床的需求。
机床行业的低碳经济
2011年是“十一五”规划实施的最后一年、关键一年,也是充满希望的一年。机床全行业将在中央关于2010年经济工作方针指导下,勤奋工作,开拓创新,为机床工具行业加快结构调整、转变发展方式做出新的贡献。国际模具及五金塑胶产业供应商协会负责人罗百辉指出,2011年机床全行业应该突出战略重点,明确主攻方向,进一步加快结构调整和转变发展方式,为行业健康持续发展创造条件和环境。
第一,进一步加快机床产品结构调整。压缩低档、普通产品生产;淘汰落后、污染、高耗能产品;发展技术含量和经济附加值高的产品;由提供单机向提供成套成线设备方向发展等。
第二,进一步完善产业链。加大政策扶持力度,突破数控机床产业发展瓶颈,大力发展数控系统和功能部件,提高数控系统、功能部件在产业中的比重;鼓励发展数控刀具、复杂刀具、精密量仪、高档磨具磨料和超硬材料及精密模具制品。
第三,实施企业结构调整。发挥重点骨干企业批量制造能力优势,鼓励通用型主机制造适度集中生产;扶持“专、特、精”数控机床制造企业;扩大功能部件制造企业、制造技术服务企业规模;鼓励企业资产优化重组,推动企业结构向“大而强”、“小而专”的方向转变;发展精益管理和敏捷制造等。
世界一些发达国家以环保构筑绿色壁垒,无疑增加了国际市场准入难度。污染环境高耗能产品或被拒之门外,或被课以重税制裁。国际模具及五金塑胶产业供应商协会负责人罗百辉认为,中国机床工具企业应把低碳制造、绿色制造纳入企业的发展规划中,注重低碳经济、绿色制造技术研究应用,把握未来经济发展方向已经成为进入国际市场基础。
机床工具行业应关注重点投资领域,深入了解用户需求,加大研发适用产品力度。尽快淘汰落后产品产能,避免恶性竞争。应大胆尝试向“专、精、特”产品转移。一些企业开发出高速铁路轨道板磨床就向“专机”发展成功例子。这种需要我们填补空白领域还有很多,如:飞机用铺带机、飞机用自动钻铆机、纺机针专用机床、人体关节假肢等医疗保健领域所需零件加工设备等。目前这些设备主要依靠进口,有甚至对我国禁售。我们只有立足自主创新、开发出满足用户需求进口替代产品,才能打开新市场。数据显示,2009年以来我国机床零部件进口持续增长,这显示国产机床零部件还不能完全满足主机行业要求。零部件企业应抓住市场增长契机,开发新产品,加快进行结构调整。
低碳经济促机床产业发展
对于大批量、低技术含量的粗放型发展模式的中国机床工具行业,满足中国政府对低碳经济的发展需求,充分利用“高档数控机床与基础制造装备科技重大专项”资金,加大新产品研发力度,快速提供高性能的加工设备,将会促进行业发展。包括水电、风电、核电和太阳能发电的新能源和节能环保行业等新能源装备也正成为推动机床业快速增长和技术进步的一大动力。据国际模具及五金塑胶产业供应商协会负责人罗百辉透露,新能源装备的加工将成为机床需求的主力,这需要多种精密、大型数控、专用机床与之配套。先进的装备制造工艺,尤其是先进的机床设备是新能源装备制造产业升级的根本保障。
金属加工业,特别是数控机床作为制造业的工作母机,将承担新能源和环保行业的大型、精密零件的加工和制造。由此,中国重型机床生产商近年推出了相应的机床产品。同时,太阳能发电站、新能源汽车等也对大型、多轴、精密数控机床有大量需求。
目前,国内大型风力机组的总体设计和载荷计算能力差,控制系统、发电机、齿轮箱、轴承的设计和生产能力差,风机的轴承、控制系统等零部件还需要从国外进口。我国风电设备制造业虽然发展速度快,但真正拥有核心技术的企业不多,关键零部件基本依赖进口。而制约其提升的关键就是国内的制造工艺和加工装备相对落后。
核电设备制造也面临着类似的情况。据介绍,一座核电站需要200多台各种类型的泵。其中主泵是位于核岛心脏部位的关键部件,是核电运转控制水循环的关键,虽然核岛主泵的结构并不比其他泵复杂,但是要求极高,必须具有绝对的可靠性。主泵承压部件和功能部件的加工都需要高精度性能可靠的机床设备。正是由于没有相应的机床加工设备,核岛主泵曾长期受制于人。
此外,生产百万千瓦级核电站压力容器等,需要万吨压力机锻压成型。后续切削加工需要超重型数控立式车床、超重型数控卧式车床、大镗杆多轴联动数控镗铣床等加工设备。这些工件的价格昂贵,而且没有备件,要求成品率必须100%,因此对机床的可靠性和稳定性都有很高的要求。
目前,行业领军企业已经意识到能源装备特别是新能源装备是座金矿,并开始积极研发相关机床设备。武重自主研发的XKD2755×570-2M型数控定梁双龙门移动镗铣床适合风电齿轮这种超大规格零件的加工;齐二机床自主研制的世界最大重型TK6932数控双柱落地铣镗床为大型水电机组、核电站设备的超大型工件加工提供了关键加工机床;国内第一台太阳能全自动硅片多线切片机也宣告研制成功。
机床工业技术含量和工艺要求极高,属于技术和资本密集型产业,行业壁垒也很高,无论在国内还是在全球范围内,行业格局变化都比较缓慢。但国内机床行业如果抓住能源装备需求巨大和新能源装备迅速发展的时机,实现结构调整和技术进步并非没有可能。
国际模具及五金塑胶产业供应商协会负责人罗百辉认为,能源装备领域对机床的需求趋势为大型化、高精度和高可靠性。能源装备制造业与机床工具行业通过建立长效合作机制,有利于双方进行供需对接,确定示范工程和依托单位;有利于双方选好结合点,找出突破口,制定好行动计划,跟踪应用效果。在今后的合作中,双方宜逐步建立起项目管理办法,并形成项目全过程监督体系,引导企业提前部署前沿技术、装备的开发研制和自主创新,进一步推动国产高端数控设备自主化。
不过,从目前来看,机床行业与能源装备制造行业实现成功对接还需探索相应的模式。据了解,机床工具行业从2005年开始抓高档数控机床在高端用户中的应用,当时选择了国防军工行业作为重点应用领域。有业内人士认为,可以借鉴机床业与国防军工行业对接的成功经验,把能源企业请来一起座谈,请他们讲需求,讲要加工的产品,讲加工技术和要求,进行供需对接,然后确定示范工程和依托单位。
正如国际模具及五金塑胶产业供应商协会负责人罗百辉所言,加强机床供需间的合作和相互支持,既能推动能源装备的国产化和自主化,又能促进国内机床行业结构调整和技术进步,可以实现共赢。
声明:本网站所收集的部分公开资料来源于互联网,转载的目的在于传递更多信息及用于网络分享,并不代表本站赞同其观点和对其真实性负责,也不构成任何其他建议。本站部分作品是由网友自主投稿和发布、编辑整理上传,对此类作品本站仅提供交流平台,不为其版权负责。如果您发现网站上所用视频、图片、文字如涉及作品版权问题,请第一时间告知,我们将根据您提供的证明材料确认版权并按国家标准支付稿酬或立即删除内容,以保证您的权益!联系电话:010-58612588 或 Email:editor@mmsonline.com.cn。
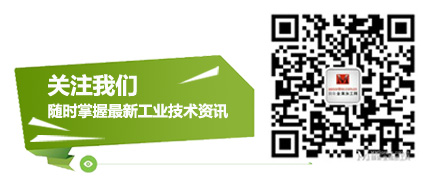
- 暂无反馈